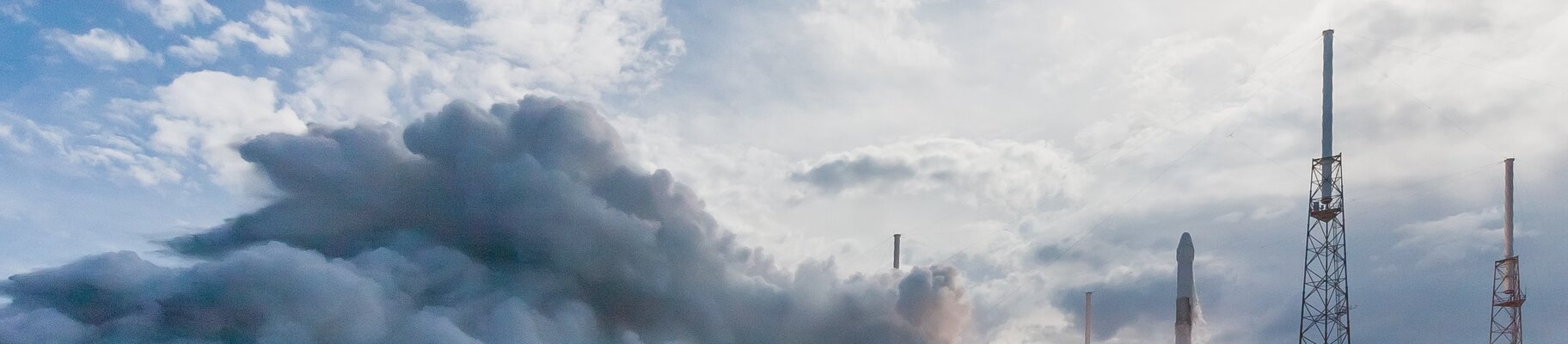
Le futur module de propulsion d'Ariane simplifié
ArianeGroup | Histoire d'une innovation
Conception tout-en-un - 122 buses d'injection et autres pièces en un seul composant intégré
La notion de "mission critique" décrit parfaitement les composants de classe 1 utilisés dans l'industrie aérospatiale. Des missions de plusieurs centaines de millions d'euros dépendent de ces composants. Par conséquent, les ingénieurs cherchent constamment à développer des composants de la plus haute qualité, fonctionnalité et robustesse, tout en simplifiant la chaîne de fabrication et en réduisant le nombre d'éléments individuels. Grâce à la technologie de fabrication additive EOS, ArianeGroup a réussi à franchir une nouvelle étape : Au lieu de 248 éléments, la tête d'injecteur d'un moteur-fusée d'un futur module de propulsion d'étage supérieur ne compte plus qu'un seul composant. La tête d'injecteur a été simplifiée et réduite à ce qui est littéralement une conception tout-en-un (AiO).

"Dans le cadre du programme Ariane, nous combinons notre force d'innovation avec l'expertise d'EOS. Ensemble, nous travaillons sur la fabrication additive d'une tête d'injecteur pour un moteur de fusée. Les résultats sont impressionnants : Une réduction significative du temps de production et des coûts réduits de 50 %."
Dr. -Ing. Steffen Beyer | Responsable de la technologie de production, des matériaux et des processus | ArianeGroup
Défi
Production d'une tête d'injection pour les moteurs de fusée avec le moins de composants possible et des coûts unitaires réduits
L'Agence spatiale européenne (ESA) souhaite occuper une position forte et indépendante dans le domaine du transport spatial en utilisant une technologie de lanceur efficace. Pour ce faire, ArianeGroup, une entreprise commune de la société aérospatiale européenne Airbus Group et du groupe français Safran, a été chargée de construire la prochaine génération. Ariane est une série de lanceurs européens conçus pour permettre la mise en orbite autour de la Terre de charges utiles lourdes, telles que les satellites de communication.
Dans un module de propulsion, des forces énormes se développent dans des conditions extrêmes. Cela exige des niveaux maximums de fiabilité et de précision dans un espace réduit. La tête d'injection est l'un des éléments centraux du module de propulsion, car elle alimente la chambre de combustion en carburant.
Sa conception traditionnelle consiste en 248 composants, produits et assemblés au cours de différentes étapes de fabrication. Les différentes étapes de traitement, telles que le moulage, le brasage, le soudage et le perçage, peuvent créer des points faibles susceptibles de constituer un risque en cas de charges extrêmes. En outre, il s'agit d'un processus long et complexe. Dans le domaine des éléments d'injecteur, la production conventionnelle nécessite le perçage de plus de 8 000 trous transversaux dans des manchons en cuivre qui sont ensuite vissés avec précision aux 122 éléments d'injecteur afin de mélanger l'hydrogène qui les traverse à l'oxygène.
Un coup d'œil sur ces chiffres montre clairement qu'un composant fonctionnellement intégré combinant tous les éléments doit être l'objectif évident mais ambitieux. Cela pourrait également libérer un potentiel économique important et réduire le nombre d'étapes de traitement ainsi que le temps de production, en particulier pour un composant de classe 1.
Solution
Un produit fabriqué de manière additive qui comprend un seul élément au lieu de 248 pièces individuelles grâce à l'intégration fonctionnelle.
La solution à ces défis est fournie par la fabrication additive. "La production de la tête d'injecteur en une seule pièce est possible grâce à la technologie EOS", explique Steffen Beyer, responsable de la technologie de production - matériaux et processus chez ArianeGroup, pour justifier le choix de l'impression 3D industrielle. "Seule la fabrication additive peut combiner des fonctionnalités intégrées, une construction légère, une conception plus simple et des délais plus courts dans un seul composant." L'équipe de projet a de nouveau choisi comme matériau un alliage à base de nickel (IN718) résistant à la chaleur et à la corrosion. Ce matériau offre une excellente résistance à la traction, à l'endurance, au fluage et à la rupture à haute température et sera également utilisé avec la nouvelle technologie de production.
"Après avoir développé avec succès le composant, nous nous sommes intéressés à la rentabilité", rapporte Fabian Riss, Production Technology - Materials & Processes. La principale exigence d'ArianeGroup était de réduire les délais et les coûts unitaires. La fabrication a d'abord été réalisée par un processus incrémentiel avec l'équipe d'ArianeGroup. EOS M 290. Après des essais pilotes réussis, la production a été étendue au système plus grand EOS M 400-4. La technologie laser 4 a permis de fabriquer le composant du module de propulsion jusqu'à quatre fois plus vite. "L'extension du processus de construction au système EOS M 400-4 à haute productivité était une étape importante pour nous afin de faire progresser l'industrialisation et la compétitivité du projet Ariane. La collaboration s'est déroulée très efficacement grâce à l'expérience et à l'expertise industrielle du personnel d'EOS. Les résultats parlent d'eux-mêmes et sont la preuve de l'excellente performance de l'équipe", ajoute Steffen Beyer.
Résultats
Les résultats de la nouvelle tête d'injecteur produite par fabrication additive sont extrêmement impressionnants : au lieu de 248 pièces, il n'y en a plus qu'une seule - avec la même fonctionnalité, et en réduisant le temps nécessaire au minimum.
La technologie d'impression 3D industrielle d'EOS, basée sur un lit de poudre, a permis, par exemple, d'imprimer les 122 buses d'injection, les plaques de base et avant, ainsi que le dôme de distribution avec les tuyaux d'alimentation correspondants pour les combustibles hydrogène et oxygène en un seul composant intégré. La productivité nettement supérieure du système multi-laser EOS M 400-4 a permis de diviser par trois le temps de construction et de réduire les coûts de 50 % dans le cas de la tête d'injection AiO par rapport aux systèmes à laser unique.
L'équipe du projet a pu enregistrer toute une série de succès supplémentaires. La conception simplifiée et les propriétés améliorées des matériaux par rapport à la qualité des pièces moulées ont permis à la technologie additive de réduire considérablement l'épaisseur des parois, sans perte de résistance.
Une réduction significative du poids signifie également une réduction supplémentaire du temps de construction et, bien sûr, des coûts.
Enfin, les procédés de fabrication additive permettent d'accélérer considérablement les cycles d'innovation. Les améliorations structurelles, les modifications de conception et la fabrication de composants d'essai au cours de la phase de développement peuvent être directement mises en production sur la base de données de CAO, sans que les ingénieurs aient à passer du temps à préparer les outils, comme c'est le cas pour les pièces moulées. L'impression 3D industrielle permet donc de faire un bond en avant en termes de délais. Alors que chaque itération nécessitait généralement environ une demi-année, une itération ne prend plus que quelques jours. De plus, l'ensemble de la chaîne de fabrication se déroule désormais en interne dans les locaux d'ArianeGroup. En un mot comme en cent : Mission accomplie !
Avantages
- -131 jours d'itération
- -247 Intégration fonctionnelle d'une pièce unique
- -Réduction des coûts de 50
Histoires d'innovation EOS
Découvrez trois décennies d'excellence en matière d'impression 3D avec EOS