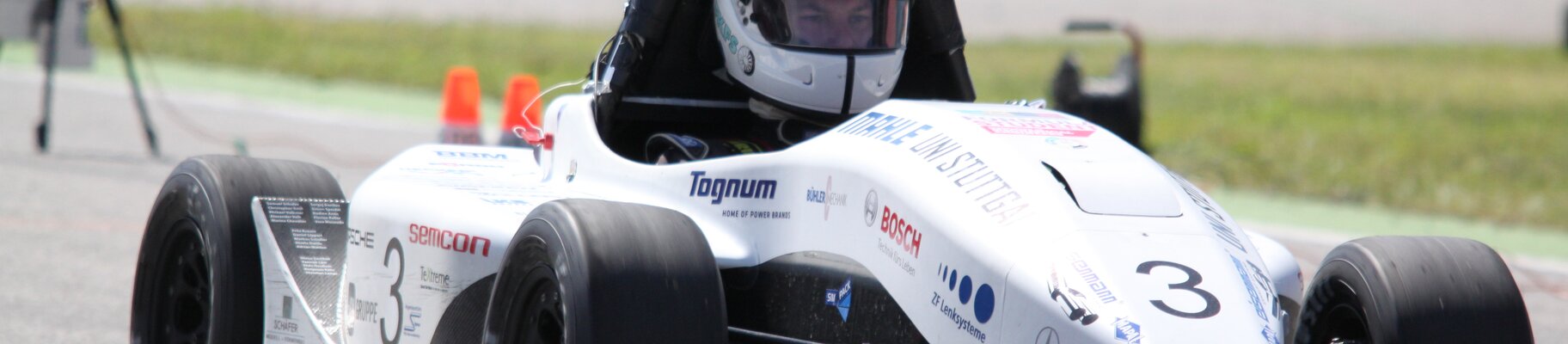
Junge Ingenieure entscheiden sich für die additive Fertigung, um das Potenzial des Teils voll auszuschöpfen
Rennteam Uni Stuttgart | Erfolgsgeschichte
-
Erhebliche Verkürzung der Entwicklungs- und Produktionszeit
-
Zuverlässig auf der Strecke dank einer um 20 % erhöhten Steifigkeit
-
Perfekte Form und Konturierung für ein um 35 % reduziertes Gewicht
"Wir freuen uns sehr, dass wir den Titel der Formula Student Germany 2012 nach Stuttgart holen konnten. Die Freiheit im Konstruktionsprozess, die die DMLS-Technologie von EOS bietet, hat eine wichtige Rolle für unseren Erfolg gespielt."
Yannick Löw | Rennteam Uni Stuttgart
Mit Leichtigkeit zum Sieg - Das Rennteam Uni Stuttgart gewinnt die Formula Student Germany mit EOS Unterstützung
Einerseits hat jeder Konstrukteur eines Achsschenkels die Aufgabe, ein möglichst stabiles Bauteil zu entwickeln - andernfalls wäre die Sicherheit des gesamten Fahrzeugs gefährdet. Andererseits dürfen die Radträger aus verschiedenen Gründen nicht zu viel wiegen.
Bereits in der Konzeptionsphase setzten die Ingenieure die CAD-Software von EOS partners Within Technologies Ltd. ein. Dank dieses Tools konnten die Konstrukteure das Teil perfekt auf die strukturellen Anforderungen abstimmen. So konnten sie dem Achsschenkel genau die geforderten physikalischen Eigenschaften verleihen - Leichtigkeit und Steifigkeit.
Zum einen entfällt bei der additiven Fertigung die Notwendigkeit, Negative oder Gussformen herzustellen. Außerdem ist der gesamte Prozess vom Entwurf bis zur Fertigung präziser, was bedeutet, dass oft keine Nachbearbeitung oder Verfeinerung erforderlich ist. Das Teil war fast sofort renntauglich.
Das Gewicht des Bauteils wurde um 660 Gramm reduziert, wodurch das Rennteam Uni Stuttgart 35 % einsparen konnte. Gleichzeitig gelang es den Ingenieuren, die Steifigkeit um 20 % zu erhöhen - große Zahlen für den Motorsport, die sich in schnelleren Rundenzeiten und geringerem Kraftstoffverbrauch niederschlagen.

"Wir haben das Teil im klassischen Feingussverfahren hergestellt. Das führte natürlich zu Einschränkungen in der Formfreiheit, so dass das Potenzial des Teils nie voll ausgeschöpft werden konnte. Schon damals hatten wir beschlossen, für die Saison 2012 neue, innovative Wege zur Herstellung des Achsschenkels zu suchen."
Yannick Löw | Rennteam Uni Stuttgart
Die Ergebnisse auf einen Blick
- 20 % Höhere Steifigkeit
- -660 g Gewichtsreduzierung
EOS-Erfolgsgeschichten
Erleben Sie drei Jahrzehnte Pionierarbeit im 3D-Druck mit EOS