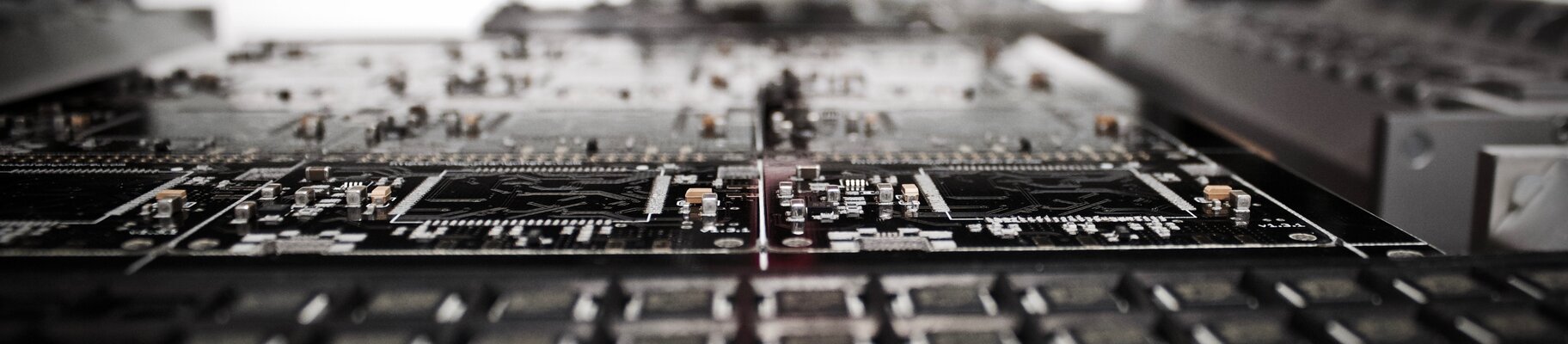
アディティブ・マニュファクチャリングによる多次元回路キャリア
ベータ・レイアウト|ケーススタディ
EOSテクノロジーで新しいプリント基板(PCB)を試作
2016年の初め、多くの人々がムーアの法則の終焉について書き、コンピューター・チップの性能はもはや2年ごとに倍増することはないだろうと予想していました。その理由は、プロセッサー自体の構造がすでに数ナノメートル以内に収まっているからです。これ以上の縮小は技術的見地からほぼ不可能である。性能を向上させ続けるために、メーカーは複数の構造層を重ねるアーキテクチャに取り組んでいる。同様のアプローチは、回路キャリアの分野でもすでに確立されている。ドイツのBeta LAYOUT GmbH社は、EOS技術を活用し、これらの革新的なキャリアのプロトタイプの製造とテストに成功している。
「アディティブ・マニュファクチャリング技術は、その多くの利点のおかげで、幅広い市場参加者に高い付加価値を提供しています。研究開発は当社のサービスを通じて利益を上げ、ひいては当社のビジネスモデルにも好影響をもたらします。これにより、多くのユーザーに先端技術のメリットを提供することができるのです。」
Manuel Martin|プロダクトマネージャー 3D-MID|Beta LAYOUT GmbH
課題
回路キャリアの個別プロトタイプの製造
回路キャリアや従来のプリント基板は、その上で動作するマイクロプロセッサの影に隠れてきました。これはいくぶん不公平です。なぜなら、もちろん、高性能な中枢神経系の恩恵がなければ、最高の頭脳を持っていてもほとんど役に立たないからです。マイクロエレクトロニクスの分野でも似たようなことが言えます。現代のほとんどすべての機器は、1つ以上のチップを組み込むために回路基板を必要とし、さらに必要な電気部品が追加されます。これにより、電気の供給から回路、信号の出力まで、さまざまなタスクを果たすネットワークが形成されるのです。
新しい機器では、従来の回路基板を設置できるスペースがごくわずかしかないことが多々あります。その理由のひとつは、多くの電子機器がますます小型化し、形自体が大きくなっても、実際の電子機器のためのスペースはほとんど残されていない傾向があるからです。既存の容積は、例えば、スクリーンの収容、より多くのインターフェイスや出力ポイント、さらに、より大きなバッテリーを収容するために必要となります。新しい回路を実験的に構築するには、シンプルな実験用PCBで十分だった時代は、今やほとんどの場合、そしてほとんどの分野でとっくに終わっています。利用可能な設置スペースと並んで、重量も重要な要素であり、コンパクトで3次元的に構成された回路基板は、ここでも重要な役割を担っています。
現代の電子製品では、回路が筐体内の限られたスペースを奪い合うことがよくあります。従来のようにPCBを積層すると、必要な部品をすべて収容することができなくなるため、前述の3次元回路キャリアが選択されるソリューションとなります。射出成形はプロトタイプを製造するにはコストがかかりすぎます。このためBeta LAYOUT社は、より安価で高性能な代替品を探すことにしました。
ソリューション
アディティブ・マニュファクチャリングほど、多層構造の要求に適した技術はありません。これは、レーザーを使って部品を層ごとに作り上げるからです。Beta LAYOUT社がこの技術に依存し、3Dプリンティングで製造されたプラスチック部品を使用しているのはこのためです。この技術革新は、プリンティング・プロセスの後に行われます;いったん製造されたモデルは、添加剤を使った特別なコーティングで仕上げられます。その後、いわゆる「レーザー・ダイレクト・ストラクチャリング」(LDS)がレイアウトを生成し、仕上げを活性化することで導体回路に変えることができます。
レーザーは物理化学反応を引き起こし、金属微粒子を生成すると同時に表面を粗くします。レーザーによる直接構造化の後、モデルは電流のない銅浴に入れられます。そこで、銅粒子が先に活性化された部分に蒸着され、導体トラックが作られます。銅被覆の後、導体トラックは電解めっきでさらに銅めっきを施すことも、直接表面仕上げを施すこともできます。この後、Beta LAYOUT社は社内の組立部門で個々の部品をユニットに追加します。完成した部品は、最初のプロトタイプやモデルとして機能し、機能テストや設計レイアウトのチェックが可能になります。
「私たちは、様々な企業のプロトタイプとして3D-MID(メカトロニクス統合デバイス)の製造を行っています。「EOSのFORMIGA P 110を使用することで、高品質の製品を迅速に顧客に提供することができます。特に実用的なのは、ウェブサイトやオンラインショップ経由の3Dモデルの注文にも対応できることです。アディティブ・マニュファクチャリングによって、私たちはビジネスモデルの拡大に成功しました。」とBeta LAYOUT 社の3D-MIDプロダクトマネージャーであるManuel Martin氏は説明します。

結果
アディティブ・マニュファクチャリングは、個人の開発者であろうと大企業であろうと、カスタムメイドの回路キャリアを新しい電子機器のプロトタイプに確実に使用できます。プラスチック部品は、迅速かつ魅力的な価格で製造できます。この工法では、必要なレベルの精度と高い部品品質が同時に得られるため、要求される基本ボディをすでにシリーズ製品に近いものとして製造することができます。
EOS技術はまた、高い柔軟性を提供します。使用されるマシンは、例えば、ガラスビーズを充填したPA 3200 GFや、アルミニウムを充填したポリアミドなど、様々な材料を処理することができます。 Alumide.PEEKのような高性能樹脂や様々な金属も利用できます。重要なのは、どの素材も高温に耐えられるということで、これは射出成形による量産の限界でもあります。
このような柔軟性により、Beta LAYOUT社は、例えば回路キャリアの特定の用途に対応することで、顧客の様々な個別要件を満たすことができます。このようにして、同社は、より低いコスト、より高い耐熱性、あるいはその他の特定の要件など、個別に最適化されたソリューションを開発することができます。
これらの利点に加えて、アディティブ・マニュファクチャリングにはもう一つの利点があります。「結局のところ、私たちがここで経験しているのは、先端技術の民主化なのです。このような技術革新がなければ、3D-MIDをサービスとして提供することはできなかったでしょう。それは、多くの中小企業や開発会社がそのようなプロトタイプを実現するチャンスがないことを意味します。その結果、話題になっている中小企業のイノベーションと創造力は勢いを失い、研究開発部門は活力を失ってしまうでしょう」とManuel Martinは言います。
アディティブ・マニュファクチャリングは、さらなる技術革新のための触媒であり、このように、おそらく新たなムーアの法則を確立するための出発点なのです。

結果の概要
- シンプル: 研究開発のための先端技術へのアクセス
- カスタマイズ: オーダーメイド製品のサービスプロバイダー
- 経済的:金型を使用しない生産によりコストを削減
EOSケーススタディ
EOSの30年にわたる3Dプリンティングのパイオニアとしての卓越性をご覧ください。