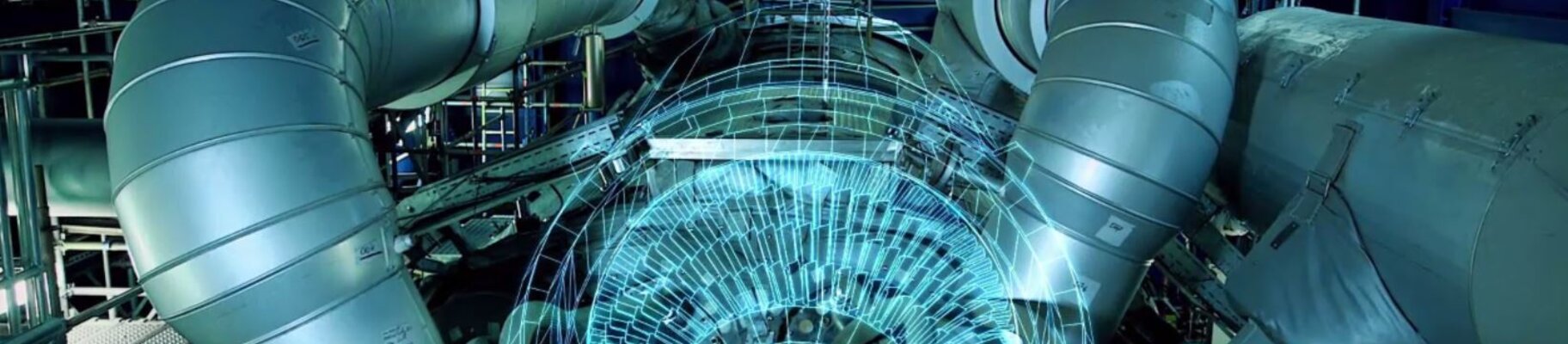
Impression 3D pour les turbines à gaz industrielles à haute performance
Etude de cas Siemens
La société suédoise Siemens ENERGY fabrique des turbines à gaz pour la production d'électricité dans les applications industrielles, pétrolières et gazières. La gamme de performances de ces turbines industrielles Siemens s'étend de 15 à 60 MW. Outre la construction, la filiale de Siemens assure également l'entretien et la maintenance à long terme de ces chefs-d'œuvre d'ingénierie. Afin de réduire les coûts de maintenance, Siemens travaille au développement et à la mise en œuvre de la technologie de fabrication additive, en utilisant la technologie et l'équipement d'EOS.
"La fabrication additive nous ouvre de nouvelles dimensions dans l'utilisation de la conception et de la production intégrées. Cette technologie nous permet de fabriquer et de réparer les composants de nos turbines à gaz industrielles beaucoup plus rapidement qu'auparavant. Dans le même temps, la fonctionnalité et les performances de la pièce sont accrues."
Vladimir Navrotsky | Responsable de la technologie et de l'innovation, Siemens Energy Service | Pétrole et gaz et applications industrielles
Défi
La turbine à gaz se compose d'une entrée d'air, d'un compresseur, d'une chambre de combustion, d'une turbine et d'une sortie de gaz chaud. L'air qui traverse le moteur est comprimé par le compresseur. Dans la chambre de combustion, l'air comprimé est mélangé à du carburant et brûlé afin d'augmenter l'énergie cinétique du flux. Dans la turbine, l'énergie cinétique du flux est convertie en énergie mécanique. Cette énergie mécanique est utilisée pour faire tourner le compresseur et le générateur de la turbine à gaz (pour produire de l'électricité) ou d'autres équipements entraînés (par exemple, le compresseur pour pomper le gaz/pétrole dans les pipelines). Pendant le fonctionnement, les composants situés sur le trajet des gaz chauds du moteur sont exposés à des températures élevées, parfois supérieures à 1 000 °C (par exemple, les aubes et les palettes). Cela entraîne une forte usure des composants du circuit des gaz chauds.
Il en va de même pour la pointe du brûleur, qui est le point d'allumage du mélange air-carburant. Ici, les effets de l'usure sont clairement visibles et mesurables. Le fabricant a effectué des tests rigoureux pour établir une période de fonctionnement prescrite après laquelle les brûleurs doivent généralement être réparés.
La procédure de réparation conventionnelle nécessitait la préfabrication de grandes sections de la pointe du brûleur.
Cette unité préfabriquée est utilisée pour le remplacement de la pointe du brûleur après la durée d'utilisation spécifiée (découpe de l'ancienne pointe et soudage de la pointe préfabriquée). La procédure de réparation conventionnelle peut prendre beaucoup de temps et impliquer un nombre important de sous-processus et d'examens. Pour simplifier et accélérer la procédure de réparation, Siemens a mis en œuvre la technologie de fabrication additive.

Solution
Une telle opération nécessite un partenaire innovant. Siemens a trouvé ce partenaire en la personne d'EOS : en plus de disposer de la technologie de fabrication additive appropriée, EOS a également été en mesure, dans un délai très court, d'adapter individuellement l'une de ses machines internes - une EOSINT M 280 - pour le traitement des métaux.

Les modifications concernaient notamment l'échelle de l'intérieur de la machine, qui devait être agrandie pour accueillir le brûleur de 800 mm. Le fabricant a également modifié d'autres composants matériels tels qu'un système de caméra et un système de mesure optique et a procédé aux adaptations correspondantes du logiciel. EOS a réalisé la refonte complète du système EOSINT en moins d'un an.
Dès le début, il est apparu clairement que l'approche était payante. Plutôt que de remplacer une grande partie de la pointe du brûleur, Siemens a commencé par retirer uniquement le matériau endommagé. En outre, lors de la réparation, les anciennes versions des brûleurs de la flotte ont pu être reconstruites selon la dernière conception. Cela signifie que les anciennes versions des brûleurs de la flotte pouvaient non seulement être réparées, mais aussi améliorées - donnant ainsi un nouveau sens à l'expression "fabrication additive".
Résultats
Les chiffres, les données et les faits montrent clairement le succès du nouveau processus de réparation. Siemens ENERGY sera en mesure d'avoir un impact significatif sur la préoccupation centrale - la réduction du délai de réparation : pour l'opérateur, il est tout aussi important que les turbines soient rapidement prêtes à être remises en service. Pour l'exploitant, il est tout aussi important que les turbines soient rapidement remises en service. Cela ouvre également des possibilités supplémentaires de réduction des coûts en ce qui concerne le processus de réparation et la maintenance.
Outre l'amélioration de son propre processus de réparation, Siemens peut désormais offrir à ses clients des avantages stratégiques : Grâce à ce nouveau processus, les experts peuvent apporter des améliorations à la technologie des turbines en intégrant les composants dans le processus de réparation. De cette manière, les opérateurs peuvent utiliser les dernières technologies, même si leurs turbines ont des années de service.
Vladimir Navrotsky, responsable de la technologie et de l'innovation chez Siemens Energy Service, Oil & Gas and Industrial Applications, résume la situation : "Grâce à cette nouvelle technologie de réparation, nous envisageons d'effectuer ces travaux de haute précision beaucoup plus rapidement."
La filiale suédoise de Siemens n'est pas la seule à considérer ce projet comme une réalisation importante. "Nous avons réussi à faire entrer notre technologie dans le domaine de la réparation. Nous avons montré que nous sommes capables de modifier rapidement notre système pour répondre aux exigences spécifiques des clients. Dans ce cas, les modifications apportées au matériel et au logiciel ont été importantes. Toutes les personnes impliquées peuvent se féliciter, non seulement du résultat final, mais aussi du chemin parcouru pour y parvenir", déclare Stefan Oswald d'EOS.

Les résultats en un coup d'œil
- Innovant : les anciennes versions des brûleurs peuvent rapidement être mises à niveau avec les technologies les plus récentes.
- Rentabilité : les réductions de coûts potentielles sont déjà visibles à un stade précoce.
- -Réduction de 90 % du temps nécessaire au processus de réparation
Études de cas EOS
Découvrez trois décennies d'excellence en matière d'impression 3D avec EOS