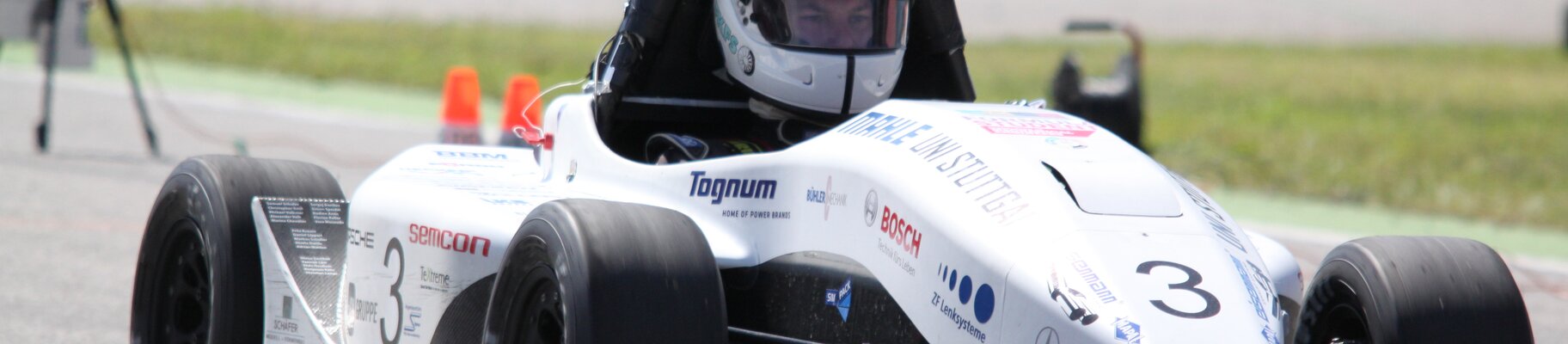
부품의 잠재력을 최대한 활용하기 위해 적층 가공을 선택한 젊은 엔지니어들
렌팀 유니 슈투트가르트 | 성공 사례
-
개발 및 생산 시간의 현저한 부족
-
20% 향상된 강성으로 트랙에서 안정적으로 주행 가능
-
완벽한 형태와 컨투어링으로 35% 감소된 무게
"포뮬러 스튜던트 독일 2012 타이틀을 슈투트가르트에 가져올 수 있게 되어 매우 기쁩니다. EOS의 DMLS 기술이 제공하는 건설 과정의 자유로움은 우리의 성공에 중요한 역할을 했습니다."
야닉 뢰우 | 렌트팀 유니 슈투트가르트
우승으로 가는 길 - 렌팀 유니 슈투트가르트, EOS 지원으로 포뮬러 스튜던트 독일 우승
한편으로 액슬 피벗의 모든 제작자는 가능한 한 최고의 안정성을 갖춘 부품을 개발해야 하며, 그렇지 않으면 차량 전체의 안전이 손상될 수 있습니다. 반면에 휠 마운트는 여러 가지 이유로 무게가 너무 무거워서는 안 됩니다.
개념 설계 단계부터 엔지니어들은 EOS 파트너인 Within Technologies Ltd의 CAD 소프트웨어를 활용했습니다. 이 툴 덕분에 제작자들은 부품을 구조적 요구 사항에 완벽하게 일치시킬 수 있었습니다. 이러한 방식으로 너클에 필요한 물리적 특성인 가벼움과 강성을 정확하게 부여할 수 있었습니다.
적층 제조를 사용하면 네거티브나 금형 형태를 제작할 필요가 없습니다. 또한 설계부터 제작에 이르는 전체 공정이 더욱 정밀해져 재작업이나 정제가 필요하지 않은 경우가 많습니다. 부품은 거의 즉시 레이스에 투입할 수 있었습니다.
부품의 무게가 660그램 감소하여 렌팀 유니 슈투트가르트는 35%의 비용을 절감했습니다. 동시에 엔지니어들은 강성을 20% 높이는 데 성공했는데, 이는 모터스포츠에서 큰 수치이며 랩타임 단축과 연료 소비 감소로 이어지는 수치입니다.

"우리는 전통적인 정밀 주조 공정을 사용하여 부품을 제작했습니다. 물론 이 방식은 형태의 자유도에 제한이 있어 부품의 잠재력을 완전히 실현할 수 없었습니다. 당시에도 2012 시즌에는 스티어링 스터브 액슬을 제조하는 새롭고 혁신적인 방법을 연구하기로 결정했었습니다."
야닉 뢰우 | 렌트팀 유니 슈투트가르트
한 눈에 보는 결과
- 20% 더 높은 강성
- -660g 무게 감소
EOS 성공 사례
EOS와 함께 30년 동안 3D 프린팅의 우수성을 개척해 온 과정을 살펴보세요.