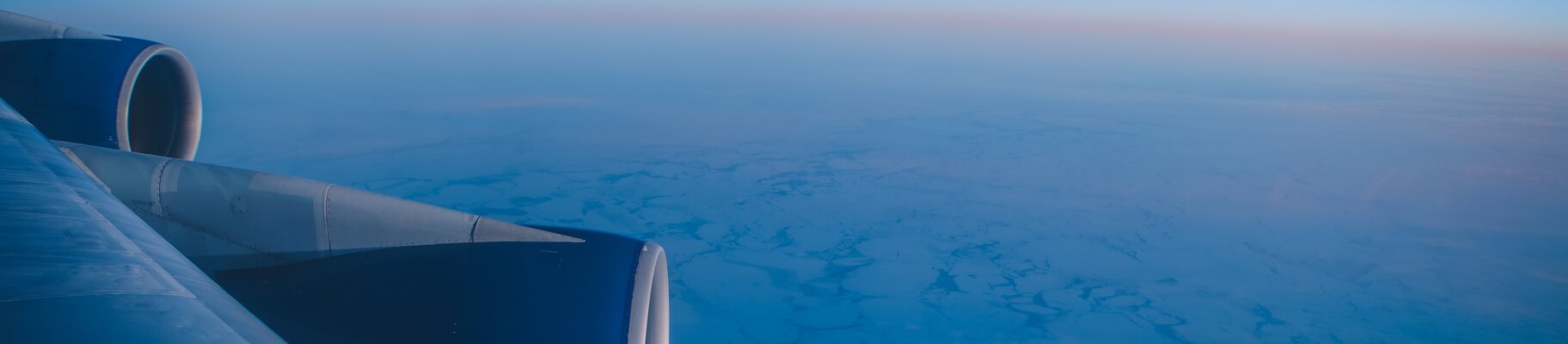
航空工业中的 3D 打印
高效、可持续地生产高科技部件
增材制造发动机、涡轮机部件等
想要以经济高效的方式尽快制造出具有复杂几何形状和明确空气动力学特性的功能部件?难以想象?不是。
发动机和涡轮部件以及机舱内饰部件就是工业3D 打印可以实现的典型例子。
功能集成、日益复杂的设计及其零部件的开发是航空航天业的主要驱动力。节约材料、减轻重量、减少燃料消耗和二氧化碳排放。如今,这些课题比以往任何时候都更加重要。因此,领先的航空航天公司在规划未来生产战略时,早已将增材制造 技术融入其中。
在与航空航天领域领先企业的密切合作下,我们完成并伴随着许多不同的成功案例。
我们的附加值体现在始终如一的解决方案上:从提供和实施 3D 打印系统,到针对材料、系统、部件或完整组件的合格工艺提供个性化咨询和支持。这种深入的合作正在提升行业的创新实力。一些主要的市场参与者正计划在未来几年内对飞机内饰的重要部分采用增材制造技术。
一览
3D 打印在航空领域的优势
-
减轻重量
工业 3D 打印可以制造非常坚固的轻质结构,使重量减轻约 40-60%。其效果是:更精简的成本结构、节省材料和降低油耗。 -
功能集成
该工艺可将最大功能集成到尽可能少的部件中。其优点是:降低了组装和质量保证成本,并消除了与许多不同部件组装相关的漏洞。 -
更灵活的生产规划
无工具生产工艺可以更快地调整产品。通过按需生产,无需延长交付周期,可大大减少备件存储量。在飞机较长的生命周期内,成本优势非常明显。 -
符合行业标准的材料和强度
EOS 系统为航空航天业加工专用材料。3D 打印部件符合行业特定要求,达到航空航天业常用的各种安全相关危险等级。 -
复杂零件
工业 3D 打印可实现广泛的设计优化--从零件定制和升级到只有增材制造才能实现的独家创新。 -
降低二氧化碳排放量
更高效的发动机、涡轮机和轻质内饰件可减少飞机的燃料消耗,从而降低二氧化碳排放量。 -
显著降低成本
增材制造是一种无需工具的工艺。这意味着与传统制造工艺相比,可以大大节约成本。
利用工业 3D 打印制造航空发动机部件
建造发动机和涡轮机意味着要应对各种挑战,如优化体积、性能和环保性。在这些领域,3D 打印可以做出重大贡献。它可以生产出具有复杂几何形状、明确空气动力学和流体动力学特性的发动机,以及单个零件重量最多可减轻 60% 的轻质结构。使用 3D 打印加工超级合金也更具成本效益,因为材料使用率更低。其结果是:在飞机的整个使用寿命期间,环境污染大大减少。由单件制成的部件也更有弹性,不易损坏。
航空领域的 EOS 技术
客户感言
空客 A350 飞机舱门的锁定轴
空中客车公司是全球航空航天工业和相关服务业的领导者。EOS 的 3D 打印技术帮助空中客车公司制造出成本和资源效率更高的飞机。增材制造飞机舱门锁轴取得了显著成果:
- 增材制造制造的部件重量减轻 45%,但坚固性保持不变
- 通过减少材料用量和装配时间,可节约 25% 的生产成本
- 部件数量从 10 个减少到 1 个
- 在一架 A350 飞机上安装 16 个门轴,重量减轻超过 4 千克
该组件由 EOS 系统EOS M 400-4 上的钛金属制成。

利用 EOS 系统批量生产空客发动机部件
德国领先的发动机制造商 MTU 航空发动机公司对其 EOS 机器进行了优化,以批量生产安全、经济的零件。利用增材制造,MTU 为空客 A320neo 新一代静洁动力® PW1100G-JM 发动机的齿轮涡轮风扇制造孔镜凸台。A320neo 涡轮风扇的低压涡轮是首个默认配备增材制造 内膛镜凸缘的涡轮。EOS 技术的成本优势是生产和开发的决定性因素之一。

航空质量保证
对审批的高安全要求是航空领域的一大挑战。从原材料到最终产品,每个飞行部件都必须受到持续监控,不能有任何缺陷。
MTU 航空发动机公司与 EOS 合作开发了一种用于制造过程的光学断层扫描技术,并将其应用于名为 EOSTATE Exposure OT 的系列产品中。通过可设置参数的软件,可以对各层零件的质量得出详细结论。通过这种方式,光学层析成像技术可以验证可重复性,提高零件、构建工作和打印系统之间的可比性,并为批量生产应用中的成本效益质量保证创造适当的条件。

-
快速:大大缩短开发、制造和交付时间
-
灵活:设计自由度极高
-
成本效益高:材料和工具用量少,大大降低了开发和制造成本
-
EOS 系统支持全面的质量保证,包括在线监测和光学断层扫描。
利用工业 3D 打印技术制造组件和结构件
降低成本驱动因素--这是为航空业更高效地制造结构件的关键因素。数字化制造流程提供了广泛的机会。借助增材制造,可以将多个零件组合成一个部件,从而省去装配等生产步骤。目前占用大量资金的备件存储过程也将被淘汰。只有在需要部件时才进行生产,而不需要任何前期工序。此外,增材制造结构部件相对较轻,有助于平衡飞机的二氧化碳排放量。

利勃海尔
空客 A380 主飞行控制装置部件
利勃海尔航空航天公司是航空工业系统的领先供应商。公司拥有五十多年的经验,开发、制造和维护各种飞机仪器,包括飞行控制和执行系统、起落架、空气管理系统和齿轮箱。
利勃海尔利用其金属 3D 打印机EOS M 400-4,为空客 A380 生产了创新型高压液压阀块。新型增材制造阀块的性能与传统部件相同,但重量更轻,单个部件数量更少。该部件由钛合金制成,满足飞行操作所需的所有认证要求。
- -重量减轻 35
- -10 个独立部件的功能集成
快速制造的内饰和飞机配件
聚合物增材制造技术在车厢内饰方面变得越来越重要。原因有以下几点:在这种环境下,高度定制化和灵活的免工具生产至关重要。车厢内使用的材料也必须满足非常严格的要求,例如在易燃性方面。技术必须能够加工这些材料,尤其是在需要扭曲绞合等复杂设计时。最后,还需要有一个连贯的制造过程,并尽量减少复杂的后处理,以及数字化备件战略和数字化备件,并有虚拟库存。聚合物工业 3D 打印技术符合所有这些标准。

阿提哈德工程公司
未来的飞机客舱
阿提哈德工程公司是中东地区最大的飞机维护、修理和运营 (MRO) 服务提供商。作为阿提哈德航空集团的子公司,该公司在阿布扎比国际机场的现代化设施内提供全天候的维护服务,包括设计、复合材料维修、客舱改装和部件相关服务。
"阿提哈德与 EOS 携手开设了中东地区首家 3D 打印制造工厂,该工厂获得了欧洲航空安全局(EASA)的批准,可以设计和制造飞机零部件"。
EOS P 396 系统可使用PA 2241 FR等聚合物材料制造部件,因此可用于制造在飞机检查过程(即 C 检查)中更换的机舱部件。在飞机定期停机(航线维护)期间进行维护时,还可以通过制造所需的部件来快速弥补缺陷。
"阿提哈德航空和 EOS 以高质量的解决方案和技术创新而闻名,双方拥有相同的理念:"EOS 欧洲、中东和非洲地区高级副总裁 Markus Glasser 表示:"我们希望共同将飞机内饰部件的设计和生产提升到一个新的水平。"快速成型制造的机舱内饰件具有显著的附加值,这得益于简化的维修、轻质的设计、更短的交付周期和灵活的定制选项。这解决了航空航天业的一些关键挑战"。
欧洲、中东和非洲地区高级副总裁 | EOS GmbH

航空工业中的 3D 打印
我们的增材制造解决方案和客户案例