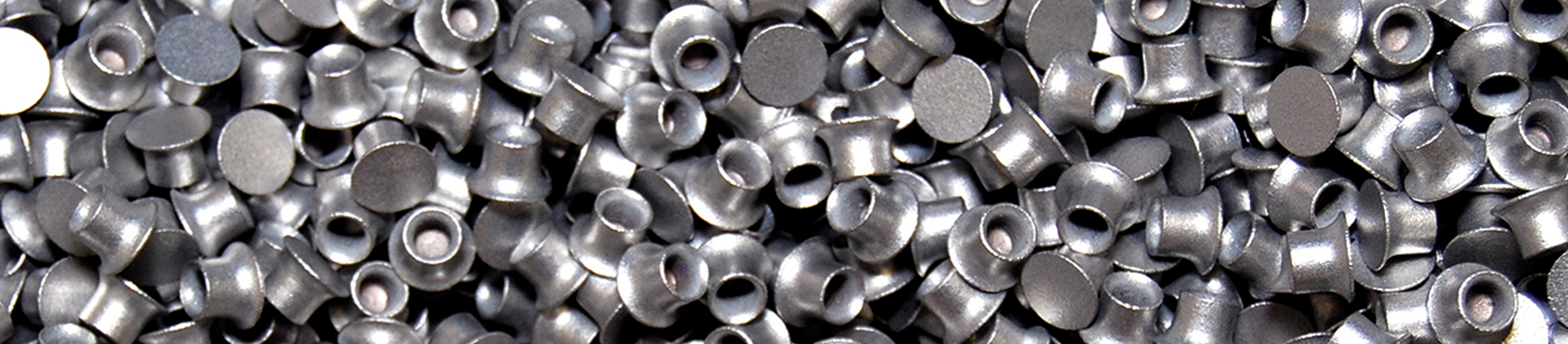
Von Engpässen zu Durchbrüchen: Die Reise von Atlas Copco zum 3D-Druck
Atlas Copco | Fallstudie
Steigerung der Produktionseffizienz
- 92 % kürzere Vorlaufzeit von 6-12 Wochen auf nur 3-4 Tage
- Einsparung von 30 % der Produktionskosten durch den Wegfall der Kosten für externe Zulieferer und die Reduzierung der Arbeitsstunden
- Reduzierung des Materialabfalls von ca. 7 % auf nahezu Null
- Verbesserte Flexibilität bei der Reaktion auf ungeplante Aufträge und dringende Kundenanforderungen
Lange Vorlaufzeiten, Unterbrechungen der Lieferkette und steigende Produktionskosten sind häufige Herausforderungen in der modernen Fertigung. Herkömmliche Methoden können oft nicht mit der wachsenden Nachfrage nach Flexibilität, Geschwindigkeit und Effizienz mithalten. Für Unternehmen, die sich auf ausgelagerte Komponenten verlassen, können Verzögerungen und Ineffizienzen zu kostspieligen Rückschlägen und verpassten Chancen führen.
Atlas Copco, ein führender Anbieter von Industrielösungen, sah sich bei der Produktion seiner Nietausgabeschale - einer wesentlichen Komponente in selbststanzenden Nietsystemen für die Automobilindustrie - mit genau diesen Herausforderungen konfrontiert. Durch die Einführung der internen additiven Fertigung (AM) konnte das Unternehmen nicht nur diese Hindernisse überwinden, sondern auch erhebliche Kosteneinsparungen erzielen, den Ausschuss reduzieren und die Vorlaufzeiten drastisch verkürzen. Durch den Einsatz der EOS P 396 und dem Polymerwerkstoff PA 2200 hat Atlas Copco seinen Produktionsansatz geändert. In dieser Fallstudie wird untersucht, wie die additive Fertigung zu messbaren Verbesserungen führte und die Fertigungsstrategie des Unternehmens umgestaltete.

"Die Zusammenarbeit mit EOS hat uns eine schlüsselfertige Lösung geliefert und uns geholfen, unsere Prozesse so anzupassen, dass wir jetzt mit mehreren Komponenten in Serienproduktion sind, schnell Hunderte von Prototypen erstellen und in nur 18 Monaten einen ROI erreicht haben."
Jason Edwards, Technischer Leiter bei Atlas Copco
Herausforderung
In der Vergangenheit war Atlas Copco bei Komponenten wie der Nietauswurfschale, einem wichtigen Teil seiner Stanznietsysteme, die in der Automobilbranche weit verbreitet sind, auf externe Lieferanten angewiesen. Diese Abhängigkeit führte zu verlängerten Vorlaufzeiten von 6 bis 12 Wochen, erhöhten Produktionskosten und einer komplizierten Lieferkette. Darüber hinaus trugen die konventionellen Herstellungsverfahren zu einem Materialabfall von etwa 7 % bei, was den Bedarf an einer nachhaltigeren Lösung deutlich machte.
"Die Zusammenarbeit mit EOS und Additive Minds hat uns eine schlüsselfertige Lösung beschert und uns geholfen, unsere Prozesse so anzupassen, dass wir jetzt mehrere Komponenten in Serie produzieren, Hunderte von Prototypen herstellen und in nur 18 Monaten einen ROI erzielen konnten", erklärt Jason Edwards, Technical Manager bei Atlas Copco.
Sortieren & Zuführen
3D-gedruckte Schale liefert effizient Nieten und rationalisiert automatisierte Fertigungsprozesse


Lösung
Um diese Herausforderungen zu meistern, arbeitete Atlas Copco mit EOS und seiner Beratungsabteilung Additive Minds zusammen, um die AM-Fähigkeiten ins Haus zu holen. Das Unternehmen entschied sich für den 3D-Drucker EOS P 396 , der für seine Flexibilität und Präzision bekannt ist, und nutzte das Polymermaterial PA 2200 für die Herstellung der Nietschale. Durch diese Umstellung konnte Atlas Copco seine Lieferkette straffen, die Abhängigkeit von Drittanbietern verringern und eine bessere Kontrolle über die Produktionszeitpläne erlangen. Der interne AM-Ansatz erleichterte auch das Rapid Prototyping und ermöglichte rasche Iterationen und Designoptimierungen.
Ergebnisse
Die Umstellung auf die hauseigene additive Fertigung hat für Atlas Copco entscheidende Ergebnisse gebracht. Eine der wichtigsten Verbesserungen war die drastische Verkürzung der Vorlaufzeiten. Zuvor benötigte die Produktion der Nietschüssel 6 bis 12 Wochen, was vor allem auf die Abhängigkeit von externen Lieferanten und die Komplexität der traditionellen Fertigungsprozesse zurückzuführen war. Mit der Einführung des 3D-Druckers EOS P 396 konnten die Vorlaufzeiten auf nur 3 bis 4 Tage reduziert werden - eine bemerkenswerte Verkürzung um 92 %. Diese Verbesserung ermöglichte eine schnellere Reaktion auf Produktionsanforderungen und eine größere Flexibilität bei der Erfüllung dringender Kundenwünsche.
Kosteneinsparungen waren ein weiteres wichtiges Ergebnis. Durch den Wegfall externer Zulieferer, die Reduzierung des Personalaufwands und die Rationalisierung des gesamten Produktionsprozesses konnte Atlas Copco die Produktionskosten um 30 % senken. Die Effizienz der additiven Fertigung minimierte die Kosten für Umrüstungen, Einrichtungsänderungen und das Management der Lieferkette. Darüber hinaus wurde durch die Präzision und Zuverlässigkeit des AM-Prozesses der Materialabfall erheblich reduziert. Während bei herkömmlichen Fertigungsmethoden etwa 7 % Materialabfall anfielen, konnte diese Zahl mit dem neuen Verfahren auf nahezu Null gesenkt werden. Diese Reduzierung trug nicht nur zur Kosteneffizienz bei, sondern unterstützte auch die Nachhaltigkeitsziele durch die Minimierung des Ressourcenverbrauchs.
Durch die Einführung der additiven Fertigung konnte Atlas Copco seine Produktionsflexibilität, Kosteneffizienz und Umweltfreundlichkeit verbessern - ein Beweis für das enorme Potenzial von AM in industriellen Anwendungen. "AM hat sich für uns als transformativ erwiesen. Wir gewinnen neue Aufträge auf der ganzen Welt, weil wir direkt, zu niedrigeren Kosten und mit kurzen Vorlaufzeiten liefern können. Mit EOS haben wir einen Partner, der uns während der gesamten Umstellung unterstützt hat, uns schnellen Support bietet und uns weiterhin bei der Konstruktion von Komponenten berät, um das beste Ergebnis mit unserem 3D-Drucker zu erzielen", fasst Jason Edwards, Technical Manager bei Atlas Copco, zusammen.
Effizient und verlässlich
Die Umstellung auf den hauseigenen 3D-Druck bedeutet, dass Atlas Copco weniger Komponenten von Drittanbietern benötigt und nicht mehr durch Lieferkettenvorlaufzeiten und Transportverzögerungen behindert wird.


"Die additive Fertigung hat für uns einen Wandel bewirkt. Wir erhalten neue Aufträge auf der ganzen Welt, weil wir direkt, zu niedrigeren Kosten und mit kurzen Vorlaufzeiten liefern können.
Jason Edwards, Technischer Leiter bei Atlas Copco
EOS-Fallstudien
Erleben Sie drei Jahrzehnte Pionierarbeit im 3D-Druck mit EOS