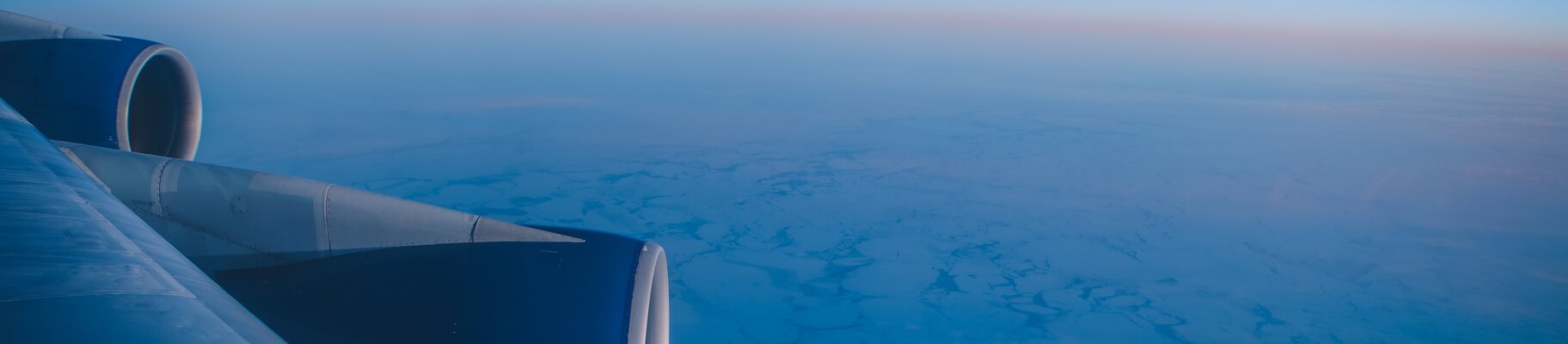
3D-Druck für die Luftfahrt
Effizient und nachhaltig produzierte Hightech-Teile
Additive Fertigung für Triebwerke, Turbinenteile und mehr
Sie wollen Funktionsteile mit komplexen Geometrien und definierten aerodynamischen Eigenschaften kostengünstig und möglichst schnell herstellen? Undenkbar? Nein.
Triebwerks- und Turbinenteile sind typische Beispiele dafür, was mit dem industriellen 3D-Druck möglich ist, ebenso wie Teile für die Kabineninnenausstattung.
Funktionsintegration, die Entwicklung immer komplexerer Konstruktionen und die dazugehörigen Teile sind die wichtigsten Faktoren in der Luft- und Raumfahrtindustrie. Die Einsparung von Materialien und Gewicht reduziert sowohl den Treibstoffverbrauch als auch die CO2-Emissionen. Diese Themen sind heute wichtiger als je zuvor. Deshalb haben führende Unternehmen der Luft- und Raumfahrtindustrie die additive Fertigungstechnologie schon lange in die Planung ihrer Produktionsstrategien für die Zukunft einbezogen.
In enger Zusammenarbeit mit führenden Unternehmen aus der Luft- und Raumfahrtbranche haben wir viele unterschiedliche Erfolgsgeschichten realisiert und begleitet.
Unser Mehrwert besteht in einer durchgängigen Lösung: von der Bereitstellung und Implementierung von 3D-Drucksystemen bis hin zur individuellen Beratung und Unterstützung mit qualifizierten Verfahren für Materialien, Systeme, Teile oder komplette Baugruppen. Diese intensive Zusammenarbeit treibt die Innovationskraft der Branche voran. Einige große Marktteilnehmer planen, in den kommenden Jahren wesentliche Teile der Innenausstattung ihrer Flugzeuge additiv zu fertigen.
Auf einen Blick
Vorteile des 3D-Drucks für die Luftfahrt
-
Weniger Gewicht
Mit dem industriellen 3D-Druck können sehr stabile und leichte Strukturen hergestellt werden, die eine Gewichtsreduzierung von etwa 40-60 % ermöglichen. Die Auswirkungen: schlankere Kostenstrukturen, Materialeinsparungen und geringerer Kraftstoffverbrauch. -
Funktionale Integration
Das Verfahren ermöglicht die Integration maximaler Funktionalität in möglichst wenigen Teilen. Die Vorteile: Die Montage- und Qualitätssicherungskosten werden gesenkt und die Schwachstellen, die mit der Zusammenstellung vieler verschiedener Komponenten verbunden sind, werden beseitigt. -
Flexiblere Produktionsplanung
Durch den werkzeuglosen Produktionsprozess können Produktanpassungen schneller umgesetzt werden. Die Ersatzteilbevorratung kann durch die Fertigung auf Abruf ohne lange Vorlaufzeit erheblich reduziert werden. Die Kostenvorteile machen sich bei den langen Lebenszyklen von Flugzeugen deutlich bemerkbar. -
Industriekonforme Werkstoffe und Festigkeiten
EOS-Systeme verarbeiten spezielle Materialien für die Luft- und Raumfahrtindustrie. 3D-gedruckte Teile erfüllen branchenspezifische Anforderungen an verschiedene sicherheitsrelevante Gefahrenstufen, die in der Luft- und Raumfahrt üblich sind. -
Komplexe Teile
Der industrielle 3D-Druck ermöglicht ein breites Spektrum an Konstruktionsoptimierungen - von der Anpassung von Teilen und Upgrades bis hin zu exklusiven Innovationen , die nur additiv hergestellt werden können. -
GeringereCO2-Emissionen
Effizientere Triebwerke, Turbinen und Leichtbauteile für die Innenausstattung senken den Treibstoffverbrauch und damit dieCO2-Emissionen von Flugzeugen. -
Signifikante Kostensenkungen
Die additive Fertigung ist ein werkzeugloses Verfahren. Dies bedeutet, dass im Vergleich zu konventionellen Fertigungsverfahren erhebliche Kosteneinsparungen erzielt werden können.
Herstellung von Triebwerksteilen für die Luftfahrt mit industriellem 3D-Druck
Beim Bau von Motoren und Turbinen gilt es, Herausforderungen wie die Optimierung von Volumen, Leistung und Umweltfreundlichkeit zu meistern. In diesen Bereichen kann der 3D-Druck einen wichtigen Beitrag leisten. Er ermöglicht die Herstellung von Triebwerken mit anspruchsvollen Geometrien, definierten aerodynamischen und strömungsdynamischen Eigenschaften sowie von Leichtbaustrukturen, deren Einzelteile bis zu 60 % weniger wiegen. Auch die Verarbeitung von Superlegierungen ist mit dem 3D-Druck kostengünstiger, da der Materialeinsatz geringer ist. Das Ergebnis: eine deutlich geringere Umweltbelastung über die gesamte Lebensdauer des Flugzeugs. Aus einem Stück gefertigte Teile sind zudem widerstandsfähiger und weniger anfällig für Beschädigungen.
EOS-Technologie für die Luftfahrt
Was unsere Kunden zu sagen haben
Verriegelungsschacht für die Flugzeugtür eines Airbus A350
Airbus ist ein weltweit führendes Unternehmen in der Luft- und Raumfahrtindustrie und den damit verbundenen Dienstleistungen. Die 3D-Drucktechnologie von EOS hilft Airbus dabei, ein kosten- und ressourceneffizienteres Flugzeug zu bauen. Bei der additiven Fertigung einer Verriegelungswelle für Flugzeugtüren wurden bemerkenswerte Ergebnisse erzielt:
- 45 % Gewichtsreduzierung des additiv gefertigten Teils bei gleichbleibender Robustheit
- 25 % Einsparungen bei den Produktionskosten durch Reduzierung des Materialverbrauchs und der Montagezeiten
- Anzahl der Teile von 10 auf 1 reduziert
- Gewichtsreduzierung von mehr als 4 kg bei 16 Türschächten in einem A350-Flugzeug
Das Bauteil wurde aus Titan auf dem EOS-System EOS M 400-4 hergestellt.

Serienproduktion von Teilen für ein Airbus-Triebwerk mit EOS Systems
Die MTU Aero Engines, Deutschlands führender Triebwerkshersteller, hat ihre EOS-Maschinen optimiert, um sichere und kostengünstige Teile in Serie zu fertigen. Mit der additiven Fertigung fertigt die MTU die Endstücke für die Getriebefans der neuen Generation des PurePower® PW1100G-JM-Triebwerks des Airbus A320neo. Die Niederdruckturbine im A320neo-Turbofan ist die erste Turbine überhaupt, die standardmäßig mit additiv gefertigten Borescope Nodes ausgestattet ist. Die Kostenvorteile der EOS-Technologie waren einer der entscheidenden Faktoren sowohl für die Produktion als auch für die Entwicklung.

Qualitätssicherung in der Luftfahrt
Die hohen Sicherheitsanforderungen für die Zulassung sind eine große Herausforderung im Luftfahrtsektor. Jedes Teil, das fliegen soll, muss vom Rohmaterial bis zum Endprodukt kontinuierlich überwacht werden, und es darf keine Fehler geben.
In Zusammenarbeit mit EOS hat die MTU Aero Engines ein optisches Tomographieverfahren für den Bauprozess zu einem Serienprodukt entwickelt: EOSTATE Exposure OT . Die parametrisierbare Software lässt detaillierte Rückschlüsse auf die Qualität der Bauteile in jeder Schicht zu. Damit ermöglicht die optische Tomographie den Nachweis der Reproduzierbarkeit, verbessert die Vergleichbarkeit zwischen Bauteilen, Bauaufträgen und Drucksystemen und schafft die Voraussetzungen für eine kosteneffiziente Qualitätssicherung in der Serienfertigung.

-
Schnell: Entwicklungs-, Fertigungs- und Lieferzeiten werden erheblich verkürzt
-
Flexibel: sehr hohe Gestaltungsfreiheit
-
Kosteneffizient: geringer Material- und Werkzeugverbrauch, drastische Reduzierung der Entwicklungs- und Herstellungskosten
-
Das EOS-System unterstützt eine umfassende Qualitätssicherung, einschließlich Online-Überwachung und optischer Tomographie.
Herstellung von Baugruppen und Konstruktionsteilen mit industriellem 3D-Druck
Kostentreiber reduzieren - ein Schlüsselfaktor, um Strukturteile für den Luftfahrtsektor effizienter herzustellen. Digitalisierte Fertigungsverfahren bieten weitreichende Möglichkeiten. Dank der additiven Fertigung können mehrere Teile zu einem einzigen Bauteil kombiniert werden, wodurch Produktionsschritte wie die Montage entfallen. Auch die Lagerhaltung von Ersatzteilen, die derzeit viel Kapital bindet, wird überflüssig. Die Produktion erfolgt immer nur dann, wenn ein Teil benötigt wird, ohne dass irgendwelche Vorprozesse erforderlich sind. Außerdem sind additiv gefertigte Strukturteile vergleichsweise leichter, was dazu beiträgt, denCO2-Fußabdruck von Flugzeugen auszugleichen.

Liebherr
Teile für die primäre Flugsteuerung des Airbus A380
Liebherr Aerospace ist ein führender Anbieter von Systemen für die Luftfahrtindustrie. Mit mehr als fünfzig Jahren Erfahrung entwickelt, fertigt und wartet das Unternehmen eine Vielzahl von Flugzeuginstrumenten, einschließlich Flugsteuerungs- und Betätigungssystemen, Fahrwerken, Luftmanagementsystemen und Getrieben.
Mit seinem Metall-3D-Drucker EOS M 400-4 hat Liebherr einen innovativen Hochdruck-Hydraulikblock für den Airbus A380 hergestellt. Der neue additiv gefertigte Ventilblock erreicht die gleiche Leistung wie das konventionell gefertigte Teil, ist aber wesentlich leichter und enthält weniger Einzelkomponenten. Das Teil besteht aus einer Titanlegierung und erfüllt alle für den Flugbetrieb erforderlichen Zertifizierungsanforderungen.
- -35 % Gewichtsreduzierung
- -10 Einzelteile Funktionsintegration
Additiv gefertigte Innenausstattung und Flugzeugbeschläge
Die additive Fertigung mit Polymertechnologie wird auch für die Innenausstattung von Kabinen immer wichtiger. Dafür gibt es mehrere Gründe: In dieser Art von Umgebung sind eine hohe Individualisierung und eine flexible, werkzeuglose Produktion entscheidend. Die in der Kabine verwendeten Materialien müssen außerdem sehr strenge Anforderungen erfüllen, z. B. in Bezug auf die Entflammbarkeit. Die Technologie muss in der Lage sein, diese Materialien zu verarbeiten, insbesondere wenn komplexe Konstruktionen wie verdrillte Litzen erforderlich sind. Schließlich ist ein konsistenter Bauprozess mit minimal komplexer Nachbearbeitung erforderlich, ebenso wie eine digitale Ersatzteilstrategie und digitale Ersatzteile mit virtuellen Beständen. Die Polymertechnologie für den industriellen 3D-Druck erfüllt alle diese Kriterien.

Etihad Technik
Die Flugzeugkabine der Zukunft
Etihad Engineering ist der größte Dienstleister für Flugzeugwartung, -reparatur und -betrieb (MRO) im Nahen Osten. Als Tochtergesellschaft der Etihad Aviation Group bietet das Unternehmen in seinen modernen Anlagen am Abu Dhabi International Airport rund um die Uhr Wartungsdienstleistungen an, darunter Konstruktion, Reparaturen von Verbundwerkstoffen, Kabinenumrüstung und teilbezogene Dienstleistungen.
"Gemeinsam mit EOS eröffnete Etihad die erste 3D-Druck-Fertigungsanlage im Nahen Osten, die von der Europäischen Agentur für Flugsicherheit (EASA) für die Entwicklung und Herstellung von Flugzeugteilen zugelassen ist."
Das System EOS P 396 ermöglicht die Herstellung von Teilen aus Polymermaterialien wie PA 2241 FR und kann daher zur Herstellung von Kabinenteilen verwendet werden, die während der Flugzeuginspektion, den so genannten C-Checks, ausgetauscht werden. Außerdem können Defekte schnell behoben werden, indem die benötigten Teile während der regulären Wartungsarbeiten im Rahmen der Flugzeugstillstandszeiten (Line Maintenance) hergestellt werden.
"Etihad und EOS sind bekannt für qualitativ hochwertige Lösungen und technologische Innovationen und teilen die gleiche Denkweise: "Gemeinsam wollen wir das Design und die Produktion von Teilen für die Flugzeuginnenausstattung auf die nächste Stufe heben", sagt Markus Glasser, Senior Vice President für die Region EMEA bei EOS. "Additiv gefertigte Teile für die Flugzeuginnenausstattung bieten dank vereinfachter Reparaturen, Leichtbauweise, kürzerer Lieferzeiten und flexibler Anpassungsmöglichkeiten einen erheblichen Mehrwert. Damit werden einige der wichtigsten Herausforderungen der Luft- und Raumfahrtindustrie angegangen."
Markus Glasser | Senior Vice President für die Region EMEA | EOS GmbH

3D-Druck für die Luftfahrt
Unsere Lösungen für die Additive Fertigung & Kundenbeispiele