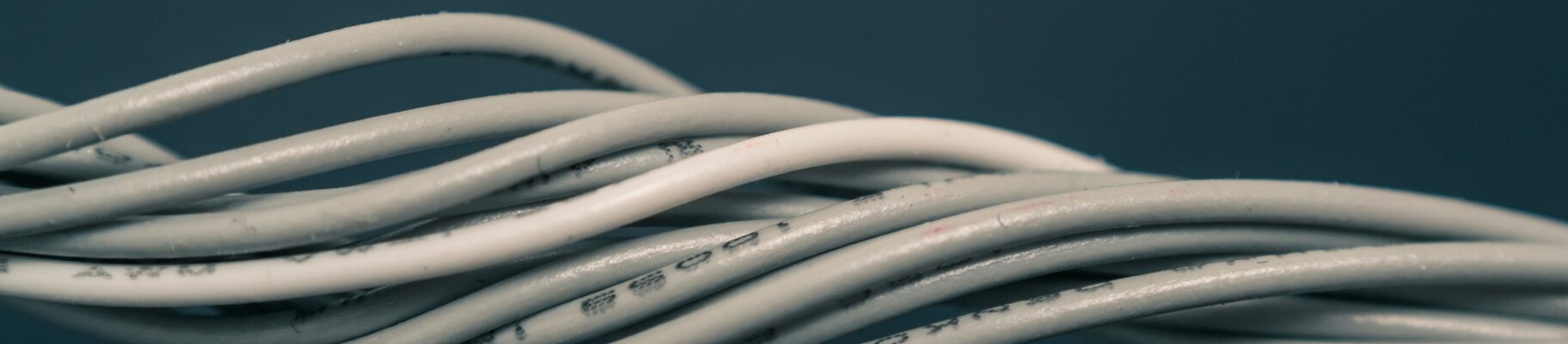
Präzision und Stabilität: Die Zukunft der elektrischen Steckverbinder durch FDR 3D-Druck
WAGO | Fallstudie
Hervorragende Leistungen erbringen
- Schnelle Lieferung mit Komponenten, die innerhalb von Tagen und nicht Wochen verfügbar sind
- Erstklassige Qualität, die vom Endprodukt kaum zu unterscheiden ist
- Optimierte Effizienz mit minimaler Nachbearbeitung
- Detailauflösung erfüllt die Anforderungen der
Labortest des Prototyps
Ohne Strom geht in unserer Gesellschaft und Wirtschaft fast nichts mehr - die Stromleitungen in Häusern, Fabriken, Schiffen, Zügen usw. sind die Lebensadern unserer Zeit. Damit die Elektronen ihre Energie transportieren können, müssen sie über Kabel an die richtige Stelle gelangen. Dazu braucht es zuverlässige Anschlusskomponenten, wie sie WAGO in Ostwestfalen herstellt. In Anlehnung an die kalifornische IT-Hochburg Silicon Valley wird der dortige Elektronik-Cluster auch "Terminal Valley" genannt. Und das zu Recht, wie WAGO beweist: Im Bereich der additiven Fertigung (AM) nutzt der Prototypenbau ein hochauflösendes Verfahren zur Herstellung von Prototypen in der Verbindungstechnik, die sogenannte Fine Detail Resolution (FDR). So konnte WAGO die Federklemmen für ein neues Produkt auf der EOS FORMIGA P 110 FDR mit PA 1101 sehr schnell und präzise prototypisieren - und damit die Time-to-Market für eine neue elektrische Anschluss- und Verteilerdose erfolgreich verkürzen.

"Der Mensch braucht Modelle. Wenn man schnelle Fortschritte machen will, führt kein Weg am industriellen 3D-Druck vorbei. Er ist unser Arbeitspferd. Das reguläre Selektive Lasersintern hat uns bereits beeindruckt, aber FDR hat es in puncto Feinheit, Präzision und Geschwindigkeit noch einmal übertroffen."
Olaf Zoschke | Leiter des Prototypenbaus WAGO GmbH & Co. KG
Herausforderung
Das Verbinden zweier elektrischer Leitungen mag zunächst einfach klingen, stellt aber im Detail hohe Anforderungen an Innovation, Funktion, Sicherheit und Qualität. Wo Strom fließt, gibt es zu Recht genaue Vorschriften. Verbindungen müssen praktischen, sachlichen und gesetzlichen Sicherheitsanforderungen genügen: "Ein Kabel darf auch unter Last nicht einfach aus der Kontaktstelle herausrutschen", erklärt Olaf Zoschke, Leiter des Prototypenbaus bei der WAGO GmbH & Co. KG. "Außerdem muss die Kontaktkontur von entsprechender Qualität sein. Wäre diese nicht gewährleistet, könnte es zu Personen- und Sachschäden kommen." Er leitet den Prototypenbau bei WAGO: Mit seinem siebenköpfigen Team erstellt er Design- und Funktionsprototypen sowie Prüfmuster, die in internen und externen Labors Funktions- und Sicherheitstests bestehen müssen; vorher darf kein neues Produkt verkauft werden.
Entsprechend umfangreich und häufig sind die Sicherheitsprüfungen für die von WAGO und seinen Marktbegleitern entwickelten Produkte. Dabei gilt es, einige Herausforderungen zu meistern: Ob an der Zählerstation im Haus oder im Schaltschrank im Triebwagen, der Platz für elektrische Verteilungen wird immer kleiner. Gleichzeitig steht immer weniger Zeit zur Verfügung, um entsprechende Produkte zu entwickeln, zu testen und auf den Markt zu bringen. "Wer schnell sein will, kommt an der additiven Fertigung nicht vorbei", bringt es Olaf Zoschke auf den Punkt. Zudem müssen die Muster dem endgültigen Serienprodukt möglichst genau entsprechen - denn sie sollen nicht nur Prüfingenieure, sondern auch Fachhändler und andere Käufer überzeugen.
Bei der Entwicklung einer neuen Anschlussdose mit möglichst geringem Bauraum erwies sich die Konstruktion der Kabelzugentlastung als besondere Herausforderung: Wird ein Leiter in die Dose gesteckt, muss er sicher einrasten. Dies geschieht über einen Klemmmechanismus. Dieser rastet über ein Verriegelungsgetriebe ein. Etwaige Zugkräfte auf den Leiter müssen durch diese Fixierung an seiner Isolierung aufgenommen werden. Der Kontakt selbst darf nicht beansprucht werden. Um den Größenanforderungen gerecht zu werden, müssen auch die auf die Laschen aufgebrachten Zahnräder so klein wie möglich sein. Gleichzeitig ist ein hohes Maß an Stabilität erforderlich, um die einschlägigen Sicherheitsvorschriften zu erfüllen. In der Serienfertigung ist ein solcher Anforderungskatalog umsetzbar, weil sich die Kosten für herkömmliche Verfahren auf große Stückzahlen verteilen lassen. Aber im Prototypenbau?
Präzise und schnell
Der 3D-Druck ermöglichte es WAGO, innerhalb kürzester Zeit eine voll funktionsfähige Anschlussdose zur Marktreife zu entwickeln.


Lösung
"Wir verändern das Bauteil natürlich während des Entwicklungsprozesses im Zuge von ersten Tests und Optimierungen. Hier ist die additive Fertigung bekanntlich im Vorteil. Vor allem aber brauchen wir bestimmte Losgrößen für die Funktions- und Labortests. Wir sprechen hier von zehn bis 50 Stück, die natürlich absolut gleichwertig sein müssen. Die hohe Präzision, die zum Beispiel für Feinverzahnungen erforderlich ist, war bis vor kurzem nicht möglich", erklärt Olaf Zoschke. Erst FDR hat es möglich gemacht, die Vorteile des industriellen 3D-Drucks in Anwendungen mit sehr filigranen Bauteilen einzubringen.
Das feindetailauflösende Verfahren der additiven Fertigung mit Hilfe der FORMIGA P 110 FDR ist an dieser Stelle die perfekte Wahl: Aufgrund der sehr kleinen Bauteile wird nur eine kleine Baukammer benötigt, um die benötigten Stückzahlen in einem Durchgang herzustellen. So entsteht auch eine "perfekte zeitliche Abstimmung" mit den anderen Teilen der Prototypen. Diese werden je nach Anforderung mit anderen Verfahren hergestellt, unter anderem mit dem gröberen Selektiven Lasersintern (SLS). "Für das größere Teil 1 reicht zum Beispiel konventionelles SLS, für das kleinere Teil 2 setzen wir auf FDR. SLS ist zwar schneller als der hochauflösende 3D-Druck, aber aufgrund der Teilegröße bekommen wir die Muster in etwa der gleichen Zeit", erklärt Olaf Zoschke anschaulich.
Das Prototyping-Team legt im Vorfeld fest, welches Verfahren jeweils zum Einsatz kommen soll: Die Entscheidung dafür sowie für das Material wird bereits in der CAD-Planung getroffen - je nach späterem Verwendungszweck. Entscheidend ist letztlich die Frage, wie die geforderte Qualität in der geforderten Menge sinnvoll geliefert werden kann. Dabei kann das Team von Olaf Zoschke die Stärken der einzelnen Verfahren und Materialien gezielt nutzen. "FDR ist die goldene Mitte von Präzision, hoher Kantenschärfe und Funktionsintegration; PA 1101 als Werkstoff ist dafür sehr gut geeignet. Es gibt Prototyping-Verfahren, die noch genauer sind. Allerdings fehlt dort zum Beispiel die Funktionsintegration. Standard-SLS wäre schneller, ist aber nicht so genau", ergänzt der Leiter des Prototypenbaus.
Ergebnisse
Und diese hochauflösende goldene Mitte der 3D-Druckverfahren hat zum gewünschten Ziel geführt: WAGO konnte die Muster der Zahnräder und Platten erfolgreich herstellen - in der gewünschten Zeit, in den geforderten Toleranzen und in den benötigten Stückzahlen. Auf diese Weise ist ein langlebiges Bauteil entstanden, das dem späteren Serienprodukt in puncto Langlebigkeit in nichts nachsteht. Die Herstellung und Nachbearbeitung dauerte nur etwa zwei Tage, andere Verfahren benötigen ein bis zwei Wochen. Apropos Nachbearbeitung: Aufgrund der hohen Auflösung des FDR-Verfahrens für die additive Fertigung waren nur wenige Nacharbeiten am Bauteil notwendig.
Olaf Zoschke bestätigt dies: "Die EOS-Produkte haben auch ohne FDR immer eine sehr gute Qualität geliefert. Wir haben in der Nachbearbeitung immer beeindruckende Ergebnisse erzielt. Mit Fine Detail Resolution sind diese noch besser. Wir erreichen einen extrem guten Wert für das Prototyping von etwa 80 Prozent der Qualität des späteren Serienbauteils. Das hat auch unsere Produktentwickler begeistert." Ein weiterer Grund für die Überlegenheit der hochauflösenden Technologie beim SLS liegt in der Nachbearbeitung: Das Verfahren ermöglicht auch die chemische Glättung von Unebenheiten. Dies führt zu leichten "Unschärfen" und ist daher nicht ganz so präzise wie die Herstellung mittels FDR.
Auf diese Weise erhielt das WAGO-Bauteil auch die notwendigen Produkteigenschaften für die Musterprüfungen: Die filigranen Laschen und ihre Verzahnung sorgen für die nötige Festigkeit. Gleichzeitig sind sie so hochwertig gefertigt, dass sie nahtlos und damit robust ineinandergreifen - die Verhakung führt zu der erforderlichen Leiterklemmkraft. Und mehrfache interne und externe Tests haben bewiesen: Wenn ein additiv gefertigtes Bauteil hält, hält es auch in der Serie. Das innovative FDR-Verfahren hat also gehalten, was es verspricht: die Präzision und Geschwindigkeit des industriellen 3D-Drucks weiter zu steigern, bei voll integrierter Funktionalität.
Robust & Zuverlässig
3D-Druck kann erstklassige Qualität liefern, die vom Endprodukt kaum zu unterscheiden ist
"Die EOS-Produkte haben auch ohne FDR immer eine sehr gute Qualität geliefert. Wir haben in der Nachbearbeitung immer beeindruckende Ergebnisse erzielt. Diese sind mit Fine Detail Resolution noch besser. Wir erreichen einen extrem guten Wert für das Prototyping von etwa 80 Prozent der Qualität des späteren Serienbauteils. Das hat auch unsere Produktentwickler begeistert."
Olaf Zoschke | Leiter des Prototypenbaus WAGO GmbH & Co. KG
EOS-Fallstudien
Erleben Sie drei Jahrzehnte Pionierarbeit im 3D-Druck mit EOS