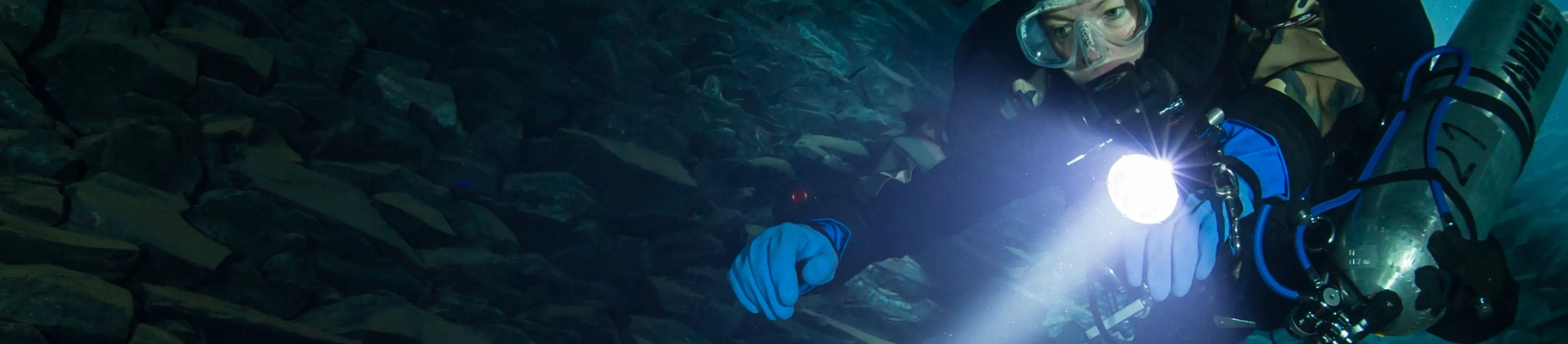
Drucken der perfekten Tauchlampe
Canto Ing. GmbH & THOR Offshore Engineering GmbH | Innovationsgeschichte
Beispiel für ein additiv gefertigtes Teil
Vorteile der 3D-gedruckten Tauchlampe
→ Funktionsintegration reduziert die Anzahl der Einzelkomponenten
→ Wasserfester Kunststoff PA 2200 widersteht extremen Belastungen
→ Wirtschaftliche Produktion auch bei kleinen Losgrößen
"Der additiv gefertigte Bajonettverschluss ist ein technisches Highlight der Thor Rev 2.0. Wir haben die Bauteilabmessungen, das Gewicht und die Stabilität sowie die Funktionsintegration optimiert - alles in einem einzigen Bauteil. Die daraus resultierende Zuverlässigkeit und Präzision hat dazu geführt, dass der Thor Rev 2.0 von Spezialeinheiten der Polizei und des Militärs in Europa eingesetzt wird. Dank der EOS-Technologie konnten Spritzgusswerkzeugkosten in Höhe von 35.000 Euro und Montagekosten von rund 6,80 Euro pro Leuchte eingespart werden."
Hagen Tschorn | Geschäftsführer | Canto Ing. GmbH und THOR offshore engineering GmbH
Additive Fertigungstechnologie
für das perfekte Tauchlicht
Die Thor Unterwasserleuchte wurde für technische und professionelle Taucher, einschließlich derjenigen, die im Dienstleistungsbereich tätig sind, für den Einsatz in Tiefen von bis zu 200 Metern entwickelt. Der Verriegelungsmechanismus der Thor Rev 2.0 wird mittels additiver Fertigung hergestellt. Diese Technologie ermöglicht es, das interne System, das mit Hilfe von Federn eingerastet wird, als ein einziges, robustes und funktionell integriertes Bauteil zu fertigen.
Um die strengen Materialanforderungen des Projekts zu erfüllen, entschied sich Canto für den EOS-Kunststoff PA 2200, ein Material, das sowohl undurchlässig als auch extrem langlebig ist. Es war das erste Mal, dass dieses Material in einem derartigen Kontext verwendet wurde. Die präzise Bauweise, die hohe Fertigungsqualität des Lasersintersystems FORMIGA P110 und die grundsätzlich robuste Bauweise machten den leichten Werkstoff zur idealen Lösung für das Projekt.
Die Thor Rev 2.0 setzt neue Maßstäbe für technische Taucher: Mit einem Gewicht von nur 580 Gramm ist die Lichtquelle äußerst komfortabel zu handhaben. Durch die Funktionsintegration konnte die Anzahl der zu montierenden Einzelteile von drei auf nur noch eines reduziert werden. Außerdem sparte sich Canto die Herstellung eines aufwendigen Spritzgusswerkzeugs, was zusätzliche Kosten von bis zu 34.800 Euro bedeutet hätte. Trotz des großen Spielraums, den die Tauchleuchte mit ihrer Leichtbauweise bietet, erfüllen Qualität und Haltbarkeit des Produkts alle gewünschten Anforderungen.
Canto hat die additive Fertigungstechnologie nicht nur für die Produktion dieser Serie, sondern auch für die Produktentwicklung eingesetzt.
"EOS hat uns gezeigt, dass sie die Anbieter von kreativen Lösungen bei der Suche nach neuen Anwendungsfeldern unterstützen. Das Unternehmen hat uns in die Lage versetzt, unseren Endkunden eine Komplettlösung anzubieten: Engineering und Fertigung."
Hagen Tschorn | Geschäftsführer | Canto Ing. GmbH und THOR offshore engineering GmbH
Systeme und Lösungen
Additive Fertigung mit Kunststoffen
EOS-Innovationsgeschichten
Erleben Sie drei Jahrzehnte Pionierarbeit im 3D-Druck mit EOS