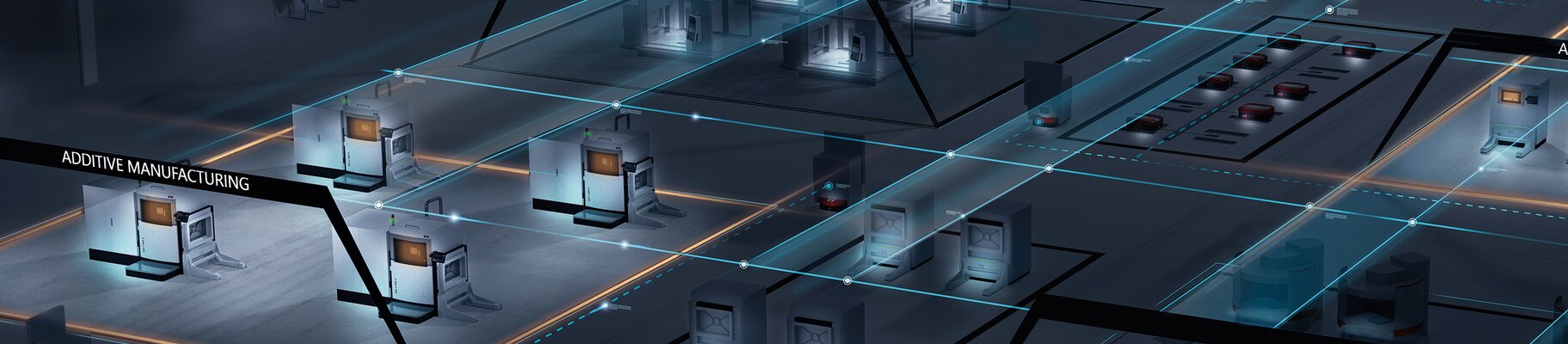
Skalieren Sie Ihre Additive Manufacturing Produktion
23. August 2021 | Lesedauer: 9 min
Wie lässt sich die Produktivität einer industriellen 3D-Druckfabrik mit minimalem Aufwand steigern und optimieren? Wir haben eine Simulationssoftware eingesetzt, um den Additive Manufacturing-Prozess und die Nachbearbeitungsschritte zu simulieren. Unser Kundenanwendungsfall macht den Skalierungsprozess leicht nachvollziehbar.
Wie erzielt man die höchste Investitionsrendite?
Die Skalierung der Additive Manufacturing (AM)-Produktion ist eine schwierige Aufgabe, da Sie mehrere Faktoren berücksichtigen müssen, bevor Sie sich für eine Skalierungsstrategie entscheiden.
Dieser Artikel richtet sich an diejenigen, die die Produktivität ihrer AM-Fabrik mit minimalem Aufwand steigern und optimieren möchten. Wir beschreiben einen konkreten Anwendungsfall eines Kunden, der den Skalierungsprozess leicht nachvollziehbar macht.
Die größte Herausforderung
Der Kunde wollte die Produktion erhöhen, indem er seine beiden vorhandenen EOS P 396 Maschinen durch drei EOS P 396 Systeme ergänzte. Das Team war sich jedoch nicht sicher, ob die vorhandenen Nachbearbeitungsmaschinen den höchsten Durchsatz mit einer Ein-Mann-Schicht bewältigen würden. Das AM-Produkt blieb das gleiche, was bedeutet, dass auch der Arbeitsablauf und die Art der Ausrüstung gleich blieben. Die größte Herausforderung bestand darin, die zusätzlichen Nachbearbeitungsgeräte und -ressourcen so zu optimieren, dass der höchste Durchsatz erzielt und gleichzeitig die Kosten pro Teil so niedrig wie möglich gehalten werden konnten.
Wir unterstützten den Kunden durch die Entwicklung eines maßgeschneiderten Produktionsmodells mit geeigneten variablen Eingangsparametern. Durch Variation dieser Eingangsparameter können verschiedene Szenarien erstellt werden, um die Empfindlichkeit des Durchsatzes und der Kosten pro Teil zu prüfen. Diese Informationen helfen dem Kunden bei der Entscheidung für das optimale Szenario mit den geringsten zusätzlichen Investitionen zur Skalierung der AM-Produktion.
Zusammenfassend lässt sich sagen, dass wir die Engpässe in der Fabrik identifiziert haben. Durch kleine Änderungen in der Nachbearbeitung konnten wir die Produktion um 24 % steigern, die Gewinnspanne um 124 % erhöhen, die Kapitalrendite (ROI) um 115 % steigern und die Kosten pro Teil (CPP) um 18 % senken.
Einsatz der Simulation zur Lösung des Problems der Produktionsoptimierung
Ein erfolgreicher Business Case für die Serienproduktion erfordert eine eingehende Analyse aller Produktionsparameter, die sich auf den Output und die Kosten auswirken. Diese Produktionsparameter stehen oft in einem nichtlinearen Verhältnis zueinander, so dass es kaum möglich ist, sie mit einer Excel-Tabelle zu optimieren. Eine Simulationssoftware hingegen berücksichtigt alle produktionsbezogenen Komplexitäten und löst das Optimierungsproblem auf einfachere Weise.
Wir bei EOS verwenden Tecnomatix Plant Simulation von Siemens und bieten unseren Kunden an, maßgeschneiderte Lösungen zu simulieren, um ein gutes Prozessverständnis für eine Make-or-Buy-Entscheidung zu erhalten.
Wir verwenden Simulationssoftware, um den AM-Prozess und die Nachbearbeitungsschritte zu simulieren. Ein erfolgreiches AM-Unternehmen muss den Nachbearbeitungsdurchsatz und die Kosten analysieren, was manchmal über Erfolg oder Misserfolg entscheidet. Die Simulation macht es einfacher, die komplexe Prozesskette zu untersuchen.
Plant Simultation ist eine diskrete Ereignissimulation, die alle geplanten Ereignisse untersucht. Dauert die Bearbeitung eines Auftrags beispielsweise 1 Stunde, berücksichtigt der Simulator die Start- und Endzeit des Auftrags. Es wird nicht simuliert, wie der Auftrag bearbeitet wird, sondern zu welchem Zeitpunkt ein Ereignis eintritt. Andere geplante Ereignisse sind die Schichtzeiten der Arbeiter, die Rüstzeit, die Wartungszeit einer Maschine, usw.
Einführung in die Fallstudie
Plant Simultation ist eine diskrete Ereignissimulation, die alle geplanten Ereignisse untersucht. Dauert die Bearbeitung eines Auftrags beispielsweise 1 Stunde, berücksichtigt der Simulator die Start- und Endzeit des Auftrags. Es wird nicht simuliert, wie der Auftrag bearbeitet wird, sondern zu welchem Zeitpunkt ein Ereignis eintritt. Andere geplante Ereignisse sind die Schichtzeiten der Arbeiter, die Rüstzeit, die Wartungszeit einer Maschine, usw.
Station zum Auspacken | x1 |
System zur Verwaltung des Pulvers | x1 |
DyeMansion Powershot C | x1 |
DyeMansion Powershot S | x1 |
DyeMansion DM60 | x2 |
UV-Behandlung | x1 |
Oberflächenbehandlung | x2 |
Trocknungsbereich | x1 |
Inspektionstisch | x1 |
Mit dem EOS P 396 kann der Kunde Aufträge drucken, die 144 Teile enthalten. Zwei EOS P 396 können 426 Aufträge pro Jahr oder 61.344 Teile pro Jahr produzieren. Der Kunde muss zusätzlich 600 Aufträge pro Jahr oder 66.400 zusätzliche Teile pro Jahr produzieren. Eine erste Berechnung zeigt, dass drei weitere EOS P 396 benötigt würden, um das Ziel zu erreichen, was eine hohe Investition für das Unternehmen bedeutet. Ziel der Produktionssimulation war es daher, herauszufinden, ob die Produktionsleistung mit der gleichen Anzahl von Nachbearbeitungsanlagen erreicht werden kann, wobei alle Produktionskomplexitäten wie Ausfälle, Wartung und Schichtmodelle zu berücksichtigen sind.
Wie wir vorgegangen sind:
Die gesamte Anlage wurde in 3 Bereiche unterteilt (siehe Abbildung 1):
- AM-Drucker
- Pulver-Management
- Nachbearbeitung
Der Kunde bevorzugt drei Regionen, um das Risiko einer Kreuzkontamination des Pulvers zu minimieren. Wir erstellten zunächst ein Simulationsmodell mit den beiden vorhandenen EOS P 396 und dann ein zweites Modell mit drei zusätzlichen EOS P 396 und den oben aufgeführten Anlagen. Der Kunde arbeitet von Montag bis Freitag in einer Ein-Mann-Schicht. Während des Analyseprozesses haben wir alle Arten von Variablen wie Verbrauchsmaterialien und Bediener für die Produktionsanlage sorgfältig angepasst.
Eine diskrete Ereignissimulation kann alle Ereignisse simulieren, die sich zu einem bestimmten Zeitpunkt ereignen. Sie berücksichtigt die Start- und Endzeit, aber nicht, was dazwischen passiert.
Nehmen wir zum Beispiel an, Sie betreten den Geldautomaten um 17:50 Uhr und verlassen ihn um 17:53 Uhr. Die Simulation zeigt ein Ereignis um 17:50 Uhr an, was der Beginn des Ereignisses ist, und springt dann auf 17:53 Uhr, was das Ende des Ereignisses ist. In der Betriebssimulation springt die Uhr von einem geplanten Ereignis zum nächsten.
Im Kontext der Fertigung ist es ein Teil, das zur Bearbeitung in eine Maschine eintritt und diese wieder verlässt, sobald der Prozess abgeschlossen ist. Bei der Bearbeitung eines Teils können verschiedene Schritte erforderlich sein (Rüstzeit, Ladezeit, Entladezeit), die alle in die Simulation einbezogen werden können. Die Simulationsstudie hilft, den Durchsatz und die Auslastung der Maschinen zu erhöhen. Sie kann auch dabei helfen, die Anzahl der Mitarbeiter, die Ausrüstung, die Maschinen und die Lagergröße zu bestimmen, um den besten Business Case zu erzielen.
Analyse und Ergebnisse der Simulation
Optimierung des AM- und Pulvermanagementbereichs
Wir begannen mit der Simulation des AM-Bereichs und des Bereichs für das Pulvermanagement, bevor wir die Nachbearbeitungsanlagen einschlossen. Das Schichtmodell wurde gegenüber dem Original wie folgt geändert:
- Schicht: 1 Schicht (8 Stunden), Montag - Freitag
- Bauzeit: 20 Stunden.
Nachdem das Modell erstellt war, bestand die erste Herausforderung darin, die optimale Anzahl von Arbeitern für diese beiden Tätigkeiten zu ermitteln. Wir haben fünf Experimente durchgeführt (Exp.) und festgestellt, dass ein Arbeiter für diese beiden Bereiche ausreicht, wie in Tabelle 1 dargestellt. Unabhängig davon, ob wir 1 oder 5 Mitarbeiter haben, bleibt der Durchsatz gleich (1.065 Aufträge pro Jahr).
Anzahl der Operatoren | Produzierte Arbeitsplätze |
---|---|
Exp 1 1 | 1065 |
Exp 2 2 | 1065 |
Exp 3 3 | 1065 |
Exp 4 4 | 1065 |
Exp 5 5 | 1065 |
Tabelle 1: Anzahl der Betreiber im Bereich AM & Powder Management und entsprechende Jahresproduktion
Als Nächstes konzentrierten wir uns auf die Optimierung der Anzahl der Pulvertransportboxen (EOS-Multi-Box, siehe Abbildung 1), mit denen ein Arbeiter das Pulver an die EOS-Maschinen verteilen kann. In zehn Iterationen haben wir festgestellt, dass sieben EOS-Multiboxen die optimale Anzahl sind, um einen Durchsatz von 1062 Aufträgen pro Jahr zu erreichen (siehe Tabelle 2). Die Produktionssteigerung durch mehr als sieben Multiboxen rechtfertigt nicht die zusätzlichen Kosten. Es gibt nur einen Gewinn von drei Aufträgen pro Jahr (von 1062 auf 1065), und die höheren Kosten, die in diesem Bericht nicht aufgeführt sind, rechtfertigen diesen geringen Produktionsgewinn nicht.
Anzahl der Multiboxen | Produzierte Arbeitsplätze |
---|---|
Exp 01 1 | 184 |
Exp 02 2 | 367 |
Exp 03 3 | 551 |
Exp 04 4 | 732 |
Exp 05 5 | 911 |
Exp 06 6 | 983 |
Exp 07 7 | 1062 |
Exp 08 8 | 1064 |
Exp 09 9 | 1064 |
Exp 10 10 | 1065 |
Tabelle 2: Anzahl der Multiboxen und der jeweiligen Aufträge
Optimierung des Post-Processing-Bereichs:
Nach der Optimierung des AM- und Pulvermanagementbereichs war der Nachbearbeitungsbereich die nächste anspruchsvolle Aufgabe. Er umfasste sieben verschiedene Prozessstationen mit zehn Schritten:
- Teilereinigung in DyeMansion* Powershot C
- Reinigung mit Ultraschall
- Oberflächenbehandlung
- Reinigung mit Ultraschall
- Trocknen
- Oberflächenbehandlung in DyeMansion* Powershot S
- UV-Behandlung
- Einfärben in DyeMansion DM60
- Oberflächenbehandlung in DyeMansion* Powershot S
- UV-Behandlung
(*DyeMansion ist Teil des EOS Ecosystems)
Außerdem gab es einige Herausforderungen in Bezug auf den Arbeitsablauf beim Kunden. Zum Beispiel sollten die Strahlstationen (Powershot S und C) unseres Partners DyeMansion nur die Hälfte der in einem Build produzierten Teile (72 von 144 Teilen) bearbeiten, also zwei Lose pro Build. Bei allen anderen Stationen wie dem DyeMansion DM60-Färbesystem, der Oberflächenveredelung, der Trocknung usw. müssen jedoch alle Aufträge bearbeitet werden, d. h. ein Los pro Bau.
Nachdem das ursprüngliche Modell um den Nachbearbeitungsbereich erweitert worden war, konzentrierten wir uns auf die Ermittlung der optimalen Anzahl von Bedienern. Ausgehend von dem AM-Optimum von 1062 Aufträgen pro Jahr haben wir fünf verschiedene Konfigurationen mit 1-5 Bedienern durchgeführt. Wie aus Tabelle 3 hervorgeht, wären für den Nachbearbeitungsbereich 4 Bediener erforderlich, um einen wesentlich höheren Durchsatz als die bisherige Anzahl der Arbeiter zu erzielen. 4 zusätzliche Arbeitsplätze rechtfertigen nicht die (hier nicht ausgewiesenen) zusätzlichen Kosten für einen zusätzlichen Mitarbeiter (848 gegenüber 849 Arbeitsplätzen).
Anzahl der Betreiber | Arbeitsplätze entstehen durch AM | Durch AM + produzierte Aufträge Nachbearbeitung |
---|---|---|
Exp 1 1 | 1062 | 228 |
Exp 2 2 | 1062 | 666 |
Exp 3 3 | 1062 | 787 |
Exp 4 4 | 1062 | 848 |
Exp 5 5 | 1062 | 849 |
Tabelle 3: Anzahl der Bediener für den Nachbearbeitungsbereich und die jeweiligen Aufgaben
Schlussfolgerung
Die Kernaussage ist, dass die Skalierung und Optimierung Ihrer AM-Produktionsstrategie eine komplizierte Aufgabe sein kann. Es handelt sich um eine einzigartige Herausforderung, die auf ein bestimmtes Layout mit unterschiedlichen Schlüsselparametern für jedes Szenario zugeschnitten ist. Wenn Sie Ihre Strategie nicht analysieren und berücksichtigen, kann dies zu falschen Schlussfolgerungen führen. Mit unserer Simulationskompetenz und 30 Jahren AM-Erfahrung können wir für Sie eine erfolgreiche Skalierungsstrategie entwickeln, um die höchste Maschinenauslastung und die niedrigsten Kosten pro Teil zu erreichen.