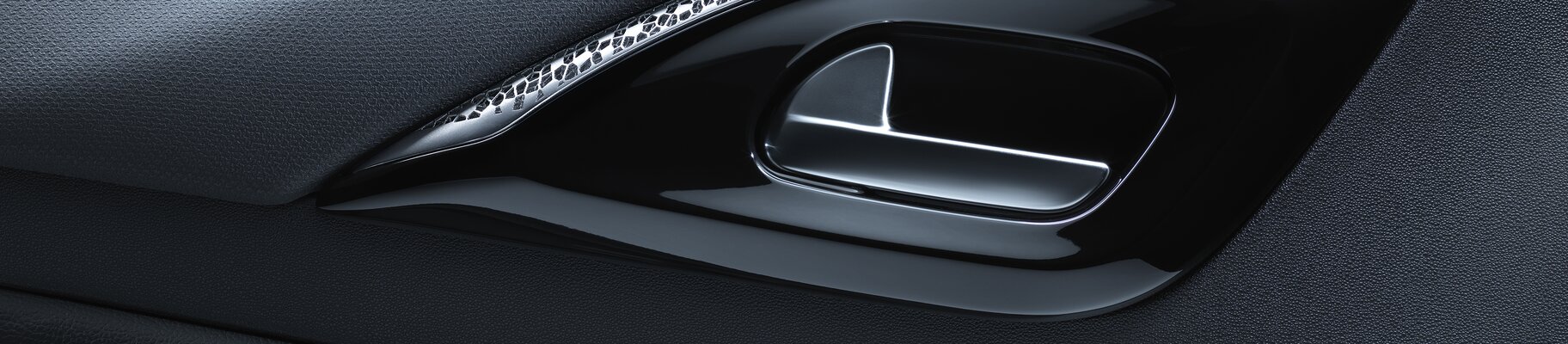
カスタマイズカーアクセサリーのためのアディティブ・マニュファクチャリング
Spartacus3D|成功事例
DS 3 Dark Side リミテッドエディション - アディティブ・マニュファクチャリングによる先進のイノベーション
自動車の分野では、売れ筋モデルの限定版は賢いマーケティング手法です。しかし、自動車メーカーは常に、市場セグメントにおいて競合他社と差別化する具体的な方法を模索しています
。PSAグループのブランドであるDSオートモビルズは、一連の象徴的なモデルのおかげで、数年でプレミアム・セグメントでの地位を確立することに成功しました。コンパクトモデルのDS 3は、このセグメントで広く認知され、定期的に限定モデルが発表されています。今回のダークサイド・エディションでは、DSオートモービルは通常の装備よりもさらに踏み込んで、3Dプリンターで製作したパーツを組み込むことで、革新への継続的な取り組みを強調したいと考えました。アディティブ・マニュファクチャリングは、DSのデザインチームに完全な創造的自由を与えただけでなく、Spartacus3Dの専門家がEOS M 290 のマシンで作業したおかげで、非常に迅速かつ簡単に製造および実装することができました。
「最初から最後まで、私たちの専門技術にとって挑戦的であると同時にエキサイティングな、とてつもないプロジェクトでした。これらのクルマが今、世界中にあることを想像するとわくわくします。そして、このプロジェクト全体を通して、EOSの信頼性、品質、サポートが頼りになることがわかっていました。」
Charles de Forges|マネージング・ディレクター|Spartacus3D

課題
ユニークなデザインと迅速な市場投入で、DS 3限定車用の高品質アクセサリーを製造する。
このプロジェクトは、DSデザインチームがDS 3限定モデルのインテリアを革新的に強化する方法を探し始めたところから始まりました。そのアクセサリーは、自動車メーカーの絶え間ない技術革新の追求を際立たせるとともに、プレミアムセグメントで要求される最高水準の品質を満たすものでなければなりませんでした。デザイナーは当初から、アディティブ・マニュファクチャリングの可能性を活用し、この分野で世界初となる作品を発表することを決めていました。アディティブ・マニュファクチャリングは、まったく新しいデザインの可能性を開きます;
DSオートモビルズは、DS 3に毎年いくつかの限定モデルを発表しています。デザインチームはまた、高級感があり、耐性があり、簡単で見栄えのする仕上げが可能な素材であるチタンを選びました。
しかし、自動車分野では3Dプリンティングがプロトタイピングに一般的に使用されているとはいえ、アディティブ・マニュファクチャリングによる量産は、特に金属部品ではまだ非常に珍しいものでした。そのため、DS Automobilesは、アディティブ・マニュファクチャリングの専門知識と、必要な生産量に対応できるだけの生産能力の両方を備えたパートナーを見つける必要がありました。目標は、世界中の市場に約700台の自動車を供給することでした。また、このプロジェクトでは、自動車の生産計画に合わせて、開発期間は限られたもので、市場投入の時期に関して非常に正確な目標が設定されていました。
各限定版には特定の価格目標があるため、すべての付加製造部品は全体の予算に収まるものでなければなりません。調査の結果、ドアハンドルとキーホルダーの2つの部品が選ばれました。
フランスの材料変換グループFariniaの子会社であるSpartacus3Dは、これらの要件をすべて満たしていました。同社は長年3Dプリンティングを使用しており、DSチームから提供された設計を生産に移すのに役立つアディティブ・マニュファクチャリングに関する非常に深い知識を持っていました。同社のEOS M 290マシンとEOS Titanium Ti64により、Spartacus3Dは、DS Automobilesが目指していたデザインと品質要件を満たすために必要なすべてのスキルと、プロジェクトを期限内に完了するために必要な生産能力と後処理能力を備えていました。
ソリューション
EOS M 290でEOSチタンTi64のパーツを量産
DSのデザインチームは、革新的なパラメトリック・デザインを用いて、ドアハンドルの内側カバーと電子キーホルダーのディテールを非常に複雑なチタンメッシュで作り上げ、DS Automobilesの革新性と品質へのこだわりを際立たせました。
品質、コスト、デザインの最適な妥協点を見つけるために、DSのデザインチームとSpartacus3Dとの間で何度も試行錯誤が必要でした。これには、複数のプロトタイプの製造も含まれましたが、これは1個の生産ロットで製造できるアディティブ・マニュファクチャリングにとって特に容易なものでした。
このプロセスの一環として、DSの設計チームは部品の仕上げも選択しました。最終的に、手作業による研磨で得られる魅力的なマット仕上げに落ち着きました。品質チームは、歪み、表面品質(気孔率や光沢など)、カッティングエッジの正確な受け入れ基準を定義しました。並行して、部品製造の最適化に着手しました;コストを削減するために、Spartacus3Dは最適な造形方向とサポート構造を決定するだけでなく、レーザー溶融戦略を独自に改良する必要がありました。チタンは、溶融プロセス中に残留応力が発生することが知られており、細長いドアハンドルカバーは、最大限の歪みが発生する可能性がありました。応力緩和のための熱処理を追加することは、コスト的に実行不可能でした;代わりに、このリスクを防ぐためにいくつかの特定のパラメータが使用されました。コストを削減する他の方法としては、バッチあたりの部品数を増やしたり、サポートの数を減らしたり、粉末の消費量や後処理時間などを減らすことが挙げられます。

Spartacus3Dのアディティブ・マニュファクチャリングに関する専門知識は、デザインエンジニアリングから3Dプリンティングの最適化まで、プロセスのあらゆる段階を通じて非常に貴重であり、製品開発のライフサイクルを短縮し、市場投入までの時間を短縮することにつながりました。最適な材料を選択することで、剛性を確保し、後処理後の最高の部品品質を保証することができました。「この非常に革新的なプロジェクトでDS Automobilesのパートナーに選ばれたことは光栄です。彼らのブランドは、長年にわたりフランスの自動車産業においてエレガンスとノウハウを忠実に体現してきました。これはまた、我々の努力が報われたことを意味し、Spartacus3Dが量産のための強力なソリューションを提供できることを示しています。私たちのワークショップにあるDMLSシステムを使えば、最高のパーツを製造できるとわかっていました」とSpartacus3Dのマネージング・ディレクター、Charles de Forges氏は語ります。
結果
Spartacus3Dの3Dプリンティングの専門知識のおかげで、DS設計チームの要件に最適化されたアディティブ・マニュファクチャリング戦略を開発することができました。パラメトリックデザインは、EOSテクノロジーの可能性をフルに活用しています。2つのパーツの非常に複雑なオリジナルデザインは、アディティブ・マニュファクチャリングによってほぼ1対1で製造することができ、複数のユニットを同時に製造できるように最適化されました。これにより、製造コストを最小限に抑えることができました。
EOSチタニウムTi64という素材は、製造後の仕上げも可能にし、ドアハンドルカバーとキーホルダーに光沢のある表面と高級感を与えました。その結果、DSオートモビルズの象徴であるフレンチ・エレガンス、革新性、プレミアムな高級感を完璧に融合させた、洗練されたデザインと非常に複雑な構造を持つ、ほとんど芸術としか言いようのない仕上がりとなりました。
1台に3個ずつ、合計2,000個を10回ほどで生産し、およそ2,000時間の製造時間を要しました。DSのデザインチームによるデザインの検証から最終部品の納品まで、プロジェクト全体はわずか数週間で完了しました。
DS Automobilesは、従来の製造の限界を超えることで、自動車分野でユニークなものを作り出すことができ、DS 3 Dark Sideが競合他社から際立つことを可能にしました。DSのデザインチームは、Spartacus3Dが提供した専門知識とEOSアディティブ・マニュファクチャリングソリューションの能力のおかげで、複雑なプロジェクトを短期間で管理することができました。

結果の概要
- コスト効率: 品質に影響を与えることなく、1回の造形ジョブで200パーツを生産
- 精密さ: 長さ30cmの薄型ドアハンドルカバーが直立時に歪まないよう、造形パラメータを改善。
- 高速:1部品あたりの生産時間は1時間未満
- デザインの自由度:3次元の複雑なチタンメッシュは、DSオートモビルズの革新性と高級感の要求に応える
EOS成功事例
EOSの30年にわたる3Dプリンティングのパイオニアとしての卓越性をご覧ください。