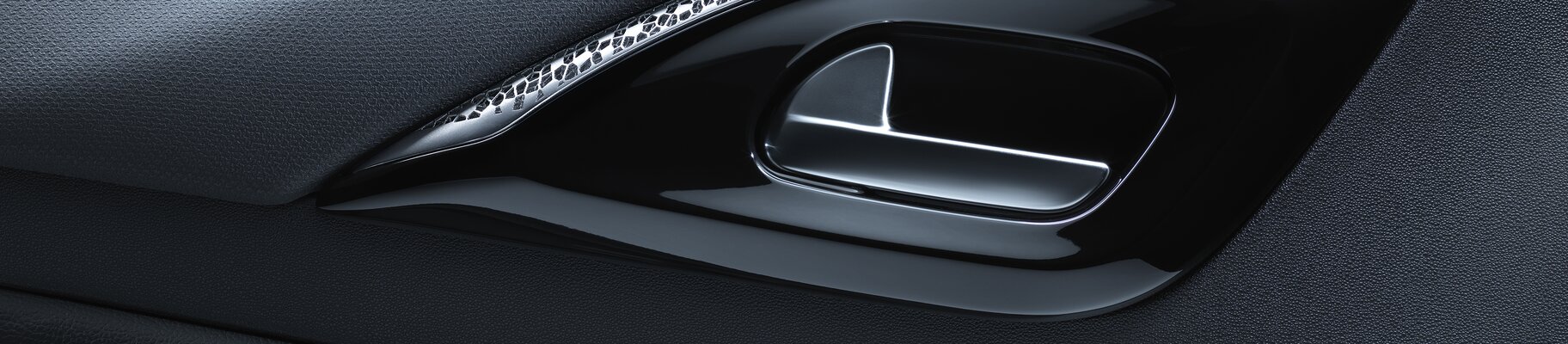
Additive Fertigung für maßgeschneidertes Autozubehör
Spartacus3D | Erfolgsgeschichte
DS 3 Dark Side Limited Edition - Fortschrittliche Innovation durch additive Fertigung
In der Automobilbranche sind limitierte Auflagen von Erfolgsmodellen ein kluger Marketingzug. Aber die Automobilhersteller suchen immer nach spezifischen Wegen, um sich von ihren Konkurrenten in ihren Marktsegmenten zu unterscheiden. DS Automobiles, eine Marke der PSA-Gruppe, hat es innerhalb weniger Jahre geschafft, sich mit einer Reihe von ikonischen Modellen im Premiumsegment zu etablieren. Das kompakte Modell DS 3 ist in diesem Segment weithin bekannt und wird regelmäßig in limitierter Auflage herausgebracht. Für die Dark Side Edition wollte DS Automobile über die übliche Ausstattung hinausgehen und 3D-gedruckte Teile verwenden, um ihr kontinuierliches Engagement für Innovation zu unterstreichen. Die additive Fertigung gab dem DS-Designteam völlige kreative Freiheit und ermöglichte dank der Spartacus3D-Experten, die mit einer EOS M 290 -Maschine arbeiteten, eine sehr schnelle und einfache Umsetzung und Produktion .
"Es war von Anfang bis Ende ein großartiges Projekt, das ebenso spannend wie herausfordernd für unser Know-how war. Wir sind begeistert, wenn wir uns vorstellen, dass all diese Autos jetzt auf der ganzen Welt unterwegs sind. Und während des gesamten Projekts wussten wir, dass wir auf die Zuverlässigkeit, die Qualität und den Support von EOS zählen können."
Charles de Forges | Geschäftsführer | Spartacus3D

Herausforderung
Herstellung von hochwertigem Zubehör für den DS 3 in limitierter Auflage mit einzigartigem Design und kurzer Markteinführungszeit
Das Projekt begann, als das DS Design-Team nach innovativen Verbesserungen für den Innenraum des DS 3 Limited Edition suchte. Die Accessoires sollten das ständige Streben des Automobilherstellers nach Innovation unterstreichen und gleichzeitig den höchsten Qualitätsansprüchen des Premiumsegments genügen. Von Anfang an beschlossen die Designer, das Potenzial der additiven Fertigung zu nutzen und eine Weltpremiere auf diesem Gebiet zu präsentieren. Die additive Fertigung eröffnet völlig neue Designmöglichkeiten;
DS Automobiles bietet jedes Jahr mehrere limitierte Editionen des DS 3 an, so dass diese neuen Optionen eine echte Neuerung für das Team darstellen. Das Designteam hat sich außerdem für Titan entschieden, ein Material, das einen Hauch von Luxus vermittelt, widerstandsfähig ist und eine einfache und gut aussehende Verarbeitung ermöglicht.
Doch während der 3D-Druck in der Automobilbranche häufig für Prototypen eingesetzt wird, ist die Serienproduktion mit additiver Fertigung immer noch sehr selten, insbesondere bei Metallteilen. Daher musste DS Automobiles einen Partner finden, der sowohl über Fachwissen im Bereich der additiven Fertigung als auch über ausreichende Produktionskapazitäten verfügt, um den Anforderungen des Unternehmens gerecht zu werden. Ziel war es, rund 700 Fahrzeuge weltweit auf den Markt zu bringen. Das Projekt hatte auch einen begrenzten Entwicklungszeitrahmen, der mit der Produktionsplanung des Fahrzeugs übereinstimmte, und sehr genaue Ziele in Bezug auf die Markteinführung.
Jede limitierte Auflage hat ein bestimmtes Preisziel, so dass alle additiv gefertigten Teile in das Gesamtbudget passen müssen. Die Untersuchungsphase führte zur Auswahl von zwei Teilen: dem Türgriff und dem Schlüsselhalter.
Spartacus3D, eine Tochtergesellschaft der französischen Materialtransformationsgruppe Farinia, erfüllte alle diese Anforderungen: Da das Unternehmen bereits seit Jahren 3D-Druck einsetzt, verfügt es über sehr gute Kenntnisse der additiven Fertigung, um die vom DS-Team vorgelegten Entwürfe in die Produktion umzusetzen. Mit der EOS M 290 und der EOS Titanium Ti64 verfügte Spartacus3D über alle notwendigen Kompetenzen, um die von DS Automobiles angestrebten Design- und Qualitätsanforderungen zu erfüllen, sowie über die erforderlichen Produktions- und Nachbearbeitungskapazitäten, um das Projekt fristgerecht zu liefern.
Lösung
Serienfertigung der Teile auf einer EOS M 290 in EOS Titanium Ti64
Das DS-Designteam verwendete ein innovatives parametrisches Design, um die inneren Türgriffabdeckungen und das Detail des elektronischen Schlüsselhalters aus einem sehr komplizierten Titangeflecht zu gestalten, was die Innovation und das Qualitätsbewusstsein von DS Automobiles unterstreicht.
Um den besten Kompromiss zwischen Qualität, Kosten und Design zu finden, waren viele Iterationen zwischen dem DS-Designteam und Spartacus3D erforderlich. Dazu gehörte auch die Herstellung mehrerer Prototypen, was bei der additiven Fertigung in einer einzigen Produktionscharge besonders leicht möglich ist.
Im Rahmen dieses Prozesses wählte das DS-Designteam auch die Oberfläche der Teile aus und entschied sich schließlich für eine attraktive matte Oberfläche, die durch manuelles Polieren erzielt wurde. Das Qualitätsteam legte genaue Abnahmekriterien für die Verformung, die Oberflächenqualität (z. B. Porosität und Glanz) und die Schnittkanten fest. Parallel zu diesem Hin und Her arbeitete Spartacus3D auch an der Optimierung der Produktion der Teile. Um die Kosten zu senken, musste Spartacus3D nicht nur die beste Ausrichtung und Stützstruktur bestimmen, sondern auch die firmeneigene Laserschmelzstrategie verfeinern. Es ist bekannt, dass Titan während des Schmelzvorgangs einige Eigenspannungen erzeugt, und die lange und dünne Türgriffabdeckung war ein guter Kandidat für maximale Verformung. Eine zusätzliche Wärmebehandlung zum Spannungsabbau war aus Kostengründen nicht möglich; stattdessen wurden einige spezifische Parameter verwendet, um dieses Risiko zu vermeiden. Andere Möglichkeiten, die Kosten zu senken, bestehen darin, die Anzahl der Teile pro Charge zu erhöhen oder die Anzahl der Auflagen, den Pulververbrauch, die Nachbearbeitungszeit usw. zu verringern.

Das Fachwissen von Spartacus3D im Bereich der additiven Fertigung war in jedem Schritt des Prozesses von unschätzbarem Wert, von der Konstruktion bis zur Optimierung des 3D-Drucks, was zu kürzeren Produktentwicklungszyklen und schnellerer Markteinführung führte. Die Auswahl des optimalen Materials trug dazu bei, die Steifigkeit zu gewährleisten und eine maximale Teilequalität nach der Nachbearbeitung sicherzustellen. "Es ist ein Privileg, als Partner von DS Automobiles für dieses sehr innovative Projekt ausgewählt worden zu sein. Ihre Marke steht seit Jahren für Eleganz und Know-how in der französischen Automobilindustrie. Dies bedeutet auch, dass unsere Bemühungen belohnt werden und zeigt, dass Spartacus3D in der Lage ist, robuste Lösungen für die Serienproduktion anzubieten. Mit den DMLS-Systemen, die wir in unserer Werkstatt haben, wussten wir, dass wir in der Lage sein würden, die besten Teile zu produzieren", sagt Charles de Forges, Geschäftsführer von Spartacus3D.
Ergebnisse
Dank des 3D-Druck-Know-hows von Spartacus3D war es möglich, eine additive Fertigungsstrategie zu entwickeln, die für die Anforderungen des DS-Designteams optimiert war. Der parametrische Entwurf schöpft das Potenzial der EOS-Technologie voll aus: Der sehr komplexe ursprüngliche Entwurf der beiden Teile konnte dank der additiven Fertigung fast eins zu eins hergestellt werden und wurde so optimiert, dass mehrere Einheiten gleichzeitig gefertigt werden konnten. Dadurch wurden die Produktionskosten auf ein Minimum reduziert.
Das Material, EOS Titanium Ti64, ermöglichte auch eine Nachbearbeitung, die den Türgriffabdeckungen und dem Schlüsselhalter eine glänzende Oberfläche und einen hochwertigen Look verlieh. Das Ergebnis könnte man fast als Kunst bezeichnen, mit einem eleganten, raffinierten Design und einer sehr filigranen Struktur, die französische Eleganz, Innovation und Premium-Exklusivität perfekt vereint - alles, wofür DS Automobiles steht.
Es gab etwa 10 Produktionsläufe mit insgesamt 2.000 Teilen - 3 Stück in jedem Auto -, für die etwa 2.000 Fertigungsstunden benötigt wurden. Das gesamte Projekt wurde in nur wenigen Wochen abgeschlossen, von der Validierung des Designs durch das DS-Designteam bis zur Lieferung der endgültigen Teile.
DS Automobiles war in der Lage, etwas Einzigartiges im Automobilsektor zu schaffen, indem die Grenzen der traditionellen Fertigung überschritten wurden, wodurch sich der DS 3 Dark Side von seinen Mitbewerbern abheben konnte. Das DS-Designteam war in der Lage, ein komplexes Projekt in sehr kurzer Zeit zu bewältigen - dank der Expertise von Spartacus3D und den Möglichkeiten der additiven Fertigungslösungen von EOS.

Die Ergebnisse auf einen Blick
- Kosteneffizient: Produktion von 200 Teilen pro Bauauftrag ohne Qualitätseinbußen
- Präzise: Verbesserung der Prozessparameter zur Vermeidung von Verformungen der 30 cm langen und dünnen Türgriffabdeckung beim aufrechten Bauen
- Schnell: weniger als eine Stunde Produktionszeit pro Teil
- Designfreiheit: Dreidimensionales, filigranes Titangewebe erfüllt die Anforderungen von DS Automobiles an Innovation und Premium-Exklusivität
EOS-Erfolgsgeschichten
Erleben Sie drei Jahrzehnte Pionierarbeit im 3D-Druck mit EOS