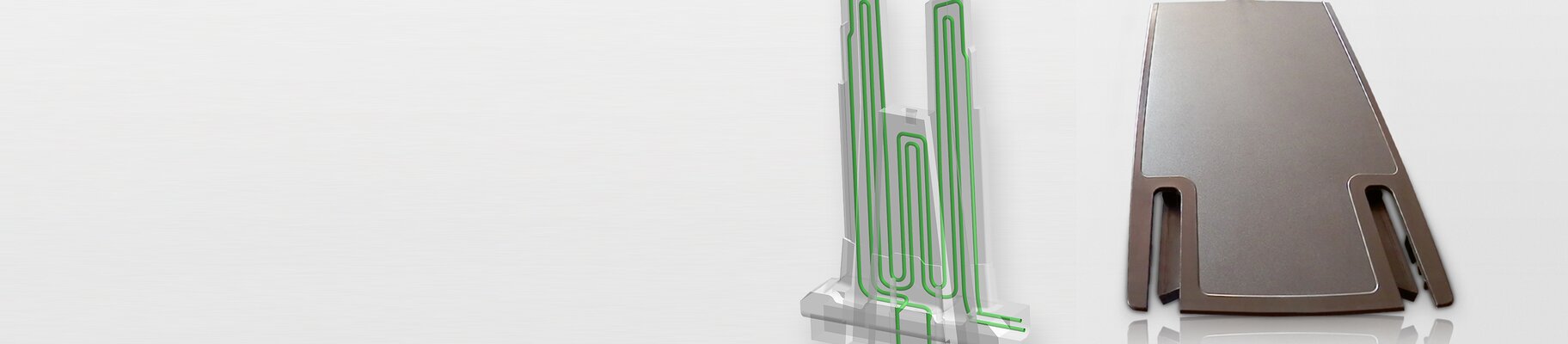
Additive Fertigung für konforme Kühlung nutzen
Effizienzsteigerung durch 3D-Druck von Metall
Innomia | Erfolgsgeschichte
-
Kostensenkung durch 17 % kürzere Zykluszeiten bei den Kunststoff-Spritzgussteilen
-
Verlängerung der Wartungsintervalle für Produktionsanlagen von zwei auf fünf oder sechs Wochen
-
Gleichmäßige Abkühlung verhindert Verformung des plastischen Endprodukts
Metall-3D-Druck für konturnahe Kühlung
Innomia setzt EOS 3D-Drucker ein, um den Produktionsprozess für spritzgegossene Kunststoffteile zu optimieren. Dabei ging es um eine Überarbeitung des Kühlprozesses. Der Fall betrifft die Herstellung der Armlehne zwischen den Vordersitzen.

Warum konforme Kühlung?
Die Wärmeenergie des flüssigen Grundmaterials muss durch das gesamte Fertigungswerkzeug abgeführt werden, damit der Kunststoff erstarren kann. Der Abkühlungsprozess entscheidet unter anderem über die Qualität des Bauteils. Denn eine ungleichmäßige Wärmeableitung kann zu Verformungen führen. Als logische Konsequenz begannen die Konstrukteure von Innomia mit der Entwicklung eines neuen Kühllösungssystems für Werkzeugeinsätze. Die optimierte Abführung der im Produktionsprozess entstehenden Wärme stand dabei ganz oben auf der Prioritätenliste.
Das Team entschied sich für integrierte Präzisionskühlkanäle, eine konforme Kühlung, eine bewährte Anwendung der DMLS-Technologie und eine der Lösungen, die nur Additive Manufacturing-Verfahren bieten können. Der EOS Metall-3D-Drucker, ein seit vielen Jahren bewährtes System, wurde für Innomia eingesetzt.
Die Präzisionskühlung und die Fertigung mittels Additive Manufacturing Technologie haben die gewünschten Ergebnisse gebracht. Die Temperaturverteilung und die damit verbundene Wärmeabfuhr sind nun wesentlich homogener. Da sich die Wärme verteilt und sowohl das Werkzeug als auch das Bauteil schneller verlässt, reicht eine Wassertemperatur von 60 °C zur Kühlung aus - das reduziert den Energiebedarf. Die Oberfläche der Wendeschneidplatte selbst erwärmt sich nicht über 90 °C, eine Tatsache, die es den Ingenieuren außerdem ermöglichte, die Feuchtigkeitsprobleme in der Umgebung zu lösen.
Dank Innomia und der EOS 3D-Drucktechnologie profitiert der Innomia-Kunde Magna von einem auf fünf bis sechs Wochen verlängerten Wartungsintervall. Das Problem der Luftfeuchtigkeitskondensation und möglicher Hohlraumkorrosion wurde vollständig gelöst. Die gleichmäßigen Kühlkanäle funktionieren so gut, dass der Zeitbedarf für den Produktionszyklus nun 17 % niedriger ist als zuvor.
"Das Problem der Kühlung war etwas, mit dem wir uns schon lange beschäftigen wollten. Wir wussten, wie ein verbessertes Produkt aussehen müsste, aber es war einfach nicht möglich, es herzustellen. Mit der additiven Fertigung ist uns der Durchbruch gelungen. Wir konnten die Kühlkanäle genau so planen, wie wir sie haben wollten, und dann den Formkern entsprechend herstellen. Der Laser verschmilzt das Metallpulver Schicht für Schicht, so dass praktisch jede Form möglich ist. Das Ergebnis hat uns auf allen Ebenen überzeugt. Wartung, Qualität des Endprodukts, Kosten, Wärmeableitung - es war das perfekte Projekt."
Pavel Strnadek | Leiter der Werkzeugwartung | Magna
Die Ergebnisse auf einen Blick
-
-17% Zykluszeit
-
Senkung der Kosten
-
Die Wartung der Produktionsanlagen wurde von alle 2 Wochen auf alle 5 oder 6 Wochen ausgedehnt.
"Die Automobilindustrie in Europa ist einem harten Wettbewerb ausgesetzt. Diese Tatsache wirkt sich natürlich auch auf Zulieferer wie Magna aus. Deshalb ist es für uns sehr wichtig, nach höchsten Qualitätsstandards zum niedrigsten Preis produzieren zu können. Mit der Optimierung unserer Produktionsanlage durch die verbesserte Kühlung unserer Werkzeuge haben wir ein Paradebeispiel dafür geschaffen, wie Technologie zur Effizienzsteigerung beitragen kann. Wir haben die Wartungskosten für unsere Produktionsanlage gesenkt, die Qualität unserer Bauteile optimiert und die Zahl der Produktionszyklen erhöht. So konnten wir das Qualitätsversprechen, das wir unserem Kunden gegeben haben, einhalten und gleichzeitig unsere eigenen hohen Ansprüche an die Kosteneffizienz erfüllen."
Lubos Rozkosny | CEO | Innomia
EOS-Erfolgsgeschichten
Erleben Sie drei Jahrzehnte Pionierarbeit im 3D-Druck mit EOS