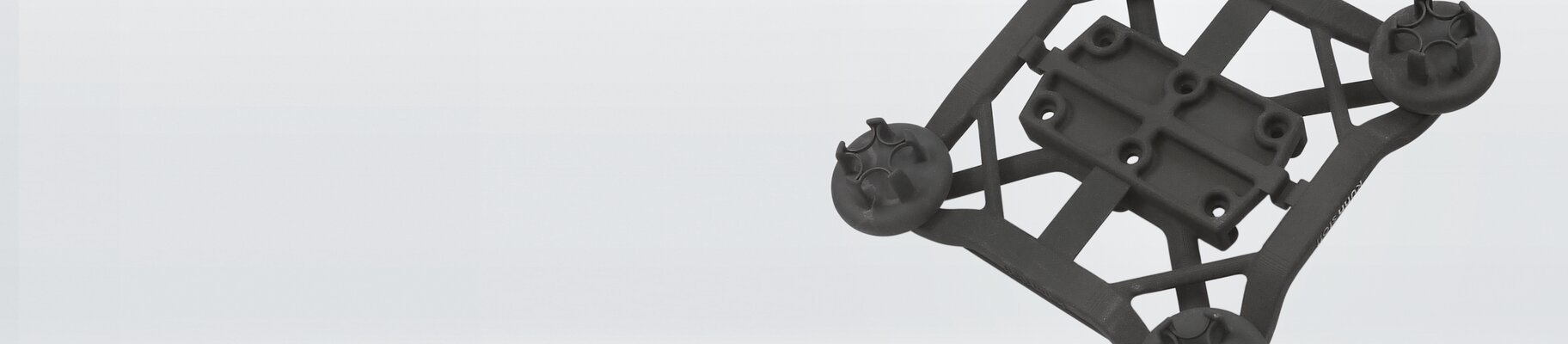
EOS 기술로 가볍고 내구성이 뛰어난 적층 제조 그립 시스템
비트만 그룹 & 쿤스톱 | 사례 연구
EOS 기술로 가볍고 튼튼하게 제작된 기능성 베이스 플레이트가 있는 기관지 그리퍼
손은 인류 진화의 결정적인 디딤돌 중 하나로, 엄지와 다른 손가락이 마주보는 인간의 손은 물건을 쥐고, 탐색하고, 작업하는 데 이상적인 도구입니다. 따라서 손은 문화 활동과 기술 발전의 핵심입니다. 기계가 사용되는 공정 중 하나는 다음 작업 단계로 옮기기 위해 원하는 거의 모든 부품을 자동으로 잡는 것입니다.
이러한 그리핑 기계는 엔지니어링의 걸작입니다. 쿤스토프(Kuhn-Stoff GmbH & Co KG)는 EOS 적층 제조 기술을 적용하여 전문 엔지니어링에 전념해 왔습니다. 이 공정은 레이저 빔으로 녹인 플라스틱 분말로 기계 부품을 층층이 형성하는 과정을 수반합니다. 이러한 방식으로 쿤스톱은 독일 뉘른베르크에 위치한 비트만 로봇 시스템 GmbH를 위해 매우 가볍고 튼튼하며 내구성이 뛰어난 기관지 그리퍼를 개발 및 생산했습니다. 이 그리퍼 4개는 공압 덕트가 통합된 지지 프레임에 장착되어 있습니다.

"우리는 수년 동안 다양한 자동화 분야에 걸쳐 적층 가공으로 제작된 부품을 배치해 왔습니다. 기관지 그리퍼는 우리의 모든 요구 사항을 충족하며, 실제로는 이를 뛰어넘습니다. 이 부품은 일상적인 성능 면에서 매우 신뢰할 수 있습니다."
마이클 톨츠 | 독일 기술 책임자 겸 지사장 | 뉘른베르크의 비트만 로봇 시스템 GmbH
도전 과제
고객은 로봇 및 자동화 시스템 제조업체입니다. 쿤스태프는 공압 메커니즘을 통해 생산 기계에서 기계 부품을 들어 올리고 운반한 다음 내려놓는 기계식 그리퍼를 다시 설계해 달라는 요청을 받았습니다. 그리퍼는 이전 제품보다 가벼우면서도 필요한 하중을 이동시킬 수 있어야 한다는 요구 사항이 설정되었습니다. 설계의 복잡성은 단순화되어야 하고 부품은 효율성 기준을 충족할 수 있어야 합니다.
이러한 그립 시스템은 주어진 시간 내에 가능한 한 많은 기계 부품을 이동하기 위해 빠르게 작동해야 한다는 물리학적인 측면에서 무게의 중요성이 부각되었습니다.
질량이 불활성이라는 사실은 질량을 움직이게 하려면 힘을 가해야 한다는 것을 의미합니다. 하중이 무거울수록, 그리고 빠르게 움직일수록 가속과 감속에 필요한 힘은 더 커집니다.
에너지 효율의 관점과는 별개로, 이 사실은 시스템의 내구성에도 특히 부정적인 영향을 미칩니다. 작용하는 힘이 클수록 기계의 마모가 증가하기 때문입니다.
이전 버전의 그리퍼는 알루미늄, 고무 튜브 및 여러 연결 요소로 만들어져 생산 비용이 많이 들었습니다. 쿤스톱의 레이어 제조 전문가들은 설계를 대폭 간소화한다는 목표를 세웠습니다. 기계 부품의 새로운 구조는 무게 감소에 일정 부분 기여해야 했습니다. 나머지 부분은 적층 제조의 핵심 장점 중 하나인 구조 최적화를 통해 달성해야 했습니다. 작업이 시작되자 곧 새로운 그리퍼를 제작 후 마무리 작업이나 추가 조립 없이 단일 부품으로 생산할 수 있다는 것이 분명해졌습니다.

솔루션
쿤스톱 팀은 먼저 그리퍼의 기능과 작동 요건을 검토하기 시작했습니다. 압축 공기가 유연한 멤브레인으로 유입되면 그리퍼의 집게가 열리고, 압축 공기가 꺼지면 시스템이 닫히는 것과 마찬가지로 그리퍼의 집게가 닫힙니다. 플라스틱의 유연성 외에도 부품은 필요한 동작 순서를 수행하기 위해 90°까지 회전할 수 있어야 합니다. 이러한 요구 사항을 고려하여 필요한 부품 수를 단 두 개의 부품으로 줄일 수 있었습니다.
설계 프로세스가 완료되자 쿤스톱은 FORMIGA P 100을 사용하여 새로운 그립 시스템 생산 작업을 시작했습니다. 단 몇 시간 만에 그립 시스템의 두 구성품이 폴리아미드로 생산되었습니다. EOS 기술 덕분에 공압 덕트와 커넥터가 베이스 플레이트에 완전히 통합되었습니다.
"평소와 마찬가지로 EOS 시스템을 사용한 생산은 원활하고 문제없이 진행되었습니다. 최종 결과는 다시 한 번 모든 관계자들에게 깊은 인상을 남겼습니다. 단 한 번의 공정 단계로 고객의 모든 요구 사항을 뛰어넘는 기능적으로 통합된 부품을 만들 수 있었습니다. 요컨대, 적층 가공은 이제 일상적인 현실이 되었지만 그 결과물은 여전히 놀랍습니다."라고 Kuhn-Stoff GmbH의 CEO인 Hannes Kuhn은 말합니다.

"우리는 8년 이상 EOS 기술을 사용해 왔으며 긍정적인 결과만 얻었습니다. 설계 유연성을 올바르게 적용하면 고객에게 시장에서 거의 독보적인 이점을 제공할 수 있는 상당한 이점을 제공합니다."
하네스 쿤 | CEO | Kuhn-Stoff GmbH & Co KG
결과
무게 감소라는 주요 목표를 달성하기 위해 쿤스톱은 220g으로 86% 감량하는 데 성공했습니다. 가벼운 무게에도 불구하고 그리퍼는 까다롭고 지속적인 사용에도 필요한 하중을 견딜 수 있으며, 5백만 사이클 후 스트레스 테스트를 중단하고 지정된 서비스 수명에 도달했습니다. 이 기간 동안 단 한 건의 결함이나 고장도 발생하지 않았습니다. 그 이유는 베이스 플레이트에 통합된 에어 덕트에도 불구하고 달성한 구조의 강도 덕분입니다. 또한 유연한 설계 덕분에 작은 충돌이 발생하더라도 그리퍼 시스템이나 사출 성형 공구가 손상되지 않습니다. 경우에 따라서는 더 가벼운 무게 덕분에 더 작은 로봇 유형을 사용할 수 있어 비용을 크게 절감할 수 있습니다. 또한 그리퍼의 높이가 낮아 사출 성형기의 클램핑 플래튼의 필요한 개방 폭이 줄어들어 작업 사이클 수를 늘릴 수 있었습니다. 결론은 운영 비용 절감입니다.
기존 제품 대비 제조 비용이 50% 절감되었습니다. 이는 부품 수를 21개에서 2개로 줄였을 뿐만 아니라 무게를 줄였기 때문입니다. 마찬가지로 중요한 것은 생산 시간이 단축되었다는 점입니다. 이전에는 12일이 걸렸던 그립 시스템을 이제 3일이면 제조할 수 있습니다.
"새로운 그립 시스템에 매우 만족하고 있습니다. 이 제품은 이전 제품과 마찬가지로 고강도, 지속적인 사용에도 효과적이지만 더 저렴하고 가벼우며 더 빠르게 생산할 수 있다는 것이 입증되었습니다. 저는 그립 제조 분야에서 적층 제조가 기관지 그립퍼 생산에 가져온 것만큼 중요한 발전을 본 적이 없습니다. 이 생산 방식은 당사의 자동화 솔루션에 매우 긍정적인 영향을 미쳤습니다."라고 Wittmann Robot Systeme GmbH의 기술 책임자 겸 지사장인 Michael Tolz는 설명합니다. 때때로 혁명은 진화에 비해 장점이 있을 수 있습니다.
한 눈에 보는 결과
-
-1350그램: 무게 86% 감소
-
비용 -50% 절감: 생산 비용 50% 절감
-
구성 요소 -19개: 개별 구성 요소가 21개에서 2개로 감소

EOS 사례 연구
EOS와 함께 30년 동안 3D 프린팅의 우수성을 개척해 온 과정을 살펴보세요.