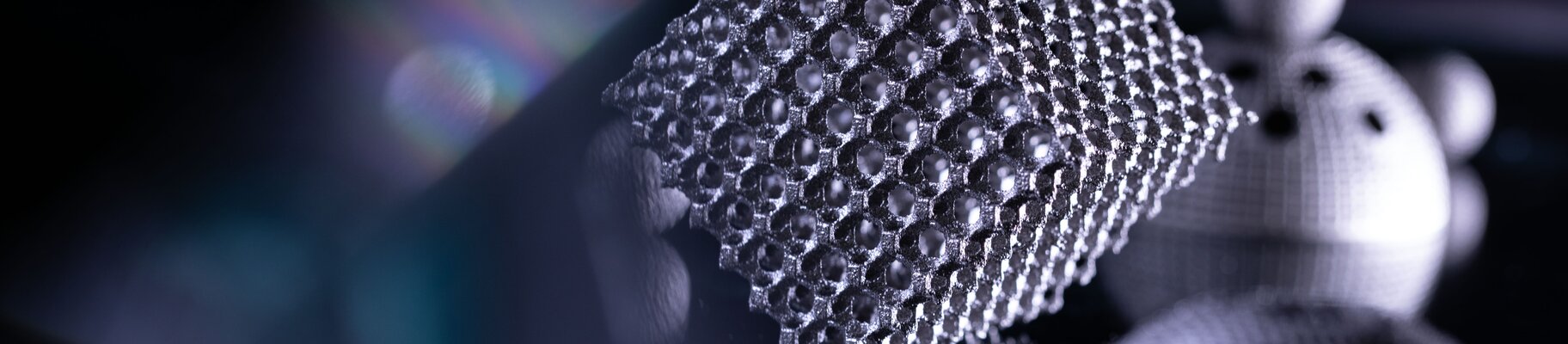
S'inspirer - Métal
Solutions pour la fabrication additive de métaux
Des pièces de qualité industrielle - à chaque fois
Nos solutions d'impression 3D de métaux industriels permettent d'obtenir des pièces de qualité industrielle hautement reproductibles, quelle que soit la complexité de votre conception ou l'audace de vos plans à l'échelle. EOS offre une flexibilité inégalée, ce qui vous permet d'adapter facilement votre conception de fabrication et d'application à vos besoins de production et de personnalisation.
Nos clients dans le domaine de l'impression 3D sur métal comprennent une vaste collection d'organisations, y compris des leaders du marché, des perturbateurs de l'industrie et des laboratoires de recherche nationaux. De l'aérospatiale à l'automobile, en passant par les fabricants d'implants médicaux, les énergies renouvelables et les biens de consommation, nous avons fourni des solutions d'impression 3D industrielles en métal qui répondent aux besoins de chacun. Découvrez quelques-unes des réussites de nos clients et laissez-vous inspirer pour votre prochain projet d'application imprimée en 3D.
Moteur-fusée avec LAUNCHER
L'utilisation de l'impression 3D pour la fabrication de moteurs de fusée permet de repenser et de réinventer complètement la fonctionnalité des composants. Par exemple, il est possible d'intégrer des canaux de refroidissement dans une chambre de combustion ou de regrouper plusieurs pièces en un seul modèle. Avec le soutien d'EOS et d'AMCM, la société aérospatiale américaine VAST lance des charges utiles de petite et moyenne taille dans l'espace plus efficacement que jamais. Il en résulte des fusées de conception nouvelle et innovante, ainsi que le plus grand moteur de fusée au monde jamais fabriqué de manière additive en une seule pièce. Le moteur est basé sur une conception de fusée standard, mais il est complété par des nervures internes pour un refroidissement optimal. VAST a réussi à construire, tester et développer cette nouvelle conception rapidement et à moindre coût, entièrement grâce à l'impression 3D. Au début du projet, l'espace de construction et les propriétés des matériaux ont rapidement été identifiés comme des obstacles. AMCM, une société du groupe EOS qui propose des machines spécialisées adaptées aux besoins des clients, a relevé le défi.
La chambre de combustion, imprimée en 3D à partir d'un alliage de cuivre sur les machines M4K de l'AMCM, est la plus grande chambre de combustion d'un seul tenant au monde pour les moteurs à fusée liquide. Elle mesure 86 cm de haut et le diamètre de la tuyère de sortie est de 41 cm. Le booster a remporté un prix de 1,5 million de dollars lors du Space Pitch Day de l'US Air Force, qui a été organisé pour accélérer le programme de développement et d'essai du booster E-2. Les premiers essais à grande échelle ont déjà été planifiés.
"Traditionnellement, la fabrication de ce type de pièce nécessite des millions de dollars d'investissement dans des machines personnalisées. Aujourd'hui, l'impression 3D permet d'imprimer la chambre de combustion, la buse et le col en une seule pièce. Grâce à ce progrès, notre travail est plus facile que jamais". - Max Haot, directeur général de VAST

Le futur module de propulsion d'Ariane simplifié
La notion de "mission critique" décrit parfaitement les composants de classe 1 utilisés dans l'industrie aérospatiale. Des missions de plusieurs centaines de millions d'euros dépendent de ces composants. Par conséquent, les ingénieurs cherchent constamment à développer des composants de la plus haute qualité, fonctionnalité et robustesse, tout en simplifiant la chaîne de fabrication et en réduisant le nombre d'éléments individuels. Grâce à la technologie de fabrication additive EOS, ArianeGroup a réussi à franchir une nouvelle étape : Au lieu de 248 éléments, la tête d'injecteur d'un moteur-fusée d'un futur module de propulsion d'étage supérieur ne compte plus qu'un seul composant. La tête d'injecteur a été simplifiée et réduite à ce qui est littéralement une conception tout-en-un (AiO).
"Dans le cadre du programme Ariane, nous combinons notre force d'innovation avec l'expertise d'EOS. Ensemble, nous travaillons sur la fabrication additive d'une tête d'injecteur pour un moteur de fusée. Les résultats sont impressionnants : Réduction significative du temps de production et diminution des coûts de 50 %." - Steffen Beyer, responsable de la technologie de production, des matériaux et des processus d'ArianeGroup.

Impression 3D d'un support d'antenne satellite avec RUAG
Pour beaucoup de gens, parler de l'immensité infinie de l'univers évoque des histoires de science-fiction, généralement racontées par un studio de cinéma hollywoodien. Cependant, dans la réalité, plus que dans tout autre domaine, c'est sans doute dans la navigation spatiale qu'une volonté forte et une vision claire sont essentielles pour créer la technologie nécessaire et la préparer à être déployée dans le cosmos. C'est le défi qu'a dû relever le groupe technologique suisse RUAG lors de la construction de son satellite Sentinel, destiné à observer notre planète depuis le ciel. Même ici, au-delà de l'atmosphère terrestre, FA joue un rôle clé. Le groupe suisse RUAG avait besoin d'un support d'antenne de conception optimale, l'optimisation du poids étant un élément crucial, mais pas le seul aspect qui devait résister à la comparaison entre FA et la fabrication traditionnelle. En raison des vibrations et des forces G auxquelles une pièce est soumise lors du lancement d'une fusée et de sa mise en orbite, la stabilité et la rigidité constituaient un deuxième élément essentiel de la nouvelle conception.
"EOS associe l'innovation à une grande expérience de la fabrication additive. Les systèmes offrent des possibilités vraiment intéressantes pour tous les marchés, quel que soit le secteur." - Andreas Berkau, PDG, CITIM GmbH

En savoir plus
Histoires de succès et de blogs sur le métal rendus possibles par EOS
Sélection des matériaux
Webinaires sur le métal et livres blancs réalisés par EOS