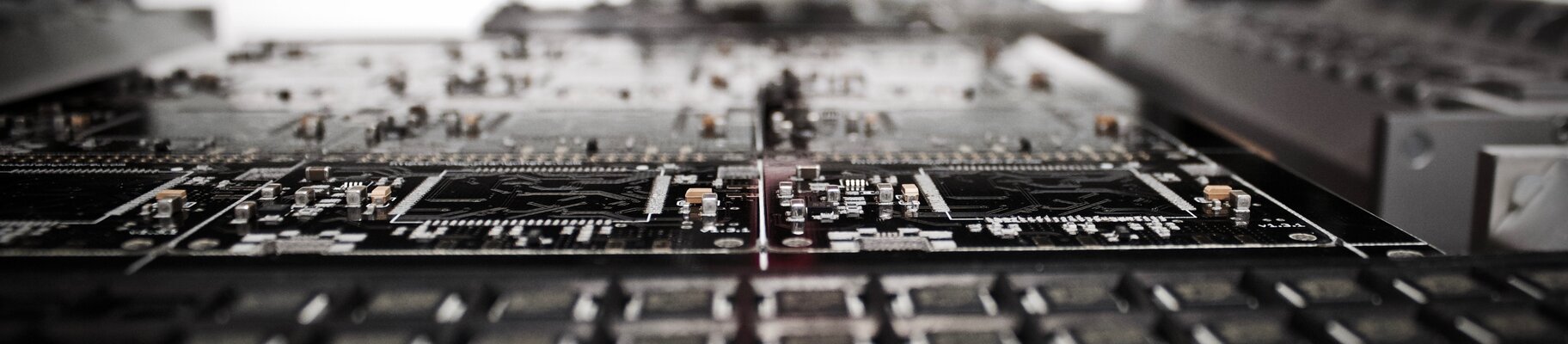
Mehrdimensionale Schaltungsträger mit additiver Fertigung
Beta LAYOUT | Fallstudie
Prototypen für neue Leiterplatten (PCBs) mit EOS-Technologie erstellt
Anfang 2016 schrieben viele über das Ende des Mooreschen Gesetzes und rechneten damit, dass sich die Leistung von Computerchips nicht mehr alle zwei Jahre verdoppeln würde. Der Grund dafür ist, dass die Strukturen auf den Prozessoren selbst bereits im Bereich von wenigen Nanometern des Möglichen liegen. Eine weitere Verkleinerung ist aus technischer Sicht fast unmöglich. Um die Leistung weiter zu verbessern, arbeiten die Hersteller an einer Architektur, bei der mehrere Strukturschichten übereinander gestapelt werden. Ein ähnlicher Ansatz hat sich bereits im Bereich der Schaltungsträger etabliert. Das deutsche Unternehmen Beta LAYOUT GmbH hat die EOS-Technologie erfolgreich für die Herstellung und Erprobung der Prototypen dieser innovativen Träger genutzt.
"Die additive Fertigungstechnologie bietet dank ihrer vielen Vorteile einen hohen Mehrwert für eine breite Palette von Marktteilnehmern. Forschung und Entwicklung profitieren von unseren Dienstleistungen, was sich wiederum positiv auf unser Geschäftsmodell auswirkt. So können wir die Vorteile der Spitzentechnologie einer großen Zahl von Anwendern anbieten."
Manuel Martin | Produktmanager 3D-MID | Beta LAYOUT GmbH
Herausforderung
Herstellung von individuellen Prototypen für Schaltungsträger
Schaltungsträger und traditionelle Leiterplatten standen schon immer ein wenig im Schatten der Mikroprozessoren, die auf ihnen arbeiten. Das ist ein wenig ungerecht, denn natürlich nützt das beste Gehirn wenig, wenn man nicht über ein leistungsfähiges zentrales Nervensystem verfügt. Ähnlich verhält es sich in der Mikroelektronik: Fast alle modernen Geräte benötigen eine Platine, auf der ein oder mehrere Chips und die zusätzlich benötigten elektrischen Bauteile untergebracht sind. So entsteht ein Netzwerk, das eine Reihe von Aufgaben erfüllt, von der Stromversorgung über die Schaltung bis hin zur Ausgabe von Signalen.
In neuen Geräten ist oft nur noch sehr wenig Bauraum für herkömmliche Leiterplatten vorhanden. Ein Grund dafür ist, dass viele elektronische Geräte immer kleiner werden; und auch wenn die Form selbst größer ist, bleibt meist nur wenig Platz für die eigentliche Elektronik übrig. Das vorhandene Volumen wird zum Beispiel für die Unterbringung von Bildschirmen, immer mehr Schnittstellen und Ausgängen sowie größeren Batterien benötigt. Die Zeiten, in denen eine einfache Laborplatine für den experimentellen Aufbau von neuen Schaltungen ausreichte, sind in den meisten Fällen und Branchen längst vorbei. Neben dem verfügbaren Bauraum ist das Gewicht ein entscheidender Faktor - auch hier spielen kompakte, dreidimensional aufgebaute Leiterplatten eine wichtige Rolle.
Bei modernen elektronischen Produkten müssen die Schaltungen oft um den begrenzten Platz im Gehäuse konkurrieren. Konventionell gestapelte Leiterplatten können nicht mehr alle notwendigen Bauteile aufnehmen, so dass die bereits erwähnten dreidimensionalen Schaltungsträger die Lösung der Wahl werden. Auch hier stellen die immer kürzer werdenden Lebenszyklen vieler Geräte eine zusätzliche Herausforderung dar: Spritzguss ist für die Herstellung von Prototypen viel zu teuer. Aus diesem Grund hat sich die Beta LAYOUT GmbH auf die Suche nach einer kostengünstigen und leistungsfähigen Alternative gemacht.
Lösung
Es gibt keine Technologie, die besser für die Anforderungen der Mehrschichtarchitektur geeignet ist als die additive Fertigung. Denn sie nutzt einen Laser, um ein Bauteil Schicht für Schicht aufzubauen. Deshalb setzt Beta LAYOUT auf diese Technologie und verwendet Kunststoffteile, die im 3D-Druckverfahren hergestellt werden. Die Innovation findet nach dem eigentlichen Druckprozess statt: Nach der Herstellung werden die Modelle mit einem speziellen Finish beschichtet, das mit einem Additiv versehen wird. Die anschließende sogenannte Laser-Direkt-Strukturierung (LDS) erzeugt Layouts, die durch Aktivierung des Lacks in Leiterbahnen verwandelt werden können.
Der Laser löst eine physikalisch-chemische Reaktion aus, bei der metallische Sporen entstehen und gleichzeitig die Oberfläche aufgeraut wird. Nach der Laserdirektstrukturierung werden die Modelle in ein stromloses Kupferbad gelegt. Dort werden Kupferpartikel auf den zuvor aktivierten Bereichen abgeschieden, um Leiterbahnen zu erzeugen. Nach der Verkupferung können die Leiterbahnen durch Galvanisieren weiter verkupfert oder direkt mit einem Oberflächenfinish versehen werden. Anschließend fügt Beta LAYOUT in der firmeneigenen Montageabteilung die einzelnen Komponenten zum Gerät zusammen. Die fertigen Teile dienen als erste Prototypen und Modelle, um die Funktion zu testen und das Design zu überprüfen.
"Wir bieten die Fertigung von 3D-MID (mechatronic integrated devices) als Prototypen für verschiedene Unternehmen an", erklärt Manuel Martin, Produktmanager 3D-MID bei der Beta LAYOUT GmbH. "Durch die Arbeit mit der FORMIGA P 110 von EOS sind wir in der Lage, unseren Kunden schnell hochwertige Produkte zu liefern. Besonders praktisch ist dabei, dass wir sogar Bestellungen von 3D-Modellen über Websites und Online-Shops abwickeln können. Mit der additiven Fertigung haben wir unser Geschäftsmodell erfolgreich erweitert."

Ergebnisse
Ob für Einzelentwickler oder große etablierte Unternehmen, die additive Fertigung sorgt dafür, dass maßgeschneiderte Schaltungsträger für die Prototypen neuer elektronischer Geräte eingesetzt werden können. Die Kunststoffkomponenten können schnell und kostengünstig hergestellt werden. Gleichzeitig bietet das Verfahren die nötige Präzision und hohe Bauteilqualität, so dass der benötigte Grundkörper wie ein seriennahes Produkt gefertigt werden kann - ein nicht zu unterschätzender Aspekt, insbesondere bei Testläufen.
Die EOS-Technologie bietet zudem ein hohes Maß an Flexibilität: Die eingesetzte Maschine ist in der Lage, verschiedene Materialien zu verarbeiten, darunter zum Beispiel das mit Glaskugeln gefüllte PA 3200 GF oder das aluminiumgefüllte Polyamid Alumide. Auch Hochleistungskunststoffe wie PEEK und verschiedene Metalle sind möglich. Entscheidend ist, dass alle Materialien hohe Temperaturen vertragen, eine Einschränkung des Spritzgießverfahrens in der Serienproduktion.
Durch diese Flexibilität ist Beta LAYOUT in der Lage, die verschiedenen individuellen Anforderungen seiner Kunden zu erfüllen, indem es zum Beispiel auf die besonderen Eigenschaften des Verwendungszwecks des Schaltungsträgers eingeht. So kann das Unternehmen individuelle, optimierte Lösungen entwickeln, sei es im Hinblick auf geringere Kosten, eine höhere Temperaturbeständigkeit oder andere spezifische Anforderungen.
Neben diesen Vorteilen bietet die additive Fertigung noch einen weiteren Bonus: "Letztlich erleben wir hier eine Demokratisierung der Spitzentechnologie. Ohne Innovationen könnten wir 3D-MID als Dienstleistung gar nicht anbieten", sagt Manuel Martin. "Das würde bedeuten, dass viele kleinere Unternehmen und Entwicklungshäuser keine Chance hätten, solche Prototypen zu realisieren. Damit würde die viel beschworene Innovations- und Gestaltungskraft kleiner und mittlerer Unternehmen an Schwung verlieren und der Forschungs- und Entwicklungssektor wäre deutlich weniger dynamisch."
Die additive Fertigung ist ein Katalysator für weitere Innovationen - und auf diese Weise vielleicht ein Ausgangspunkt für ein neues Moore'sches Gesetz.

Die Ergebnisse auf einen Blick
- Einfach: Zugang zu Spitzentechnologie für Forschung und Entwicklung
- Customized: Dienstleister für maßgeschneiderte Produkte
- Wirtschaftlich: werkzeuglose Produktion senkt Kosten
EOS-Fallstudien
Erleben Sie drei Jahrzehnte Pionierarbeit im 3D-Druck mit EOS