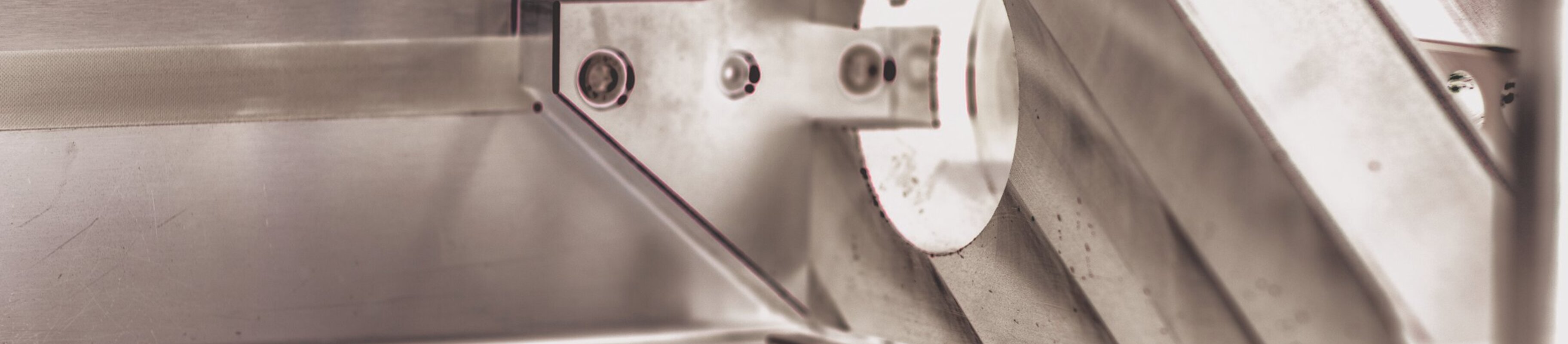
금속 적층 제조 리코터가 빌드 품질에 미치는 영향
2022년 7월 27일 | 읽기 시간: 4 분
금속 3D 프린팅 작업을 위한 적층 제조 리코터 블레이드를 선택하는 것은 어려운 결정처럼 보일 수 있지만, 꼭 그럴 필요는 없다고 한다면 어떨까요? 저희 연구팀은 적층 제조 리코터와 파우더 조합이 제작 품질에 어떤 영향을 미치는지 더 잘 이해하기 위해 다양한 실험을 해왔습니다.
리코터 재질에는 어떤 것이 있나요?
리코터 칼날에는 여러 종류가 있으며, 각각 다른 재질로 만들어지고 다른 용도로 사용됩니다. 하지만 일반적으로 소프트와 하드의 두 가지 카테고리로 구분할 수 있습니다.
소프트 리코터 블레이드에는 엘라스토머 립 또는 카본 브러시가 있으며 일반적으로 완성된 부품에 더 세밀한 디테일이 필요한 더 섬세한 프로젝트에 사용됩니다. 이러한 종류의 리코터는 불완전한 부분을 구부릴 수 있어 리코터 걸림으로 인한 작업 중단의 위험을 줄일 수 있지만, 부품이 덜 깔끔하게 마감될 수 있습니다. 소프트 리코터는 표면적이 넓은 고종횡비 부품에도 효과적입니다.
하드 리코터 블레이드는 고속 강철(HSS) 또는 자성 금속 분말 제작에 이상적인 산화 지르코늄 세라믹 블레이드로 제작할 수 있습니다. 하드 리코터는 재료 및 공정 개발을 개선하면서 더 높은 수준의 파트 품질과 반복성을 제공하기 때문에 EOS 3D 프린터에 선호되는 선택입니다. 하드 리코터는 블레이드가 소프트 리코터만큼 관대하지 않기 때문에 잼이 발생할 가능성이 높지만, 미세한 구조물을 제작해야 하는 경우 하드 리코터가 최선의 선택은 아닙니다.
적층 제조 리코터 테스트
적층 제조 리코터와 금속 파우더의 다양한 조합이 빌드의 최종 품질에 어떤 영향을 미치는지 알아보기 위해 세 가지 리코터와 세 가지 프린트 재료를 선택하여 일련의 비교 테스트를 진행했습니다.
선택한 세 가지 금속은 EOS Aluminium AlSi10Mg, EOS Titanium Ti64, EOS MaragingSteel MS1입니다. 널리 사용되는 이 세 가지 금속 분말을 선택한 이유는 각각의 특성이 다르기 때문입니다. 알루미늄 파우더는 항공우주 및 모빌리티 분야에서 자주 사용되는 경량 합금이며, 티타늄은 다양한 산업, 특히 의료용 임플란트 생산에 사용되는 훨씬 더 밀도가 높고 견고한 소재입니다. 스틸 파우더는 툴링 생산에 자주 사용되는 자성 소재입니다. 실험과 관련하여 이러한 파우더의 주요 차별화 요소는 다양한 밀도와 파우더 입자 분포이며, 이를 통해 다양한 리코터가 다양한 파우더 유형에 어떤 영향을 미치는지 관찰할 수 있습니다.
각 금속은 실리콘 립과 카본 브러시라는 동일한 소프트 리코터로 테스트했습니다. 자성 특성으로 인해 스틸 파우더는 세라믹 하드 블레이드로 테스트했고, 나머지 두 금속은 HSS 리코터와 함께 테스트했습니다.
다양한 표준화된 빌드를 배치하여 각 빌드를 직접 비교할 수 있도록 했습니다. 첫 번째 작업 레이아웃에는 다양한 방향의 원통과 정육면체와 같은 일련의 간단한 모양을 배치했습니다. 이 작업은 각 리코터-파우더 조합에 대해 한 번씩, 그리고 표준 '컨트롤' 버전으로 총 7번 실행되었습니다.
두 번째 작업은 미세한 디테일 인쇄를 위해 엘라스토머 블레이드를 테스트하기 위해 특별히 설계되었습니다. 이 작업의 부품에는 격자 공과 격자 내부 구조의 체스 루크가 추가되어 리코터의 기능을 실제로 시험해 보았습니다. 이 두 번째 작업에서는 파트를 완성한 후 손상된 블레이드가 파우더 베드에 어떤 영향을 미치는지 관찰할 수 있도록 빌드 플랫폼의 절반을 일부러 비워두었습니다.
무엇을 찾았나요?
간단히 말해, 어떤 금속 분말을 사용하든 각 리코터 간에 실질적인 차이는 발견되지 않았습니다. 생산된 부품 사이에 전혀 차이가 없었다는 것이 아니라 특정 파우더에 어떤 리코터를 사용하든 눈에 띄는 차이가 발생하지 않았다는 의미입니다. 예를 들어 티타늄 파우더로 프린팅하는 동안 각 리코터를 사용했을 때 제작된 모든 부품은 상당히 일관적이었습니다.
각 빌드에 대해 세 가지 주요 사항을 평가하여 차이가 발생할 수 있는 부분을 확인했습니다. 첫째, 리코터 블레이드 성능을 살펴보고 어떤 리코터-파우더 조합이 더 걸리기 쉬운지 확인했습니다. 둘째, 완성된 부품의 전반적인 품질, 즉 제작 부품의 기계적 특성과 다공성 등 다른 부품과 차별화된 점이 있는지 조사했습니다. 셋째, 빌드 후 파우더 베드를 분석하여 다양한 밀도의 파우더가 선택한 리코터에 다르게 반응할 수 있는 파우더 '뭉침' 등 빌드 재료에 장애가 있는지 확인했습니다.
모든 리코터-파우더 조합에서 프린터 성능, 제작 품질 및 파우더 베드 무결성이 모두 '양호한 제작'을 위한 필수 매개 변수 내에 있는 것으로 나타났습니다. 몇 가지 아주 사소한 불일치가 발견되었는데, 이는 재료 로트의 변경 때문일 수 있다는 가설을 세웠습니다.
무엇을 배웠나요?
이 연구를 통해 제작 품질 관점에서 볼 때 금속 파우더와 리코터의 조합은 중요하지 않다는 사실을 확인했습니다. 중요한 것은 제작하는 파트의 의도된 목적입니다. 테스트한 각 금속 파우더와 리코터는 다양한 실제 응용 분야에서 이점을 제공합니다. 올바른 부품에 적합한 금속을 사용하는 것이 가장 중요한 목표이며, 부품이 최상의 성능을 발휘할 수 있는 리코터를 사용하는 것은 그 다음 단계입니다.
발견된 작은 결함에서 3D 프린터의 파우더와 리코터 변경으로 인한 잠재적 오염이 한 작업에서 다음 작업으로 제작되는 부품의 성능에 어떤 영향을 미칠 수 있는지 연구를 계속하고 싶습니다. 이것이 바로 다음 연구 단계의 초점이 될 것입니다: 부품과 파우더 베드에 대한 화학 분석을 수행하여 오염이 있는지 확인하고, 이것이 다양한 리코터-파우더 조합을 사용하여 제작된 부품의 장기적인 실제 적용에 영향을 미치는지 여부를 확인합니다.
백서를 다운로드하여 다양한 금속 리코터-파우더 조합의 제작 품질에 대한 자세한 연구 내용을 알아보세요.