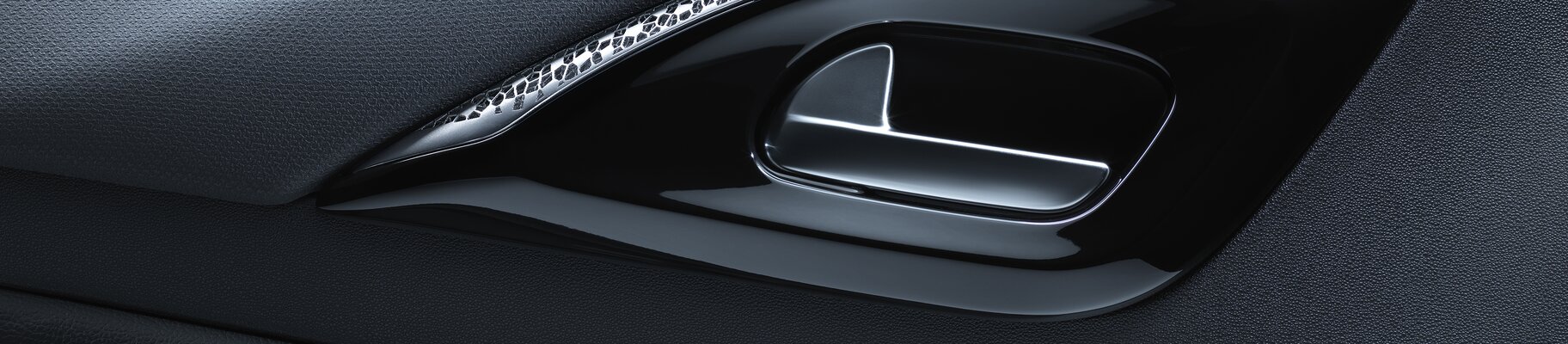
Fabrication additive pour des accessoires automobiles personnalisés
Spartacus3D - Histoire d'une réussite
DS 3 Dark Side Limited Edition - Innovation avancée grâce à la fabrication additive
Dans le secteur automobile, les éditions limitées de modèles à succès constituent une démarche marketing intelligente. Mais les constructeurs automobiles sont toujours à la recherche de moyens spécifiques pour se distinguer de leurs concurrents sur leurs segments de marché. DS Automobiles, une marque du groupe PSA, a réussi à s'imposer sur le segment haut de gamme en quelques années grâce à une série de modèles emblématiques. Le modèle compact DS 3 a bénéficié d'une large reconnaissance sur ce segment, et des éditions limitées sont régulièrement dévoilées. Pour l'édition Dark Side, DS Automobile a voulu aller plus loin que l'équipement habituel en incluant des pièces imprimées en 3D pour souligner son dévouement continu à l'innovation. La fabrication additive a donné une totale liberté de création à l'équipe de conception de DS, ainsi qu'une mise en œuvre et une production très rapides et faciles grâce aux experts de Spartacus3D travaillant avec une machineEOS M 290 .
"Ce fut un projet extraordinaire du début à la fin, aussi passionnant que stimulant pour notre expertise. Nous sommes ravis d'imaginer que toutes ces voitures sont aujourd'hui réparties dans le monde entier. Et tout au long de ce projet, nous savions que nous pouvions compter sur la fiabilité, la qualité et le soutien d'EOS."
Charles de Forges | Directeur général | Spartacus3D

Défi
Fabrication d'accessoires de haute qualité pour les voitures DS 3 en édition limitée, avec des designs uniques et une mise sur le marché rapide
Le projet a démarré lorsque l'équipe de DS Design a commencé à chercher des améliorations innovantes pour l'intérieur de l'édition limitée de la DS 3. Les accessoires devaient souligner la recherche constante d'innovation du constructeur automobile tout en satisfaisant aux normes de qualité les plus élevées exigées par le segment haut de gamme. Dès le départ, les concepteurs ont décidé d'exploiter le potentiel de la fabrication additive pour présenter une première mondiale dans ce domaine. La fabrication additive ouvre de toutes nouvelles possibilités de conception ;
DS Automobiles présente chaque année plusieurs éditions limitées pour la DS 3, c'est pourquoi ces nouvelles options changent vraiment la donne pour l'équipe. L'équipe de conception a également choisi le titane, un matériau qui donne une touche luxueuse, qui est résistant et qui permet une finition facile et esthétique.
Mais si l'impression 3D est couramment utilisée dans le secteur automobile pour le prototypage, la production en série par fabrication additive est encore très rare, en particulier pour les pièces métalliques. DS Automobiles a donc dû trouver un partenaire disposant à la fois d'une expertise en matière de fabrication additive et d'une capacité de production suffisante pour répondre à ses besoins en termes de volume. L'objectif était de livrer environ 700 voitures sur les marchés du monde entier. Le projet avait également un délai de développement limité pour correspondre au planning de production de la voiture, avec des objectifs très précis en termes de mise sur le marché.
Chaque édition limitée a un objectif de prix spécifique, de sorte que toutes les pièces fabriquées de manière additive doivent s'inscrire dans le budget global. La phase d'enquête a abouti au choix de deux pièces : la poignée de porte et le porte-clés.
Spartacus3D, filiale du groupe français de transformation de matériaux Farinia, répondait à toutes ces exigences : utilisant l'impression 3D depuis des années, l'entreprise possède une connaissance très approfondie de la fabrication additive qui l'a aidée à traduire en production les conceptions fournies par l'équipe de DS. Avec sa machine EOS M 290 et EOS Titanium Ti64, Spartacus3D possédait toutes les compétences nécessaires pour répondre aux exigences de conception et de qualité que DS Automobiles s'efforçait d'atteindre, ainsi que les capacités de production et de post-traitement requises pour livrer le projet dans les délais.
Solution
Production en série des pièces sur un EOS M 290 en EOS Titanium Ti64
L'équipe de conception de DS a utilisé un design paramétrique innovant pour créer les couvercles intérieurs des poignées de porte et le détail du porte-clés électronique dans une maille de titane très complexe, soulignant l'innovation et l'engagement de DS Automobiles en matière de qualité.
Afin de trouver le meilleur compromis entre la qualité, le coût et le design, de nombreuses itérations ont été nécessaires entre l'équipe de conception de DS et Spartacus3D. Il a notamment fallu fabriquer plusieurs prototypes, ce que la fabrication additive rend particulièrement facile à réaliser en un seul lot de production.
Dans le cadre de ce processus, l'équipe de conception de DS a également choisi la finition des pièces ; elle a finalement opté pour une belle finition mate obtenue par polissage manuel. L'équipe qualité a défini des critères d'acceptation précis pour la distorsion, la qualité de la surface (porosité et brillance) et les arêtes de coupe. Parallèlement à ce va-et-vient, Spartacus3D a également travaillé à l'optimisation de la production des pièces ; afin de réduire les coûts, Spartacus3D devait non seulement déterminer la meilleure orientation et la meilleure structure de support, mais aussi affiner sa stratégie exclusive de fusion au laser. Le titane est connu pour générer des contraintes résiduelles au cours du processus de fusion, et le couvercle de la poignée de porte, long et fin, était un bon candidat pour une distorsion maximale. L'ajout d'un traitement thermique de réduction des contraintes n'était pas viable en termes de coûts ; à la place, certains paramètres spécifiques ont été utilisés pour prévenir ce risque. D'autres moyens de réduire les coûts consistent à augmenter le nombre de pièces par lot ou à réduire le nombre de supports, la consommation de poudre, le temps de post-traitement, etc.

L'expertise de Spartacus3D en matière de fabrication additive s'est avérée précieuse à chaque étape du processus, de l'ingénierie de la conception à l'optimisation de l'impression 3D, ce qui a permis de raccourcir les cycles de développement des produits et d'accélérer la mise sur le marché. La sélection du matériau optimal a permis d'assurer la rigidité et de garantir une qualité maximale des pièces après le post-traitement. "C'est un privilège d'avoir été choisi comme partenaire de DS Automobiles pour ce projet très innovant. Leur marque représente fidèlement l'élégance et le savoir-faire de l'industrie automobile française depuis des années. Cela signifie également que nos efforts sont récompensés et montre que Spartacus3D est capable d'offrir des solutions robustes pour la production en série. En utilisant les systèmes DMLS dont nous disposons dans notre atelier, nous savions que nous serions en mesure de produire les meilleures pièces", déclare Charles de Forges, directeur général de Spartacus3D.
Résultats
Grâce à l'expertise de Spartacus3D en matière d'impression 3D, il a été possible de développer une stratégie de fabrication additive optimisée pour les besoins de l'équipe de conception de DS. La conception paramétrique exploite pleinement le potentiel de la technologie EOS : la conception originale très complexe des deux pièces a pu être produite presque à l'unité grâce à la fabrication additive et a été optimisée de manière à ce que plusieurs unités puissent être fabriquées en même temps. Les coûts de production ont ainsi été réduits au minimum.
Le matériau, EOS Titanium Ti64, a également permis une finition post-production, donnant une surface brillante et un aspect haut de gamme aux couvercles des poignées de porte et au porte-clés. Le résultat pourrait presque être décrit comme de l'art, avec un design épuré et raffiné et une structure très complexe qui combine parfaitement l'élégance française, l'innovation et l'exclusivité haut de gamme - tout ce que DS Automobiles représente.
Il y a eu environ 10 séries de production pour un total de 2 000 pièces - 3 pièces dans chaque voiture - ce qui a nécessité environ 2 000 heures de fabrication. L'ensemble du projet a été réalisé en quelques semaines seulement, depuis la validation de la conception par l'équipe de conception de DS jusqu'à la livraison des pièces finales.
DS Automobiles a pu créer quelque chose d'unique dans le secteur automobile en dépassant les limites de la fabrication traditionnelle, ce qui a permis à la DS 3 Dark Side de se démarquer de la concurrence. L'équipe de conception de DS a pu gérer un projet complexe dans un délai très court grâce à l'expertise fournie par Spartacus3D et aux capacités des solutions de fabrication additive d'EOS.

Les résultats en un coup d'œil
- Rentabilité : production de 200 pièces par tâche de construction sans impact sur la qualité
- Précision : amélioration des paramètres du processus afin d'éviter la déformation du couvercle de la poignée de porte de 30 cm de long et de faible épaisseur lors de la construction en position verticale.
- Rapide : moins d'une heure de production par pièce
- Liberté de conception : la maille tridimensionnelle en titane répond aux exigences de DS Automobiles en matière d'innovation et d'exclusivité haut de gamme.
Les succès d'EOS
Découvrez trois décennies d'excellence en matière d'impression 3D avec EOS