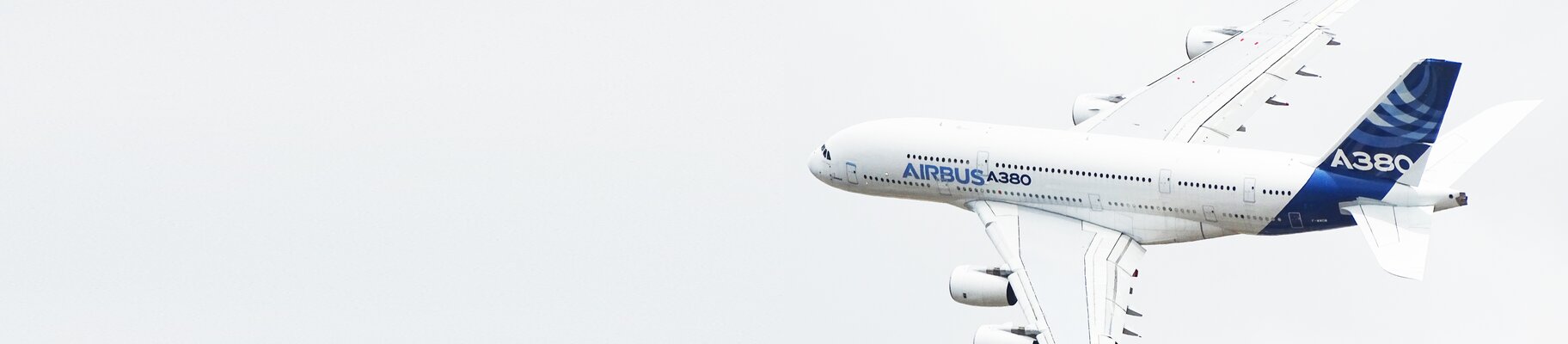
Liebherr - Premier composant hydraulique primaire de commande de vol en métal imprimé en 3D
Voler sur un Airbus A380 | Success Story
"D'ici quelques années, nous pensons que les pièces métalliques imprimées en 3D telles que le bloc de soupapes seront fabriquées en série chez Lieberr-Aerospace et livrées à nos clients. Le bloc de soupapes imprimé en 3D a prouvé que la fabrication additive avec la technologie EOS est réalisable pour la construction de composants de vol primaires critiques".
Alexander Altmann | Ingénieur en chef, Fabrication additive, Recherche et technologie | Liebherr-Aerospace Lindenberg GmbH
Défi
Remplacer un composant hydraulique primaire conventionnel des commandes de vol par une pièce fabriquée de manière additive - répondant à toutes les exigences de certification pour le vol.
Dans le contexte d'une prise de conscience écologique croissante, de l'augmentation du prix des carburants et du manque de sources d'énergie alternatives, l'industrie aérospatiale doit trouver de nouvelles technologies pour rester compétitive. L'impression 3D industrielle sur lit de poudre a le potentiel d'apporter un changement fondamental et de faciliter la fabrication de composants innovants. Liebherr a lancé son programme de fabrication additive il y a six ans déjà. Aujourd'hui, l'entreprise a prouvé que la technologie d'impression 3D de métaux EOS est applicable aux collecteurs hydrauliques des avions. En collaboration avec Airbus et une équipe de recherche de l'université technologique de Chemnitz, Liebherr a lancé un projet financé par le ministère fédéral de l'économie et de l'énergie (BMWi).
L'objectif était de remplacer un composant de vol primaire conventionnel, un bloc de vannes hydrauliques à haute pression, par un composant fabriqué de manière additive.
À bord d'un avion, de nombreux composants travaillent ensemble pour assurer la sécurité du vol. Un actionneur de spoiler déplace le spoiler dans la position souhaitée pour réduire la portance de l'avion. Ce type de composants primaires de commande de vol exige les normes de qualité et de précision les plus élevées lors de la production. Traditionnellement, la fabrication des blocs de soupapes commence par un matériau brut forgé, qui est ensuite usiné, taillé, percé et enfin assemblé. Cette chaîne de processus est longue et complexe, ce qui laisse peu de place à l'optimisation. Toutefois, le nombre même d'étapes du processus illustre la marge de manœuvre pour les améliorations possibles grâce à l'impression 3D de métaux. Il est clair que la substitution ne suffit pas ; la nouvelle pièce doit être plus légère, efficace en termes de ressources et respectueuse de l'environnement pour démontrer la faisabilité de la fabrication additive en tant que technologie prometteuse pour l'avenir.
Solution
Fabrication d'un composant léger imprimé en 3D avec moins de pièces et une chaîne de processus efficace
La solution a consisté à développer une chaîne de conception et de processus à mettre en œuvre dans l'industrie aéronautique en utilisant la technologie d'impression 3D industrielle fiable et de haute qualité d'EOS. Tout d'abord, la pièce conventionnelle a été analysée. Les structures hydrauliques ont été identifiées et les sections auxiliaires ont été supprimées. Le positionnement des principaux composants a été reconsidéré à la lumière de leur espace d'installation et des exigences d'interface, dans le but d'optimiser les lignes de connexion intelligentes et courtes. Cette démarche a jeté les bases de la conception de la nouvelle pièce. "Avec l'impression 3D industrielle, la complexité n'est soudain plus un problème. Sur le systèmeEOS M 290 , les composants sont construits à partir d'un grand nombre de couches minces, chacune d'une épaisseur de 30 à 60 μm, ce qui nous permet de construire des géométries complexes ", explique Alexander Altmann, ingénieur en chef de la fabrication additive, de la recherche et de la technologie chez Liebherr-Aerospace Lindenberg GmbH. "Les éléments fonctionnels ont été directement reliés les uns aux autres à l'aide de tuyaux incurvés. Cela évite d'avoir recours à un système complexe de tuyaux avec de nombreux alésages transversaux, ce qui permet de gagner du temps en production."
Le matériau choisi, un alliage de titane, est particulièrement adapté à l'aviation car il présente de nombreux avantages. Il permet de réaliser des économies de poids et de réduire les coûts d'exploitation, car il est très léger, mécaniquement stable et présente une très bonne résistance à la corrosion. Les étapes de post-traitement comprennent par exemple un traitement thermique pour réduire les contraintes, ainsi qu'un traitement spécial pour les canaux hydrauliques.
Enfin, "il ne doit pas y avoir le moindre doute quant à la fiabilité et à la sécurité des composants et du matériau à partir duquel ils sont fabriqués. Grâce à la technologie EOS, nous sommes en mesure de fabriquer de manière fiable des composants en titane de la plus haute qualité, ce qui est une condition préalable à l'étape suivante de la production en série", explique Alexander Altmann.
Bloc de soupapes fabriqué par Liebherr sur EOS M 290: mêmes performances, 35 % de poids en moins
Résultats
Le nouveau bloc de vannes à fabrication additive offre les mêmes performances que le bloc conventionnel, mais il est 35 % plus léger et comporte moins de pièces. Il a été possible d'intégrer 10 éléments fonctionnels dans le nouveau bloc de vannes, ce qui a permis d'éliminer le système complexe de tuyauterie comportant de nombreux alésages transversaux.
"Cela pourrait être le slogan de la fabrication additive - faire la même chose mais avec moins de masse et moins de pièces - mais il s'agit d'une étape importante pour nous, chez Liebherr-Aerospace", déclare M. Altmann. La nouvelle pièce imprimée en 3D a été testée avec succès lors d'un vol d'essai de l'A380.
L'impression 3D industrielle est moins complexe et extrêmement efficace en termes de matériaux par rapport au processus de fraisage traditionnel et permet de réduire au minimum les déchets de titane. "Aujourd'hui, la fabrication d'un bloc de valve prend environ une journée et nous pensons pouvoir réduire le temps de construction de plus de 75 % avec le site EOS M 400-4", déclare Alexander Altmann.
Mais ce n'est pas tout : le bloc de soupapes léger imprimé en 3D et les futures pièces imprimées en 3D contribueront également à réduire la consommation de carburant et les émissions de CO2 et de NOX. C'est pourquoi Liebherr s'attache à comprendre les méthodes de fabrication additive dans les moindres détails afin de mettre en place des processus de production d'une fiabilité absolue. Avec EOS, Liebherr dispose d'un fournisseur de technologie et d'un partenaire qui facilite l'assurance qualité pendant le processus de fabrication additive. En participant à une phase pilote, Liebherr a pu contribuer au développement de EOSTATE Exposure OT , un nouveau module de la suite de surveillance EOS qui permet une inspection transparente et en temps réel des composants.
"À l'avenir, cela accélérera l'identification des défauts des matériaux au cours du processus d'impression 3D industrielle et contribuera à réduire la nécessité de recourir à des processus d'assurance qualité en aval, tels que la tomographie assistée par ordinateur", explique Alexander Altmann.
Les résultats en un coup d'œil
- -75 % de temps de production
- -35% Réduction du poids
- -10 pièces uniques Intégration fonctionnelle
Histoires d'innovation EOS
Découvrez trois décennies d'excellence en matière d'impression 3D avec EOS