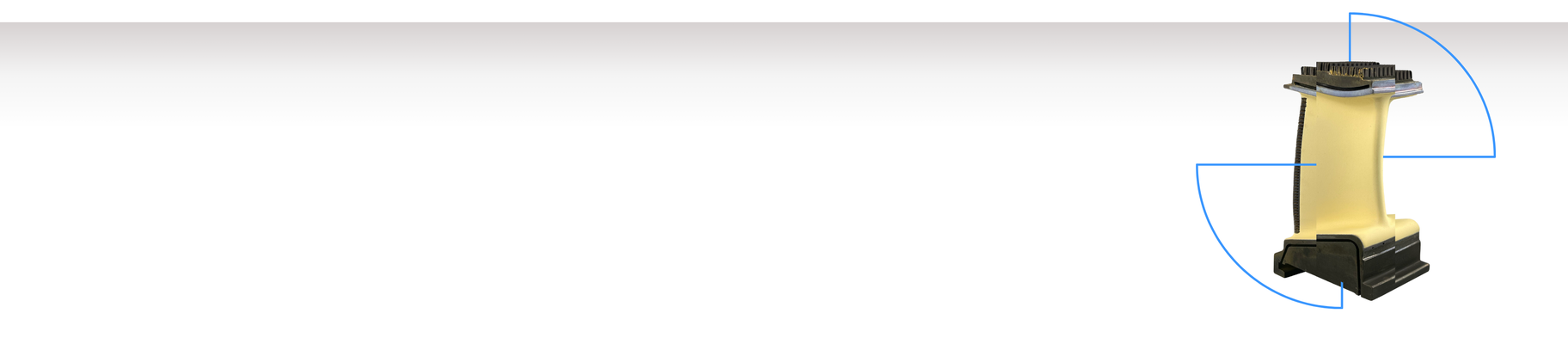
ターボ機械&タービン
ターボ機械用部品のアディティブ・マニュファクチャリング
ターボ機械はエネルギー生成に欠かせないものです。その高性能部品は、複雑なハイテク設計を特徴としており、エネルギー需要の増加に伴い、ますます堅牢で強力である必要があります。さらに、ターボ機械の部品は、融点を超える温度でも耐性を発揮し、信頼性を高める必要があります。
3D金属プリンティング(DMLS)は、とりわけ最適化された冷却戦略を実現するための適切な技術的基盤を提供します。部品は、より正確に焦点を合わせてエネルギーを伝搬し、適用するように設計および製造できます。例えば、革新的な修理工程は、元の部品に磨耗した部分を直接作り足すことで、ターボ機械部品の効率に革命をもたらしています。
3Dプリンターによるタービン部品の利点
成功事例
Material Solutions & Siemens - 革新的なプロジェクトで顕著な成果
Siemens、Material Solutions、EOSのコラボレーションは、3D金属プリンティングが「動く」アプリケーションでも妥協することなく実行可能な、信頼性と実績のある技術であることを示しています。注目すべきは、新しいタービンブレードの開発です。この部品は、Siemens NXと共同で開発され、EOSシステムで造形され、Material Solutionsで製造されました。
- 性能は13,000rpmまで向上
- 開発期間を75%短縮、リードタイムを50%短縮
- 周囲温度1,250 °Cまで使用可能
ブレード、燃料噴射装置、バーナー、燃焼室、クラッド、シール、ハウジング:エネルギー分野の部品を製造する場合、機能統合と耐熱性が寿命とプロセス選択の決定的な要因になります。これらの要素に対して、産業用3Dプリンティングは、従来の製造プロセスでは到達できなかった可能性を開きます。その用途は、3Dプリンターによるタービンブレード製作から革新的な修理ソリューションまで多岐にわたります。このページでは、私たちがどのようにお客様とともにターボ機械の新境地を切り開いたかについて詳しくご紹介します。
成功事例
Siemens - 機能を統合したバーナーフロント
Siemensは、機能統合を特徴とするバーナーフロントの製造にEOSシステムを採用しています - Siemens NXで再設計され、EOS M 400-4で量産されます。材料はEOSNickelAlloy HXです。
部品は単一ピースとして製造され、13の異なる部品はなくなりました。使用する材料が減るため、部品は大幅に軽量化され、リードタイムは26週間から3週間に短縮されました。金属の加熱が減るため、部品の寿命が延びます。
成功事例
Siemens - 3Dプリンティングに基づくメンテナンス管理の最適化
大規模なエネルギー発電プラントでは、修理やメンテナンス作業によるダウンタイムが大きなコスト要因となっています。特に、複雑で一体化されたチャンネルを持つ部品では、DMLSに基づくハイブリッド修理プロセスが、時間とコストを節約するユニークな方法を可能にします。どのように機能するのか?摩耗した部分が、元の部品上に直接再構築されます。これには広範な利点があります:
- 追加の溶接工程は不要
- 再構築された部分と元の部分とのつながりの質が向上
- 内部構造のアラインメントは維持される
困難な課題とスマートな解決策
カスタマイズされたEOSシステムにより、Siemensはガスタービンで高い熱応力を受けるバーナーチップの精密かつ迅速なメンテナンスプロセスの開発に成功しました。修理は磨耗した素材の上に直接造形するため、時間とコストを節約できます。
- 修理時間が90%短縮
- 修理プロセスが大幅に合理化された
- 技術的な改善は修理の際に取り入れることができる
Euro-K
新しいバーナーは、気体燃料と液体燃料を同じように効率的に使用できます。最適化された新しい形状は、アルコールを蒸留して作られるフーゼル油のような、燃焼が難しいとされる液体燃料の使用も可能にしました。また、バーナーの革新的な設計により、燃焼室のサイズを20%縮小できたこともプラスに働いています。

ターボ機械部品に必要なすべてをワンストップで提供
高温を含む多様なアプリケーションに対応できる、再現性の高い部品品質と幅広い材料ポートフォリオを備えた堅牢なシステムを提供しています。また、包括的な品質モニタリングのためのツールやソフトウェア、貴社のニーズに対応するコンサルティング部門も提供しています。