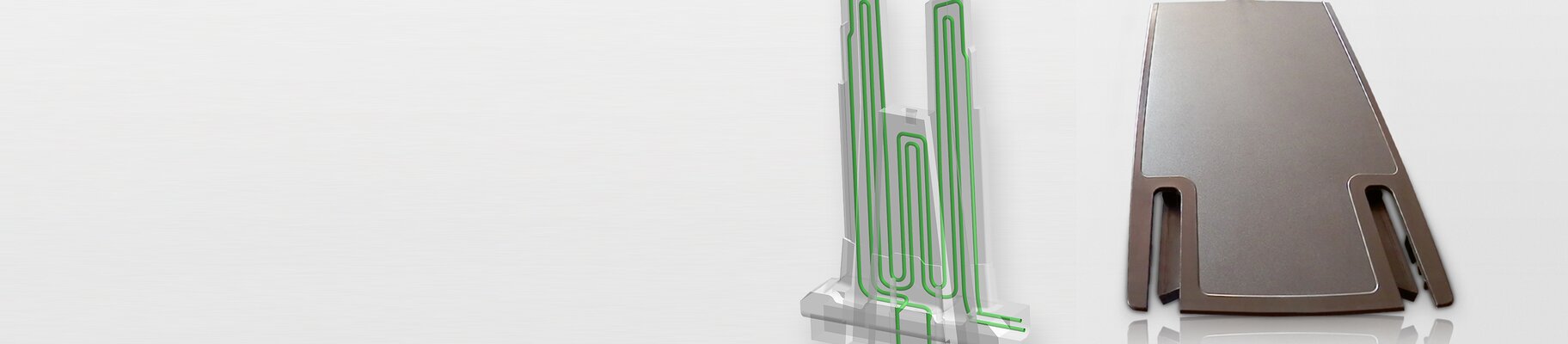
Utilisation de la fabrication additive pour le refroidissement conforme
Augmenter l'efficacité grâce à l'impression 3D de métaux
Innomia - Histoire d'une réussite
-
Les coûts sont réduits grâce à une diminution de 17 % des temps de cycle pour les moulages par injection plastique.
-
L'entretien des installations de production est passé de toutes les deux semaines à toutes les cinq ou six semaines.
-
Le refroidissement uniforme empêche la déformation du produit final en plastique
Impression 3D de métaux pour le refroidissement conforme
Innomia utilise des imprimantes 3D EOS pour optimiser le processus de production de pièces en plastique moulées par injection. Il s'agit d'une révision du processus de refroidissement. Le cas concerne la fabrication de l'accoudoir situé entre les sièges avant.

Pourquoi le refroidissement conforme ?
L'énergie thermique du matériau de base liquide doit être dissipée dans l'ensemble de l'outil de fabrication pour permettre au plastique de se solidifier. Le processus de refroidissement détermine, entre autres, la qualité du composant. En effet, une dissipation irrégulière de la chaleur peut entraîner des déformations.
Les concepteurs d'Innomia ont donc logiquement commencé à développer un nouveau système de refroidissement des plaquettes d'outils. L'optimisation de l'évacuation de la chaleur générée par le processus de production figurait en tête de liste des priorités.
L'équipe a décidé d'opter pour des canaux de refroidissement de précision intégrés, le refroidissement conforme, une application testée et éprouvée dans le cadre de la technologie DMLS, et l'une des solutions que seuls les processus de fabrication additive peuvent fournir. L'imprimante 3D métal EOS, un système éprouvé depuis de nombreuses années, a été déployée pour Innomia.
Le refroidissement de précision et la production à l'aide de la technologie de fabrication additive ont donné les résultats escomptés. La distribution de la température et la dissipation de la chaleur qui y est associée sont désormais nettement plus homogènes. La chaleur étant répartie et quittant plus rapidement l'outil et le composant, une température de l'eau de 60 °C suffit pour le refroidissement, ce qui réduit l'énergie nécessaire. La surface de la plaquette elle-même ne s'échauffe pas au-delà de 90 °C, ce qui a permis aux ingénieurs de résoudre les problèmes d'humidité dans la zone environnante.
Grâce à Innomia et à la technologie d'impression 3D EOS, Magna, client d'Innomia, bénéficie d'un intervalle de maintenance étendu à cinq ou six semaines. Le problème de la condensation de l'humidité de l'air et de la corrosion potentielle des cavités a été entièrement résolu. Les canaux de refroidissement uniformes fonctionnent si bien que le temps nécessaire au cycle de production est désormais inférieur de 17 % à ce qu'il était auparavant.
"La question du refroidissement est un problème que nous essayons de résoudre depuis longtemps. Nous savions à quoi devrait ressembler un produit amélioré, mais sa fabrication n'était tout simplement pas possible. La fabrication additive nous a permis de faire une percée. Nous avons pu planifier les canaux de refroidissement exactement comme nous le souhaitions et fabriquer le noyau du moule en conséquence. Le laser fusionne la poudre métallique couche par couche, de sorte que toutes les formes sont possibles. Le résultat nous a convaincus à tous les niveaux. Maintenance, qualité du produit final, coûts, dissipation de la chaleur - c'est le projet parfait.
Pavel Strnadek | Responsable de la maintenance des outils | Magna
Les résultats en un coup d'œil
-
-17% Temps de cycle
-
Réduction des coûts
-
L'entretien de l'usine de production est passé de toutes les 2 semaines à toutes les 5 ou 6 semaines
"L'industrie automobile en Europe est soumise à une forte concurrence. Ce fait a naturellement un effet sur les fournisseurs tels que Magna. C'est pourquoi il est très important pour nous de pouvoir produire selon les normes de qualité les plus élevées au prix le plus bas. Avec l'optimisation de notre usine de production grâce à l'amélioration du refroidissement de nos outils, nous avons créé un exemple classique de la manière dont la technologie peut contribuer à accroître l'efficacité. Nous avons réduit les coûts de maintenance de notre usine de production, optimisé la qualité de nos composants et augmenté le nombre de cycles de production. Nous avons ainsi pu tenir la promesse de qualité que nous avions faite à notre client et, en même temps, répondre à nos propres exigences élevées en matière de rentabilité".
Luboš Rozkošný | PDG | Innomia
Les succès d'EOS
Découvrez trois décennies d'excellence en matière d'impression 3D avec EOS