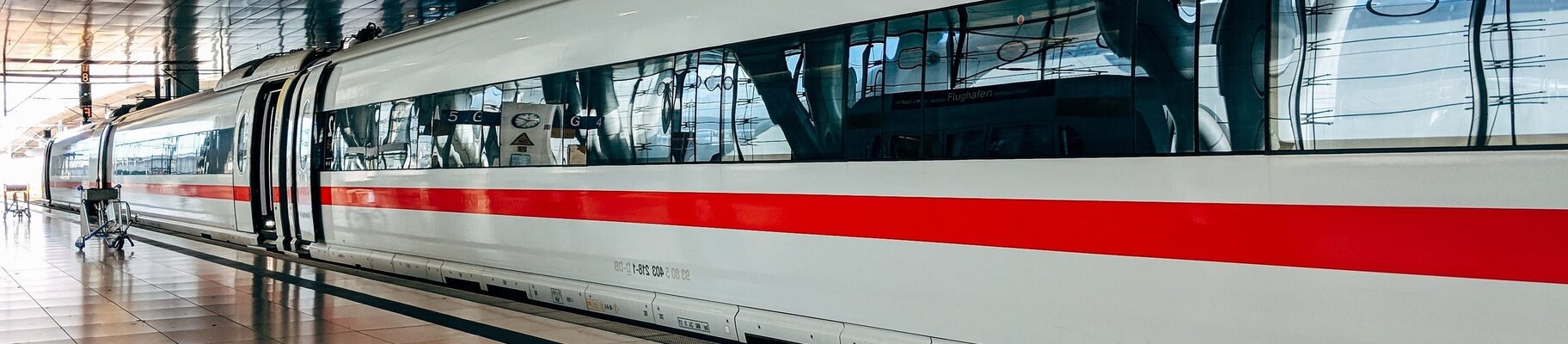
Der schnelle Weg zu 3D-gedruckten, individuellen Zugteilen mit additiver Fertigung von EOS
Hasenauer & Hesser | Erfolgsgeschichte
Deutsche Bahn wählt Additive Manufacturing für die Instandhaltung ihrer Züge
Die ICE-Flotte der Deutschen Bahn umfasst knapp 160 Züge der dritten Generation aus verschiedenen Baureihen. Jeder einzelne von ihnen sieht noch modern aus und fühlt sich auch so an - dank stilvollem Design und regelmäßig aufgefrischtem Interieur. Trotzdem gilt in der Verkehrsbranche alles, was vor 1996 gebaut wurde, als Youngtimer. Wie bei Autos aus dieser Zeit ist es auch bei diesen Zügen schwierig, Ersatzteile zu finden. Doch die Deutsche Bahn lässt sich nicht beirren und setzt auf die industrielle 3D-Drucktechnologie von EOS.

"Der enorme Vorteil der additiven Fertigung besteht darin, dass wir immer neuwertige Ersatzteile herstellen können, so dass wir unsere Züge über Jahrzehnte hinweg instand halten können. Wir müssen keine Kompromisse bei der Qualität oder Leistung eingehen. Außerdem sind die Kosten niedriger als bei kundenspezifischen Formen."
Florens Lichte | Leiter 3D-Druck | DB Fahrzeuginstandhaltung GmbH
Herausforderung
ICE-Züge der dritten Generation sind etwas abschreckend. Bei einem Leergewicht von 270 Tonnen bis weit über 400 Tonnen und einer Fahrgeschwindigkeit von 140 bis 190 Meilen pro Stunde wird die Vielzahl der Komponenten an Bord jedes Zuges leicht übersehen. Die kleinsten Bauteile sind oft die schwierigsten. Während handelsübliche Schrauben leicht zu ersetzen sind, können viele andere kleine Sonderanfertigungen nicht einfach beim Hersteller nachbestellt werden, wenn sie abgenutzt sind oder ausfallen. Bei einigen Teilen wurde die Produktion eingestellt, bei anderen sind die Hersteller zahlungsunfähig. Von jedem Teil werden in der Regel nur wenige Exemplare benötigt. Hohe Werkzeugkosten und Mindestabnahmemengen machen die Herstellung mit herkömmlichen Methoden unwirtschaftlich.
Eine Charge von 160 Stück ist winzig im Vergleich zu Aufträgen im industriellen Maßstab. Im Vergleich dazu werden jährlich Hunderttausende von mittelgroßen Fahrzeugen hergestellt; selbst bei Flugzeugen können die jährlichen Produktionszahlen für erfolgreiche Kurz- und Mittelstreckenmodelle mehrere Tausend erreichen.
Dies ist zwar ein Beweis für die Nachhaltigkeit von Zügen als Transportmittel, aber die kleinen Produktionsmengen erschweren die Produktion und Lagerlogistik von Ersatzteilen. Ähnliche Probleme treten auch bei vielen anderen speziell angefertigten Komponenten auf. In dem hier betrachteten konkreten Beispiel wurden Ersatzteile für einige sehr empfindliche Leuchtstoffröhrenhalterungen für die Anzeigeleuchten im elektronischen Bordinformationssystem der ICE-3- und ICE-T-Züge benötigt. Auf den Monitoren werden den Fahrgästen Informationen über die Geschwindigkeit, die Tageszeit und den nächsten Bahnhof angezeigt.
Im Laufe der Zeit werden die 9,4 x 0,4 x 0,3 Zoll großen Spritzgussteile durch normalen Verschleiß und Versprödung allmählich geschwächt, so dass sie alle 10 bis 15 Jahre ersetzt werden müssen. Schienenfahrzeuge sind für eine Lebensdauer von mehr als 25 Jahren ausgelegt, aber es ist nicht ungewöhnlich, dass ein Zug 40 bis 50 Jahre in Betrieb bleibt, in Ausnahmefällen sogar länger. Trotzdem hat der Lieferant beschlossen, diese Teile auslaufen zu lassen. Pro Jahr werden etwa 40 Stück benötigt. Das damit betraute Instandhaltungsunternehmen, das Elektronikzentralwerk (EZW) in München, machte sich auf die Suche nach Alternativen oder Partnern, die Antworten haben könnten. Diese Suche führte die Bahntechnik-Experten direkt zur additivenFertigung und den damit verbundenen Möglichkeiten.

Lösung
Die Technologie der additiven Fertigung ist die perfekte Lösung, da es sich um kleine Losgrößen handelt. Sie erfordert keine umfangreichen Vorbereitungsarbeiten, z. B. zum Einrichten der Fertigungswerkzeuge. "Nach unserer Erfahrung würde eine Lösung, die auf einer gleichwertigen Aluminiumform und manueller Entnahme beruht, mehrere Tausend Euro kosten, selbst wenn man die Handhabungs- und Einrichtungskosten für jeden Auftrag sowie die jährlichen Lager- und Wartungskosten für die Formen nicht mit einbezieht. Außerdem würde die Herstellung der Formen etwa drei Monate dauern, und die ersten Muster würden danach noch einmal einen Monat in Anspruch nehmen", erklärt Florens Lichte, Leiter des Bereichs 3D-Druck bei der DB Fahrzeuginstandhaltung GmbH.
Möchte ein Unternehmen ein Bauteil additiv fertigen, muss es weder eigene industrielle 3D-Drucker anschaffen noch eigenes Know-how aufbauen - das Geschäftsmodell der Auftragsfertiger kommt allen zugute. Diesen Weg hat auch die Deutsche Bahn gewählt. Ihr Logistikunternehmen hat nun schon mehrfach erfolgreich mit der Hasenauer & Hesser GmbH zusammengearbeitet. Doch der Teufel steckte im Detail, verrät Hans-Jörg Hesser, Geschäftsführer der Hasenauer & Hesser GmbH: "Unser oberstes Ziel war es, die Funktionalität des Bauteils zu erhalten. Dazu mussten die Spezifikationen des Bauteils überarbeitet und an das schichtweise Herstellungsverfahren angepasst werden. 3D-Druck ist normalerweise einfach, aber dieses Projekt erforderte enorme Erfahrung. Das in den ICE-Zügen verwendete Bauteil ist lang, schmal und dünnwandig. Aus diesem Grund verzieht es sich unglaublich leicht. Die Positionierung der Teile innerhalb der Baukammer war von entscheidender Bedeutung, zumal wir für diesen Auftrag über 200 Vorrichtungen gleichzeitig herstellen wollten."

"Wir verfügen über mehr als 10 Jahre Erfahrung in der additiven Fertigung und verwenden EOS-Systeme, so lange wir denken können. Wir sind begeistert von der Qualität der Bauteile und der Zuverlässigkeit der Systeme. Sie ermöglichen es uns, erstklassige Ersatzteile rechtzeitig an unsere Kunden zu liefern."
Hans-Jörg Hesser | Geschäftsführer | Hasenauer & Hesser GmbH
Ergebnisse
Die Vorrichtungen wurden mit der FORMIGA P 110 gebaut. Da weder 3D-CAD-Daten noch Konstruktionszeichnungen zur Verfügung standen, entstanden durch den Re-Engineering-Schritt Kosten im unteren vierstelligen Bereich. Die Herstellungskosten lagen damit über 80 % unter denen des Spritzgusses. Insgesamt benötigte das Projekt vom Start bis zur ersten Lieferung einen Monat, so dass die 3D-gedruckten Teile viermal schneller verfügbar waren. Eventuelle Nachbestellungen konnten innerhalb von 24 Stunden erledigt werden. Mitarbeiter des EZW München testeten die gedruckten Teile selbst vor Ort auf Form, Passform und Funktion. Das Ergebnis war überzeugend: Die additiv gefertigten Vorrichtungen erfüllten jede einzelne Anforderung des Kunden. "Die Teile waren passgenau und haben sich nicht verzogen. Wir haben bereits mindestens 20 Stück eingebaut", ergänzt Florens Lichte.
Für Lichte und seine Kollegen in Deutschland ging es jedoch um mehr als nur um das Bestehen der Funktionsprüfungen. Alle Kunststoffe, die für den Einsatz in der Eisenbahnindustrie bestimmt sind, müssen die in EN 45545-2 / DIN 5510-2 (für bestehende Fahrzeuge) festgelegten Brandschutzanforderungen erfüllen. Je nach Bauteilgröße, Gewicht, Lage im Fahrzeug und Abstand zu anderen Bauteilen gibt es unterschiedliche Anforderungen und zum Teil zusätzliche Ausnahmen. Das für dieses Projekt ausgewählte EOS-Material PA 2210 FR musste umfangreichen Brandtests unterzogen werden, um sicherzustellen, dass es die spezifischen Anforderungen seines Einsatzzwecks erfüllt. Diese neuen Teile halten die Fahrgäste nicht nur auf dem Laufenden, sondern sorgen auch für ihre Sicherheit, wenn sie mit halsbrecherischer Geschwindigkeit über die Gleise rasen.
Die Ergebnisse auf einen Blick
- 75 % Verkürzung der Produktionszeit
- 80 % Senkung der Produktionskosten
EOS-Erfolgsgeschichten
Erleben Sie drei Jahrzehnte Pionierarbeit im 3D-Druck mit EOS