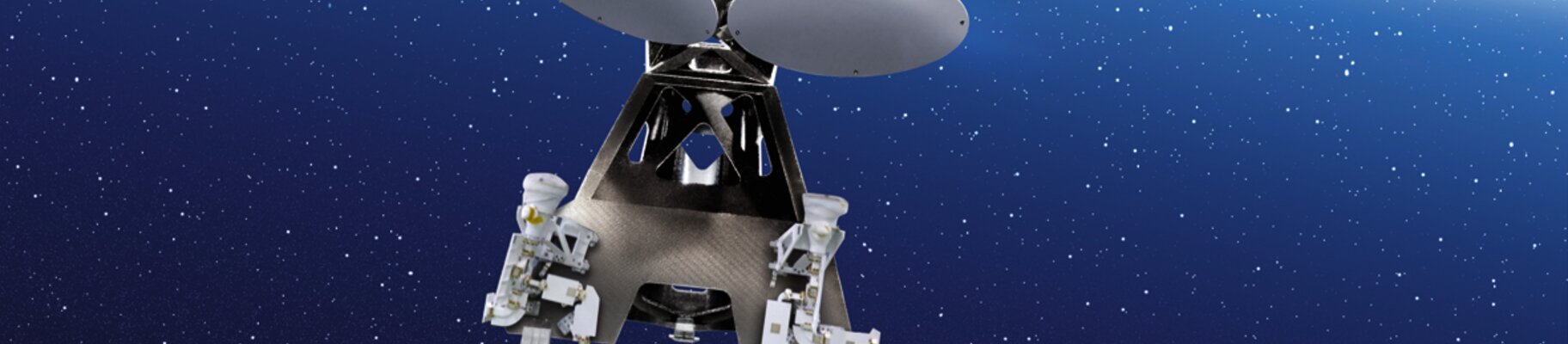
Le processus de fabrication avancée d'Airbus Defence and Space par EOS optimise la technologie des satellites
Airbus Defence and Space utilise la technologie EOS pour la production de pièces de satellites | Success Story
-
Meilleure résistance à la température
-
Réduction du temps de production
-
Réduction des coûts de production de plus de 20
"La méthode de fabrication additive a apporté des avantages mesurables à des aspects critiques du projet, sans qu'il soit nécessaire de faire des coupes ailleurs. Pas de compromis - c'est quelque chose que les ingénieurs aiment entendre, mais qu'ils n'entendent pas souvent.
Otilia Castro Matias | COC Antennae | Airbus Defence and Space
La génération actuelle de satellites comprend des supports spécifiques qui servent de lien entre le corps du satellite et les réflecteurs et installations d'alimentation montés à son extrémité supérieure. Les ingénieurs d'Airbus Defence and Space ont été confrontés à deux défis majeurs en ce qui concerne la construction de ces supports de retenue : d'une part, les supports doivent fixer solidement le corps du satellite. D'autre part, les supports doivent atténuer les fluctuations extrêmes de température dans l'espace.
Le choix s'est porté sur la technologie de fabrication additive de pièces métalliques proposée par EOS. Le titane restait ainsi un matériau éprouvé et utilisable. Elle a également permis d'adapter facilement la conception des composants.
Les nouveaux dispositifs répondent à toutes les attentes des experts concernés. Le plus important est l'amélioration de la résistance à la température de l'ensemble de la structure, qui peut désormais supporter facilement et durablement une marge de 330 °C sous une force de 20 kN. Outre les avantages techniques, des réductions de coûts ciblées ont été réalisées : les économies réalisées au niveau de la production s'élèvent à elles seules à plus de 20 %. De plus, les ingénieurs ont réussi à mettre la pièce au régime : le gain de poids est d'environ 300 g, soit près d'un kilo par satellite.

"L'utilisation du titane comme matériau pour les supports de fixation de nos satellites s'est avérée très efficace. La principale faiblesse, cependant, était la connexion des supports avec le panneau de carbone de l'alimentation et de l'assemblage du réflecteur, car ici la contrainte thermique était un facteur négatif. Grâce à la fabrication additive, nous avons pu redessiner le support et éliminer cette vulnérabilité. Il y a eu d'autres avantages, tels qu'une production plus courte, plus rentable et plus légère.
Otilia Castro Matias | COC Antennae | Airbus Defence and Space
Les résultats en un coup d'œil
- -20 % Réduction des coûts de production
- -300 grammes Réduction du poids