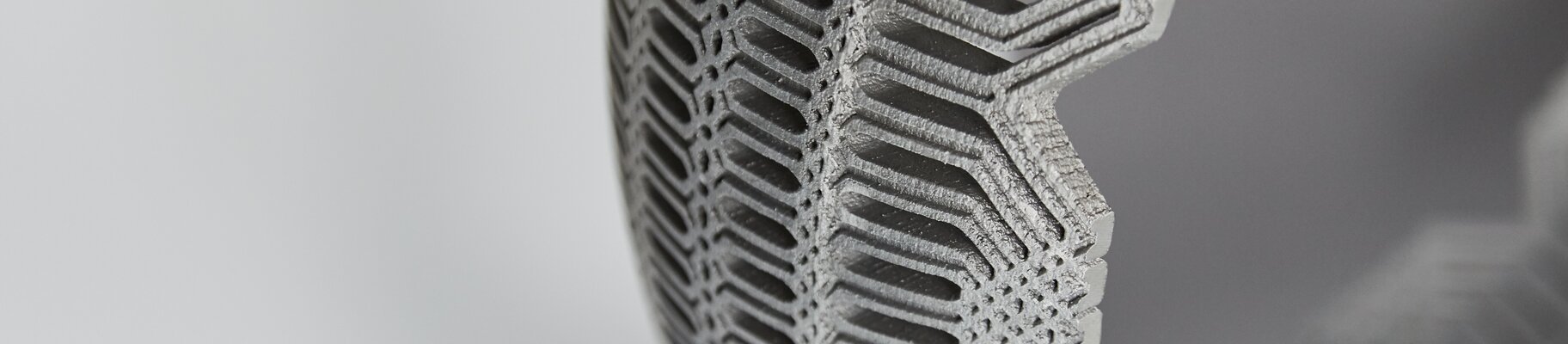
L'impression 3D dans le secteur manufacturier
Applications et exemples pratiques
Meilleures pratiques pour l'impression 3D dans les environnements de fabrication et de production
Pression sur les coûts, exigences réglementaires, demandes croissantes des clients, et bien d'autres choses encore. Les entreprises du secteur de la production et de l'industrie sont confrontées à un ensemble de défis en constante évolution. Dans le même temps, des questions telles que l'efficacité de l'énergie et des ressources deviennent de plus en plus importantes.
La fabrication additive offre un large éventail d'avantages potentiels, rentables et durables aux entreprises du secteur de la production et de l'industrie.
L'impression 3D industrielle ouvre de nouvelles perspectives et apporte des solutions dans de nombreux domaines, de la production de pièces à l'optimisation du retour sur investissement. Chez EOS, nous proposons des solutions personnalisées à partir d'une source unique pour la technologie et tout ce dont vous avez besoin pour une transition sûre et rapide.