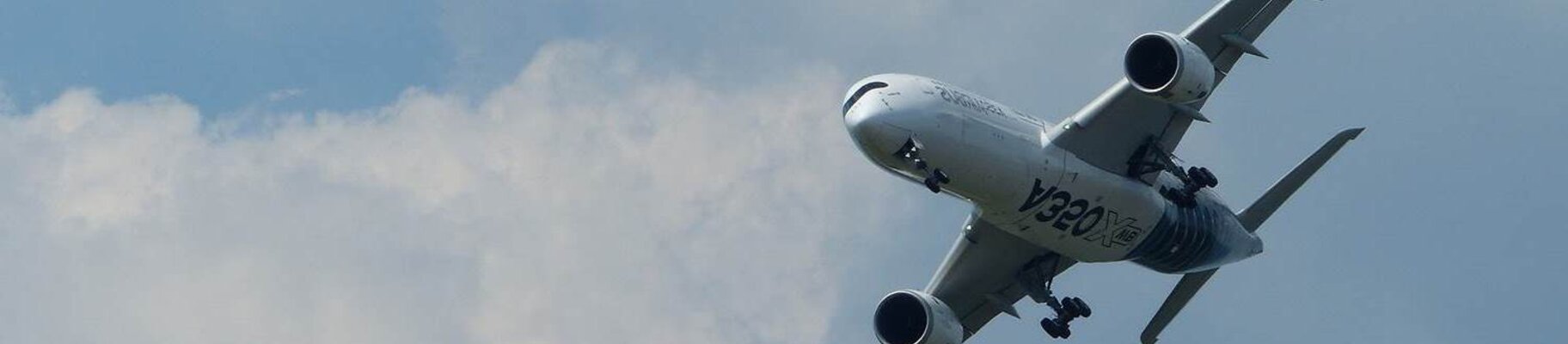
Fabrication additive de haute technologie de Sogeti pour le nouvel Airbus A350 XWB
Acheminement des câbles de l'A350 XWB - De la conception au composant en deux semaines - Histoire d'une réussite
Le moment où un avion commercial entièrement nouveau prend l'air pour la première fois est toujours spécial - et cela a été particulièrement vrai pour l'Airbus A350 XWB. Enfant du nouveau millénaire, il était clair dès le départ que les travaux de développement se concentreraient sur des matériaux et des processus de production innovants - l'objectif n'était rien de moins que de construire l'avion le plus performant au monde. En tant que technologie d'avenir, la fabrication additive était une autre possibilité à prendre en compte lors du développement. Dans le cadre d'un projet pilote, les experts de Sogeti High Tech ont réussi à développer un support de câble sur le longeron avant de la dérive de l'avion de ligne en un temps record, soit deux semaines seulement entre l'esquisse initiale et la pièce finie. La technologie et l'expertise d'EOS ont joué un rôle essentiel dans ce processus de développement.
"Obtenir un composant existant 'FA-ready' en seulement deux semaines signifiait que nous devions réussir du premier coup. L'excellente collaboration proactive avec EOS a rendu possible cette entreprise ambitieuse, avec des résultats exceptionnels.
Carlos Ribeiro Simoes | Leader de l'offre de fabrication additive | Sogeti High Tech
Défi
Développement et production d'un support de passage de câbles pour une caméra dans le stabilisateur vertical de l'A350 par fabrication additive, dans des délais très courts
Le projet consistait spécifiquement à produire un support de routage de câbles pour le dernier modèle d'Airbus. Le support était finalement nécessaire pour l'alimentation électrique et le transport des données d'une caméra située dans la dérive, offrant une vue de l'extérieur aux passagers et une orientation au sol aux pilotes.
Le cahier des charges du produit demandait un composant fonctionnellement opérationnel et apte à la production en série. Cette tâche a été confiée à Sogeti High Tech, filiale à 100 % de Cap Gemini S.A., société cotée à la Bourse de Paris.
Le défi particulier dans ce cas était le court délai d'exécution de seulement deux semaines. L'ensemble du développement devait être réalisé dans ce laps de temps : L'analyse de la pièce et de l'installation actuelle, l'étude des paramètres visant à optimiser la topologie et son interprétation, ainsi que la conception et la production de la pièce finie. La monture devait également comporter le moins de structures de support possible afin d'éviter tout traitement ultérieur.
En outre, les spécifications du composant prévoyaient l'intégration du support de câble encliquetable, la réduction du poids et la conformité aux exigences strictes de la certification ultérieure de l'industrie aéronautique.
Le composant fabriqué de manière conventionnelle était composé de pièces de tôle formées et de nombreux rivets - plus de 30 pièces individuelles au total. Les connecteurs de la partie supérieure étaient en plastique, et donc dans un matériau différent de celui des autres pièces du support. L'objectif était de développer une solution intégrée composée d'une seule pièce comprenant également les connecteurs, afin de réduire considérablement les temps de construction et d'installation. L'objectif de réduction du poids pour la fabrication additive a été déterminé par une étude des paramètres basée sur l'optimisation de la topologie.
Solution
La réduction à un seul composant et la fabrication sur EOS M 400 réduisent le temps de production à 19 heures.
Pour le nouveau composant, Sogeti High Tech a suivi le processus de développement éprouvé pour la conception de pièces fabriquées de manière additive. Le projet a débuté par une analyse du composant existant, produit de manière conventionnelle, en termes de processus de fabrication à venir - avec un résultat extrêmement positif. La fonctionnalité, le matériau et la structure complexe du composant en ont fait un candidat idéal pour la technologie d'impression 3D sur lit de poudre d'EOS. La liberté de conception offerte par cette technologie permet de produire des structures complexes en une seule pièce, ce qui signifie qu'il est possible d'opter pour une conception plus légère sans négliger l'intégration fonctionnelle.
Cette analyse a ensuite permis de définir ce que l'on appelle l'espace de conception, c'est-à-dire l'espace que le support d'acheminement des câbles peut occuper. L'alliage d'aluminium AlSi10Mg, idéal pour les structures complexes à parois minces, a été choisi comme matériau. Les interfaces avec les zones externes sont restées les mêmes, formant l'espace de non-conception, ce qui signifie qu'aucune modification n'a dû leur être apportée. Les charges définies ont été prises comme conditions limites pour l'optimisation de la topologie dans l'étude des paramètres, fournissant la base d'une nouvelle conception.
Comme d'habitude, un logiciel d'IAO a été utilisé pour les calculs d'optimisation de la topologie ; en revanche, une solution dédiée à la conception de structures avec des surfaces de forme libre a été utilisée pour la nouvelle conception. Sogeti High Tech a créé la conception elle-même. Afin de respecter le délai d'exécution de deux semaines, EOS a calculé le temps de construction et les paramètres optimisés à partir des résultats de l'optimisation topologique à l'aide du logiciel EOSPRINT. Cela a permis de créer l'implémentation IAO pour la pièce fabriquée tout en tenant compte des possibilités et des limites du processus de fabrication et de la nécessité d'éviter les structures de support.
"En plus d'un matériel exceptionnel, EOS offre également une expertise complète dans la réalisation de composants fabriqués de manière additive, ce que nous considérons comme très important.
Carlos Ribeiro Simoes | Leader de l'offre de fabrication additive | Sogeti High Tech
Résultats
Grâce à la coopération entre Sogeti et EOS, il a été possible de développer un composant optimisé pour la fabrication additive qui exploite pleinement la liberté de conception offerte par la technologie DMLS tout en tenant compte de ses restrictions. Cela a permis d'intégrer dans la conception des connecteurs pour l'acheminement des câbles et d'incorporer un renforcement local dans des zones critiques spécifiques afin d'optimiser la structure. Des ouvertures et des entretoises autoportantes à l'intérieur du composant permettent de réduire au minimum l'effort et donc les coûts de post-traitement.
En outre, la monture peut être produite très rapidement, à tout moment. La fabrication, qui s'effectue sur un support de 90μm d'épaisseur, ne prend que 19 heures au lieu des 70 jours nécessaires auparavant. EOS M 400 avec des épaisseurs de couche de 90μm - ne prend que 19 heures au lieu des 70 jours nécessaires auparavant.
Cela correspond à une réduction du temps de production de plus de 90 %. Cela s'explique en grande partie par le fait que les nombreuses étapes individuelles et les 30 pièces qui existaient auparavant ont été regroupées dans un composant central qui peut désormais être produit en une seule fois. En outre, il n'est plus nécessaire de fabriquer et de stocker les différentes pièces, ce qui peut s'avérer coûteux. Le stockage de l'ensemble des composants est également beaucoup plus simple.
Sogeti a pu gagner énormément de temps non seulement en production, mais aussi en développement. L'ensemble du processus, de l'esquisse initiale au composant fini, n'a pris que deux semaines. Il s'agit d'un délai phénoménal. Dans le même temps, la conception se traduit par une plus grande efficacité en termes de poids.
Alors que la pièce d'origine fabriquée de manière conventionnelle pesait 452 grammes, le support de câble fabriqué de manière additive ne pèse que 317 grammes - et il est bien connu que l'industrie aéronautique compte chaque gramme dans l'intérêt de réduire la consommation de carburant au minimum. Le client, Airbus, a été plus que satisfait des résultats.
Le résultat en un coup d'œil
- -29 Pièces uniques Intégration fonctionnelle
- -90 % de réduction du temps de production
- -135 grammes Réduction du poids
En savoir plus
Découvrez trois décennies d'excellence en matière d'impression 3D avec EOS