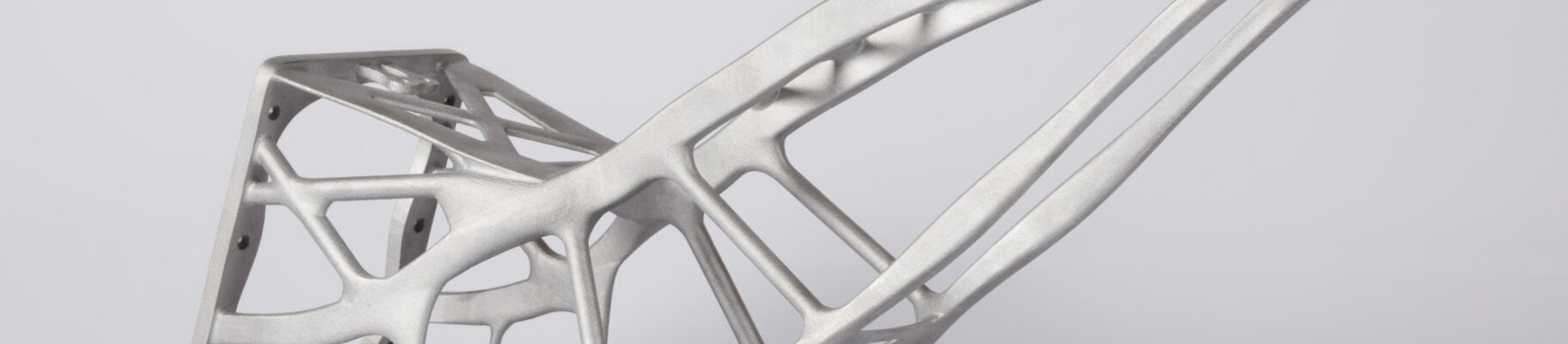
Pièces de satellites imprimées en 3D par RUAG
Support d'antenne pour le satellite Sentinel de RUAG - certifié pour un déploiement dans l'espace extra-atmosphérique | Innovation Story
Pour beaucoup de gens, parler de l'immensité infinie de l'univers évoque des histoires de science-fiction, généralement racontées par un studio de cinéma hollywoodien. Cependant, dans la réalité, plus que dans tout autre domaine, c'est sans doute dans la navigation spatiale qu'une volonté forte et une vision claire sont essentielles pour créer la technologie nécessaire et la préparer à être déployée dans le cosmos. C'est le défi qu'a dû relever le groupe technologique suisse RUAG lors de la construction de son satellite Sentinel, destiné à observer notre planète depuis le ciel. Même ici, au-delà de l'atmosphère terrestre, la fabrication additive joue un rôle clé.
C'est en quelque sorte la quadrature du cercle : nous avons réussi à alléger considérablement un composant tout en le rendant plus robuste. Les caractéristiques du composant ont fait leurs preuves lors de tests réalisés avec la rigueur requise pour le secteur aérospatial. Dans les années à venir, nous entendrons encore beaucoup parler de la fabrication additive - j'en suis convaincu !
Franck Mouriaux | Directeur Général Structures | RUAG
Défi
Production d'un support d'antenne extrêmement léger et robuste pour les satellites Sentinel
Selon des rapports du Centre allemand pour l'aérospatiale (DLR) datant de 2016, les coûts de mission de l'exploration spatiale par kilogramme de charge utile transportée s'élèvent à plus de 20 000 euros. Chaque gramme économisé réduit le coût total du lancement, car le système nécessite moins de carburant pour l'ascension. Par conséquent, les ingénieurs aérospatiaux doivent réduire chaque gramme possible de chaque composant, car le poids excédentaire s'accumule rapidement. Dans ce cas, le groupe suisse RUAG avait besoin d'un support d'antenne conçu de manière optimale.
Mais l'optimisation du poids ne suffit pas. Lors du lancement d'une fusée, la charge utile est véritablement secouée et le niveau de vibration est considérable.
En outre, les vitesses énormes de plusieurs milliers de kilomètres à l'heure, sans parler des forces G élevées, signifient que le vol ne sera pas aussi doux que ce que l'on peut attendre d'un avion de ligne. La stabilité et la rigidité constituent un deuxième élément essentiel de tout cahier des charges. Malheureusement, cette exigence est généralement diamétralement opposée à la nécessité d'une conception légère.
Les ingénieurs utilisent des structures complexes pour trouver un compromis viable entre la forme et le poids.
L'équipe RUAG a cherché une combinaison optimale de résistance et de poids pour la structure de son support d'antenne, les méthodes de fabrication conventionnelles ayant été épuisées.
Heureusement, la fabrication additive offrait la possibilité parfaite d'obtenir la liberté de conception nécessaire. L'essai des composants a représenté un défi particulier, notamment en raison des vibrations susmentionnées. Dans l'espace, la fiabilité est primordiale, car les réparations ne sont généralement pas possibles. Cela explique également pourquoi l'autorisation de ces composants est un processus aussi long et complexe. Chaque certification représente une consécration pour les ingénieurs qui l'ont obtenue.
Production d'un composant par fabrication additive qui, grâce à ses structures complexes, répond à toutes les exigences en matière de poids et de stabilité.
Dans de tels cas, la chaîne de production complète joue un rôle important, en particulier dans le secteur aérospatial. "Il est évident que les immenses avantages de la production de composants par fabrication additive nous intéressaient beaucoup", explique Franck Mouriaux, directeur général des structures chez RUAG. "Par exemple, la liberté de conception et les composants complexes nous permettent de gagner du poids. La possibilité d'intégrer des fonctions est également très utile. En fin de compte, il s'agit d'identifier ces avantages potentiels, de les mettre en œuvre de manière optimale et d'obtenir les autorisations nécessaires. Le composant le plus simple ne sert à rien s'il ne peut pas être utilisé".
Les essais fondamentaux d'adéquation et de rigidité ont constitué le point de départ de la conception du support d'antenne. L'étape suivante a consisté à sélectionner les matériaux, à définir les processus et à réaliser les premiers essais de base concernant les caractéristiques des matériaux. Les structures d'essai initiales ont ensuite été construites pour servir de point de départ à l'optimisation topologique du composant. RUAG a finalement réussi à obtenir la forme - théoriquement - parfaite pour le support d'antenne, grâce à la combinaison d'un travail intensif avec un système de CAO et de FEM d'Altair et des conseils d'EOS sur la conception et la construction en utilisant la fabrication additive.

Le support d'antenne d'environ 40 cm de long a été fabriqué par la société citim GmbH de Barleben (Allemagne) à l'aide du site EOS M 400. Avec un volume de construction de 400 x 400 x 400 mm, il a été possible de produire deux antennes, 30 pièces d'essai de traction et divers articles d'essai en un seul ordre de construction. La durée de construction a été d'environ 80 heures. Le jeu de paramètres utilisé était une épaisseur de couche de 60 µm, optimisée pour la qualité de la surface et la productivité.
L'alliage d'aluminium utilisé, EOS Aluminium AlSi10Mg, se caractérise par une grande solidité et une forte résistance aux contraintes dynamiques, ce qui en fait un matériau parfaitement adapté aux composants soumis à de fortes contraintes. Des essais complets ont été réalisés pour démontrer les caractéristiques requises - dans le secteur aérospatial, ces essais représentent jusqu'à 80 % de la portée totale d'un projet. Des structures spécialement fabriquées ont été utilisées pour les essais. Les ingénieurs ont notamment examiné les supports à l'aide de tomographes informatiques. Diverses procédures mécaniques et physiques ont également été effectuées. À certains moments, les contraintes exercées sur le composant ont délibérément dépassé les limites de charge, ce qui a finalement entraîné la destruction des pièces d'essai.
EOS associe l'innovation à une grande expérience de la fabrication additive. Les systèmes offrent des possibilités vraiment intéressantes pour tous les marchés, dans tous les secteurs.
Andreas Berkau, ingénieur diplômé, PDG de citim GmbH
Résultat
Le résultat de ces efforts est que le nouveau support d'antenne pour les satellites Sentinel a dépassé toutes les attentes. Le composant a été certifié et, par conséquent, son utilisation dans l'espace a été approuvée. Cette réussite est d'autant plus remarquable que l'utilisation de la fabrication additive dans l'espace n'en est qu'à ses débuts.
Par exemple, les exigences minimales de rigidité du composant ont été dépassées de plus de 30 % - une marge largement suffisante pour garantir, même après un vol turbulent, une position idéale de l'antenne - et la communication radio avec la Terre a été assurée. Le niveau de stabilité requis a été atteint, en partie grâce à la répartition très uniforme des contraintes.
En outre, le recours à la fabrication additive a permis de réduire considérablement le poids du composant final, qui est passé de 1,6 kg à 940 g, soit une économie de plus de 40 %.
Dans ce cas, l'utilisation d'une technologie innovante a permis de réaliser une combinaison improbable : amélioration des caractéristiques des composants et réduction des coûts du système. "Nous sommes très satisfaits des résultats de ce projet. Nous sommes entrés dans un territoire inconnu du point de vue du processus et avons été récompensés par un composant stable et léger", déclare l'ingénieur aérospatial Mouriaux.
"La fabrication additive a montré qu'elle pouvait répondre aux exigences procédurales fondamentales des voyages spatiaux. Les multiples avantages de la conception et les caractéristiques du composant lui-même l'ont certainement prouvé. Je vois un grand potentiel pour cette technologie à l'avenir".
Les résultats en un coup d'œil
- 30% Rigidité - Exigences minimales dépassées de 30%
- 40% Réduction du poids
Autres avantages
- Intelligent : la liberté de conception permet une répartition uniforme des forces
- Accrédité : exigences du secteur aérospatial vérifiées par des tests complets
En savoir plus
Découvrez trois décennies d'excellence en matière d'impression 3D avec EOS