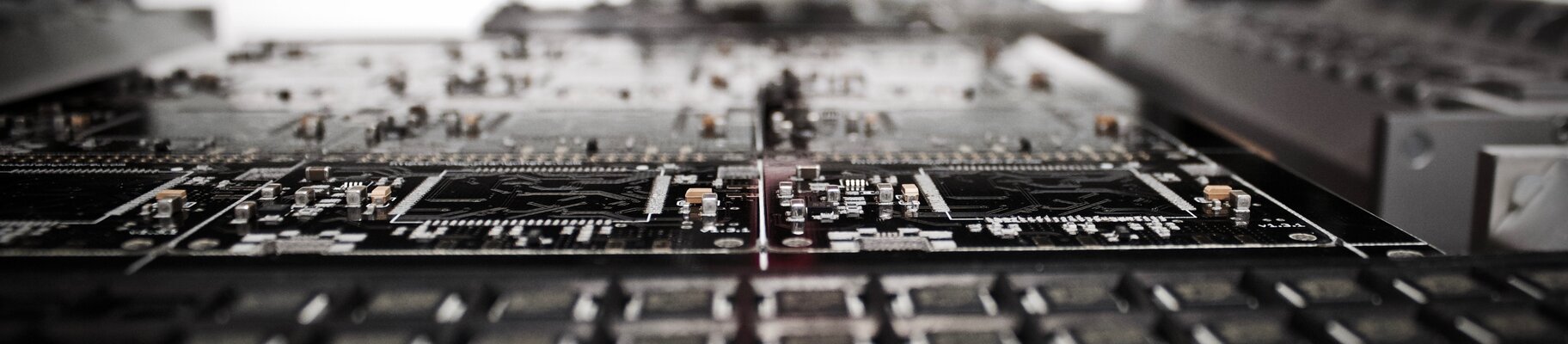
Supports de circuits multidimensionnels par fabrication additive
Beta LAYOUT | Etude de cas
Prototypes de nouveaux circuits imprimés créés avec la technologie EOS
Au début de l'année 2016, nombreux étaient ceux qui écrivaient sur la fin de la loi de Moore, anticipant que les performances des puces informatiques ne doubleraient plus tous les deux ans. La raison en est que les structures des processeurs eux-mêmes se situent déjà à quelques nanomètres de ce qui est possible. D'un point de vue technique, il est pratiquement impossible de réduire encore les performances. Pour continuer à améliorer les performances, les fabricants travaillent sur l'architecture, qui empile plusieurs couches structurelles les unes sur les autres. Une approche similaire a déjà été mise en place dans le domaine des supports de circuits. La société allemande Beta LAYOUT GmbH a réussi à exploiter la technologie EOS pour fabriquer et tester les prototypes de ces supports innovants.
"Grâce à ses nombreux avantages, la technologie de fabrication additive offre une forte valeur ajoutée à un large éventail d'acteurs du marché. La recherche et le développement profitent de nos services, ce qui a un impact positif sur notre modèle d'entreprise. Cela nous permet d'offrir les avantages d'une technologie avancée à un grand nombre d'utilisateurs".
Manuel Martin | Chef de produit 3D-MID | Beta LAYOUT GmbH
Défi
Production de prototypes individuels pour les supports de circuits
Les supports de circuits et les circuits imprimés traditionnels ont toujours été un peu éclipsés par les microprocesseurs qui y sont intégrés. C'est un peu injuste car, bien sûr, avoir le meilleur cerveau ne sert pas à grand-chose sans les avantages d'un système nerveux central performant. Il en va de même dans le secteur de la microélectronique : presque tous les appareils contemporains ont besoin d'un circuit imprimé pour intégrer une ou plusieurs puces, ainsi que les composants électriques supplémentaires nécessaires. Il en résulte un réseau qui remplit toute une série de tâches, de l'alimentation en électricité à l'émission de signaux, en passant par la fabrication de circuits.
Dans les nouveaux appareils, il n'y a souvent que très peu d'espace disponible pour les cartes de circuits imprimés conventionnelles. Cela s'explique notamment par le fait que de nombreux équipements électroniques sont de plus en plus petits et que, même lorsque la forme elle-même est plus grande, il reste généralement très peu d'espace pour l'électronique proprement dite. Le volume existant est nécessaire pour loger des écrans, par exemple, de plus en plus d'interfaces et de points de sortie, ainsi que des batteries plus volumineuses. L'époque où un simple circuit imprimé de laboratoire suffisait pour la construction expérimentale de nouveaux circuits est aujourd'hui révolue, dans la plupart des cas et des secteurs. Outre l'espace d'installation disponible, le poids est un facteur clé - les circuits imprimés compacts, construits en trois dimensions, ont également un rôle important à jouer à cet égard.
Dans les produits électroniques contemporains, les circuits doivent souvent se disputer l'espace limité du boîtier. Lorsqu'ils sont empilés de manière conventionnelle, les circuits imprimés ne peuvent plus contenir tous les composants nécessaires, de sorte que les supports de circuits tridimensionnels susmentionnés deviennent la solution de choix. Là encore, les cycles de vie de plus en plus courts de nombreux appareils posent des défis supplémentaires : le moulage par injection est beaucoup trop coûteux pour fabriquer des prototypes. C'est pourquoi Beta LAYOUT GmbH a décidé de rechercher une alternative moins coûteuse et plus performante.
Solution
Aucune technologie n'est mieux adaptée aux exigences de l'architecture multicouche que la fabrication additive. En effet, elle utilise un laser pour construire un composant, couche par couche. C'est pourquoi Beta LAYOUT s'appuie sur cette technologie et utilise des pièces en plastique fabriquées par impression 3D. L'innovation intervient après le processus d'impression lui-même : une fois fabriqués, les modèles sont recouverts d'une finition spéciale fournie par un additif. La "structuration directe au laser" (LDS) qui s'ensuit génère des tracés qui peuvent être transformés en pistes conductrices en activant la finition.
Le laser déclenche une réaction physico-chimique qui crée des spores métalliques tout en rendant la surface rugueuse. Après la structuration directe au laser, les modèles sont placés dans un bain de cuivre exempt de courant électrique. Des particules de cuivre sont alors déposées sur les zones précédemment activées pour créer des pistes conductrices. Après le revêtement de cuivre, les pistes conductrices peuvent être soumises à un cuivrage supplémentaire par galvanisation ou être directement pourvues d'une finition de surface. Beta LAYOUT ajoute ensuite les différents composants à l'unité dans le département d'assemblage interne de l'entreprise. Les pièces finies servent de prototypes et de modèles initiaux, ce qui permet de tester les fonctions et de vérifier les schémas de conception.
"Nous proposons à diverses entreprises la fabrication de prototypes 3D-MID (dispositifs mécatroniques intégrés) ", explique Manuel Martin, chef de produit 3D-MID chez Beta LAYOUT GmbH. "Grâce à la FORMIGA P 110 d'EOS, nous sommes en mesure de livrer rapidement des produits de haute qualité à nos clients. Ce qui est particulièrement pratique, c'est que nous sommes même en mesure de traiter des commandes de modèles 3D via des sites Web et des boutiques en ligne. La fabrication additive nous a permis d'étendre avec succès notre modèle commercial.

Résultats
Qu'il s'agisse de développeurs individuels ou de grandes entreprises établies, la fabrication additive permet d'utiliser des supports de circuits sur mesure pour les prototypes de nouveaux appareils électroniques. Les composants en plastique peuvent être produits rapidement et à un prix attractif. Le processus offre simultanément le niveau de précision nécessaire et une qualité élevée des composants, ce qui permet de fabriquer le corps de base requis comme s'il s'agissait déjà d'un produit proche de la série - un aspect qu'il ne faut pas sous-estimer, en particulier pour les essais.
La technologie EOS offre également une grande flexibilité : la machine utilisée est capable de traiter différents matériaux, comme par exemple le PA 3200 GF rempli de billes de verre ou le polyamide chargé d'aluminium. Alumide. Des polymères haute performance tels que le PEEK et divers métaux sont également disponibles. Le point crucial est que tous les matériaux sont capables de résister à des températures élevées, une limitation du processus de moulage par injection dans la production en série.
Grâce à cette flexibilité, Beta LAYOUT est en mesure de répondre aux diverses exigences individuelles de ses clients, par exemple en répondant aux caractéristiques particulières de l'utilisation prévue du support de circuit. L'entreprise peut ainsi développer des solutions individuelles et optimisées, que ce soit en termes de réduction des coûts, de résistance accrue à la température ou d'autres exigences spécifiques.
Outre ces avantages, la fabrication additive offre également un autre atout : "En fin de compte, nous assistons ici à une démocratisation de la technologie de pointe. Sans de telles innovations, nous ne serions pas en mesure d'offrir le service 3D-MID", déclare Manuel Martin. "Cela signifierait que de nombreuses petites entreprises et maisons de développement n'auraient aucune chance de réaliser de tels prototypes. Par conséquent, le pouvoir d'innovation et de création des petites et moyennes entreprises, dont on parle tant, perdrait de son élan et le secteur de la recherche et du développement serait beaucoup moins dynamique."
La fabrication additive est un catalyseur pour d'autres innovations et, de cette manière, peut-être un point de départ vers l'établissement d'une nouvelle loi de Moore.

Les résultats en un coup d'œil
- Simple : accès aux technologies de pointe pour la recherche et le développement
- Personnalisé : fournisseur de produits sur mesure
- Économique : la production sans outil réduit les coûts
Études de cas EOS
Découvrez trois décennies d'excellence en matière d'impression 3D avec EOS