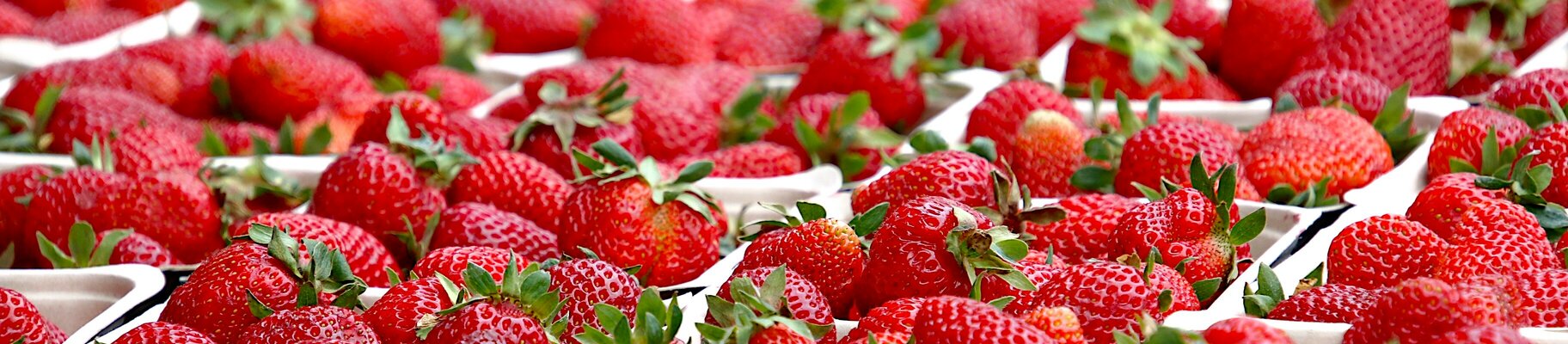
제조의 재정의 - 3D 프린팅 충진 시스템의 지능형 자동화
APC-TEC | 사례 연구
규정 준수 패키징
- 86% 비용 절감
- 더 적은 부품과 더 짧은 조립 시간으로 생산 속도 향상
- (EU) 1935/2004, (EU) 10/2011 및 GMP 표준을 준수하는 규정 준수
- 복잡한 기계 부품 제거 및 프로그래밍 복잡성 감소로 인한 안정성 향상
- 컴팩트한 프로덕션 환경을 위한 공간 절약형 디자인
식품 포장 산업은 효율성, 비용 절감, 더욱 엄격해진 안전 규정 준수 사이에서 균형을 맞춰야 하는 혁신의 압박을 끊임없이 받고 있습니다. 기존의 자동화 방식은 부피가 크고 복잡한 기계 시스템에 의존하는 경우가 많아 유지보수 및 프로그래밍이 많이 필요합니다.
생산 체인에서 작은 조정만으로도 상당한 경쟁 우위를 확보할 수 있으며, 식품 안전 인증을 받은 재료를 사용한 적층 제조(AM)는 더 큰 도약을 가능하게 하는 것으로 입증되고 있습니다. 한 가지 예로 제품 취급을 혁신하여 복잡성, 비용 및 처리 시간을 줄인 혁신적인 확장 플랩 메커니즘이 있습니다. 이 획기적인 접근 방식은 자동화를 향상시킬 뿐만 아니라 현대 식품 생산에서 가능한 것을 재정의합니다.

"산업용 3D 프린팅으로 생산을 간소화함으로써 비용을 절감했을 뿐만 아니라 기계 고장 위험을 줄여 장기적인 운영 안정성을 보장할 수 있었습니다."
폴 보치오넥 | apc-tec GmbH의 총괄 매니저
도전 과제
한 식품 산업 제조업체는 종이 인레이가 비스킷과 캔 표면이 직접 접촉하는 것을 방지하면서 섬세한 비스킷 스틱을 캔에 넣을 수 있는 효율적인 솔루션이 필요했습니다. 외부 그리퍼를 사용하는 기존 방식은 과도한 공간과 복잡한 프로그래밍, 수많은 개별 부품이 필요했기 때문에 비용, 처리 시간, 잠재적 오류에 대한 우려가 있었습니다. 또한 전체 솔루션은 엄격한 식품 접촉 규정을 준수하는 동시에 빠르게 변화하는 생산 조건에서 높은 기계적 신뢰성을 유지해야 했습니다.
솔루션
apc-tec GmbH는 포장 공정을 효율적으로 자동화하기 위해 컴팩트한 지능형 기계 시스템을 개발했습니다. 기존의 외부 그립 메커니즘을 사용하는 대신 apc-tec은 비스킷 스틱으로 채우기 전에 종이 인레이를 제자리에 고정하는 확장 클램프를 캔 내부에 통합했습니다. "우리의 혁신적인 솔루션은 기존 제조 방식으로는 달성할 수 없었던 방식으로 이 생산 공정을 최적화했습니다. EOS의 3D 프린팅으로 구현된 지능형 기계 부품 설계와 완전한 식품 접촉 신고를 결합하여 식품 안전 자동화의 판도를 바꿨습니다."라고 apc-tec GmbH의 총괄 매니저인 폴 보치넥(Paul Bocionek)은 설명합니다.
이 접근 방식은 필요한 구성 요소의 수를 크게 줄여 추가 센서와 복잡한 프로그래밍 가능 로직 컨트롤러가 필요하지 않습니다. 전체 시스템은(EU) 1935/2004,(EU) 10/2011 및 GMP(우수 제조 관리 기준) 표준을 준수하는 PA 2200을 포함하여 식품 안전 인증을 받은 재료를 사용하여 설계 및 생산되었습니다. 또한 확장 플랩은 고정밀 산업용 3D 프린팅으로 제조되어 신속한 프로토타이핑, 반복 및 생산이 가능합니다. "EOS 장비는 높은 기계적 신뢰성을 제공할 뿐만 아니라 규정을 준수하는 PA 2200 소재를 사용하여 각 부품이 효율성 저하 없이 엄격한 식품 산업 요건을 충족합니다."라고 Bocionek은 강조합니다.
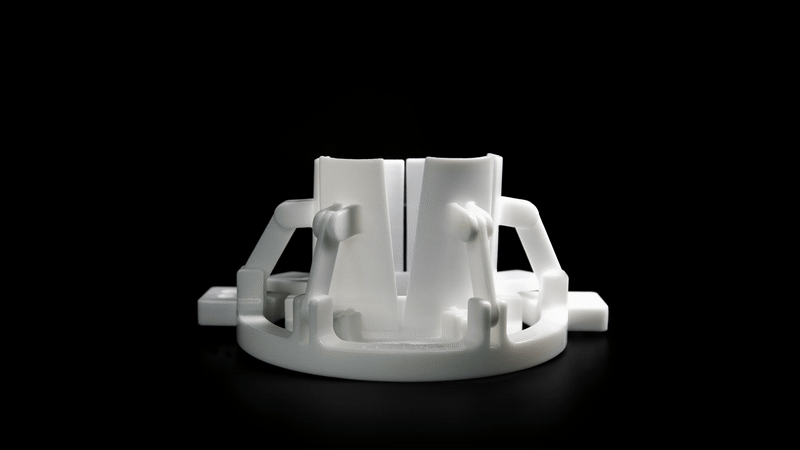
결과
apc-tec의 확장 플랩을 도입한 후 생산 공정은 훨씬 더 효율적이고 비용 효율적이며 식품 안전 규정을 준수하는 방식으로 변모했습니다. 적층 가공을 통해서만 달성할 수 있었던 컴팩트한 디자인 덕분에 외부 그립 메커니즘이 필요 없어져 더욱 간소화되고 공간 절약적인 접근 방식이 가능해졌습니다. 부품 수가 줄어든 덕분에 재료 비용뿐만 아니라 조립 및 프로그래밍과 관련된 시간과 복잡성도 최소화할 수 있었습니다. "산업용 3D 프린팅으로 생산을 간소화함으로써 비용을 절감했을 뿐만 아니라 기계 고장 위험을 줄여 장기적인 운영 안정성을 보장할 수 있었습니다."라고 보치오넥은 말합니다.
여러 기계 부품을 제거하고 시스템 통합을 간소화한 덕분에 초기 설치 비용이 15,000유로에서 단 2,000유로로 줄어들어 재정적 효과도 상당했습니다. 또한 산업용 3D 프린팅을 사용하여 전체 플랩을 단 한 단계로 제조할 수 있었기 때문에 신속한 설계 반복, 툴링 요구 사항 최소화, 기존 공급망과 관련된 지연 없이 온디맨드 제조가 가능하여 생산 및 구현 일정이 크게 단축되었습니다.
비용과 효율성을 개선하는 것 외에도 이 새로운 구성 요소는 EU 식품 접촉 규정 및 GMP 표준을 완벽하게 준수하여 공정에 사용되는 모든 재료와 전체 공급망이 최고의 위생 및 안전 요구 사항을 충족하도록 보장합니다. 이는 적층 가공이 식품 생산의 혁신을 어떻게 주도할 수 있는지를 보여주는 획기적인 사례입니다.
"우리 솔루션은 기존 제조 방식으로는 달성할 수 없었던 방식으로 이 생산 공정을 최적화했습니다. EOS의 3D 프린팅으로 구현된 지능형 기계 부품 설계와 완전한 식품 접촉 신고의 결합은 식품 안전 자동화의 판도를 바꿀 것입니다."
폴 보치오넥 | apc-tec GmbH의 총괄 매니저
EOS 사례 연구
EOS와 함께 30년 동안 3D 프린팅의 우수성을 개척해 온 과정을 살펴보세요.