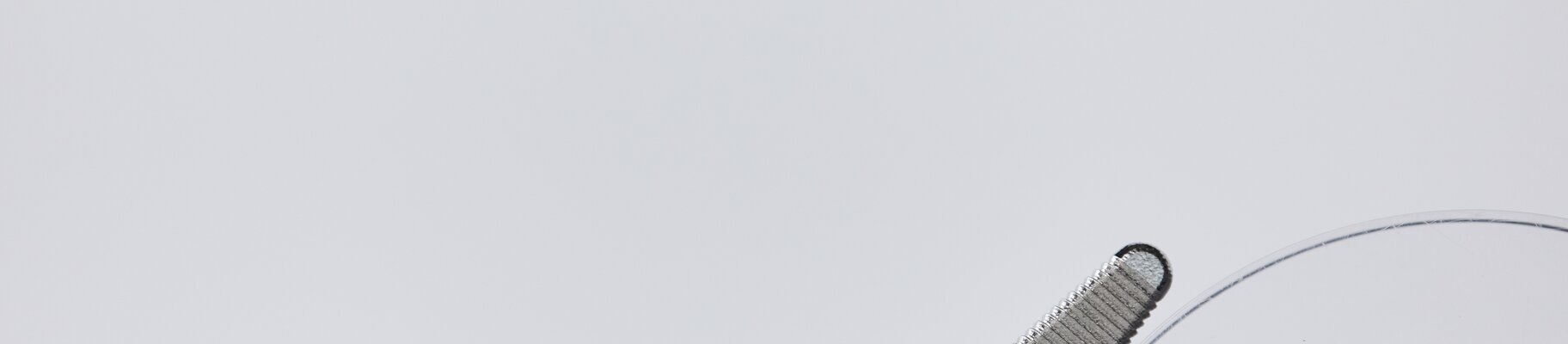
L'impression 3D au service de la technologie médicale
Production personnalisée et optimisée
Créer des innovations qui font la différence
La fabrication additive offre à l'industrie médicale une grande liberté de conception, d'adaptation et d'intégration fonctionnelle. Pour les fabricants de prothèses dentaires, de produits médicaux et orthopédiques, d'orthèses et de prothèses, cela crée de nombreuses opportunités d'une grande portée. Le contrôle total des formes, des matériaux et des conceptions spécifiques sur la base de données propres au patient permet d'offrir des traitements plus personnalisés, de simplifier la reconstruction biomécanique et de mettre en œuvre rapidement des méthodes thérapeutiques innovantes.
"Avec plus de 30 ans d'expérience dans la fabrication de toutes sortes de machines et de solutions pour la fabrication additive, nous avons accompagné et soutenu nos clients à travers une gamme variée de projets médicaux passionnants et innovants. Ce faisant, nous avons appris à comprendre les exigences spécifiques de ce marché."
Nous concevons notre technologie de production pour refléter notre connaissance des défis associés aux certifications et aux exigences spécifiques des matériaux. Pour de meilleurs soins aux patients.
Des solutions standardisées vers une approche spécifique au patient
La fabrication additive permet de fabriquer des prothèses, des orthèses et des implants dentaires directement à partir des données anatomiques individuelles de chaque patient. Il en résulte des produits sur mesure rapidement disponibles, ce qui améliore considérablement le processus de guérison et le pronostic.
L'impression 3D industrielle ouvre des perspectives considérables aux fabricants de prothèses dentaires, de produits de technologie médicale et orthopédique, d'orthèses et de prothèses : le potentiel de personnalisation des produits, associé à la rentabilité, permet de fabriquer des produits de meilleure qualité et plus viables économiquement, et de développer de nouveaux modèles commerciaux.

S'éloigner des solutions standardisées pour améliorer la fonctionnalité
La capacité de créer des géométries complexes et d'intégrer des fonctionnalités grâce au processus de fabrication additive offre de vastes avantages dans le domaine de la technologie orthopédique et de la fabrication d'équipements médicaux complexes.
Nos technologies sont maintenant utilisées dans les implants personnalisés depuis plusieurs années. Dans les cas complexes, traitement du cancer, révision d'implant ou accidents graves, ces patients peuvent bénéficier de la technologie de fabrication additive d'EOS qui permet de concevoir un produit spécifique et potentiellement très complexe et de le rendre rapidement disponible sur la base de leur diagnostic individuel. La technologie d'impression 3D d'EOS peut également être utilisée pour créer une grande variété de structures de surface, ce qui peut simplifier des processus tels que l'ostéointégration, c'est-à-dire la croissance entre le tissu osseux vivant et la surface de l'implant osseux.
Pour les équipements médicaux de haute technologie et les machines spécialisées, la liberté de conception permet de simplifier les assemblages et d'intégrer des fonctionnalités dans la pièce. Dans ces cas, la fabrication additive peut être rentable même avec des lots de petite taille. Les coûts d'outillage sont éliminés, de même que les coûts d'assemblage et de logistique.
Avec l'impression 3D, la conception est dictée par la fonctionnalité et non plus par la fabricabilité. Qu'il s'agisse de fabriquer des implants, des instruments chirurgicaux ou des produits médicaux complexes, la fabrication additive vous permet de réimaginer la géométrie. Vous pouvez ainsi concevoir et fabriquer vos produits plus efficacement pour leurs applications spécifiques.

Impression 3D pour les implants et les instruments chirurgicaux
Implants et instruments chirurgicaux spécifiques au patient et précis grâce à l'imprimante 3D
La technologie de fabrication additive EOS permet de créer des instruments et des implants adaptés avec précision, directement à partir de données de CAO.
Ce processus permet de fabriquer des implants sur la base des données anatomiques recueillies auprès du porteur et de les livrer rapidement. Cela permet d'éviter les temps d'attente ou les complications dues à des périodes d'inactivité prolongées, et les implants s'adaptent mieux. Il accélère également le processus de guérison dans son ensemble et a un impact positif durable sur la qualité de vie du patient.
"Les produits peuvent être conçus en fonction du diagnostic, quel que soit leur niveau de complexité, ils peuvent être fabriqués et livrés à la clinique dans les plus brefs délais. La fabrication conventionnelle prend environ 6 semaines, alors qu'avec la fabrication additive, la production est possible en seulement 10 jours.
La fabrication additive par EOS peut également être utilisée pour créer une grande variété de structures de surface, ce qui peut simplifier des processus tels que l'ostéointégration, à savoir la croissance entre le tissu osseux vivant et la surface de l'implant osseux. Les applications des implants imprimés en 3D comprennent les implants de la colonne vertébrale, les articulations de l'épaule (remplacement de la glène, implants de la hanche) et les implants pour la zone OMF (chirurgie buccale et maxillo-faciale).
Pour les interventions complexes, les chirurgiens ont de plus en plus recours à des instruments à usage unique spécifiques au patient. Les implants peuvent ainsi être insérés avec plus de précision, ce qui accroît le succès de l'opération pour les patients, les chirurgiens et les hôpitaux. Ces instruments personnalisés peuvent également être fabriqués à l'aide d'une imprimante 3D. Le chirurgien bénéficie d'un produit de haute qualité et précis qui répond aux normes strictes associées aux applications médicales.
L'impression en 3D permet une plus grande variété ("personnalisation de masse") et la production peut être réalisée "à la demande". Par rapport aux instruments à usage multiple, les hôpitaux économisent sur les coûts de stérilisation et de stockage et bénéficient d'une plus grande productivité.







L'impression 3D en pratique
Permedica : Impression 3D d'un cotyle de hanche artificielle

Pour afficher la vidéo, vous devez accepter les cookies de marketing.
Structure de surface pour une meilleure ostéointégration
L'implant peut être considérablement optimisé grâce à l'impression 3D. Le cotyle de la hanche se compose de parties fixes qui assurent la stabilité nécessaire et d'éléments à structure grossière. Ces éléments sont structurés directement pour assurer un ancrage solide de l'implant : les structures grossières sont avantageuses en termes de transmission de la pression, tandis que les structures plus petites soutiennent la fixation initiale. De cette manière, la structure complexe simplifie l'ostéointégration et accélère le processus de guérison.
Une production flexible est possible
En collaboration avec l'équipe d'EOS Additive Minds et le système bien établi pour les métaux, Permedica a réussi à créer un produit entièrement nouveau. EOS M 290 pour les métaux, Permedica a réussi à créer un produit totalement nouveau. L'ensemble de l'implant est fabriqué en une seule étape de production sur l'imprimante 3D et serait incroyablement difficile à reproduire avec des méthodes de fabrication conventionnelles. Grâce à la grande flexibilité de la fabrication additive, la surface et la taille du cotyle de la hanche peuvent être spécifiées individuellement pour chaque patient.
Livre blanc : Étude de capacité multi-machines pour les structures en treillis
Ce livre blanc étudie les performances d'un travail standardisé avec des structures en treillis imprimé sur trois systèmes EOS M 290 différents utilisant EOS Titanium Ti64ELI. En bref, les résultats vérifient que
-
La répétabilité des capacités d'une machine à l'autre est prouvée, la densité relative et la résistance à la compression atteignant toutes deux le niveau de confiance Six Sigma.
-
Il existe une forte corrélation entre la densité relative et la résistance à la compression.
-
Cette corrélation élevée permet de réduire la portée et les efforts des tests.
Vous voulez en savoir plus ? Obtenez le livre blanc gratuit ici.

Histoires de réussite d'EOS
Produits d'implantologie avec systèmes de fabrication EOS

Développement de matériaux biocompatibles pour les implants
Success story|Université du Michigan
L'Université du Michigan utilise une FORMIGA P 100 pour produire des implants personnalisés et vitaux pour les enfants. En collaboration avec EOS, elle développe de nouveaux matériaux biocompatibles.

Implants crâniens produits par fabrication additive
Histoire d'une réussite client | Alphaform
Développement et fabrication d'un implant de précision pour la zone crânienne avec une perméabilité particulière pour les liquides et la dissipation de la chaleur.
Instruments de médecine fabriqués de manière additive




BodyCad : Système de guidage chirurgical pour les opérations du genou
Pour afficher la vidéo, vous devez accepter les cookies de marketing.
En collaboration avec BodyCad, EOS a mis au point un gabarit de forage chirurgical pour l'arthroplastie personnalisée du genou. Le système offre une méthode plus précise et contrôlée pour préparer l'os à recevoir l'implant. La combinaison d'un implant spécifique au patient et d'un gabarit de forage chirurgical a été mise au point pour faciliter des interventions précises de remplacement ou de restauration du genou qui reflètent les caractéristiques anatomiques et le système musculo-squelettique du patient.
Le résultat a été un système révolutionnaire de genou unicompartimental (UKS) avec des instruments chirurgicaux spécifiques au patient. Les nouveaux instruments, dotés de gabarits de perçage personnalisés, garantissent une plus grande précision à moindre coût, des temps d'opération réduits et de meilleurs résultats cliniques. Fabriqué sur une FORMIGA P 110 avec le matériau PA 2201.
- Efficacité : les instruments peuvent être créés rapidement
- Rentable : coûts réduits par rapport aux procédés conventionnels
- Rapidité : les instruments spécifiques au patient peuvent être livrés dans un délai de 21 jours
Plates-formes stéréotaxiques pour la neurochirurgie
Production en petites séries de composants chirurgicaux de précision à l'aide d'une FORMIGA P 100.

Nos solutions de fabrication additive pour la technologie orthopédique
La fabrication additive permet d'optimiser le traitement des patients, de réduire les séjours à l'hôpital et d'atténuer les effets secondaires. Grâce à nos systèmes, vous pouvez fabriquer des implants et des instruments individuels à partir de matériaux de haute qualité et compatibles avec les exigences médicales, sur la base de données de CAO en 3D. Qu'il s'agisse de métaux ou de polymères, nos solutions d'impression 3D permettent de produire sans outil des produits hautement personnalisés à des coûts unitaires faibles dans un cadre rentable.
Nous vous aidons à mettre en œuvre vos produits
Grâce au système d'impression 3D approprié et à nos services complets de conseil et de formation, nos clients maîtrisent avec succès leur entrée dans la fabrication d'implants et d'instruments de haute précision spécifiques aux patients.
Notre portefeuille de solutions intégrées
Votre solution de production à partir d'une source unique
Nous proposons des solutions de fabrication 3D spécifiques aux clients pour l'ensemble de la chaîne de valeur - de la conception, du design et de l'ingénierie à la production et au post-traitement, jusqu'à la pièce finie. Profitez de plus de 30 ans d'expérience dans le domaine de la fabrication additive et bénéficiez de notre portefeuille complet de systèmes, de conseils et de services pour l'impression 3D industrielle de technologies et d'instruments orthopédiques, le tout auprès d'un seul et même fournisseur. En collaboration avec vous et notre réseau de partenaires très efficace, nous pouvons développer les solutions dont vous avez besoin pour votre propre production afin d'obtenir un portefeuille complet de solutions.
Fabrication additive pour les laboratoires et les équipements médicaux
Développés et produits plus rapidement, avec plus de souplesse et de rentabilité
Pour les équipements de laboratoire et les systèmes d'imagerie médicale (également connus sous le nom de diagnostic par imagerie ou simplement d'imagerie, par exemple CT, MRT ou équipement à rayons X), la fabrication additive est une technologie de production qui offre de nouvelles possibilités d'optimiser à la fois le produit et les coûts de fabrication.
De nombreux dispositifs médicaux et pièces d'équipement de laboratoire sont des produits de niche complexes qui ne sont produits qu'en petites séries. La production conventionnelle nécessite souvent des outils coûteux dont le coût doit ensuite être ajouté aux produits. En revanche, la fabrication additive fonctionne sans outils, ce qui permet de fabriquer des pièces en petites séries, jusqu'à la taille d'un lot.
Le processus de production est basé sur les données CAO des pièces. Cette technologie offre une grande liberté de conception, ainsi que la possibilité d'intégrer des fonctionnalités directement dans la pièce. Il en résulte des délais de mise sur le marché plus courts et un large éventail de possibilités d'optimisation des produits.
Découvrez ici quelles pièces d'équipement de laboratoire et d'imagerie diagnostique peuvent être optimisées dès aujourd'hui grâce à l'impression 3D d'EOS, et quelles machines et quels matériaux conviennent à votre application.
-
Production sans outil et réduction des coûts d'assemblage
-
Conception flexible et intégration fonctionnelle
-
Cycles de développement et délais de mise sur le marché plus rapides
3 pièces d'assemblage au lieu de 32 - le rotor de lavage de Hettich
Le fabricant de centrifugeuses Hettich a considérablement amélioré la rentabilité de sa production en série grâce à la fabrication additive et tire pleinement parti de l'impression 3D. Hettich a inventé et breveté un nouveau type de centrifugeuse qui permet de sédimenter et de séparer les composants sanguins en un seul appareil.

Pour afficher la vidéo, vous devez accepter les cookies de marketing.
Le ROTOMAT se compose d'un tambour moteur avec six conteneurs et des plateaux de collecte. Les conteneurs ont une géométrie élaborée et sont soumis à des vitesses de rotation élevées, avec des accélérations pouvant atteindre 1 200 fois l'accélération due à la gravité. Les centrifugeuses utilisent la force centrifuge pour séparer les mélanges en leurs composants. Les applications typiques comprennent la préparation d'échantillons de sang ou la réalisation d'un panel sanguin. Lorsqu'il est fabriqué de manière conventionnelle, chaque rotor de lavage se compose de 32 pièces distinctes qui doivent être assemblées. Cela nécessite des outils complexes et un processus d'assemblage qui prend du temps, d'autant plus que les injecteurs en acier inoxydable doivent être soigneusement ébavurés.
Le passage à la technologie EOS s'est avéré payant pour Hettich - avec des chiffres exceptionnels
- Le rotor de lavage a été redessiné et se compose désormais de 3 pièces d'assemblage au lieu de 32 - avec une fonctionnalité améliorée.
- Les conteneurs sont fabriqués sans outil, ce qui réduit les coûts de production.
- Les productions de petites séries et les adaptations régionales peuvent être facilement mises en œuvre.
- L'assemblage ne nécessite plus d'outils et l'étape de l'ébavurage, qui prend beaucoup de temps, est complètement éliminée.
Structures complexes, détails délicats, intégration fonctionnelle
La fabrication additive ouvre un large éventail de possibilités pour les équipements d'imagerie médicale. Le processus d'impression 3D permet de réaliser des géométries individuelles très complexes, y compris des structures qui ne seraient pas possibles avec la fabrication conventionnelle. Par exemple, les pièces des systèmes de tomographie assistée par ordinateur, de tomographie par résonance magnétique ou de radiologie peuvent être améliorées et fabriquées de manière plus rentable.

Imprimante 3D pour grilles anti-éclaboussures
Les grilles à rayons X (grilles anti-diffusion) captent les rayons X déviés par les tissus du patient avant qu'ils n'atteignent le film ou la plaque d'imagerie. Cela améliore le contraste et la précision des images radiographiques. La fabrication conventionnelle de grilles à rayons X est extrêmement difficile et longue, et donc coûteuse.
Mais l'impression 3D permet de fabriquer cette conception sophistiquée selon une approche nouvelle et optimisée. Le système EOS M 290 combiné au matériau EOS Tungsten W1 est la première et unique solution au défi exigeant de la fabrication de grilles radiographiques actuellement disponible sur le marché. Il présente un grand avantage et un coût unitaire plus intéressant que la fabrication par des méthodes conventionnelles.

La fabrication additive pour un ajustement parfait
Impression 3D pour la production de prothèses et d'orthèses
Nous proposons des systèmes, des matériaux et des processus, des logiciels et des services - tout ce dont vous avez besoin pour l'impression 3D de prothèses et d'orthèses. Avec nos solutions, les techniciens et les entreprises orthopédiques bénéficient de données fiables, de processus stables et de décennies d'expérience sur le marché.
Pourquoi l'impression 3D ? Avec les processus de fabrication conventionnels, le modèle doit être adapté manuellement à chaque patient. Le grand nombre d'étapes impliquées signifie que la production est coûteuse et prend du temps.
En termes de personnalisation et de rentabilité, les méthodes de production conventionnelles telles que le moulage, la modélisation et le fraisage atteignent rapidement leurs limites.
La fabrication additive offre un maximum d'avantages pour les patients et les fabricants. Le processus de fabrication est basé sur les données de numérisation de chaque patient, ce qui signifie que les prothèses et orthèses imprimées en 3D sont adaptées de manière optimale à l'anatomie et aux besoins du porteur.
"Les orthèses et les prothèses aident leurs porteurs à obtenir une meilleure mobilité. Mais chaque porteur a une anatomie, une utilisation et des besoins thérapeutiques différents. Les solutions d'impression 3D d'EOS combinent avec succès des processus de fabrication rapides et un confort optimal pour le porteur."






Avantages de la fabrication additive pour les orthèses et les prothèses
- Potentiel de personnalisation pratiquement illimité en termes de conception et de fonctionnalité
- Confort optimal pour le porteur : conception légère et stable malgré des structures complexes
- Durable - moins de consommation de matériaux, puisque les matériaux restants peuvent être réutilisés
- Les ajustements nécessaires peuvent être mis en œuvre rapidement, par exemple pour les enfants en pleine croissance.
- Confort accru grâce à l'intégration fonctionnelle pour plus d'élasticité, des conceptions respirantes, etc.
- Processus entièrement numérique, de la numérisation au produit fini, pour une disponibilité plus rapide
Fabrication de prothèses plantaires à la demande
Mecuris propose une plateforme numérique pour les patients, les médecins, les ateliers orthopédiques et les fournisseurs médicaux. À partir des données qui lui sont soumises, elle propose la fabrication à façon de prothèses imprimées en 3D sur des systèmes EOS.
Les pieds prothétiques personnalisés permettent une marche naturelle. Le processus de fabrication additive réduit considérablement les délais, assure un confort maximal et permet une conception personnalisée.

Pour afficher la vidéo, vous devez accepter les cookies de marketing.
Denise Schindler, cycliste paralympique
Des prothèses optimales grâce à l'impression 3D d'EOS et de Mecuris
Pour afficher la vidéo, vous devez accepter les cookies de marketing.
Des orthèses parfaitement adaptées pour les enfants
La jeune entreprise britannique Andiamo utilise les systèmes EOS pour fabriquer des orthèses sur mesure pour les enfants. Traditionnellement, les orthèses sont fabriquées à partir d'empreintes en plâtre. Ce processus est lent, nécessite beaucoup de ressources et offre peu de possibilités de personnalisation.
Certains patients, en particulier les jeunes patients en pleine croissance, doivent subir cette procédure à plusieurs reprises. Les délais d'attente peuvent aller jusqu'à six mois - pour une orthèse qui ne sera peut-être même pas adaptée lorsqu'elle sera prête. La fabrication additive réduit la période d'attente au minimum. À l'aide d'un scanner corporel en 3D, une orthèse précise et parfaitement adaptée est fabriquée et livrée en l'espace d'une semaine.
