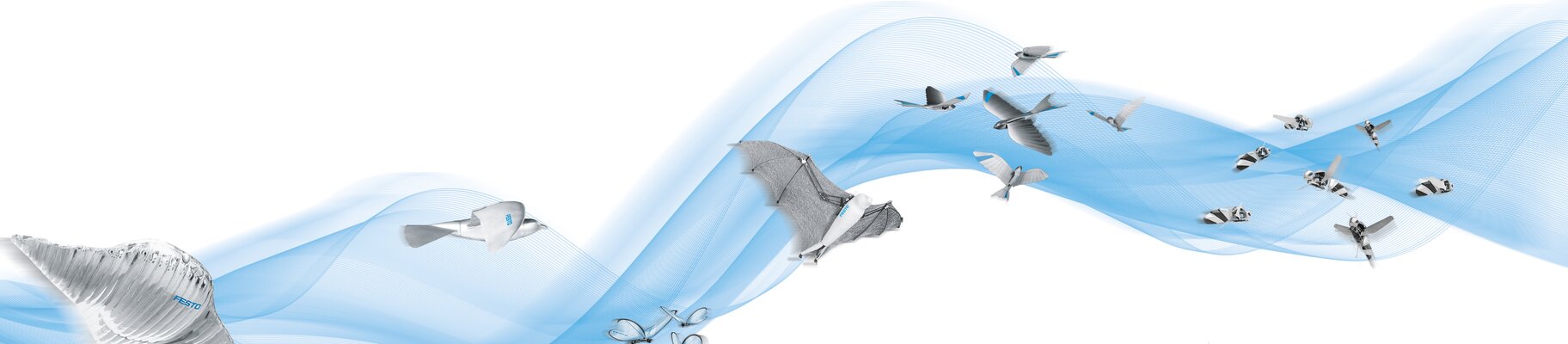
Bionische Bienendrohnen: Die Zukunft der autonomen Schwarmtechnologie nimmt Fahrt auf
Festo | Fallstudie
Pionierarbeit im Leichtflug
- 75% reduziertes Rahmengewicht auf nur 3 Gramm
- Erfolgreicher autonomer Schwarmflug mit 20 Einheiten
- Schnelle Design-Iterationen und kurze Vorlaufzeiten
- ebnete den Weg für kompliziertere Leichtbaukonstruktionen in der Zukunft
Bei anspruchsvollen Anwendungen wie Such- und Rettungseinsätzen kann die Leistung von Drohnen über Erfolg oder Misserfolg entscheiden. Leichte, autonome Systeme, die in der Lage sind, in komplexen Umgebungen präzise zu navigieren, sind sehr gefragt und stoßen an die Grenzen der Technik und der Materialwissenschaft. Was aber, wenn die Antwort auf die Suche nach neuen seriellen Möglichkeiten gar keine typische Drohne wäre?
Das ist die Bionic Bee - ein von der Natur inspiriertes Mikroflugzeug, das von Festo entworfen und mit modernster additiver Fertigung (AM) hergestellt wurde. Dieses bemerkenswerte Projekt ist nicht nur ein Vorzeigebeispiel für Biomimikry, sondern auch eine Demonstration dafür, wie fortschrittliches Design und 3D-Druck die Leichtbauweise revolutionieren. Festo entwickelte das Konzept, während 1zu1 und EOS das Fachwissen und die Technologie zur Verfügung stellten, um eine ehrgeizige Idee in die Realität umzusetzen. Das Ergebnis: ein ultraleichter, wendiger Roboterbienenschwarm, der die Möglichkeiten des autonomen Flugs neu definiert.

"Der Einsatz der FDR-Technologie war für die BionicBee ein entscheidender Schritt. Indem wir die additive Fertigung an ihre Grenzen gebracht haben, konnten wir das Gewicht unseres Rahmens von 12 Gramm auf nur 3 Gramm reduzieren - ohne Kompromisse bei der Stabilität."
Mattias-Manuel Speckle | Leiter der Abteilung Additive Manufacturing Prototyping bei Festo
Herausforderung
Die Entwicklung der BionicBee stellte eine einzigartige Herausforderung dar. Mit einer Flügelspannweite von 240 Millimetern und einem Gewicht von nur 34 Gramm galt es, eine Struktur zu entwerfen, die ein Gleichgewicht zwischen Ultraleichtbauweise, Haltbarkeit und Funktionalität herstellt. Der Körper der Biene musste einen bürstenlosen Motor, drei Servomotoren, eine Batterie, ein Getriebe und mehrere Leiterplatten aufnehmen, um eine präzise Flügelbewegung zu ermöglichen. Das Entwicklungsteam von Festo setzte auf AM, um die Struktur des Rahmens zu optimieren, aber frühe Prototypen stießen oft auf Einschränkungen in Bezug auf Robustheit oder Flexibilität. Herkömmliche Systeme zum selektiven Lasersintern (SLS) konnten die feinen, komplizierten Geometrien nicht herstellen, die der Rahmen unter realen Bedingungen aufweisen muss. Selbst kleinste Unterschiede im Materialverhalten oder Unstimmigkeiten bei der Herstellung hätten die Flugleistung beeinträchtigen können. Der enge Zeitplan erhöhte den Druck, die Ergebnisse schnell und effizient zu liefern, zusätzlich.
Lösung
Festo wandte sich an 1zu1, um Fertigungsexpertise zu erhalten, und 1zu1 wählte das EOS FORMIGA P 110 FDR, um die erforderlichen komplizierten, leichten Komponenten zu liefern. Durch die Kombination des bionischen Designansatzes von Festo mit den hochauflösenden Fähigkeiten der FORMIGA P 110 FDRentwickelte das Team einen Rahmen, der ein effektives Gleichgewicht zwischen minimaler Masse und struktureller Stärke bietet. Dieser Aufbau ermöglichte es Festo auch unter Zeitdruck, schnell zu iterieren und die filigrane Gitterstruktur der Biene zu verfeinern. Philipp Schelling, Production Manager SLS bei 1zu1, erklärt: "Die BionicBee verlangte extrem feine Merkmale und eine konstante Leistung der Teile im Flug. Die fine detail resolution (FDR) von EOS mit dem einzigartigen CO-Laser, dessen ultrafeiner Strahl nur halb so groß ist wie bei Standard-SLS-Systemen, war ideal, um diese Anforderungen zu erfüllen und die Vision von Festo zu verwirklichen."
Durch die Verwendung von PA 1101 - einem zäheren und flexibleren Polymer - wurde sichergestellt, dass die Gitterstruktur sowohl leicht als auch haltbar ist und den strengen Anforderungen des autonomen Flugs gerecht wird. Teile aus PA 1101 weisen eine hohe Schlagzähigkeit und Bruchdehnung auf und behalten konstante mechanische Eigenschaften über einen weiten Temperaturbereich. Dieser auf nachwachsenden Rohstoffen basierende Werkstoff bietet im Vergleich zu PA 12 eine überlegene Leistung, einschließlich der Fähigkeit, höchsten mechanischen Belastungen standzuhalten, ohne abzusplittern.
Festo optimierte den Rahmen mit algorithmusgesteuerter Modellierung weiter und entfernte unnötiges Material, um eine drastische Gewichtsreduzierung von 75 % zu erreichen. Das Team hat außerdem eine automatische Kalibrierungsfunktion implementiert, die die Steuerungsparameter jedes BionicBee nach einem kurzen Testflug abstimmt und so verbleibende Schwankungen im Materialverhalten ausgleicht. "Wir sahen in der BionicBee die perfekte Herausforderung, um zu zeigen, was FDR leisten kann. Dieses Projekt zeigt, wie präzise, ultradünne Strukturen, die durch das FORMIGA P 110 FDR ermöglicht werden, den Leichtbau revolutionieren können - auch bei größeren Bauteilgrößen", sagt Philipp Schelling, Produktionsleiter SLS bei 1zu1.
Durch enge Zusammenarbeit und einen agilen Produktionsprozess lieferte 1zu1 Prototypen und Komponenten innerhalb eines engen Zeitplans. Dieser kollaborative Ansatz ermöglichte es Festo, den Rahmen der BionicBee in Echtzeit zusammenzubauen und zu testen.
Ergebnisse
Die Partnerschaft zwischen Festo, 1zu1 und EOS war wegweisend für die Entwicklung, Herstellung und den Betrieb autonomer Flugobjekte. Die optimierte Gitterstruktur reduzierte das Gewicht des Rahmens, ein Schlüsselfaktor für die Verlängerung der Flugdauer und die Verbesserung der Manövrierfähigkeit. "Indem wir AM bis an die Grenzen ausreizen, konnten wir das Gewicht unseres Rahmens von 12 Gramm auf nur 3 Gramm reduzieren - ohne dabei die Stabilität zu beeinträchtigen", so Mattias-Manuel Speckle, Leiter Additive Manufacturing Prototyping bei Festo. Die Flugfähigkeiten von BionicBee wurden durch einen synchronisierten Schwarm von 20 Einheiten demonstriert, wobei fortschrittliche Lokalisierungs-, Kommunikations- und Kontrollsysteme zum Einsatz kamen. Gleichzeitig beschleunigte AM die Innovationszyklen, indem es ein schnelles Prototyping und eine On-Demand-Produktion ermöglichte, wodurch die Entwicklungszeiten erheblich verkürzt wurden. Diese erfolgreiche Zusammenarbeit ist zu einer Blaupause für künftige Leichtbauvorhaben geworden und unterstreicht den Einfluss von funktionalem Design und hochauflösendem AM auf das Erreichen eines noch nie dagewesenen Niveaus von Effizienz und Leistung.
Licht und Agilität
Die BionicBee ist das kleinste Flugobjekt aus dem Bionic Learning Network von Festo. Sie wiegt etwa 34 Gramm, ist 22 Zentimeter lang und hat eine Flügelspannweite von 24 Zentimetern.


"Die BionicBee war für uns die perfekte Herausforderung, um zu zeigen, was FDR leisten kann. Dieses Projekt unterstreicht, wie präzise, ultradünne Strukturen, die durch das FORMIGA P 110 FDR ermöglicht werden, den Leichtbau revolutionieren können - auch bei größeren Bauteilgrößen."
Philipp Schelling | Produktionsleiter SLS bei 1zu1
Natürlich & Autonom
Mit der BionicBee hat das Team von Festo ein Flugobjekt entwickelt, das in großer Zahl und völlig autonom im Schwarm fliegen kann.


EOS-Fallstudien
Erleben Sie drei Jahrzehnte Pionierarbeit im 3D-Druck mit EOS