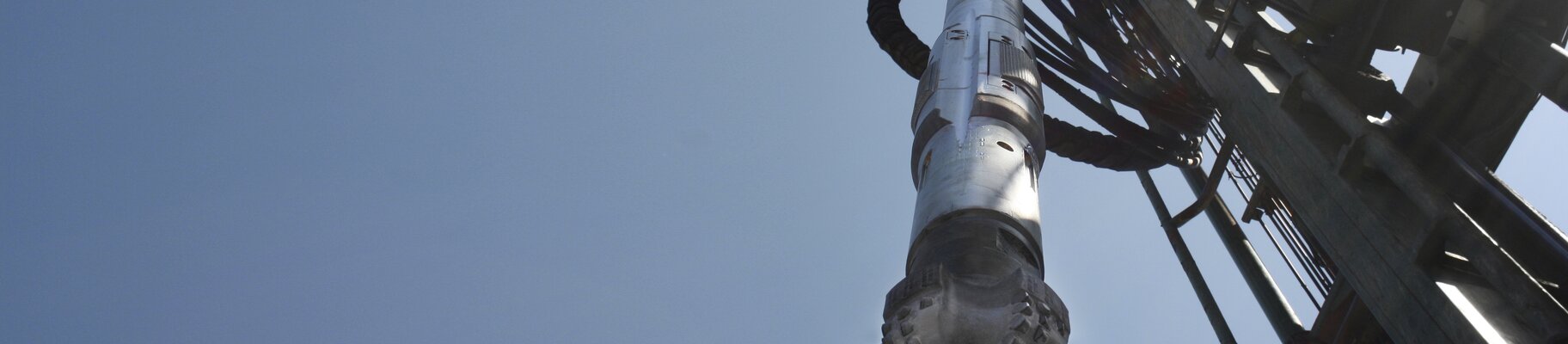
유전 시추 장비 제조업체
APS 기술 | 사례 연구
3D 프린팅 유전 시추 장비의 장점
- 리드 타임 및 출시 기간 단축
- 최적화된 설계로 드릴링 정확도 향상, 후처리 및 생산 비용 절감
- 부품 수가 4개에서 1개로 줄어든 드릴링 어셈블리
- 구성 요소 75% 감소
"기존 제조 방식도 여기까지 왔지만, DMLS로 만든 부품의 향상된 효율성은 판도를 바꾸고 있습니다. 제품 수명이 길어지면 장비 유지보수로 인한 중단이 줄어들고 드릴링 시간이 길어지며 비용이 절감되는 도미노 효과가 발생합니다. 궁극적으로 이는 고객 만족도와 추가 판매 주문으로 이어집니다."
폴 시튼 | 마케팅 부사장 | APS Technology Inc.
"기존 방식으로는 18시간이 걸렸던 DMLS 부품을 봉재에서 생산할 수 있다고 가정해 봅시다. 이 부품은 인쇄하는 데 22~26시간이 걸리지만 유기 구멍과 같이 기존 방식으로는 제조할 수 없는 특징이 있을 수 있습니다. 이제 그 부품을 마감하는 데는 씰링 표면을 기계로 가공하고 공차 기능을 강화하는 데 3~4시간이면 충분합니다."
크리스 펀케 | 수석 기술 엔지니어 | APS 테크놀로지

EOS의 적층 제조 - 새로운 드릴링 경험 제공
APS는 MWD 시스템 외에도 조종 가능한 드릴 모터, 진동 댐퍼, 모델링 및 분석 도구, 로깅 센서를 포함한 다양한 지능형 도구를 제공합니다. 땅속 수백 피트 아래 암석을 절단할 때 발생하는 명백한 어려움 외에도 드릴 헤드를 냉각하고 절단면을 씻어내는 데 사용되는 가압 유체는 마모성이 강하고 매우 빠르게 지나갑니다.
EOS는 내구성이 뛰어난 금속을 기반으로 한 적층 제조라는 완벽한 솔루션을 준비했습니다. 이 기술을 사용하여 이 회사는 단시간에 오래 지속되는 부품을 제작할 수 있었습니다. 이 솔루션은 다음과 같은 이름으로 알려져 있습니다: EOSINT M 280. 설계자는 DMLS를 통해 이전에는 제조할 수 없었던 복잡한 형상을 만들 수 있으며, 이제 이와 같은 문제를 훨씬 더 쉽게 관리할 수 있게 되었습니다.
APS는 EOS 기술을 사용하여 드릴링 어셈블리의 부품 수를 4개의 개별 부품에서 단 하나로 줄였습니다. 부품 수 감소와 새로운 부품 형상이라는 이점 외에도 설계자들은 제품 개발 주기가 훨씬 더 짧아졌다는 사실을 발견하고 있습니다. 또한 DMLS는 회사의 광범위한 기계 공장에서 비용을 절감하고 있으며, 가공하는 데 며칠 또는 몇 주가 걸리던 지그와 픽스처를 이제 무인 상태에서 하룻밤 사이에 인쇄할 수 있게 되었습니다.
EOS 사례 연구
EOS와 함께 30년 동안 3D 프린팅의 우수성을 개척해 온 과정을 살펴보세요.