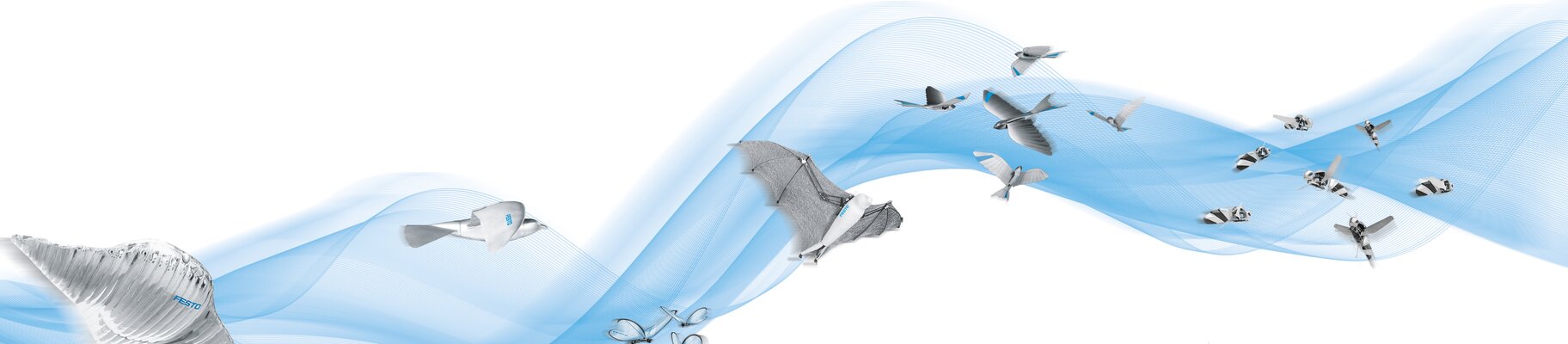
Drones abeilles bioniques : L'avenir de la technologie des essaims autonomes prend son envol
Festo - Étude de cas
Les pionniers du vol léger
- Le poids du cadre a été réduit de 75 % à seulement 3 grammes
- Vol en essaim autonome réussi avec 20 unités
- Itérations de conception rapides et délais d'exécution courts
- A ouvert la voie à des conceptions légères plus complexes à l'avenir
Dans des applications à fort enjeu comme la recherche et le sauvetage, les performances des drones peuvent faire la différence entre le succès et l'échec. Les systèmes légers et autonomes capables de naviguer avec précision dans des environnements complexes sont très demandés et repoussent les limites de l'ingénierie et de la science des matériaux. Mais que se passerait-il si la réponse à la quête de nouvelles possibilités sérielles n'était pas du tout un drone classique ?
Voici l'abeille bionique, un micro-avion inspiré par la nature, conçu par Festo et réalisé grâce à la fabrication additiveFA de pointe. Ce projet remarquable n'est pas seulement une vitrine du biomimétisme ; c'est une démonstration de la façon dont la conception avancée et l'impression 3D révolutionnent le vol léger. Festo a développé le concept, tandis que 1zu1 et EOS ont fourni l'expertise et la technologie nécessaires pour transformer une idée ambitieuse en réalité. Le résultat : un essaim d'abeilles robotisées ultralégères et agiles qui redéfinit les possibilités de vol autonome.

"L'utilisation de la technologie FDR a changé la donne pour le BionicBee. En poussant la fabrication additive à ses limites, nous avons pu réduire le poids de notre cadre de 12 grammes à seulement 3 grammes, sans compromettre la stabilité."
Mattias-Manuel Speckle - Responsable de la fabrication additive de prototypes chez Festo
Défi
La création du BionicBee a représenté un défi unique. Avec une envergure de 240 millimètres et un poids de seulement 34 grammes, l'objectif était de concevoir une structure qui concilie construction ultra-légère, durabilité et fonctionnalité. Le corps de l'abeille devait abriter un moteur sans balais, trois servomoteurs, une batterie, une boîte de vitesses et plusieurs circuits imprimés pour permettre un mouvement précis des ailes. L'équipe de développement de Festo a adopté la FA pour optimiser la structure du cadre, mais les premiers prototypes se sont souvent heurtés à des limites en termes de robustesse ou de flexibilité. Les systèmes conventionnels de frittage sélectif par laser (SLS) ne pouvaient pas produire les géométries fines et complexes nécessaires pour que le châssis fonctionne dans des conditions réelles. Les moindres différences dans le comportement des matériaux ou les incohérences de fabrication auraient pu affecter les performances de vol. En outre, les délais serrés ont ajouté une pression supplémentaire pour obtenir des résultats rapides et efficaces.
Solution
Festo a fait appel à 1zu1 pour son expertise en matière de production, et 1zu1 a choisi le système EOS FORMIGA P 110 FDR pour fournir les composants complexes et légers requis. En associant l'approche de conception bionique de Festo aux capacités de haute résolution de la FORMIGA P 110 FDR, l'équipe a mis au point un cadre qui concilie efficacement masse minimale et résistance structurelle. Cette configuration a également permis à Festo de procéder à des itérations rapides et d'affiner la délicate structure en treillis de l'abeille, même en cas de contraintes de temps. Comme l'explique Philipp Schelling, responsable de la production SLS chez 1zu1, "Le BionicBee exigeait des caractéristiques extrêmement fines et une performance constante des pièces en vol. La technologie de fine detail resolution (FDR) d'EOS avec le laser CO unique en son genre, dont le faisceau ultrafin est deux fois plus petit que celui des systèmes SLS standard, était idéale pour répondre à ces exigences et donner vie à la vision de Festo."
L'utilisation du PA 1101 - un polymère plus résistant et plus souple - a permis de garantir que la structure en treillis était à la fois légère et durable, et qu'elle répondait aux exigences rigoureuses des vols autonomes. Les pièces en PA 1101 présentent une résistance élevée aux chocs et à la rupture, et conservent des propriétés mécaniques constantes sur une large plage de températures. Ce matériau issu de ressources renouvelables offre des performances supérieures à celles du PA 12, notamment la capacité de supporter les charges mécaniques les plus élevées sans éclater.
Festo a encore optimisé le cadre à l'aide d'une modélisation pilotée par algorithme, en supprimant les matériaux inutiles pour obtenir une réduction de poids spectaculaire de 75 %. L'équipe a également mis en œuvre une fonction d'étalonnage automatique qui règle les paramètres du contrôleur de chaque BionicBee après un court vol d'essai, atténuant ainsi toute variation résiduelle dans le comportement des matériaux. "Nous avons considéré le BionicBee comme le défi parfait pour montrer ce que la FDR peut faire. Ce projet montre comment les structures précises et ultra-minces rendues possibles par le système FORMIGA P 110 FDR peuvent révolutionner la conception de pièces légères, même de grande taille ", explique Philipp Schelling, responsable de la production SLS chez 1zu1.
Grâce à une étroite collaboration et à un processus de production agile, 1zu1 a livré des prototypes et des composants dans un délai serré. Cette approche collaborative a permis à Festo d'assembler et de tester le cadre du BionicBee en temps réel.
Résultats
Le partenariat entre Festo, 1zu1 et EOS a ouvert de nouvelles perspectives en matière de conception, de fabrication et d'exploitation d'objets volants autonomes. La structure en treillis optimisée a permis de réduire le poids du cadre, un facteur clé pour allonger la durée du vol et améliorer la manœuvrabilité. "En poussant la FA à ses limites, nous avons pu réduire le poids de notre cadre de 12 grammes à seulement 3 grammes, sans compromettre la stabilité", a déclaré Mattias-Manuel Speckle, responsable du prototypage par fabrication additive chez Festo. Les capacités de vol de BionicBee ont été démontrées par un essaim synchronisé de 20 unités, mettant en évidence des systèmes avancés de localisation, de communication et de contrôle. Parallèlement, la FA a accéléré les cycles d'innovation en permettant un prototypage rapide et une production à la demande, réduisant ainsi considérablement les délais de développement. Cette collaboration fructueuse est devenue un modèle pour les futures entreprises légères, soulignant l'impact de la conception fonctionnelle et de la FA à haute résolution sur l'obtention de niveaux d'efficacité et de performance sans précédent.
Lumière & Agil
Le BionicBee est le plus petit objet volant du réseau d'apprentissage bionique de Festo. Il pèse environ 34 grammes, mesure 22 centimètres de long et a une envergure de 24 centimètres.


"Nous avons considéré le BionicBee comme le défi idéal pour montrer ce que le système FDR peut faire. Ce projet montre comment les structures précises et ultra-minces rendues possibles par le système FORMIGA P 110 FDR peuvent révolutionner la conception de produits légers, même pour des pièces de grande taille".
Philipp Schelling | Directeur de production SLS chez 1zu1
Naturel et autonome
Avec le BionicBee, l'équipe de Festo a mis au point un objet volant capable de voler en grand nombre et de manière totalement autonome au sein d'un essaim.


Études de cas EOS
Découvrez trois décennies d'excellence en matière d'impression 3D avec EOS