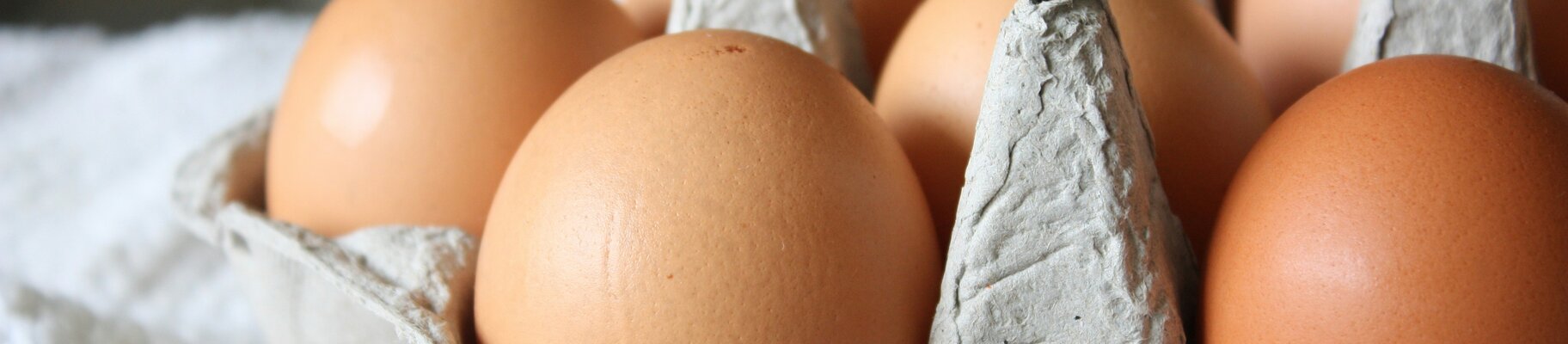
성형 섬유 생산을 위한 3D 프린팅 도구
페이르 엔지니어링 | 사례 연구
깔끔한 포장
- 툴 비용 50% 절감
- 생산 시간이 몇 주로 단축됩니다.
- 소규모 배치 규모에서도 수익성 확보
익숙한 표현인 날달걀과 같은 물건을 취급하세요. 달걀 껍질만큼이나 단단한 달걀 상자는 일반적으로 집으로 안전하게 운송하기 위해 가장 먼저 선택되는 포장재입니다. 성형 펄프 포장은 보호 기능을 제공하고 환경 친화적입니다. 오스트리아의 엔지니어링 서비스 제공업체인 Payr는 적층 가공을 통해 이 도구를 생산에 최적화하여 더 빠르고 비용 효율적으로 생산할 수 있도록 했습니다. 또한 운송 거리를 단축하고 소량 생산이 가능해졌습니다.

"EOS 장비를 사용하여 다른 공급업체의 장비로는 제조할 수 없는 견고한 부품을 생산할 수 있게 되었습니다."
피터 폴 페이 | Payr 엔지니어링 전무 이사
도전 과제
성형 펄프 - 단어 자체는 재료만큼 흔하지 않습니다. 폐지로 만들든 풀과 같은 재생 가능한 섬유 재료로 만들든, 점점 더 많은 기업이 재활용 및 재활용 가능한 재료를 보호 포장재로 사용하고 있습니다. 소매 환경에서는 처음에 언급한 달걀 상자부터 전자제품이나 가전제품을 보호하는 맞춤형 포장에 이르기까지 다양합니다. 기술 발전 덕분에 오늘날 이 소재는 더 많은 기능을 수행할 수 있습니다. 발수성, 방수성 등 플라스틱 없이도 이 모든 것이 가능합니다.
그 결과 이 소재는 다른 응용 분야에서도 관심을 끌게 되었습니다. 지금까지는 포장에 필요한 조각 수가 문제였습니다. 그 이유 중 하나는 생산 공정입니다. 기본적으로 펄프라고 불리는 물에 용해된 소재를 진공을 통해 작은 구멍이 많은 코팅이 된 천공 몰드로 빨아들입니다. 액체는 이 스크린을 통해 배출되거나 빨려 들어갑니다. 주로 아시아 생산 현장에서는 구멍이 뚫린 몰드를 수작업으로 체로 덮었는데, 이는 매우 비싸고 시간이 많이 걸리는 절차였습니다.
Payr는 도구, 특히 체에 초점을 맞춰 이러한 문제를 해결했습니다: "이러한 부품을 수작업으로 완성하려면 국내에서는 비용이 너무 많이 들고 해외로 긴 운송 경로를 거쳐야 하므로 비용이 수반됩니다. 기존 공정의 생산 및 제조 시간으로 인해 어느 쪽이든 최적화할 수 있는 잠재력이 있었습니다."라고 Payr Engineering의 상무이사이자 Payr 그룹의 주주인 Peter Paul Payr는 설명합니다. "그래서 우리는 스크린 생산을 위한 대안을 찾다가 적층 제조에서 그 대안을 찾았습니다."
비용 효율적이고 지속 가능한
성형 펄프 포장의 생산 공정

솔루션
Payr는 특히 혁신적인 접근 방식을 고안해냈습니다. 금형과 스크린은 금속 코어와 격자 구조라는 두 가지 구성 요소로 이루어져 있었는데, 수작업으로 모양을 만들고 적용했습니다. 적층 가공 덕분에 정적으로 안정적인 금형의 원래 기능과 금형 전체에 규칙적으로 분산된 배수 기능을 하나의 부품에 결합한 혁신적인 배수 구조가 개발되었습니다. 그 결과 단 한 번의 생산 단계만 거치면 됩니다. 따라서 생산이 더욱 간소화되고 전체 공정 속도가 빨라지면서도 고품질을 동일하게 유지할 수 있습니다.
Payr가 선택한 소재는 적층 제조에서 흔히 사용되는 플라스틱 PA 12입니다. 이 소재는 3D 프린터로 미세한 스크린 구조를 훌륭하게 재현할 수 있기 때문에 저렴하면서도 충분히 견고합니다. 피터 폴 페이르는 이것이 쉬운 일이 아니라고 말합니다: "EOS는 포트폴리오에 매우 고성능의 제품인 EOS P 396. 특히 격자 구조와 관련하여 다른 알려진 제조업체의 성능을 훨씬 능가하는 성능을 보유하고 있습니다. 다른 어떤 장치로도 이 애플리케이션에 필요한 구성 요소의 안정성을 달성할 수 없었습니다."
한편으로는 배수 구조의 기하학적 구조에 따라 재료가 금형에 얼마나 달라붙는지, 나중에 포장이 얼마나 안정적으로 유지되는지가 결정되기 때문에 펄프의 흐름 저항을 정확하게 제어하려면 정밀도가 매우 중요하며, 따라서 성공의 열쇠가 됩니다. 다른 한편으로는 수분이 얼마나 남아 있는지에 영향을 미쳐 건조 시간에 영향을 미칩니다. 물론 적층 제조는 금형 설계의 자유도가 높고 생산에 필요한 전체 시간이 짧다는 '고전적인' 장점도 제공합니다.
결과
그러나 진실의 순간은 항상 목표가 달성되었는지 확인할 때 찾아옵니다. 이전에는 조달에 몇 달이 걸렸지만 이제는 몇 주 만에 새로운 결합형 석션 유닛을 사용할 수 있습니다. 마찬가지로 중요하고 인상적인 것은 전환을 통해 달성한 비용 절감입니다: "우리는 고객에게 상당한 이점을 제공할 수 있습니다. 툴 제조 비용이 기존 제조 방식보다 최소 50% 이상 절감되었습니다. 따라서 3D 프린팅 금형은 소량 또는 다품종 포장에 매력적입니다."라고 Peter Paul Payr는 자랑스럽게 말합니다. 적층 제조가 제공하는 디자인의 자유로움 덕분에 벽 두께가 다른 최종 포장재를 생산할 수도 있습니다. 즉, 필요한 곳에만 재료를 사용할 수 있습니다.
페이르는 최적화된 스크린 기술과 함께 전체 생산 공정을 검토했고, 최적화된 도구를 기반으로 자체 개발한 FIBRA MINI 성형 펄프 플랜트를 통해 더 많은 잠재력을 활용할 수 있었습니다. 예를 들어 흡입 및 배수 기술을 개선할 수 있었습니다. 그 결과 품질은 향상되었지만 벽을 더 얇게 만들 수 있기 때문에 건조에 필요한 에너지가 줄어들고 자재 비용이 절감됩니다. 동시에 더 적은 재료는 인쇄에서 재활용에 이르는 전체 수명 주기에 걸쳐 이점을 제공합니다.
기업이 얻을 수 있는 또 다른 이점은 공급망의 탄력성이 훨씬 더 높아진다는 점입니다. 생산 단계를 보다 비용 효율적으로 재배치하는 것은 드문 경우일 뿐만 아니라 성형 펄프 제품 공급업체의 독립성을 높여주는 경로를 형성합니다. 이와 동시에 공급망의 간소화는 환경적 이점도 제공합니다. 지구 반 바퀴를 운송할 필요가 없어지면 자연히 이산화탄소 배출량도 줄어들기 때문입니다. 그러나 지속가능성을 위해 더욱 중요한 것은 성형 펄프의 경쟁력이 더욱 높아져 점점 더 많은 플라스틱 포장을 대체할 수 있다는 사실입니다.
따라서 페이르 엔지니어링과 고객사에게 성형 펄프 생산 공구의 생산 전환은 여러 면에서 성공적인 프로젝트입니다. "운송 경로를 단축하고 생산량을 회복하는 동시에 비용을 절감하고 품질을 향상시킬 수 있는 곳이 또 어디 있을까요?"라고 피터 폴 페이르는 묻습니다. 그리고 이 모든 이점은 적층 제조라는 기술에서 시작됩니다. 앞으로는 날달걀과 같이 점점 더 많은 제품이 생산자에서 소비자에게 전달될 것입니다.
정확하고 안정적인
PA 2200 플라스틱 소재의 혁신적인 격자형 배수 구조의 3D 프린팅 펄프 몰드


"품질 변동을 없애고 비용과 출시 시간을 단축할 수 있습니다. 고객은 공급망의 탄력성을 높이고 운송 비용과 플라스틱 포장의 양을 줄일 수 있습니다."
피터 폴 페이 | Payr 엔지니어링 전무 이사
EOS 사례 연구
EOS와 함께 30년 동안 3D 프린팅의 우수성을 개척해 온 과정을 살펴보세요.