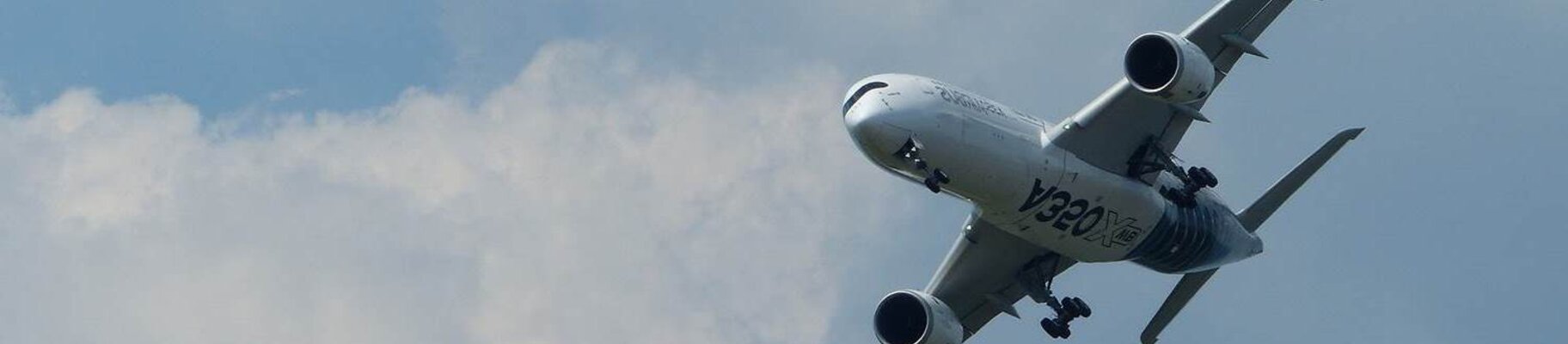
Sogeti High Tech Additive Manufacturing für den neuen Airbus A350 XWB
A350 XWB Cable Routing - In zwei Wochen vom Entwurf zum Bauteil | Erfolgsgeschichte
Der Moment, in dem sich ein völlig neues Verkehrsflugzeug zum ersten Mal in die Lüfte erhebt, ist immer etwas Besonderes - und das gilt ganz besonders für den Airbus A350 XWB. Als Kind des neuen Jahrtausends war von Anfang an klar, dass sich die Entwicklungsarbeit auf innovative Werkstoffe und Produktionsverfahren konzentrieren würde - das Ziel war nicht weniger als das effizienteste Flugzeug der Welt zu bauen. Als Zukunftstechnologie war auch die additive Fertigung eine Möglichkeit, die es bei der Entwicklung zu berücksichtigen galt. Im Rahmen eines Pilotprojekts gelang es den Experten von Sogeti High Tech, eine Kabelhalterung am vorderen Holm des Seitenleitwerks des Passagierflugzeugs in Rekordzeit zu entwickeln: Von der ersten Skizze bis zum fertigen Teil vergingen nur zwei Wochen. Die Technologie und das Know-how von EOS spielten bei diesem Entwicklungsprozess eine entscheidende Rolle.
"Ein bestehendes Bauteil in nur zwei Wochen 'AM-ready' zu machen, bedeutete, dass wir es auf Anhieb schaffen mussten. Die exzellente, proaktive Zusammenarbeit mit EOS hat dieses ehrgeizige Unterfangen möglich gemacht - mit hervorragenden Ergebnissen."
Carlos Ribeiro Simoes | Leiter des Additive Manufacturing Angebots | Sogeti High Tech
Herausforderung
Zeitkritische Entwicklung und Fertigung einer Kabelführungshalterung für eine Kamera im Seitenleitwerk des A350 mittels additiver Fertigung
Bei dem Projekt ging es konkret um die Herstellung einer Kabelführungshalterung für das neueste Airbus-Modell. Die Halterung wurde schließlich für die Stromversorgung und den Datentransport einer im Seitenleitwerk untergebrachten Kamera benötigt, die den Passagieren einen Blick nach draußen und den Piloten eine Orientierung am Boden ermöglicht.
Das Lastenheft verlangte ein funktionstüchtiges und serientaugliches Bauteil. Mit dieser Aufgabe wurde Sogeti High Tech betraut, eine hundertprozentige Tochtergesellschaft von Cap Gemini S.A., die an der Pariser Börse notiert ist.
Die besondere Herausforderung in diesem Fall war die kurze Vorlaufzeit von nur zwei Wochen. Die gesamte Entwicklung musste innerhalb dieses Zeitrahmens abgeschlossen werden: Von der Analyse des Bauteils und der aktuellen Montageanordnung über eine Parameterstudie zur Optimierung der Topologie und deren Auslegung bis hin zur Konstruktion und Fertigung des fertigen Bauteils. Außerdem sollte die Halterung so wenig Stützstrukturen wie möglich haben, um Nacharbeiten zu vermeiden.
Darüber hinaus verlangten die Spezifikationen für das Bauteil die Integration der einrastenden Kabelhalterung, eine Gewichtsreduzierung und die Einhaltung der strengen Anforderungen für die spätere Zertifizierung durch die Luftfahrtindustrie.
Das konventionell gefertigte Bauteil bestand aus Blechformteilen und zahlreichen Nieten - insgesamt mehr als 30 Einzelteile. Die Steckverbinder im oberen Bereich waren aus Kunststoff und damit aus einem anderen Material als die übrigen Einzelteile der Halterung. Ziel war es, eine integrierte Lösung zu entwickeln, die aus einem einzigen Teil besteht, das auch die Steckverbinder enthält und damit die Konstruktions- und Montagezeiten deutlich reduziert. Die Zielvorgabe für die Gewichtsreduzierung bei der additiven Fertigung wurde durch eine Parameterstudie auf Basis einer Topologieoptimierung ermittelt.
Lösung
Die Reduzierung auf ein einziges Bauteil und die Herstellung auf EOS M 400 minimiert die Produktionszeit auf 19 Stunden
Für das neue Bauteil folgte Sogeti High Tech dem bewährten Entwicklungsprozess für die Konstruktion additiv gefertigter Teile. Am Anfang des Projekts stand eine Analyse des bestehenden, konventionell gefertigten Bauteils im Hinblick auf den anstehenden Fertigungsprozess - mit einem äußerst positiven Ergebnis. Das Bauteil war aufgrund seiner Funktionalität, seines Materials und seiner bisher komplexen Struktur ein idealer Kandidat für die pulverbettbasierte 3D-Drucktechnologie von EOS. Die gestalterische Freiheit dieser Technologie erlaubt es, komplexe Strukturen in einem Stück zu fertigen, so dass ein gewichtssparendes Design gewählt werden kann, ohne die Funktionsintegration zu vernachlässigen.
Anhand dieser Analyse konnte dann der so genannte Design Space - der Raum, den die Kabelführungshalterung einnehmen darf - definiert werden. Als Material wurde die Aluminiumlegierung AlSi10Mg gewählt, die sich ideal für dünnwandige, komplexe Strukturen eignet. Die Schnittstellen zu den Außenbereichen blieben gleich und bildeten den Nichtauslegungsraum, so dass an ihnen keine Änderungen vorgenommen werden mussten. Die definierten Lasten wurden als Randbedingungen für die Topologieoptimierung in der Parameterstudie herangezogen und bildeten die Grundlage für einen neuen Entwurf.
Wie üblich wurde für die Berechnungen zur Topologieoptimierung eine CAE-Software verwendet; für das Re-Design wurde dagegen eine spezielle Lösung für den Entwurf von Strukturen mit Freiformflächen eingesetzt. Sogeti High Tech hat den Entwurf selbst erstellt. Um die Vorlaufzeit von zwei Wochen einzuhalten, berechnete EOS die Bauzeit und optimierte die Parameter aus den Ergebnissen der Topologieoptimierung mit der Software EOSPRINT. So entstand die CAE-Implementierung für das hergestellte Teil, wobei auch die Möglichkeiten und Grenzen des Fertigungsprozesses und die Notwendigkeit, Stützstrukturen zu vermeiden, berücksichtigt wurden.
"Neben hervorragender Hardware bietet EOS auch umfassendes Know-how bei der Realisierung additiv gefertigter Bauteile, was wir sehr schätzen."
Carlos Ribeiro Simoes | Leiter des Additive Manufacturing Angebots | Sogeti High Tech
Ergebnisse
Dank der Zusammenarbeit zwischen Sogeti und EOS konnte ein für die additive Fertigung optimiertes Bauteil entwickelt werden, das die Gestaltungsfreiheit der DMLS-Technologie voll ausschöpft und gleichzeitig deren Einschränkungen berücksichtigt. So konnten Steckverbindungen für die Kabelführung in das Design integriert und lokale Verstärkungen in bestimmten kritischen Bereichen eingebaut werden, um die Struktur zu optimieren. Selbsttragende Durchbrüche und Verstrebungen innerhalb des Bauteils helfen, den Aufwand und damit die Nachbearbeitungskosten gering zu halten.
Außerdem kann die Halterung extrem schnell hergestellt werden, wann immer sie benötigt wird. Die Herstellung - die auf einer EOS M 400 mit Schichtdicken von 90μm - dauert nur noch 19 Stunden statt der früher benötigten 70 Tage.
Dies entspricht einer Verkürzung der Produktionszeit um weit über 90 %. Das liegt vor allem daran, dass die vielen Einzelschritte und ehemals 30 Teile in einem zentralen Bauteil zusammengeführt wurden, das nun in einem Durchgang produziert werden kann. Außerdem müssen die Einzelteile nicht mehr aufwendig konstruiert und auf Lager gehalten werden. Auch die Lagerhaltung für die gesamte Baugruppe ist nun wesentlich unkomplizierter.
Sogeti konnte nicht nur in der Produktion, sondern auch in der Entwicklung viel Zeit einsparen. Der gesamte Prozess von der ersten Skizze bis zum fertigen Bauteil dauerte nur zwei Wochen. Das ist eine phänomenale Vorlaufzeit. Gleichzeitig bedeutet das Design auch eine größere Gewichtseffizienz.
Während das konventionell gefertigte Originalteil 452 Gramm wog, bringt der additiv gefertigte Kabelträger nur 317 Gramm auf die Waage - und in der Luftfahrtindustrie zählt bekanntlich jedes Gramm, um den Treibstoffverbrauch auf ein Minimum zu reduzieren. Der Kunde Airbus war mit dem Ergebnis mehr als zufrieden.
Das Ergebnis auf einen Blick
- -29 Einzelteile Funktionsintegration
- -90% Reduzierung der Produktionszeit
- -135 Gramm Gewichtsreduzierung
Mehr erfahren
Erleben Sie drei Jahrzehnte Pionierarbeit im 3D-Druck mit EOS