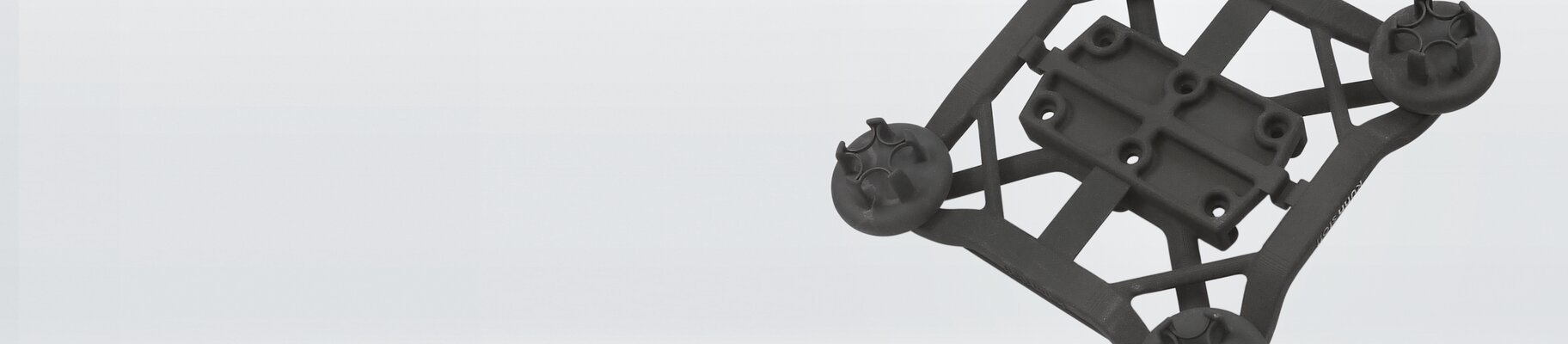
Das additiv gefertigte Griffsystem ist mit der EOS-Technologie leicht und langlebig
Wittmann Gruppe & KuhnStoff | Fallstudie
Bronchialgreifer mit funktioneller Grundplatte, leicht und langlebig mit EOS-Technologie
Die Hand ist einer der entscheidenden Meilensteine der menschlichen Evolution: Mit ihrem Daumen, der den anderen Fingern gegenübersteht, ist die menschliche Hand ein ideales Werkzeug zum Greifen, Erforschen und Arbeiten. Als solches ist sie der Schlüssel zu kulturellen Aktivitäten und technischem Fortschritt. Die Industrie macht sich dieses geniale Prinzip häufig zunutze: Einer der Prozesse, für die Maschinen eingesetzt werden, ist das automatisierte Greifen von fast jedem gewünschten Teil, um es zum nächsten Arbeitsschritt zu transportieren.
Solche Greifmaschinen sind Meisterwerke der Ingenieurskunst. Die Kuhn-Stoff GmbH & Co KG hat sich dem Sondermaschinenbau durch den Einsatz der additiven Fertigungstechnologie EOS verschrieben. Bei dem Verfahren werden Maschinenteile Schicht für Schicht aus Kunststoffpulver geformt , das mit einem Laserstrahl aufgeschmolzen wird. Auf diese Weise hat Kuhn-Stoff für die Wittmann Robot Systeme GmbH in Nürnberg einen extrem leichten, stabilen und langlebigen Bronchialgreifer entwickelt und produziert. Vier dieser Greifer sitzen auf einem Tragrahmen mit integrierten Pneumatikkanälen.

"Wir setzen seit Jahren in verschiedenen Bereichen der Automatisierungstechnik Teile ein, die mit Additive Manufacturing hergestellt wurden. Der Bronchialgreifer erfüllt alle unsere Anforderungen, ja übertrifft sie sogar. Das Teil ist sehr zuverlässig in seiner täglichen Leistung.
Michael Tolz | Leiter Technik, Deutschland und Niederlassungsleiter | Wittmann Robot Systeme GmbH in Nürnberg
Herausforderung
Der Kunde ist ein Hersteller von Robotern und Automatisierungssystemen. Kuhn-Stoff wurde beauftragt, einen mechanischen Greifer neu zu konzipieren, der Maschinenteile aus einer Produktionsmaschine über einen pneumatischen Mechanismus anhebt, transportiert und anschließend ablegt. Folgende Anforderungen wurden festgelegt: Der Greifer sollte leichter sein als sein Vorgänger, aber dennoch die geforderten Lasten bewegen können. Die Komplexität der Konstruktion sollte vereinfacht werden und das Teil muss Effizienzkriterien erfüllen können.
Die Bedeutung des Gewichts liegt in der Physik begründet: Ein solches Greifsystem muss schnell arbeiten, um möglichst viele Maschinenteile in einer bestimmten Zeiteinheit zu bewegen.
Die Tatsache, dass Masse träge ist, bedeutet, dass eine Kraft aufgebracht werden muss, um sie in Bewegung zu setzen - je schwerer eine Last ist und je schneller sie sich bewegt, desto größer sind die Kräfte, die zur Beschleunigung und Abbremsung erforderlich sind.
Abgesehen von der Energieeffizienz wirkt sich diese Tatsache besonders negativ auf die Lebensdauer des Systems aus: Je größer die einwirkenden Kräfte, desto höher der Verschleiß der Maschine.
Die bisherige Version des Greifers bestand aus Aluminium, Gummischläuchen und mehreren Verbindungselementen und war teuer in der Herstellung. Die Schichtbauexperten von Kuhn-Stoff setzten sich das Ziel, die Konstruktion deutlich zu vereinfachen. Die neue Struktur des Maschinenteils sollte zu einem Teil der Gewichtsreduktion beitragen. Ein weiterer Teil sollte durch eine strukturelle Optimierung der übrigen Teile erreicht werden - einer der zentralen Vorteile der additiven Fertigung. Zu Beginn der Arbeiten wurde schnell klar, dass der neue Greifer aus einem Stück gefertigt werden kann, ohne dass eine Nachbearbeitung oder weitere Montage erforderlich ist.

Lösung
Das Team von Kuhn-Stoff untersuchte zunächst die Funktionsweise und die Anforderungen an den Greifer: Wenn Druckluft in eine flexible Membran strömt, öffnen sich die Klauen des Greifers; ebenso schließt sich das System, wenn die Druckluft abgestellt wird. Neben der Flexibilität des Kunststoffs sollte das Teil um 90° schwenkbar sein, um den erforderlichen Bewegungsablauf auszuführen. Unter Berücksichtigung dieser Anforderungen konnte die Anzahl der benötigten Teile auf nur zwei Komponenten reduziert werden.
Nach Abschluss des Konstruktionsprozesses begann Kuhn-Stoff mit der Fertigung des neuen Griffsystems auf einer FORMIGA P 100. In nur wenigen Stunden wurden die beiden Komponenten des Griffsystems aus Polyamid gefertigt. Dank der EOS-Technologie wurden die Pneumatikkanäle und -anschlüsse vollständig in die Grundplatte integriert.
"Die Produktion mit dem EOS-System verlief wie gewohnt reibungslos und ohne Probleme. Das Endergebnis hat wieder einmal alle Beteiligten überzeugt. In einem einzigen Prozessschritt konnten wir ein funktionsintegriertes Bauteil erstellen, das alle Anforderungen des Auftraggebers übertrifft. Kurzum: Additive Fertigung ist heute alltäglich, aber die Ergebnisse sind immer noch außergewöhnlich", so Hannes Kuhn, Geschäftsführer der Kuhn-Stoff GmbH.

"Wir setzen die EOS-Technologie seit mehr als acht Jahren ein und haben ausschließlich positive Erfahrungen gemacht. Bei richtiger Anwendung bietet die Designflexibilität erhebliche Vorteile, die unseren Kunden nahezu konkurrenzlose Vorteile auf dem Markt verschaffen können."
Hannes Kuhn | Geschäftsführer | Kuhn-Stoff GmbH & Co KG
Ergebnisse
Beim Hauptziel, der Gewichtsreduzierung, erreichte Kuhn-Stoff eine Reduktion um 86 % auf nur noch 220 g. Trotz des geringen Gewichts ist der Greifer auch im anspruchsvollen Dauereinsatz belastbar: Nach 5 Millionen Zyklen beendete das Team die Belastungstests, da die vorgesehene Lebensdauer erreicht war. In diesem Zeitraum ist kein einziger Defekt oder Ausfall aufgetreten. Grund dafür ist die Festigkeit der Konstruktion, die trotz der in der Bodenplatte integrierten Luftkanäle erreicht wurde. Darüber hinaus sorgt die flexible Konstruktion dafür, dass bei kleinen Kollisionen keine Schäden am Greifersystem oder am Spritzgießwerkzeug entstehen. Das geringere Gewicht ermöglicht in einigen Fällen auch den Einsatz eines kleineren Robotertyps, was zu einer deutlichen Kostenreduzierung führt. Darüber hinaus konnte Wittmann die Zahl der Arbeitszyklen erhöhen, da die geringe Höhe des Greifers die notwendige Öffnungsweite der Aufspannplatte der Spritzgießmaschine reduziert. Das Ergebnis ist eine Reduzierung der Betriebskosten.
Die Herstellungskosten konnten im Vergleich zum konventionell gefertigten Vorgänger um 50 % gesenkt werden. Dies ist auf Gewichtseinsparungen sowie auf die Reduktion der Anzahl Komponenten von 21 auf zwei zurückzuführen. Ebenso wichtig ist die kurze Produktionszeit: Für die Herstellung des Griffsystems, für die Kuhn-Stoff bisher zwölf Tage benötigte, werden nur noch drei Tage benötigt.
"Wir sind sehr zufrieden mit dem neuen Griffsystem. Es hat sich im harten Dauereinsatz genauso bewährt wie das bisherige, ist aber günstiger und leichter und kann schneller produziert werden. Ich habe noch nie einen so bedeutenden Fortschritt bei der Herstellung von Griffen gesehen wie den, den das Additive Manufacturing bei der Produktion unseres Bronchialgreifers gebracht hat. Das Produktionsverfahren hat sich sehr positiv auf unsere Automatisierungslösungen ausgewirkt", resümiert Michael Tolz, Leiter Technik und Niederlassungsleiter der Wittmann Robot Systeme GmbH. Gelegentlich kann eine Revolution auch Vorteile gegenüber einer Evolution haben.
Die Ergebnisse auf einen Blick
-
-1350 Gramm: Gewichtsreduzierung um 86 %
-
-50 % Kosten: Senkung der Produktionskosten um 50 %
-
-19 Bestandteile: Reduktion der einzelnen Komponenten von 21 auf 2

EOS-Fallstudien
Erleben Sie drei Jahrzehnte Pionierarbeit im 3D-Druck mit EOS