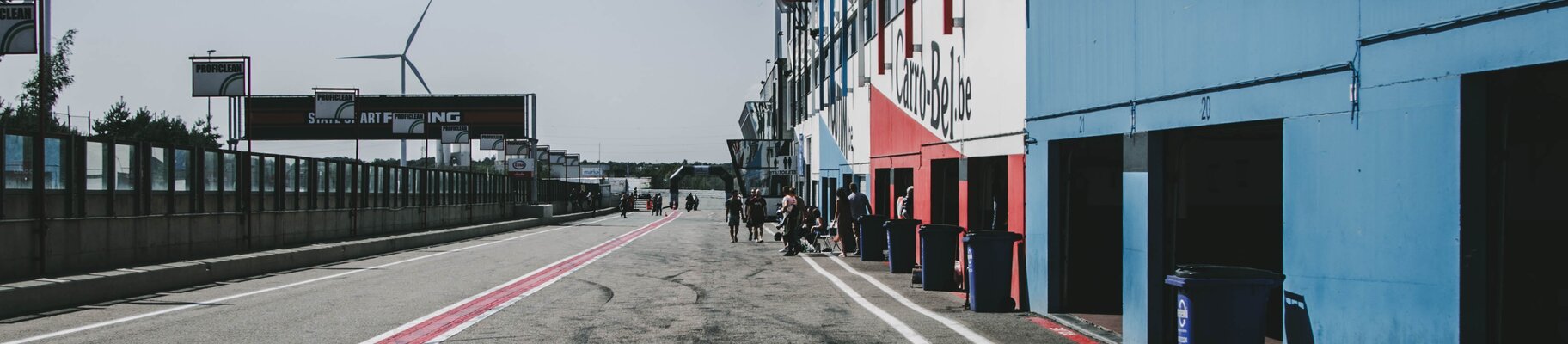
Formula Student Team nutzt EOS P 396 für 3D-gedruckten Luftstrom im Batteriegehäuse
DHBW Engineering Stuttgart | Erfolgsgeschichte
-
Konstruktion ermöglicht die schnelle Wartung von sicherheitsrelevanten Teilen
-
Reduktion des Bauteilgewichts um 80 % auf nur noch 77 g
-
Mehr als doppelt so hohe Kühlleistung im Vergleich zum Vorjahresfahrzeug
"Das Fachwissen und die Technologie von EOS haben uns wirklich geholfen, unseren elektrisch angetriebenen Rennwagen eSleek14 auf die Strecke zu bringen und tolle Zeiten zu fahren. Die Vorteile von Additive Manufacturing sind sehr überzeugend: leichte Bauteile, schnelle Umsetzung von Ideen und das alles bei extrem kleinen Stückzahlen. Durch die zur Verfügung stehenden Materialien wird die Sicherheit nicht beeinträchtigt. Dank der Anleitung von EOS konnten wir das Maximum aus dem Prozess herausholen - und uns auf der Rennstrecke beweisen."
David Köhler | Stellvertretender Leiter der Batterieentwicklung für das Rennteam 2013/2014
Ernste Leistung: Kühlsystem für Formula Student-Rennwagen mit additiver Fertigung hergestellt
Der eSleek14 des Teams DHBW Engineering Stuttgart hat zwei Elektromotoren mit je 60 PS. Der Strom, der diesen Flitzer speist, kommt aus Batterien, die seitlich im Fahrzeug angebracht sind. Die Konstruktion des Luftkühlsystems wurde von EOS als Additive Manufacturing Experte unterstützt.
Bei der Entwicklung des Batteriecontainers konnten nicht nur die Kühlkanäle zwischen den einzelnen Modulen realisiert werden, sondern auch ein Kühlkanal, der die Luft am Ende des Containers möglichst effizient wieder nach außen leitet. Um die strengen Vorgaben für das Bauteilgewicht zu erfüllen, wählte das Team für die Konstruktion das leichte Feinpolyamid PA 2200. Dieses Material zeichnet sich durch seine hohe Steifigkeit und gute Wärmeleitfähigkeit aus - perfekte Eigenschaften für den Einsatz im Motorsport.
Der Luftkanal wurde mit dem EOS P 396 hergestellt, wobei der Laserstrahl das pulverförmige Material Schicht für Schicht zum fertigen Bauteil aufschmolz. Auch das Gewicht entsprach den gewünschten Kriterien: Das Bauteil des Kühlkanals wiegt nur 77 g.

"Wir haben uns für die additive Fertigung des Kühlkanals entschieden und hatten dank der Technologie von EOS völlige Gestaltungsfreiheit. Bei so geringen Stückzahlen machte Spritzguss keinen Sinn, und wir hätten ohnehin Änderungen an der Konstruktion vornehmen müssen.
David Köhler | Stellvertretender Leiter der Batterieentwicklung für das Rennteam 2013/2014
Die Ergebnisse auf einen Blick
- -80 % Gewichtsreduzierung
- 100 % Leistungsverbesserung
EOS-Erfolgsgeschichten
Erleben Sie drei Jahrzehnte Pionierarbeit im 3D-Druck mit EOS