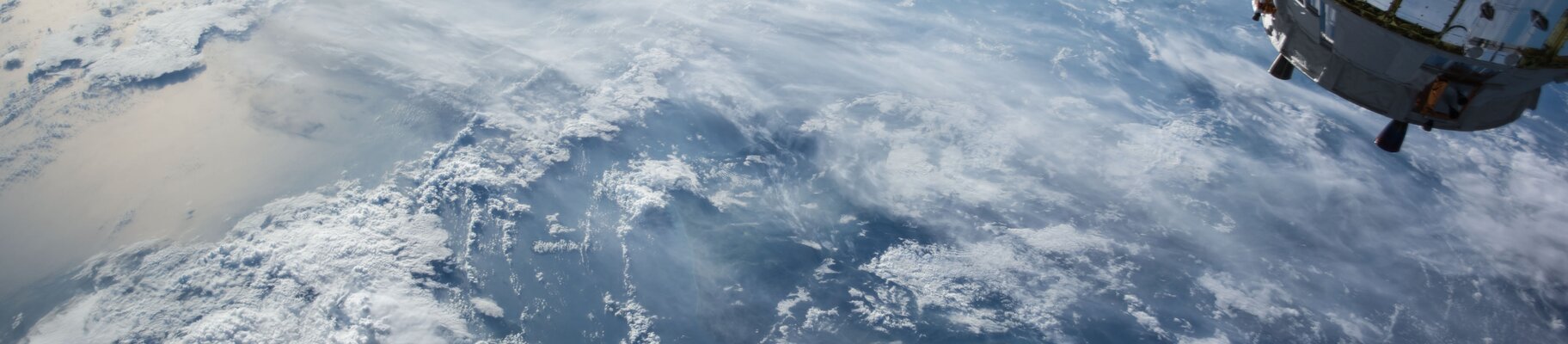
로켓 엔진
기상 데이터, 통신, 위성 위치 확인 시스템, 글로벌 사진 및 지도 등 점점 더 많은 서비스가 소형 위성을 활용하고 있거나 경우에 따라서는 소형 위성에 전적으로 의존하고 있습니다. 이러한 초소형 위성을 궤도에 올리려면 소형 발사기가 필요합니다. 이러한 발사체에 대한 시장 수요는 꾸준히 증가하고 있습니다. 지난 몇 년 동안 이 "새로운 우주" 산업은 다양한 스타트업과 개발 전문 기업들에 의해 급속도로 성장했습니다. 가장 효율적인 엔진으로 가장 큰 페이로드를 우주로 성공적으로 발사하는 회사가 경쟁에서 승리할 것입니다.
적층 제조는 최적의 엔진 설계를 유지하면서 비용을 낮게 유지하는 핵심 접근 방식이지만, 이는 엔진을 단일 부품으로 3D 프린팅할 수 있는 경우에만 가능합니다.
로켓 엔진 3D 프린팅
3D 프린팅은 로켓 엔진을 제작할 때 결정적인 이점을 제공합니다. 예를 들어 일체형 냉각 채널을 연소실에 통합하거나 여러 부품을 하나의 올인원 디자인으로 통합하는 등 부품의 기능을 완전히 재구상하고 재창조할 수 있습니다.
"EOS와 AMCM의 지원을 받는 미국 스타트업 기업 런처는 중소형 페이로드를 그 어느 때보다 효율적으로 우주로 발사하기 위해 노력하고 있습니다. 그 결과 새롭고 혁신적인 로켓 설계와 단일 부품으로 적층 제조된 세계 최대 로켓 엔진을 개발했습니다."
엔진은 표준 로켓 디자인을 기반으로 하지만 최적의 냉각을 위해 내부 리브가 확장되어 있습니다. 런처는 3D 프린팅을 통해 이 새로운 디자인을 빠르고 비용 효율적으로 제작, 테스트, 추가 개발하는 데 성공했습니다.

세계에서 가장 큰 단일 부품 3D 프린팅 로켓 엔진
제작 공간의 크기와 까다로운 재료 특성 등이 장애물이었습니다. 고객 요구 사항에 맞춘 특수 기계를 제공하는 EOS 그룹의 회사인 AMCM이 이 문제를 해결했습니다.
"AMCM의 M4K 장비로 구리 합금으로 3D 프린팅한 연소실은 액체 로켓 엔진용 단일 부품으로는 세계에서 가장 큰 연소실입니다."
챔버의 높이는 86cm(34인치), 배출 노즐 직경은 41cm(16인치)입니다. 이 부스터는 최근 E-2 부스터의 개발 및 테스트 프로그램을 가속화하기 위해 열린 미 공군 우주 피치의 날에서 150만 달러의 상금을 받았습니다. 첫 번째 대규모 테스트 실행이 이미 계획되어 있습니다. 애니메이션은 적층 가공 및 기존 방식으로 제조된 부품으로 구성된 전체 연소실을 보여줍니다.

"기존에는 이러한 유형의 부품을 제조하려면 맞춤형 기계에 수백만 달러를 투자해야 했습니다. 하지만 이제 3D 프린팅을 사용하면 연소실, 노즐, 넥을 하나의 부품으로 결합하여 프린팅할 수 있습니다. 이러한 발전 덕분에 작업이 그 어느 때보다 쉬워졌습니다."
맥스 하트, 창립자 런처
사례 연구
아리안 6 로켓 엔진용 사출 헤드
아리안 그룹은 기존 248개의 부품을 통합하고 단가를 낮추기 위해 새로운 아리안 6 로켓 부스터의 핵심 엔진 부품을 생산하기 위해 산업용 3D 프린팅을 선택했습니다. 아리안 그룹은 EOS 애디티브 마인즈 팀과 협력하여 위험을 분석하고 비용을 예상하며 레이아웃 설계 및 흐름 계획을 포함한 생산 공정을 최적화했습니다.
이 협업은 훌륭한 결과를 낳았습니다:
- -2165시간 생산 시간 단축
- -50% 비용 절감
- -247개의 개별 부품이 단일 부품으로 축소됨
- 기능 통합
아래 동영상을 통해 자세히 알아보세요.
"아리안 프로그램은 우리의 혁신적인 강점과 EOS의 전문성을 결합한 것입니다. 우리는 함께 로켓 엔진용 사출 헤드의 적층 제조를 준비하고 있습니다. 그 결과 생산 시간이 크게 단축되고 비용이 50% 절감되는 등 놀라운 성과를 거두고 있습니다."
스테펜 베이어 박사, 아리안그룹 생산 기술 책임자 - 재료 및 공정 부문 책임자