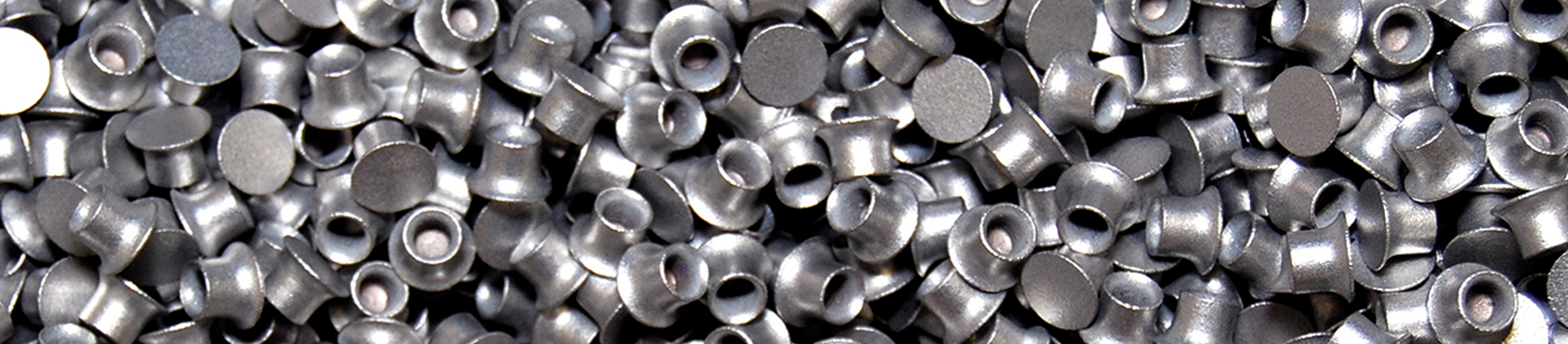
ボトルネックからブレークスルーへ:アトラスコプコの3Dプリントの旅
アトラスコプコ|ケーススタディ
生産効率の向上
- リードタイムを6~12週間からわずか3~4日に92%短縮
- 外部サプライヤー費用の削減と労働時間の短縮により、生産コストを30%削減。
- 材料廃棄物の削減 約7%からほぼゼロへ
- 突発的な注文や急を要する顧客要件への対応における敏捷性の向上
長いリードタイム、サプライチェーンの混乱、生産コストの上昇は、現代の製造業における共通の課題です。従来の方法では、柔軟性、スピード、効率に対する要求の高まりに対応できないことが多い。外注部品に依存している企業にとって、遅延や非効率はコストのかかる後退や機会損失につながる可能性があります。
産業用ソリューションのリーダーであるアトラスコプコは、自動車産業で使用されるセルフピアスリベットシステムに不可欠な部品であるリベットデリバリボウルの製造において、まさにこのような課題に直面していました。アトラスコプコは、社内で積層造形(AM)を採用することで、これらの障害を克服しただけでなく、大幅なコスト削減、廃棄物の削減、リードタイムの大幅な短縮を実現しました。EOSの EOS P 396とPA 2200ポリマー材料を使用することで、アトラスコプコは生産へのアプローチを変革しました。このケーススタディでは、積層造形によって測定可能な改善を実現し、製造戦略を再構築した方法を紹介します。

「EOSとの協力により、ターンキー・ソリューションが提供され、私たちのプロセスを適応させることができました。
アトラスコプコテクニカルマネジャー、Jason Edwards
課題
アトラスコプコは従来、自動車部門で広く使用されているセルフピアスリベットシステムの重要部品であるリベットデリバリボウルなどの部品を外部サプライヤに依存していました。このため、リードタイムが6~12週間と長くなり、製造コストが上昇し、サプライチェーンが複雑になっていました。さらに、従来の製造工程では約7%の材料廃棄が発生し、より持続可能なソリューションの必要性が浮き彫りになった。
「アトラスコプコのテクニカルマネジャー、ジェイソン・エドワーズは次のように述べています。「当社は、リードタイムの短縮、コストの削減、新製品の迅速なプロトタイプ作成につながる製造管理の強化を望んでいました。EOSとAdditive Mindsとの連携により、ターンキーソリューションが得られ、プロセスを適応させることができました。
ソート&フィード
3Dプリントされたボウルが効率的にリベットを供給し、自動化された製造工程を合理化する


ソリューション
このような課題に対処するため、アトラスコプコはEOSおよびそのコンサルタント部門であるAdditive Mindsと協力し、AM機能を社内に導入しました。アトラスコプコは、柔軟性と精度で知られるEOS P 396 3Dプリンタを選択し、ポリマー材料PA 2200を使用してリベットデリバリボールを製造しました。この移行により、アトラスコプコはサプライチェーンを合理化し、サードパーティサプライヤへの依存度を減らし、生産スケジュールをより厳密に管理できるようになりました。また、社内でのAMアプローチにより、迅速なプロトタイピングが可能になり、迅速な反復と設計の最適化が実現しました。
結果
アトラスコプコでは、社内での積層造形への移行により、画期的な成果が得られました。最も大きな改善の1つは、リードタイムが劇的に短縮されたことです。以前は、リベットのデリバリーボウルの製造に6~12週間を要していましたが、これは主に外部サプライヤに依存していたことと、従来の製造プロセスが複雑であったことが原因でした。EOS P 396 3Dプリンターの導入により、リードタイムはわずか3~4日に短縮されました。この改善により、生産需要への迅速な対応が可能になり、緊急の顧客要件にも柔軟に対応できるようになりました。
コスト削減も大きな成果でした。アトラスコプコは、外部サプライヤの必要性を排除し、作業工数を削減し、生産プロセス全体を合理化することで、生産コストを30%削減しました。積層造形の効率性により、段取り替え、セットアップの変更、サプライチェーン管理に関する費用が最小限に抑えられました。さらに、AMプロセスの精度と信頼性により、材料の無駄が大幅に削減されました。従来の製造方法では約7%の材料廃棄が発生していたが、新しいプロセスではこの数字がほぼゼロになった。この削減はコスト効率に貢献するだけでなく、資源消費を最小限に抑えることで持続可能性の目標もサポートした。
アトラスコプコは、アディティブマニュファクチャリングの採用を通じて、生産の俊敏性、コスト効率、環境面のメリットを向上させ、産業用途におけるAMの強力な可能性を実証しました。「AMは当社に変革をもたらしました。低コストで短いリードタイムで直接供給できるため、世界中で新しい契約を獲得しています。EOSでは、移行期間中ずっとサポートしてくれ、迅速なサポートを提供してくれるパートナーがいます。また、3Dプリンタで最高の結果が得られるよう、コンポーネントの設計についてアドバイスを続けてくれます」とアトラスコプコのテクニカルマネジャー、ジェイソン・エドワーズは締めくくります。
効率と信頼性
アトラスコプコは、社内で3Dプリントを行うようになったことで、必要なサードパーティ製部品の数が減り、サプライチェーンのリードタイムや輸送の遅れに制約されることがなくなりました。


「アディティブ・マニュファクチャリングは、私たちに大きな変革をもたらしました。直接、低コスト、短納期で供給できるため、世界中で新しい契約を獲得しています"
アトラスコプコテクニカルマネジャー、Jason Edwards
EOSケーススタディ
EOSの30年にわたる3Dプリンティングのパイオニアとしての卓越性をご覧ください。