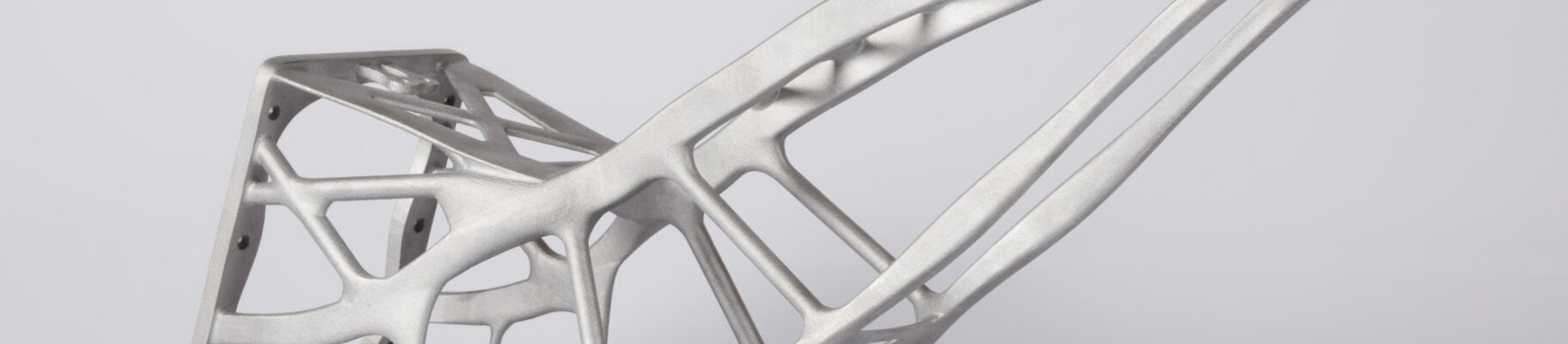
RUAG 3D 프린팅 위성 부품
RUAG의 센티널 위성용 안테나 브래킷 - 우주 공간 배치 인증 획득 | 혁신 스토리
많은 사람들이 우주의 무한한 광활함에 대해 이야기하면 보통 할리우드 영화 스튜디오에서 들려주는 공상 과학 이야기를 떠올립니다. 하지만 현실에서는 다른 어떤 분야보다도 우주 여행에 필요한 기술을 개발하고 우주에 배치할 준비를 하는 데 있어 강력한 의지와 명확한 비전이 필수적입니다. 스위스 기술 그룹 RUAG가 지구를 높은 곳에서 관측하기 위해 설계한 센티널 위성을 제작할 때 직면한 도전이 바로 이런 것이었습니다. 지구 대기권을 넘어 우주에서도 적층 제조가 핵심적인 역할을 하고 있습니다.
부품을 훨씬 더 가벼우면서도 동시에 더 견고하게 만들 수 있었습니다. 부품의 특성은 항공우주 분야에서 요구되는 엄격한 테스트를 통해 그 가치가 입증되었습니다. 앞으로 적층 제조에 대해 더 많은 이야기를 듣게 될 것이라고 확신합니다!
프랑크 모리오 | 구조 총괄 매니저 | RUAG
도전 과제
센티널 위성을 위한 매우 가볍고 견고한 안테나 브래킷 생산
2016년 독일 항공우주센터(DLR)의 보고서에 따르면, 운반된 페이로드 1kg당 우주 탐사 임무 비용은 20,000유로 이상입니다. 1그램을 절약할 때마다 상승에 필요한 연료가 줄어들기 때문에 총 발사 비용이 줄어듭니다. 결과적으로 항공우주 엔지니어는 초과 중량이 빠르게 누적되기 때문에 모든 구성 요소에서 가능한 모든 그램을 줄여야 합니다. 이 경우 스위스 RUAG 그룹은 최적으로 설계된 안테나 브래킷이 필요했습니다.
하지만 무게 최적화만으로는 충분하지 않습니다. 로켓이 발사되면 페이로드가 크게 흔들리고 진동이 상당히 심해집니다.
또한 시속 수천 킬로미터에 달하는 엄청난 속도와 높은 중력가속도는 여객기에서 기대하는 것만큼 비행이 부드럽지 않다는 것을 의미합니다. 안정성과 강성은 모든 사양 시트에서 두 번째로 중요한 요소입니다. 안타깝게도 이러한 요구 사항은 일반적으로 경량 설계의 필요성과 정반대되는 경우가 많습니다.
엔지니어는 복잡한 구조를 사용하여 형태와 무게 사이에서 실행 가능한 수준의 절충점을 찾습니다.
RUAG 팀은 기존의 제조 방식이 한계에 다다랐기 때문에 안테나 브래킷의 구조에 맞는 최적의 강도와 무게 조합을 찾았습니다.
다행히도 적층 가공은 필요한 설계의 자유를 실현할 수 있는 완벽한 가능성을 제공했습니다. 부품 테스트는 앞서 언급한 진동으로 인해 특히 어려운 과제였습니다. 우주 공간에서는 일반적으로 수리가 불가능하기 때문에 신뢰성이 중요합니다. 이는 또한 이러한 구성 요소의 인증이 장기간에 걸친 복잡한 과정인 이유를 설명합니다. 모든 인증은 이를 획득한 엔지니어에게 영예를 안겨줍니다.
복잡한 구조로 인해 무게와 안정성에 대한 모든 요구 사항을 충족하는 적층 가공을 사용하여 부품을 생산합니다.
이러한 경우, 특히 항공우주 분야에서는 전체 생산 체인이 중요한 역할을 합니다. "당연히 적층 가공으로 부품을 생산할 때 얻을 수 있는 엄청난 이점은 우리에게 큰 관심사였습니다."라고 RUAG의 구조물 총괄 매니저인 프랑크 모리외(Franck Mouriaux)는 설명합니다. "예를 들어, 설계의 자유와 복잡한 구성 요소는 무게를 줄이는 데 도움이 됩니다. 기능을 통합할 수 있는 능력도 큰 도움이 됩니다. 그러나 결국 중요한 것은 이러한 잠재적 이점을 파악하고 이상적인 방식으로 구현하며 필요한 해당 인증을 획득하는 것입니다. 아무리 단순한 구성 요소라도 사용할 수 없다면 아무 소용이 없습니다."
기본적인 적합성 및 강성 테스트는 안테나 브래킷 설계의 출발점이 되었습니다. 다음 단계는 소재 선택, 공정 정의 및 소재 특성에 대한 초기 기본 테스트로 구성되었습니다. 그런 다음 초기 테스트 구조를 구축하여 구성 요소의 위상 최적화를 위한 출발점으로 삼았습니다. RUAG는 결국 Altair의 CAD 및 FEM 시스템을 사용한 집중적인 작업과 적층 제조를 사용한 설계 및 시공에 대한 EOS의 지침을 결합하여 이론적으로 완벽한 형태의 안테나 브래킷을 완성할 수 있었습니다.

약 40cm 길이의 안테나 브래킷은 독일 바렐벤의 citim GmbH( EOS M 400)에서 제작했습니다. 제작 부피는 400 x 400 x 400mm로, 한 번의 제작 주문으로 안테나 2개, 인장 테스트 조각 30개 및 다양한 테스트 항목을 생산할 수 있었습니다. 구축 시간은 약 80시간이 소요되었습니다. 사용된 파라미터 세트는 표면 품질과 생산성을 위해 최적화된 60µm의 층 두께를 위해 사용되었습니다.
사용된 알루미늄 합금인 EOS Aluminium AlSi10Mg는 강도가 높고 동적 응력에 대한 저항력이 강해 고응력 부품에 사용하기에 매우 적합한 소재입니다. 항공우주 분야에서는 전체 프로젝트 범위의 최대 80%를 차지하는 이러한 특성을 입증하기 위해 포괄적인 테스트가 수행되었습니다. 테스트에는 특수 제작된 구조물이 사용되었습니다. 무엇보다도 엔지니어들은 컴퓨터 단층 촬영으로 브래킷을 검사했습니다. 다양한 기계적 및 물리적 절차도 수행되었습니다. 때로는 부품에 가해지는 응력이 의도적으로 하중 한계를 초과하여 결국 테스트 부품이 파손되는 경우도 있었습니다.
EOS는 혁신과 적층 제조에 대한 훌륭한 경험을 결합합니다. 이 시스템은 모든 분야의 모든 시장에 정말 흥미로운 가능성을 제공합니다.
안드레아스 베르카우(Dipl.-Ing.) | CEO | citim GmbH
결과
이러한 노력의 결과로 센티널 위성을 위한 새로운 안테나 브래킷은 모든 기대치를 뛰어넘었습니다. 이 부품은 인증을 받았으며, 우주 공간에서의 활용에 대한 승인을 받았습니다. 우주에서의 적층 가공이 아직 초기 단계라는 점을 고려하면 이 성과는 더욱 놀랍습니다.
예를 들어, 부품의 최소 강성 요건은 난기류 비행 후에도 이상적인 안테나 위치에 도달하고 지구와의 무선 통신을 보장하기에 충분한 여유인 30% 이상을 초과했습니다. 부분적으로는 매우 균일한 응력 분포 덕분에 필요한 수준의 안정성을 달성할 수 있었습니다.
또한 적층 제조를 통해 최종 부품의 무게를 1.6kg에서 940g으로 크게 줄여 40% 이상 절감할 수 있었습니다.
이 사례에서는 혁신적인 기술을 사용하여 부품 특성 개선과 시스템 비용 절감이라는 예상치 못한 조합을 달성하는 데 성공했습니다. "이 프로젝트의 결과에 매우 만족합니다. 우리는 공정 측면에서 미지의 영역에 진입했고 안정적이고 가벼운 부품으로 보상을 받았습니다."라고 항공우주 엔지니어 Mouriaux는 말합니다.
"적층 제조는 우주 여행의 기본적인 절차적 요구 사항을 충족할 수 있다는 것을 보여주었습니다. 다양한 설계 이점과 부품 자체의 특성이 이를 확실히 입증했습니다. 앞으로 이 기술의 잠재력이 매우 크다고 생각합니다."
한 눈에 보는 결과
- 30% 강성 - 최소 요구 사항 30% 초과 달성
- 40% 무게 감소
추가 혜택
- 지능형: 자유로운 설계로 균일한 힘 분배 가능
- 인증: 포괄적인 테스트를 통해 검증된 항공우주 분야의 요구 사항
자세히 알아보기
EOS와 함께 30년 동안 3D 프린팅의 우수성을 개척해 온 과정을 살펴보세요.