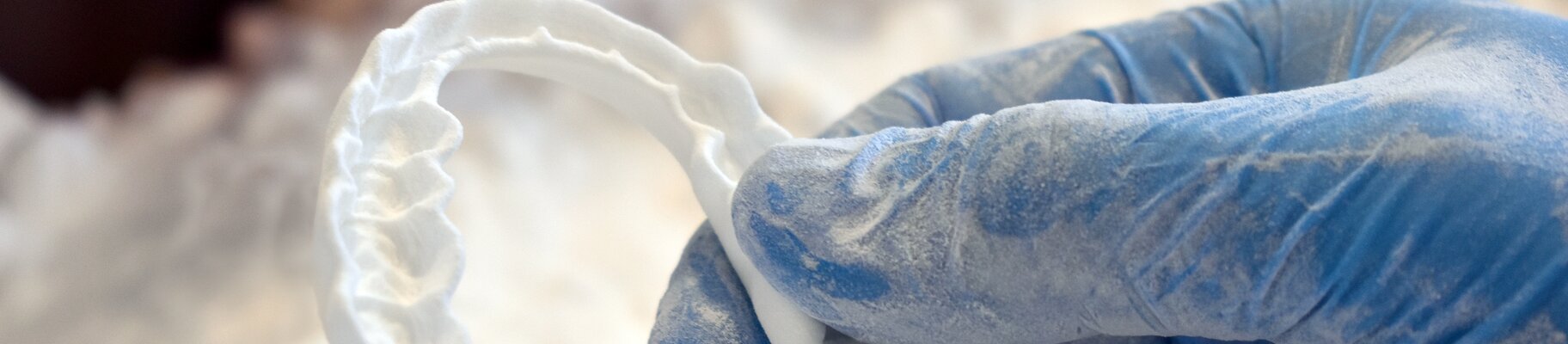
Révolutionner la dentisterie : L'impression 3D fait progresser les applications dentaires
OrthoApnea - Étude de cas
Améliorer la vie
- Amélioration de la qualité de vie de 75 000 patients dans le monde entier
- Haute précision dimensionnelle inférieure à ±0,1 mm améliorant l'adaptation et le confort des attelles
- Augmentation de 300 % de la capacité de production sans embauche de personnel supplémentaire
- Réduire les erreurs humaines grâce à un flux de travail de conception numérique plus souple
Malheureusement, le nombre de patients concernés et l'efficacité clinique d'une option de traitement ne permettent pas à eux seuls de prédire le succès de la thérapie. Alors que l'apnée obstructive du sommeil (AOS) touche environ 9 à 38 % des adultes et que des études suggèrent que jusqu'à 90 % des cas graves ne sont pas diagnostiqués, les traitements traditionnels n'ont pas encore fait leurs preuves.
De même, le bruxisme, qui touche 8 à 31 % des adultes, se heurte à des problèmes d'adhésion aux traitements conventionnels en raison d'un ajustement et d'un confort médiocres de l'appareil. Grâce à EOS FORMIGA P110 Velocis et au polyamide 12, Ortoplus a pu relever efficacement ces défis en utilisant un matériau biocompatible et des capacités de conception flexibles. Ces solutions d'impression 3D avancées permettent de créer des dispositifs médicaux sur mesure, confortables et spécifiques au patient, améliorant de manière significative l'adhésion du patient et les résultats dans le traitement du SAOS et du bruxisme.

"Grâce à la technologie avancée d'impression 3D, nous avons considérablement réduit nos délais de production, ce qui signifie que les patients reçoivent leurs dispositifs personnalisés plus rapidement que jamais."
Jesús García Urbano - PDG d'Ortoplus
Défi
Les traitements du bruxisme font généralement appel à des techniques de gestion du stress, à la kinésithérapie et à l'utilisation d'appareils buccaux tels que les gouttières occlusales. Cependant, pour les patients et les dentistes, le processus peut souvent être très coûteux en temps et en argent. Malgré l'efficacité des gouttières occlusales, l'adhésion au traitement peut être faible. L'inconfort, la difficulté à maintenir la gouttière en place pendant la nuit et les problèmes d'adaptation ou de rupture sont les raisons les plus courantes de l'abandon du traitement. En raison des efforts requis par les processus de fabrication traditionnels, la progression non traitée du bruxisme entraîne souvent des lésions dentaires importantes, qui nécessitent des traitements de restauration coûteux. En outre, la douleur et l'inconfort associés peuvent avoir un impact significatif sur la qualité de vie du patient, entraînant d'autres complications de santé et une augmentation des coûts de santé.
De même, l'apnée du sommeil, une fois diagnostiquée, n'est souvent pas traitée en raison des limites des options thérapeutiques actuelles. Les patients doivent souvent sacrifier leur confort à l'efficacité de la thérapie, et les dispositifs acryliques avec des barres et des vis présentent non seulement des taux d'échec plus élevés, mais ne sont pas non plus durables. Bien que la thérapie par pression continue des voies aériennes (CPAP) soit cliniquement efficace, jusqu'à 50 % des patients cessent de l'utiliser au cours de la première année en raison de l'inconfort, de la claustrophobie, de l'irritation de la peau, du bruit de l'appareil et des difficultés à maintenir l'appareil en place pendant le sommeil.
Précision et stabilité
Les attelles sur mesure soulagent les patients souffrant de bruxisme et d'apnée du sommeil.


Solution
Ortoplus a mis au point une solution de pointe utilisant le polyamide 12 et le site FORMIGA P 110 Velocis, garantissant des résultats reproductibles à l'échelle. Tout commence par l'enregistrement de la dentition du patient. Les gouttières en silicone doivent être numérisées par scanner. Les données numériques recueillies à l'aide de scanners intra-oraux peuvent être directement soumises à un contrôle de qualité. Sur la base de ces données vérifiées, les dispositifs sont conçus, imprimés en 3D et post-traités. Une fois qu'ils ont une finition très lisse, ils subissent un contrôle de qualité final pour s'assurer que les dispositifs sont dans un état optimal pour la livraison.
Ce flux de travail garantit la production de gouttières occlusales et de dispositifs d'avancement mandibulaire hautement durables, biocompatibles et confortables, adaptés à l'anatomie unique de chaque patient. La précision de l'impression 3D permet de créer des solutions personnalisées avec une grande précision dimensionnelle et des propriétés matérielles homogènes. Le PA 12 réduit non seulement le risque de réactions allergiques et d'irritations dues aux pièces métalliques, mais il est également résistant à la dégradation chimique et à l'usure mécanique, ce qui garantit sa durabilité au contact des tissus corporels, maximisant ainsi l'efficacité du traitement. Comme il peut être stérilisé à l'autoclave et aux rayons gamma, il aide les professionnels de la santé à se conformer aux normes de sécurité médicale les plus strictes.
Grâce à la FORMIGA P110 Velocis et à sa capacité à produire des pièces à géométrie complexe à l'échelle, les professionnels de la santé sont désormais en mesure de promettre aux patients un ajustement confortable, tout en réduisant les délais d'attente. Même en cas d'utilisation continue et de contraintes mécaniques, le PA 12 n'est pas aussi susceptible de se déformer que l'acrylique et constitue une solution plus écologique. Jesús García Urbano, PDG d'Ortoplus, conclut : "Grâce à la technologie avancée de l'impression 3D, nous avons considérablement réduit nos délais de production, ce qui signifie que les patients reçoivent leurs appareils personnalisés plus rapidement que jamais."
Résultats
Depuis la mise en œuvre de gouttières occlusales personnalisées et de MAD fabriqués avec le PA 12 et la technologie d'impression 3D EOS, Ortoplus a observé des améliorations significatives de la qualité de vie des patients souffrant de bruxisme et d'apnée du sommeil. À ce jour, son produit OrthoApnea a permis à lui seul d'aider 75 000 patients souffrant d'apnée du sommeil à atténuer leurs symptômes. Ortoplus est parvenu à ce résultat grâce à la production de dispositifs médicaux personnalisés de haute qualité. La solution Orthoapnea a été approuvée en tant que dispositif médical dans plusieurs cadres réglementaires majeurs, notamment la FDA aux États-Unis, la MDD dans l'UE, la MDEL au Canada et la TGA en Australie.
Par rapport à la fabrication traditionnelle, l'impression 3D a permis de tripler la capacité de production avec une qualité de production plus reproductible et plus précise, le tout sans qu'il soit nécessaire de recruter du nouveau personnel. Le fait de pouvoir concevoir des dispositifs numériquement a considérablement réduit le risque d'erreur humaine dans la production tout en élargissant les possibilités de conception. Les dispositifs ont également fait preuve d'une grande précision dimensionnelle, inférieure à ±0,1 mm, ce qui a considérablement amélioré l'ajustement et le confort des attelles, contribuant ainsi à la satisfaction globale du patient et à l'efficacité du traitement. "Sans les résultats fiables fournis par le polyamide 12, nous ne pourrions tout simplement pas faire ce que nous faisons. Nous avons étudié des dizaines de solutions sur le marché, mais aucune ne respectait les normes médicales tout en permettant un ajustement personnalisé comme le fait la technologie d'impression 3D d'EOS." Jesús García Urbano, PDG d'Ortoplus.
Ajusté et confortable
Améliorer l'adhésion des patients et réduire les temps d'attente en utilisant FORMIGA P110 Velocis et le matériau biocompatible PA 2200 pour créer des gouttières occlusales en nylon et des dispositifs d'avancement mandibulaire.


"Sans les résultats fiables fournis par le polyamide 12, nous ne pourrions tout simplement pas faire ce que nous faisons. Nous avons étudié des dizaines de solutions sur le marché, mais aucune ne respectait les normes médicales tout en permettant un ajustement personnalisé comme le fait la technologie d'impression 3D d'EOS."
Jesús García Urbano - PDG d'Ortoplus
Études de cas EOS
Découvrez trois décennies d'excellence en matière d'impression 3D avec EOS