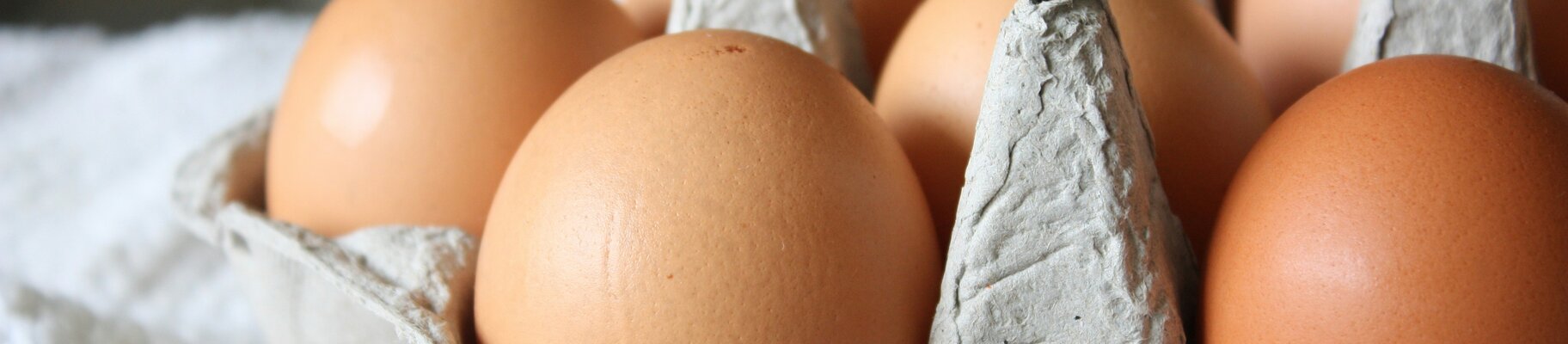
3D-gedruckte Werkzeuge für die Formfaserproduktion
Payr Engineering | Fallstudie
Sauber verpackt
- 50% niedrigere Werkzeugkosten
- Die Produktionszeit sinkt auf einige Wochen
- Rentabel auch bei kleinen Losgrößen
Mit etwas umgehen wie mit einem rohen Ei - eine bekannte Redewendung. So hart eine Eierschale auch ist, der bekannte Eierkarton ist meist die erste Wahl für den sicheren Transport nach Hause. Die geformte Zellstoffverpackung bietet Schutz und ist umweltfreundlich. Der österreichische Ingenieurdienstleister Payr hat das Werkzeug für seine Produktion mittels additiver Fertigung optimiert und kann es so schneller und kostengünstiger herstellen. Zudem konnten die Transportwege verkürzt werden und kleinere Stückzahlen sind möglich.

"Mit den Maschinen von EOS sind wir in der Lage, robuste Bauteile zu produzieren, die mit Maschinen anderer Anbieter nicht hergestellt werden könnten."
Peter Paul Payr | Geschäftsführer bei Payr Engineering
Herausforderung
Geformter Zellstoff - das Wort selbst ist nicht so geläufig wie das Material. Ob aus Altpapier oder aus nachwachsenden Fasermaterialien wie Gräsern, immer mehr Unternehmen setzen recycelte und wiederverwertbare Materialien als Schutzverpackungen ein. Im Einzelhandel reicht die Palette vom eingangs erwähnten Eierkarton bis hin zu maßgeschneiderten Verpackungen, die Elektronik- oder Haushaltsgeräte schützen. Dank des technologischen Fortschritts kann das Material heute noch mehr leisten. Fettabweisend, wasserfest - all das ist ohne Plastik möglich.
Dadurch ist das Material auch für andere Anwendungsbereiche interessant geworden. Das Problem war bisher die Stückzahl der Verpackung. Einer der Gründe dafür ist das Herstellungsverfahren. Grundsätzlich wird das in Wasser gelöste Material - der so genannte Brei - durch ein Vakuum in eine perforierte Form gesaugt, die mit vielen kleinen Öffnungen beschichtet ist. Über diese Siebe fließt die Flüssigkeit ab oder wird abgesaugt. Die perforierten Formen wurden vor allem an asiatischen Produktionsstandorten meist von Hand mit dem Sieb bespannt - ein sehr teures und zeitaufwändiges Verfahren.
Payr ging auf diese Fragen ein und konzentrierte sich dabei auf das Werkzeug und insbesondere auf das Sieb: "Die Nachbearbeitung eines solchen Bauteils von Hand wäre hierzulande zu teuer und ist mit langen Transportwegen ins Ausland verbunden, die wiederum Kosten verursachen. Aufgrund der Produktions- und Fertigungszeiten des traditionellen Verfahrens gab es so oder so Optimierungspotenzial", erklärt Peter Paul Payr, Geschäftsführer von Payr Engineering und Gesellschafter der Payr-Gruppe. "Deshalb haben wir nach einer Alternative für die Herstellung des Bildschirms gesucht und sie in der additiven Fertigung gefunden."
Kostengünstig und nachhaltig
Produktionsprozess von Zellstoffverpackungen aus Formteilen

Lösung
Payr hatte einen besonders innovativen Ansatz: Form und Sieb bestanden bisher aus zwei Komponenten: einem Metallkern und einer Gitterstruktur, die manuell geformt und aufgebracht wurde. Dank additiver Fertigung wurde eine innovative Entwässerungsstruktur entwickelt, die nun die ursprünglichen Funktionen der statisch stabilen Form und der gleichmäßig verteilten Entwässerung über die gesamte Form in einem Teil vereint. Dadurch ist nur noch ein einziger Produktionsschritt erforderlich. Dies vereinfacht die Produktion weiter und beschleunigt zudem den gesamten Prozess bei gleichbleibend hoher Qualität.
Das von Payr gewählte Material ist der in der additiven Fertigung übliche Kunststoff PA 12. Er ist kostengünstig und robust genug, weil der verwendete 3D-Drucker die feine Siebstruktur hervorragend reproduziert. Peter Paul Payr bestätigt, dass dies kein Selbstläufer ist: "EOS hat mit dem EOS P 396 ein extrem leistungsfähiges Produkt im Portfolio. Die Leistung übertrifft die anderer bekannter Hersteller deutlich, vor allem bei den Gitterstrukturen. Die Stabilität des Bauteils, die wir für diese Anwendung benötigen, haben wir mit keinem anderen Gerät erreichen können."
Präzision ist entscheidend und damit erfolgskritisch, um den Fließwiderstand des Zellstoffs richtig steuern zu können: Die Geometrie der Drainagestruktur bestimmt zum einen, wie viel Material an der Form haften bleibt und wie stabil die Verpackung später wird. Andererseits beeinflusst sie, wie viel Feuchtigkeit übrig bleibt, was sich auf die Trocknungszeit auswirkt. Natürlich bringt die additive Fertigung auch hier ihre "klassischen" Vorteile mit, wie die große Gestaltungsfreiheit der Form und die kurze Gesamtzeit für ihre Herstellung.
Ergebnisse
Die Stunde der Wahrheit kommt aber immer dann, wenn überprüft wird, ob die Ziele erreicht wurden. Hier überzeugt das neue Tool von Payr voll und ganz: Während die Beschaffungszeit früher mehrere Monate betrug, ist die neue Kombisauganlage nun in wenigen Wochen verfügbar. Ebenso wichtig - und beeindruckend - ist die durch die Umstellung erzielte Kostenreduzierung: "Hier können wir unseren Kunden einen deutlichen Vorteil bieten. Die Kosten für die Herstellung des Werkzeugs sind mindestens 50 Prozent niedriger als bei der traditionellen Fertigungsmethode. Und das macht 3D-gedruckte Formen für Verpackungen in kleinen Stückzahlen oder in Varianten attraktiv", sagt Peter Paul Payr stolz. Durch die Gestaltungsfreiheit der additiven Fertigung ist es auch möglich, Endverpackungen mit unterschiedlichen Wandstärken herzustellen, d.h. es wird nur dort Material eingesetzt, wo es notwendig ist.
Zusammen mit der optimierten Siebtechnik überprüfte Payr den gesamten Produktionsprozess - und konnte auf Basis des optimierten Werkzeugs noch mehr Potenziale mit seiner selbst entwickelten FIBRA MINI Formstoffanlage ausschöpfen. So konnte beispielsweise die Absaug- und Entwässerungstechnik verbessert werden. Daraus resultieren ein geringerer Energiebedarf für die Trocknung und niedrigere Materialkosten, weil die Wände trotz Qualitätssteigerung noch dünner gemacht werden konnten. Weniger Material bedeutet gleichzeitig Vorteile über den gesamten Lebenszyklus, vom Druck bis zum Recycling.
Ein weiterer Vorteil für die Unternehmen lässt sich nicht beziffern: Die Lieferkette wird deutlich belastbarer. Eine kostengünstigere Verlagerung eines Produktionsschrittes ist nicht nur eine Seltenheit, sondern erhöht auch die Unabhängigkeit von festen Routen für die Lieferanten von Zellstoffformprodukten. Gleichzeitig bietet diese Verschlankung der Lieferkette weitere Umweltvorteile - denn was nicht um die halbe Welt transportiert werden muss, hat natürlich auch einen kleineren CO 2e-Fußabdruck. Noch wichtiger für die Nachhaltigkeit ist jedoch die Tatsache, dass Formstoff noch wettbewerbsfähiger wird und damit immer mehr Kunststoffverpackungen ersetzen kann.
Für Payr Engineering und seine Kunden ist die Umstellung in der Produktion des Produktionswerkzeugs für Formstoff daher ein in vielerlei Hinsicht erfolgreiches Projekt. "Wo sonst lassen sich Transportwege verkürzen, die Produktion wiederherstellen und gleichzeitig Kosten senken und die Qualität steigern", fragt Peter Paul Payr. Und diese ganze Kette von Vorteilen beginnt bei der Technologie: der additiven Fertigung. In Zukunft werden immer mehr Produkte wie rohe Eier ihren Weg vom Erzeuger zum Kunden finden.
Präzise und stabil
3D-gedruckte Zellstoffform mit innovativer gitterförmiger Drainagestruktur aus Kunststoff PA 2200


"Wir können Qualitätsschwankungen beseitigen und gleichzeitig Kosten und Markteinführungszeiten reduzieren. Unsere Kunden werden in der Lieferkette widerstandsfähiger, reduzieren die Transportkosten und die Menge der Kunststoffverpackungen."
Peter Paul Payr | Geschäftsführer bei Payr Engineering
EOS-Fallstudien
Erleben Sie drei Jahrzehnte Pionierarbeit im 3D-Druck mit EOS