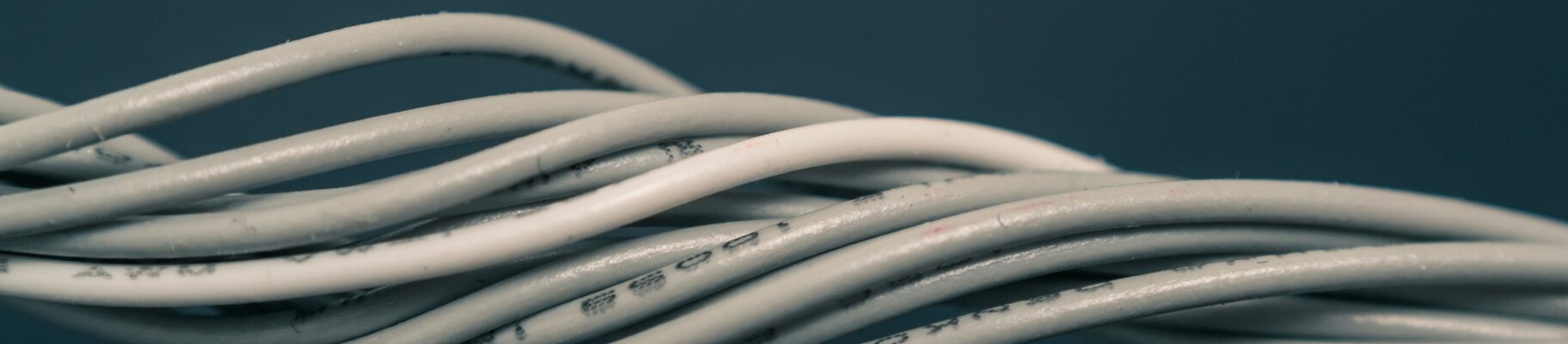
精度と安定性:FDR 3Dプリンティングが可能にする電気コネクターの未来
WAGO|ケーススタディ
卓越性の達成
- 数週間ではなく、数日でコンポーネントが入手可能な迅速な納品
- 最終製品とほとんど見分けがつかない一流の品質
- 最小限の後処理で効率化
- ディテールの解像度は
プロトタイプのラボテスト
電気がなければ、私たちの社会や経済はほとんど何も機能しない。住宅、工場、船舶、列車などの送電線は、私たちの時代のライフラインである。電子がエネルギーを運搬するためには、ケーブルを経由して適切な場所に到達しなければなりません。そのためには、東ヴェストファーレンにあるWAGO社のような信頼性の高い接続部品が必要です。カリフォルニアのIT拠点シリコンバレーにちなみ、同地のエレクトロニクスクラスターは「ターミナルバレー」とも呼ばれている。WAGOが証明しているように、その通りである:アディティブ・マニュファクチャリング(AM)の分野では、プロトタイプの製造に接続技術のプロトタイプ製造用の高解像度プロセス、いわゆるFDR(Fine Detail Resolution)を使用しています。このようにして、WAGOはPA 1101を使用したEOSFORMIGA P 110 FDR 新製品のスプリングクランプを非常に迅速かつ正確に試作することができました。

"人間にはモデルが必要だ。急速な進歩を望むなら、工業用3Dプリントを避けては通れない。私たちの主力製品です。通常の選択的レーザー焼結はすでに私たちを感心させましたが、FDRはその精巧さ、正確さ、スピードの点で一段と進化しています。."
オラフ・ゾシュケ|WAGO GmbH & Co.KG
課題
2本の導線を接続することは、最初は単純に聞こえるかもしれないが、詳細には技術革新、機能、安全性、品質に高い要求がある。電気が流れるところには、当然ながら正確な規制があります。接続は、実用上、事実上、法的な安全要件を満たさなければならない:「たとえ負荷がかかっていても、ケーブルが接点から抜け落ちるようなことがあってはなりません」とWAGO GmbH & Co.KGの試作品製造責任者であるOlaf Zoschke氏は説明します。「さらに、接触輪郭は適切な品質でなければなりません。もしこれが保証されていなければ、人身事故や物損事故が発生する可能性があります」。7人のチームとともに、設計および機能プロトタイプを作成し、社内外の研究所で機能テストと安全テストに合格しなければならないテストサンプルを作成します。
したがって、WAGOとその市場提携企業が開発する製品の安全性試験は、広範囲かつ頻繁に行われる。いくつかの課題を克服しなければなりません:家のメーター・ステーションであれ、鉄道車両の制御盤であれ、配電のためのスペースはますます狭くなっている。同時に、対応する製品を開発し、テストし、市場に投入するために利用できる時間はますます少なくなっている。「迅速であるためには、アディティブ・マニュファクチャリングは避けて通れない」とオラフ・ゾシュケは総括する。さらに、サンプルは最終的なシリーズ製品にできるだけ近いものでなければならない。テストエンジニアだけでなく、専門小売店やその他のバイヤーも納得させなければならないからだ。
ケーブルのストレインリリーフの設計は、可能な限り設置スペースを取らない新しいジャンクションボックスの開発において、特に難しいものでした:導線がソケットに挿入されると、しっかりと所定の位置にはめ込まれなければなりません。これはクランプ機構によって行われます。これはインターロックギアを介して所定の位置にロックされます。導体にかかる引張力は、絶縁体で固定されることにより吸収されなければならない。コンタクト自体に力がかかってはならない。サイズ要件を満たすために、タブに適用されるギアも可能な限り小さくなければならない。同時に、関連する安全規制を遵守するため、高度な安定性が要求される。連続生産では、従来の工程にかかるコストを大量に分散できるため、このような要件カタログを実施することができる。しかし、プロトタイプの製造ではどうだろう?
正確かつ迅速
3Dプリンティングによって、WAGOは非常に短期間で完全な機能を持つジャンクションボックスを開発し、市場に投入することができました。


ソリューション
"私たちは、初期テストや最適化の過程で、開発プロセス中にコンポーネントを自然に変更します。ここでは、積層造形が有利であることが知られています。しかし、なによりも、機能テストやラボテストのためには、一定のバッチサイズが必要です。10個から50個程度を想定していますが、もちろん、互いに完全に同等でなければなりません。例えば、微細な歯車装置に要求される高精度は、最近まで不可能でした」とオラフ・ゾシュケは説明する。工業用3Dプリンティングの利点を、非常に精巧な部品の用途に取り入れることができるようになったのは、FDRだけです」。
この時点で、FORMIGA P 110 FDR 使用した積層造形用の微細加工プロセスが最適な選択となります:コンポーネントが非常に小さいため、1パスで必要な数量を生産するのに必要なのは小さな造形チャンバーだけです。これはまた、プロトタイプの他の部品との「完璧なタイミングマッチ」を生み出します。要件に応じて、これらはより粗い選択的レーザー焼結(SLS)を含む他のプロセスで製造される。「例えば、大きなパーツ1では従来のSLSで十分ですが、小さなパーツ2ではFDRに頼っています。SLSは高解像度3Dプリンティングよりも高速ですが、パーツサイズが小さいため、ほぼ同じ時間でサンプルを得ることができます」とオラフ・ゾシュケは生き生きと説明する。
プロトタイピング・チームは、それぞれのケースでどのプロセスを使用するかを事前に決定します:CADプランニングの段階で、後の使用目的に応じて、材料と同様に決定されます。最終的に決定的に重要なのは、必要な品質を必要な数量でいかに合理的に提供できるかということです。こうして、オラフ・ゾシュケのチームは、それぞれの工程と素材の強みを具体的に活用することができる。「FDRは、精度、高いエッジの鋭さ、機能的な統合の黄金律であり、材料としてのPA1101はこれに非常に適している。さらに精度の高いプロトタイピング方法もあります。しかし、そこでは例えば機能的統合が欠けています。標準的なSLSはより高速ですが、精度は劣ります」と試作品製造の責任者は付け加える。
結果
WAGOは、ギアとプレートのサンプルを必要な時間内、必要な公差内、必要な数量だけ製造することに成功しました。このようにして、長寿命という点で後発のシリーズ製品に劣ることのない、耐久性のある部品が完成しました。製造と後処理に要した日数はわずか2日ほど。後処理といえば:積層造形用のFDRプロセスは解像度が高いため、その後の加工はほとんど必要なかった。
オラフ・ゾシュケはこのことを認めている:「EOS製品は、FDRなしでも常に非常に優れた品質を提供してくれました。EOS製品は、FDRがなくても常に非常に優れた画質を提供してくれました。ファインディテールレゾリューションを使えば、さらに良くなります。私たちは、プロトタイピングにおいて、後のシリーズのコンポーネントの約80%の品質という非常に優れた価値を達成しています。これは、私たちの製品開発者をも興奮させました。"SLSの高解像度技術が優れているもう一つの理由は、後処理にあります:このプロセスでは、凹凸を化学的に平滑化することもできる。これはわずかな "ぼかし "につながるため、FDRによる製造ほど正確ではない。
このようにして、WAGO製部品はサンプルテストに必要な製品特性も備えています:繊細なラグとその歯は、必要な強度を提供します。繊細なラグとその歯が必要な強度を提供すると同時に、高品質で製造されているため、シームレスにインターロックし、頑丈に固定されます。また、複数の内部および外部テストにより、積層造形部品が長持ちすれば、連続生産でも長持ちすることが証明されている。このように、革新的なFDRプロセスは、完全に統合された機能で、産業用3Dプリンティングの精度と速度をさらに向上させるという約束を守っている。
堅牢性と信頼性
3Dプリンティングは、最終製品とほとんど見分けがつかない一流の品質を提供できる
「EOS製品は、FDRなしでも常に非常に優れた品質を提供してくれました。私たちは、後処理によって常に素晴らしい結果を得てきました。ファインディテールレゾリューションを使えば、さらに良くなります。プロトタイピングでは、後のシリーズのコンポーネントの約80%の品質という非常に優れた価値を実現しています。これは、私たちの製品開発者をも興奮させています。"
オラフ・ゾシュケ|WAGO GmbH & Co.KG
EOSケーススタディ
EOSの30年にわたる3Dプリンティングのパイオニアとしての卓越性をご覧ください。