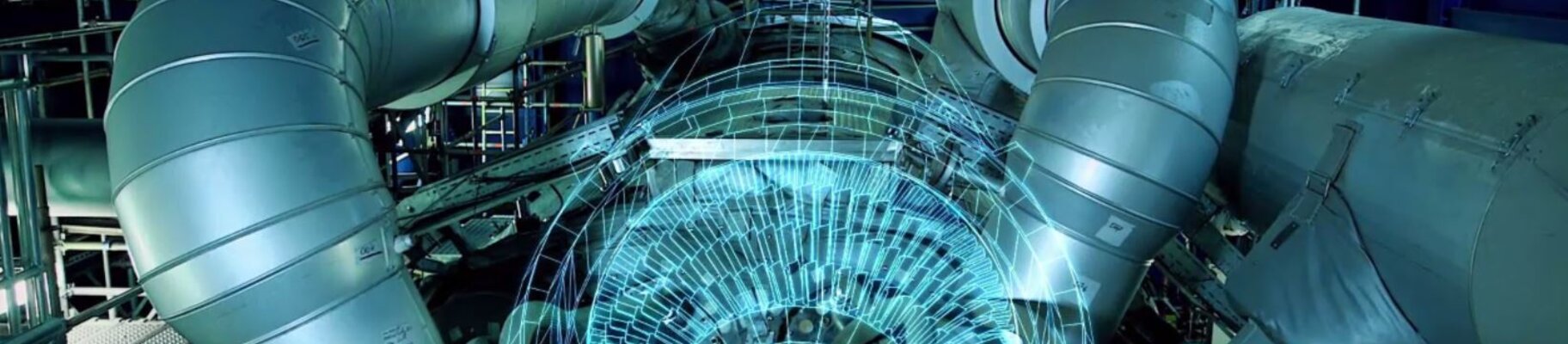
3D-Druck für industrielle Hochleistungsturbinen
Siemens | Fallstudie
Das schwedische Unternehmen Siemens ENERGY stellt Gasturbinen für die Stromerzeugung in Industrie- sowie Öl- und Gasanwendungen her. Das Leistungsspektrum dieser Siemens-Industrieturbinen liegt zwischen 15 und 60 MW. Neben dem Bau bietet die Siemens-Tochter auch den langfristigen Service und die Wartung dieser technischen Meisterwerke an. Um die Instandhaltungskosten zu senken, arbeitet Siemens an der Entwicklung und Umsetzung der Additiven Fertigung mit Hilfe der EOS-Technologie und -Anlagen.
"Additive Manufacturing eröffnet uns neue Dimensionen in der Anwendung von integriertem Design und Produktion. Mit dieser Technologie können wir Bauteile für unsere Industriegasturbinen viel schneller als bisher herstellen und reparieren. Gleichzeitig wird die Funktionalität und Leistung des Bauteils erhöht."
Dr. Vladimir Navrotsky | Leiter Technologie und Innovation, Siemens Energy Service | Öl & Gas und industrielle Anwendungen
Herausforderung
Die Gasturbine besteht aus einem Lufteinlass, einem Verdichter, einer Brennkammer, einer Turbine und einem Heißgasauslass. Die Luft, die durch das Triebwerk strömt, wird durch den Verdichter komprimiert. In der Brennkammer wird die komprimierte Luft mit Kraftstoff vermischt und verbrannt, um die kinetische Energie des Stroms zu erhöhen. In der Turbine wird die kinetische Energie des Stroms in mechanische Energie umgewandelt. Diese mechanische Energie wird zum Antrieb des Gasturbinenverdichters und des Generators (zur Stromerzeugung) oder anderer angetriebener Geräte (z. B. des Verdichters zum Pumpen des Gases/Öls durch die Pipelines) verwendet. Während des Betriebs sind die Komponenten im Heißgasweg des Triebwerks hohen Temperaturen ausgesetzt, die manchmal über 1.000 °C betragen (z. B. Schaufeln und Leitschaufeln). Dies wiederum führt zu einem hohen Verschleiß der Heißgaspfadkomponenten.
Das gilt auch für die Brennerspitze - den Punkt, an dem die Zündung des Brennstoff-Luft-Gemisches erfolgt. Hier sind die Auswirkungen von Verschleiß und Abnutzung deutlich zu sehen und zu messen. Der Hersteller hat strenge Tests durchgeführt, um eine vorgeschriebene Betriebsdauer festzulegen, nach der die Brenner normalerweise repariert werden müssen.
Das herkömmliche Reparaturverfahren erforderte die Vorfertigung großer Teile der Brennerspitze.
Diese vorgefertigte Einheit wird für den Austausch der Brennerdüse nach der vorgegebenen Betriebszeit verwendet (Ausschneiden der alten und Aufschweißen der vorgefertigten Düse). Herkömmliche Reparaturverfahren können sehr zeitaufwändig sein und erfordern eine große Anzahl von Teilprozessen und Prüfungen. Um das Reparaturverfahren zu vereinfachen und zu beschleunigen, wurde bei Siemens die Technologie der additiven Fertigung eingeführt.

Lösung
Um ein solches Vorhaben durchzuführen, braucht man einen innovativen Partner. Den hat Siemens in EOS gefunden: EOS verfügte nicht nur über die passende Additive Manufacturing Technologie, sondern war auch in der Lage, innerhalb kurzer Zeit eine der hauseigenen Maschinen - eine EOSINT M 280 - individuell für die Metallbearbeitung anzupassen.

Die Änderungen betrafen insbesondere den Maßstab des Maschineninnenraums, der vergrößert werden musste, um den 800-mm-Brenner aufzunehmen. Darüber hinaus änderte der Hersteller weitere Hardwarekomponenten wie ein Kamerasystem und ein optisches Messsystem und nahm entsprechende Anpassungen an der Software vor. EOS hat die umfangreiche Überarbeitung des EOSINT-Systems in weniger als einem Jahr durchgeführt.
Von Anfang an war klar, dass sich der Ansatz auszahlt. Anstatt einen großen Teil der Brennerspitze auszutauschen, entfernte Siemens zunächst nur das beschädigte Material. Außerdem konnten während der Reparatur frühere Versionen der Brenner in der Flotte auf die neueste Konstruktion umgerüstet werden. Dies bedeutete, dass ältere Brennerversionen der Flotte nicht nur repariert, sondern auch verbessert werden konnten - womit der Begriff "Additive Manufacturing" eine neue Bedeutung erhielt.
Ergebnisse
Zahlen, Daten und Fakten belegen eindeutig den Erfolg des neuen Reparaturverfahrens. Siemens ENERGY wird das zentrale Anliegen - die Verkürzung des Reparaturzeitrahmens - maßgeblich beeinflussen können: Für den Betreiber ist es ebenso wichtig, dass die Turbinen schnell wieder einsatzbereit sind. Damit eröffnen sich auch zusätzliche Möglichkeiten für Kostensenkungspotenziale im Reparaturprozess und bei der Wartung.
Neben der Verbesserung des eigenen Reparaturprozesses kann Siemens nun auch seinen Kunden strategische Vorteile bieten: Dank des neuen Verfahrens können die Experten Verbesserungen an der Turbinentechnik vornehmen, indem sie die Komponenten in den Reparaturprozess integrieren. Auf diese Weise können die Betreiber die neueste Technologie nutzen, auch wenn ihre Turbinen schon viele Jahre im Einsatz sind.
Dr. Vladimir Navrotsky, Leiter Technologie und Innovation bei Siemens Energy Service, Oil & Gas and Industrial Applications, fasst zusammen: "Mit dieser neuen Reparaturtechnologie wollen wir diese hochpräzisen Arbeiten viel schneller durchführen."
Nicht nur die schwedische Siemens-Tochter sieht in dem Projekt einen großen Erfolg. "Wir haben unsere Technologie erfolgreich in den Bereich der Reparatur gebracht. Wir haben gezeigt, dass wir in der Lage sind, unser System schnell auf kundenspezifische Anforderungen zu modifizieren. In diesem Fall waren die Änderungen sowohl an der Hardware als auch an der Software erheblich. Alle Beteiligten können zufrieden zurückblicken, nicht nur auf das Ergebnis, sondern auch auf den Weg dorthin", sagt Stefan Oswald von EOS.

Die Ergebnisse auf einen Blick
- Innovativ: alte Brennerversionen können schnell auf den neuesten Stand der Technik gebracht werden
- Kosteneffizient: Mögliche Kostensenkungen sind bereits in einem frühen Stadium erkennbar
- -90 % weniger Zeitaufwand für den Reparaturprozess
EOS-Fallstudien
Erleben Sie drei Jahrzehnte Pionierarbeit im 3D-Druck mit EOS