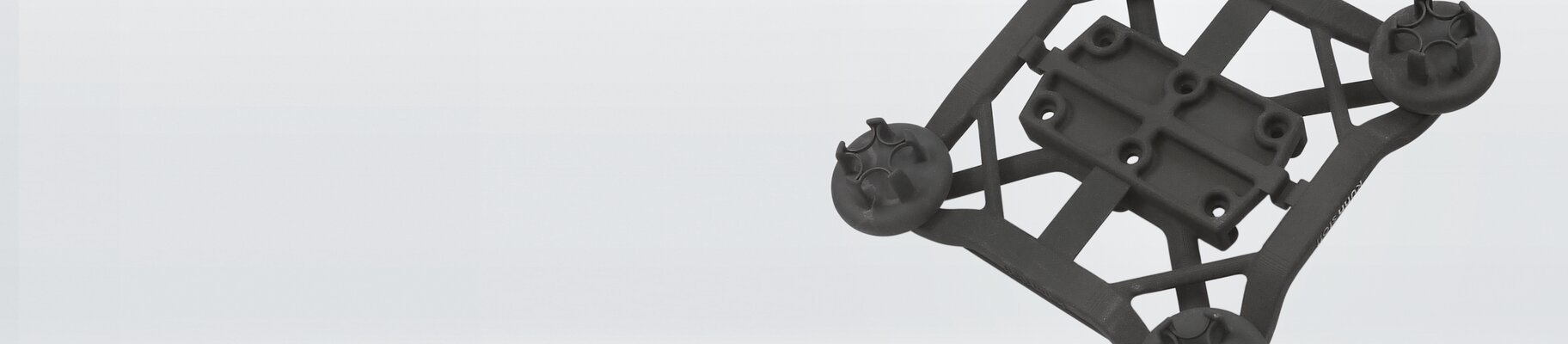
EOSテクノロジーで軽量化と耐久性を実現したグリップシステム
ヴィットマン&クーンストッフ|ケーススタディ
EOSテクノロジーにより軽量かつ耐久性を実現した機能的ベースプレート付き気管支グリッパー
親指と他の指が対になる人間の手は、握り、探求し、働くための理想的な道具です。そのため、文化活動や技術進歩の鍵ともなっています。産業界では、この独創的な原理がしばしば利用されています:機械が使用される工程のひとつに、ほとんどあらゆる部品を次の作業工程に運ぶための、自動具リッピングがあります。
そのようなグリッピングマシンは、エンジニアリングの傑作です。Kuhn-Stoff GmbH & Co KGは、EOSアディティブ・マニュファクチャリング技術を応用した特殊なエンジニアリングに専念しています。このプロセスでは、レーザー光線で溶融したプラスチック粉末から、層ごとに機械部品を形成します。このようにして、Kuhn-Stoff社は、ドイツのニュルンベルクにあるヴィットマン社(Wittmann Robot Systeme GmbH)向けに、非常に軽量で強度と耐久性に優れた気管支グリッパーを開発・製造しました。このグリッパーは、空気圧ダクトを内蔵した支持フレーム上に4台設置されています。

「私たちは何年も前から、自動化のさまざまな分野でアディティブ・マニュファクチャリングで製造された部品を導入してきました。この気管支グリッパーは、私たちの要件をすべて満たしています。この部品は、日常的な性能において非常に信頼できます。」
Michael Tolz|ドイツ技術部長兼支店長|Wittmann Robot Systeme社、ニュルンベルク
課題
お客様はロボットとオートメーションシステムのメーカーです。Kuhn-Stoffは、空気圧機構を介して生産機械から機械部品を持ち上げ、搬送し、セットダウンするメカニカルグリッパーの再設計を依頼されました。その結果、以下の要件が達成されました:グリッパーは、必要な荷重を移動させることが可能でありながら、以前のものよりも軽量であること。設計の複雑さは単純化され、部品は効率基準を満たさなければならない。
重量の重要性は物理学に帰着します:このようなグリップ・システムは、与えられた単位時間内にできるだけ多くの機械部品を移動させるために、素早く動作しなければならない。
質量が不活性であるということは、それを動かすためには力を加えなければならないということです。荷物が重く、速く動けば動くほど、加速と減速の両方に必要な力は大きくなります。
エネルギー効率の観点とは別に、この事実はシステムの耐久性にも特に悪影響を及ぼしますす:荷重が大きいほど機械の摩耗が大きくなります。
前バージョンのグリッパーは、アルミニウム、ゴムチューブ、複数の接続エレメントで構成されており、製造コストが高額でした。Kuhn-Stoff社の積層製造の専門家は、設計を大幅に簡素化するという目標を設定しました。機械部品の新しい構造は、軽量化の一部に貢献するはずです。他の部分は、アディティブ・マニュファクチャリングの利点の1つである、構造最適化によって達成されなければなりませんでした。作業が始まるとすぐに、新しいグリッパーは、製造後の仕上げやさらなる組み立てを必要とせず、単一部品として製造できることが明らかになりました。

ソリューション
圧縮空気がフレキシブルな膜に流れ込むと、グリッパーの爪が開き、同様に圧縮空気を止めるとシステムは閉じます。プラスチックの柔軟性に加え、部品は90°旋回し、必要な動作シーケンスを実行できなければなりません。これらの要件を考慮することで、必要な部品点数をわずか2点に減らすことができました。
設計プロセスの完了とともに、Kuhn-StoffはFORMIGA P 100を使用して新しいグリップシステムの製造に取り掛かりました。わずか数時間で、グリップシステムの2つの部品がポリアミドから製造されました。EOS技術のおかげで、空気圧ダクトとコネクターはベースプレートに完全に統合されました。
「いつものように、EOSシステムを使った生産はスムーズで問題ありませんでした。最終的な結果は、今回も関係者全員に感銘を与えました。1つの工程で、顧客の要求をすべて上回る機能的に統合された部品を作ることができました」。Kuhn-Stoff社のCEO、Hannes Kuhn氏は、次のように語っています。「つまり、アディティブ・マニュファクチャリングは今や日常的な現実となりましたが、その結果はやはり並外れたものでした。」

「我々はEOSテクノロジーを8年以上使用しており、好結果ばかりを得ています。正しく適用されれば、設計の柔軟性が大きなメリットをもたらし、我々の顧客は市場においてほとんど他の追随を許さない優位性を得ることができます。」
Hannes Kuhn|CEO|Kuhn-Stoff GmbH & Co KG
結果
軽量にもかかわらず、グリッパーは過酷な連続使用でも必要な荷重を支えることができます。500万サイクルの後、指定された耐用年数に達したため、チームはストレステストを中止しました。この間、不具合や故障は一度も発生していません。その理由は、ベースプレートにエアダクトが内蔵されているにもかかわらず、強度が確保されていることにあります。さらに、柔軟な設計により、小さな衝突が発生しても、グリッパーシステムや射出成形ツールに損傷を与えることはありません。場合によっては、軽量化により、より小型のロボットを使用することが可能となり、大幅なコスト削減につながります。さらにWittmann社は、グリッパーの高さが低いため、射出成形機のクランププラテンの必要な開口幅が小さくなり、作業サイクル数を増やすことができました。つまり、運転コストの削減です。
製造コストは、従来型と比べて50%削減されました。これは軽量化と、部品点数を21点から2点に削減したことによります。同様に重要なのは、製造時間が短縮されたことです。従来、 Kuhn-Stoffが12日間かけて製造していたグリップ・システムが、現在ではわずか3日間で済むようになりました。
「新しいグリップ・システムには非常に満足しています。ヘビーデューティーで継続的な使用において、以前のユニットと同様に効果的であることが証明されました。アディティブ・マニュファクチャリングが気管支グリッパーの製造にもたらしたものほど、グリップ製造の進歩が著しいものは見たことがありません。この生産方式は、当社のオートメーション・ソリューションに非常に良い影響を与えています」と、Wittmann Robot Systeme GmbHの技術責任者兼支店長であるMichael Tolz氏は総括します。革命が進化に勝ることもあるのです。
結果の概要
-
-1350グラム86%の軽量化
-
-50% のコスト削減:生産コストを50%削減
-
-19 コンポーネント:個々のコンポーネントを21から2に削減

EOSケーススタディ
EOSの30年にわたる3Dプリンティングのパイオニアとしての卓越性をご覧ください。