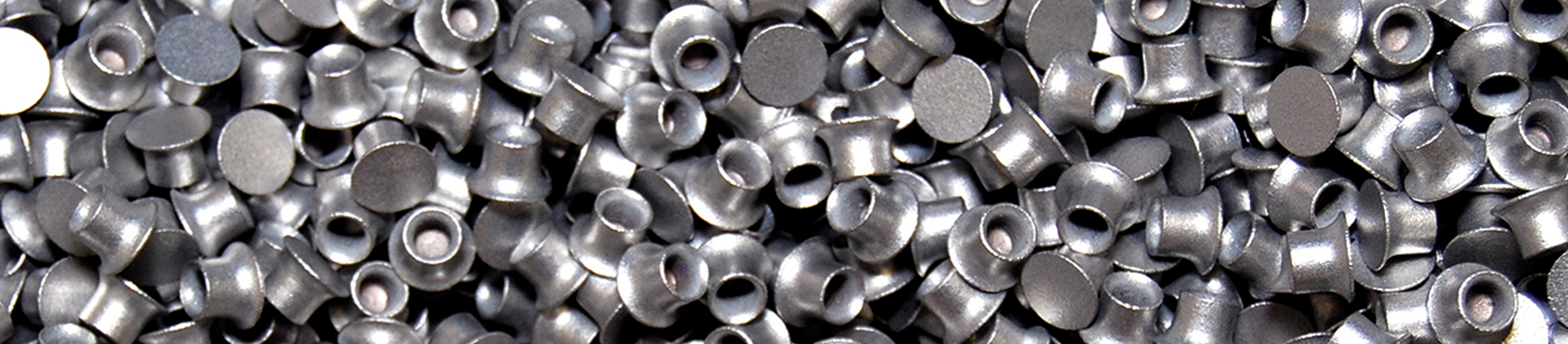
从瓶颈到突破:阿特拉斯-科普柯的3D 打印之旅
阿特拉斯-科普柯 | 案例研究
提高生产效率
- 92 %的交付周期从 6-12 周缩短至 3-4 天
- 由于取消了外部供应商费用并减少了工时,生产成本节省了 30
- 材料浪费从约 7% 减少到接近零
- 提高应对计划外订单和客户紧急要求的灵活性
交货时间长、供应链中断和生产成本上升是现代制造业面临的共同挑战。传统方法往往难以满足对灵活性、速度和效率不断增长的需求。对于依赖外包部件的公司来说,延误和低效可能导致代价高昂的挫折和机会的丧失。
作为工业解决方案的领导者,阿特拉斯-科普柯在生产铆钉输送碗时面临着这些挑战,铆钉输送碗是汽车行业使用的自冲铆接系统中的重要部件。通过采用内部增材制造 (AM),该公司不仅克服了这些障碍,还节省了大量成本,减少了浪费,并大大缩短了交货时间。使用 EOS P 396和PA 2200聚合物材料,阿特拉斯-科普柯改变了生产方式。本案例研究探讨了增材制造 如何实现可衡量的改进并重塑其制造战略。

"与 EOS 的合作为我们提供了交钥匙解决方案,并帮助我们调整了工艺流程,使我们现在能够批量生产多个组件,并正在快速制作数百个组件的原型,在短短 18 个月内就实现了投资回报"。
Jason Edwards,阿特拉斯-科普柯技术经理
挑战
传统上,阿特拉斯-科普柯依靠外部供应商提供铆钉输送碗等部件,而铆钉输送碗是汽车行业广泛使用的自冲铆接系统的关键部件。这种依赖导致交付周期延长至 6 至 12 周、生产成本增加以及供应链复杂化。此外,传统的生产工艺造成了约 7% 的材料浪费,凸显了对更具可持续性的解决方案的需求。
阿特拉斯-科普柯的技术经理 Jason Edwards 解释说:"我们希望更严格地控制生产,从而缩短交付周期,降低成本,并能够快速制作新产品的原型,"他解释说,"与 EOS 和 Additive Minds 的合作为我们提供了交钥匙解决方案,并帮助我们调整工艺,使我们现在能够批量生产多个组件,快速制作数百个新产品的原型,并在短短 18 个月内实现投资回报。
分类和进料
3D 打印 碗可有效输送铆钉,简化自动化生产流程


解决方案
为了应对这些挑战,阿特拉斯-科普柯与 EOS 及其咨询部门 Additive Minds 合作,将 AM 功能引入公司内部。他们选择了以灵活性和精度著称的EOS P 396 3D 打印机,并使用聚合物材料 PA 2200 制造铆钉输送碗。这一转变使阿特拉斯-科普柯能够精简供应链,减少对第三方供应商的依赖,并更严格地控制生产计划。内部 AM 方法还促进了快速原型制造,从而实现了快速迭代和设计优化。
成果
向内部增材制造 的转变为阿特拉斯-科普柯带来了变革性的成果。其中最重要的改进之一是大大缩短了交货时间。以前,铆钉输送碗的生产需要 6 到 12 周的时间,这主要是由于对外部供应商的依赖和传统制造工艺的复杂性造成的。使用EOS P 396 3D 打印机后,交货时间缩短至 3 至 4 天,显著缩短了 92%。这一改进可以更快地响应生产需求,并更灵活地满足客户的紧急要求。
节约成本是另一项重要成果。阿特拉斯-科普柯通过消除对外部供应商的需求、减少工时以及简化整体生产流程,使生产成本降低了 30%。增材制造 的效率最大限度地降低了与换装、设置更改和供应链管理相关的费用。此外,AM 工艺的精确性和可靠性大大减少了材料浪费。传统制造方法会造成约 7% 的材料浪费,而新工艺则将这一数字降至近乎零。这种减少不仅有助于提高成本效益,还通过最大限度地减少资源消耗支持了可持续发展目标。
通过采用增材制造,阿特拉斯-科普柯提高了生产的灵活性、成本效率和环境效益--证明了 AM 在工业应用中的强大潜力。"AM对我们来说是一个变革。我们在全球范围内赢得了新的合同,因为我们可以直接供货,成本更低,交货时间更短。阿特拉斯-科普柯的技术经理 Jason Edwards 总结说:"EOS 是我们的合作伙伴,它在我们的转型过程中一直支持我们,为我们提供快速支持,并不断为我们的部件设计提供建议,使我们的3D 打印机达到最佳效果。
高效可靠
转向内部3D 打印 意味着阿特拉斯-科普柯需要更少的第三方组件,不再受供应链交货时间和运输延误的限制。


增材制造 为我们带来了变革。我们在全球各地赢得了新合同,因为我们可以直接供货,成本更低,交货时间更短。
Jason Edwards,阿特拉斯-科普柯技术经理
EOS 案例研究
通过 EOS 探索三十年来开拓3D 打印 的卓越成就