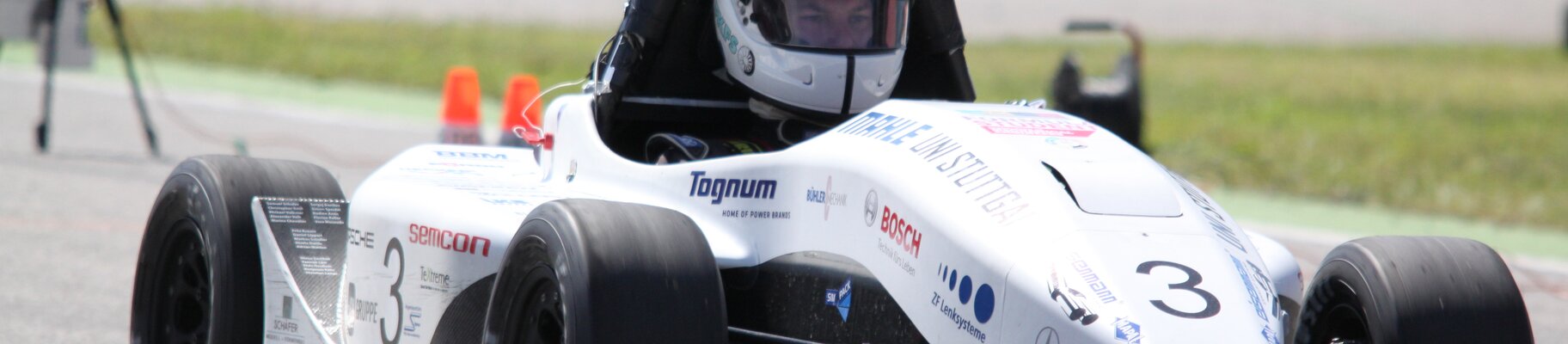
De jeunes ingénieurs choisissent la fabrication additive pour exploiter tout le potentiel de la pièce
Rennteam Uni Stuttgart | Histoire d'une réussite
-
Réduction significative des délais de développement et de production
-
Fiabilité sur la piste grâce à une rigidité accrue de 20 %.
-
Une forme et un contour parfaits pour un poids réduit de 35 %.
"Nous sommes ravis d'avoir pu apporter le titre de Formula Student Germany 2012 à Stuttgart. La liberté du processus de construction offerte par la technologie DMLS d'EOS a joué un rôle important dans notre succès."
Yannick Löw | Rennteam Uni Stuttgart
La victoire en douceur - La Rennteam Uni Stuttgart remporte la Formula Student Germany avec l'aide d'EOS
D'une part, tout constructeur d'un pivot d'essieu a pour mission de développer une pièce présentant la plus grande stabilité possible, faute de quoi la sécurité du véhicule dans son ensemble serait compromise. D'autre part, les supports de roue ne peuvent pas, pour plusieurs raisons, peser trop lourd.
Dès la phase de conception, les ingénieurs ont utilisé le logiciel de CAO d'EOS partners Within Technologies Ltd. Grâce à cet outil, les constructeurs ont pu adapter parfaitement la pièce aux exigences structurelles. Ils ont ainsi pu conférer à la charnière les propriétés physiques requises - légèreté et rigidité.
D'une part, la fabrication additive élimine la nécessité de construire des négatifs ou des moules. En outre, l'ensemble du processus, de la conception à la fabrication, est plus précis, ce qui signifie qu'il n'est souvent pas nécessaire de retravailler ou d'affiner la pièce. La pièce était presque immédiatement prête pour la course.
Le poids de la pièce a été réduit de 660 grammes, ce qui a permis à la Rennteam Uni Stuttgart d'économiser 35 %. Dans le même temps, les ingénieurs ont réussi à augmenter la rigidité de 20 % - des chiffres importants pour le sport automobile, qui se traduisent par des temps au tour plus rapides et une consommation de carburant réduite.

"Nous avons produit la pièce en utilisant le processus classique de moulage de précision. Cela a bien sûr conduit à des limitations de la liberté de forme, ce qui signifie que le potentiel de la pièce n'a jamais pu être pleinement exploité. Dès cette époque, nous avions décidé que pour la saison 2012, nous étudierions de nouvelles méthodes innovantes de fabrication de la fusée d'essieu de direction.
Yannick Löw | Rennteam Uni Stuttgart
Les résultats en un coup d'œil
- 20 % Rigidité accrue
- -660 g Réduction du poids
Les succès d'EOS
Découvrez trois décennies d'excellence en matière d'impression 3D avec EOS