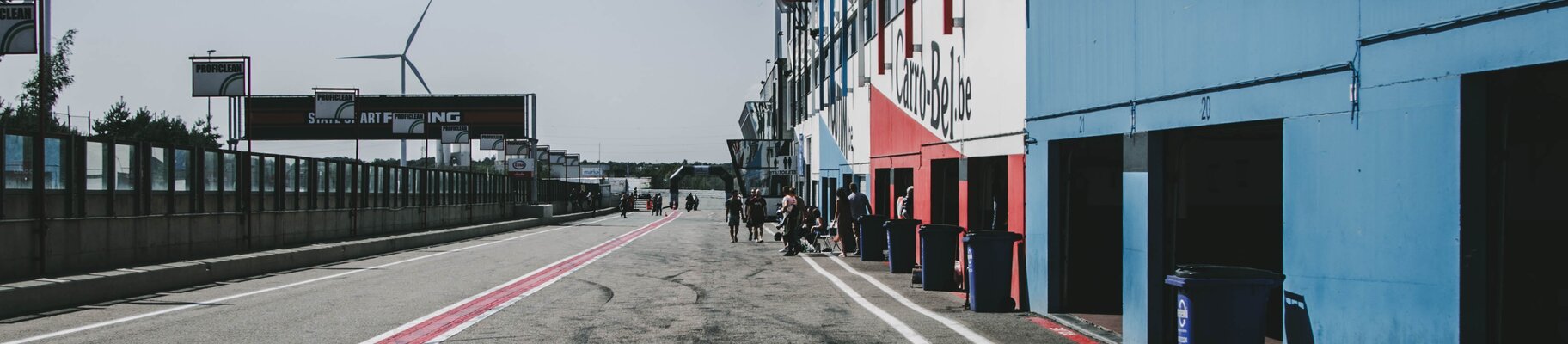
フォーミュラ学生チーム、バッテリー・ハウジングの3Dプリント・エアフローにEOS P 396 を使用
DHBW Engineeringシュトゥットガルト|成功事例
-
安全関連部品の迅速な整備を可能にする設計
-
部品重量を80%削減し、わずか77gに
-
冷却性能は前年の2倍以上
「EOSの専門的な知識と技術のおかげで、私たちの電動レーシングカーeSleek14をサーキットに導入し、素晴らしいタイムを記録することができました。アディティブ・マニュファクチャリングの利点は非常に説得力のあるものです。軽量部品、アイデアの迅速な実現、そしてこれらすべてが極めて少量の部品で可能なのです。利用可能な材料は、安全性が決して損なわれないことを意味します。EOSから受けた指導のおかげで、私たちはプロセスから最大限の力を引き出すことができました-そして、トラック上で自分たちの実力を証明しました。」
David Köhler|2013/2014年レースチーム・バッテリー開発副責任者
本気のパワー:アディティブ・マニュファクチャリングで製作されたフォーミュラ学生レースカーの冷却システム
DHBWエンジニアリング・シュトゥットガルト・チームに属するeSleek14は、それぞれ60馬力の電気モーターを2基搭載しています。このスピードマシンに供給される電力は、車体横方向に固定されたバッテリーから供給されます。空冷システムの構築は、アディティブ・マニュファクチャリングのエキスパートとしてEOSがサポートしました。
バッテリー・コンテナの開発では、個々のモジュール間の冷却チャンネルだけでなく、コンテナの端に最も効率的な方法で空気を外部に戻す冷却ダクトを実現することができました。 部品の重量に関する厳しい仕様を満たすため、チームは軽量なファインポリアミドPA2200を構造に採用しました。この素材は、高い剛性と優れた熱伝導性を特徴としており、モータースポーツ用途に最適な特性です。
エアダクトは、EOS P 396 を使って製造されました。レーザービームが粉末状の材料を層ごとに溶かし、最終的な部品を形成します。次のステップは、部品を車両にうまく組み込むことです。冷却ダクト部品の重量はわずか77g。

「私達は冷却ダクトを付加製造しようと決めました。そしてEOSの技術のおかげで、完全に自由な設計が可能でした。このような少量生産では、射出成形は意味がなく、いずれにせよ、構造設計を変更しなければならなかったでしょう。」
David Köhler|2013/2014年レースチーム・バッテリー開発副責任者
結果の概要
- -80% 軽量化
- 100 % パフォーマンス向上
EOS成功事例
EOSの30年にわたる3Dプリンティングのパイオニアとしての卓越性をご覧ください。