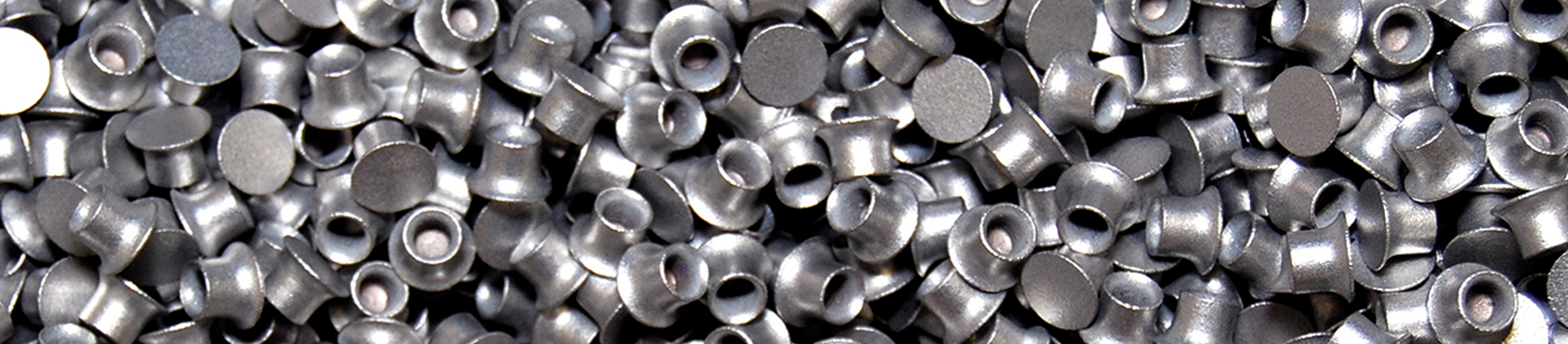
병목 현상에서 혁신으로: 아트라스콥코의 3D 프린팅 여정
아트라스콥코 | 사례 연구
생산 효율성 향상
- 리드 타임을 6~12주에서 단 3~4일로 92% 단축
- 외부 공급업체 비용 제거 및 노동 시간 단축으로 인한 생산 비용 30% 절감
- 자재 폐기물 약 7%에서 제로에 가까운 수준으로 감소
- 예기치 않은 주문 및 긴급한 고객 요구사항에 대한 민첩성 향상
긴 리드 타임, 공급망 중단, 생산 비용 상승은 현대 제조업에서 흔히 발생하는 문제입니다. 기존의 방식은 유연성, 속도, 효율성에 대한 수요 증가를 따라잡는 데 어려움을 겪는 경우가 많습니다. 아웃소싱 부품에 의존하는 기업의 경우, 지연과 비효율성으로 인해 많은 비용이 발생하고 기회를 잃을 수 있습니다.
산업용 솔루션 분야의 선두주자인 아트라스콥코는 자동차 산업에서 사용되는 자동 피어싱 리벳팅 시스템의 필수 부품인 리벳 전달 보울을 생산할 때 바로 이러한 문제에 직면했습니다. 이 회사는 사내 적층 제조(AM)를 도입하여 이러한 장애물을 극복했을 뿐만 아니라 상당한 비용 절감, 폐기물 감소, 리드 타임의 획기적인 단축을 실현했습니다. 3D 프린터 EOS P 396 및 PA 2200 폴리머 재료를 사용하여 아트라스콥코는 생산 방식을 혁신했습니다. 이 사례 연구에서는 적층 가공을 통해 측정 가능한 개선을 달성하고 제조 전략을 재편한 방법을 살펴봅니다.

"EOS와 협력하여 턴키 솔루션을 제공받고 프로세스를 조정하여 현재 여러 구성 요소를 연속 생산 중이며, 수백 개의 프로토타입을 빠르게 제작하고 있으며, 18개월 만에 ROI를 달성했습니다."
제이슨 에드워즈, 아틀라스콥코의 기술 관리자
도전 과제
전통적으로 아트라스콥코는 자동차 부문에서 광범위하게 사용되는 자동 피어싱 리벳팅 시스템의 핵심 부품인 리벳 전달 보울과 같은 부품을 외부 공급업체에 의존해 왔습니다. 이러한 의존성으로 인해 리드 타임이 6주에서 12주까지 연장되고 생산 비용이 증가했으며 공급망이 복잡해졌습니다. 또한 기존 제조 공정은 약 7%의 재료 낭비를 초래하여 보다 지속 가능한 솔루션의 필요성을 강조했습니다.
"우리는 리드 타임 단축, 비용 절감, 신제품의 신속한 프로토타입 제작 능력으로 이어질 수 있는 제조에 대한 보다 엄격한 제어를 원했습니다."라고 설명하며 "EOS 및 Additive Minds와의 협력을 통해 턴키 솔루션을 제공받고 프로세스를 조정하여 현재 여러 부품을 연속 생산하고 있고, 수백 개의 프로토타입을 빠르게 제작하며, 단 18개월 만에 ROI를 달성했습니다."라고 Atlas Copco의 기술 관리자 Jason Edwards가 설명했습니다.
정렬 및 피드
자동화된 제조 공정을 간소화하는 리벳을 효율적으로 제공하는 3D 프린팅 보울


솔루션
이러한 문제를 해결하기 위해 아트라스콥코는 EOS 및 컨설팅 사업부인 Additive Minds와 협력하여 사내에 적층 가공 기능을 도입했습니다. 유연성과 정밀도로 유명한 EOS P 396 3D 프린터를 선택하고 폴리머 소재인 PA 2200을 리벳 전달 보울 제조에 활용했습니다. 이러한 전환을 통해 아트라스콥코는 공급망을 간소화하고 타사 공급업체에 대한 의존도를 낮추며 생산 일정을 보다 엄격하게 관리할 수 있었습니다. 또한 사내 적층 가공 방식을 통해 신속한 프로토타입 제작이 가능해져 신속한 반복 작업과 설계 최적화가 가능해졌습니다.
결과
사내 적층 제조로의 전환은 아트라스콥코에 혁신적인 결과를 가져왔습니다. 가장 중요한 개선 사항 중 하나는 리드 타임이 획기적으로 단축되었다는 점입니다. 이전에는 외부 공급업체에 대한 의존도와 기존 제조 공정의 복잡성으로 인해 리벳 납품 보울을 생산하는 데 6~12주가 소요되었습니다. 3D 프린터 EOS P 396 도입한 후 리드 타임은 단 3~4일로 92%나 단축되었습니다. 이러한 개선 덕분에 생산 수요에 더 빠르게 대응하고 긴급한 고객 요구 사항을 더 유연하게 충족할 수 있었습니다.
비용 절감은 또 다른 주요 성과였습니다. 외부 공급업체의 필요성을 없애고 인건비를 줄이며 전체 생산 공정을 간소화함으로써 아트라스콥코는 생산 비용을 30% 절감할 수 있었습니다. 적층 가공의 효율성 덕분에 툴 재조정, 설정 변경 및 공급망 관리와 관련된 비용을 최소화할 수 있었습니다. 또한 적층 가공 공정의 정밀도와 신뢰성 덕분에 재료 낭비도 크게 줄었습니다. 기존 제조 방식에서는 약 7%의 자재 낭비가 발생했지만, 새로운 공정에서는 이 수치를 거의 0에 가깝게 낮췄습니다. 이러한 감소는 비용 효율성에 기여했을 뿐만 아니라 자원 소비를 최소화하여 지속 가능성 목표에도 도움이 되었습니다.
아트라스콥코는 적층 제조를 도입함으로써 생산 민첩성, 비용 효율성 및 환경적 이점을 개선하여 산업용 애플리케이션에서 적층 제조의 강력한 잠재력을 입증했습니다. "적층 가공은 우리에게 혁신적인 변화를 가져왔습니다. 저렴한 비용과 짧은 리드 타임으로 직접 공급할 수 있기 때문에 전 세계에서 새로운 계약을 체결하고 있습니다. EOS에는 전환 과정 내내 우리를 지원하고 신속한 지원을 제공하며 3D 프린터로 최상의 결과를 얻을 수 있도록 부품 설계에 대한 조언을 지속적으로 제공하는 파트너가 있습니다."라고 아틀라스콥코의 기술 관리자인 Jason Edwards는 결론을 내립니다.
효율성과 신뢰성
자체 3D 프린팅으로 전환한 덕분에 아트라스콥코는 타사 부품의 필요성이 줄어들고 공급망 리드 타임과 운송 지연의 제약을 더 이상 받지 않게 되었습니다.


"적층 제조는 우리에게 혁신적인 변화를 가져왔습니다. 저렴한 비용과 짧은 리드 타임으로 직접 공급할 수 있기 때문에 전 세계에서 새로운 계약을 체결하고 있습니다."
제이슨 에드워즈, 아틀라스콥코의 기술 관리자
EOS 사례 연구
EOS와 함께 30년 동안 3D 프린팅의 우수성을 개척해 온 과정을 살펴보세요.