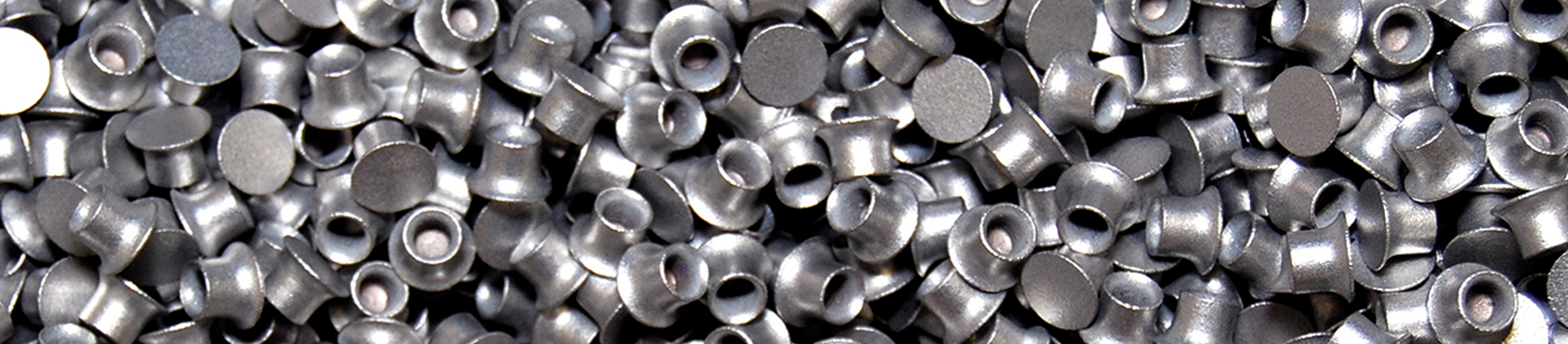
Des goulets d'étranglement aux percées : Le parcours d'Atlas Copco en matière d'impression 3D
Atlas Copco - Étude de cas
Améliorer l'efficacité de la production
- Réduction de 92 % des délais d'exécution, qui passent de 6-12 semaines à seulement 3-4 jours
- 30 % d'économies sur les coûts de production grâce à l'élimination des dépenses liées aux fournisseurs externes et à la réduction des heures de travail
- Réduction des déchets de matériaux d'environ 7 % à près de zéro
- Une plus grande agilité pour répondre aux commandes non planifiées et aux besoins urgents des clients
Les longs délais d'exécution, les perturbations de la chaîne d'approvisionnement et l'augmentation des coûts de production sont des défis courants de la fabrication moderne. Les méthodes traditionnelles ont souvent du mal à répondre à la demande croissante de flexibilité, de rapidité et d'efficacité. Pour les entreprises qui s'appuient sur des composants externalisés, les retards et les inefficacités peuvent entraîner des revers coûteux et des opportunités perdues.
Atlas Copco, leader dans le domaine des solutions industrielles, a été confronté à ces mêmes défis lors de la production de son bol de livraison de rivets, un composant essentiel des systèmes de rivetage autoperceurs utilisés dans l'industrie automobile. En adoptant la fabrication additiveFA en interne, l'entreprise a non seulement surmonté ces obstacles, mais elle a également réalisé d'importantes économies, réduit les déchets et raccourci considérablement les délais d'exécution. L'utilisation de la machine EOS P 396 et le matériau polymère PA 2200, Atlas Copco a transformé son approche de la production. Cette étude de cas explore la manière dont la fabrication additive a apporté des améliorations mesurables et remodelé sa stratégie de fabrication.

"La collaboration avec EOS nous a fourni une solution clé en main et nous a aidés à adapter nos processus de sorte que nous sommes maintenant en production en série avec plusieurs composants, que nous sommes en train de prototyper rapidement des centaines d'autres composants et que nous avons atteint le retour sur investissement en seulement 18 mois".
Jason Edwards, directeur technique chez Atlas Copco
Défi
Jusqu'à présent, Atlas Copco dépendait de fournisseurs externes pour des composants tels que le bol de livraison des rivets, une pièce essentielle de ses systèmes de rivetage autoperceurs largement utilisés dans le secteur automobile. Cette dépendance se traduisait par des délais de livraison prolongés de 6 à 12 semaines, une augmentation des coûts de production et une complexité de la chaîne d'approvisionnement. En outre, les processus de fabrication conventionnels contribuaient à la perte d'environ 7 % des matériaux, ce qui mettait en évidence la nécessité d'une solution plus durable.
Nous voulions un contrôle plus étroit de notre fabrication qui nous permettrait de réduire les délais et les coûts et de prototyper rapidement de nouveaux produits", explique Jason Edwards, directeur technique chez Atlas Copco. "Travailler avec EOS et Additive Minds nous a donné une solution clé en main et nous a aidés à adapter nos processus de sorte que nous sommes maintenant en production en série avec plusieurs composants, que nous sommes en train de prototyper rapidement des centaines d'autres et que nous avons atteint le retour sur investissement en seulement 18 mois".
Trier et nourrir
Un bol imprimé en 3D fournit efficacement des rivets, rationalisant ainsi les processus de fabrication automatisés.


Solution
Pour relever ces défis, Atlas Copco a collaboré avec EOS et sa division de conseil, Additive Minds, afin de mettre en place des capacités de FA en interne. Ils ont choisi l'imprimante 3D EOS P 396 , connue pour sa flexibilité et sa précision, et ont utilisé le matériau polymère PA 2200 pour fabriquer le bol de livraison des rivets. Cette transition a permis à Atlas Copco de rationaliser sa chaîne d'approvisionnement, de réduire sa dépendance à l'égard des fournisseurs tiers et de mieux contrôler les calendriers de production. L'approche interne de la FA a également facilité le prototypage rapide, permettant des itérations rapides et des optimisations de la conception.
Résultats
Le passage à la fabrication additive en interne a eu des effets transformateurs pour Atlas Copco. L'une des améliorations les plus significatives a été la réduction considérable des délais de production. Auparavant, la production du bol de livraison des rivets nécessitait 6 à 12 semaines, en grande partie à cause de la dépendance à l'égard des fournisseurs externes et de la complexité des processus de fabrication traditionnels. Grâce à l'imprimante 3D EOS P 396 , les délais ont été ramenés à 3 ou 4 jours seulement, soit une réduction remarquable de 92 %. Cette amélioration a permis de répondre plus rapidement aux demandes de production et de faire preuve d'une plus grande souplesse pour répondre aux besoins urgents des clients.
La réduction des coûts est un autre résultat majeur. En éliminant le recours à des fournisseurs externes, en réduisant le nombre d'heures de travail et en rationalisant l'ensemble du processus de production, Atlas Copco est parvenu à réduire ses coûts de production de 30 %. L'efficacité de la fabrication additive a permis de minimiser les dépenses liées au réoutillage, aux changements de configuration et à la gestion de la chaîne d'approvisionnement. En outre, la précision et la fiabilité du processus de FA ont permis de réduire considérablement le gaspillage de matériaux. Alors que les méthodes de fabrication traditionnelles entraînaient environ 7 % de pertes de matériaux, le nouveau processus a ramené ce chiffre à près de zéro. Cette réduction n'a pas seulement contribué à la rentabilité, mais a également soutenu les objectifs de développement durable en minimisant la consommation de ressources.
En adoptant la fabrication additive, Atlas Copco a gagné en souplesse de production, en rentabilité et en avantages environnementaux, démontrant ainsi le puissant potentiel de la FA dans les applications industrielles. "LaFA nous a transformés. Nous remportons de nouveaux contrats dans le monde entier parce que nous pouvons fournir directement, à moindre coût et dans des délais courts. Avec EOS, nous avons un partenaire qui nous a soutenus tout au long de notre transition, qui nous offre un support rapide et qui continue à nous conseiller sur la conception des composants pour obtenir le meilleur résultat avec notre imprimante 3D", conclut Jason Edwards, directeur technique chez Atlas Copco.
Efficace et fiable
Le passage à l'impression 3D en interne a permis à Atlas Copco de réduire ses besoins en composants tiers et de ne plus être limité par les délais de la chaîne d'approvisionnement et les retards de transport.


"La fabrication additive nous a transformés. Nous remportons de nouveaux contrats dans le monde entier parce que nous pouvons fournir directement, à moindre coût et dans des délais courts."
Jason Edwards, directeur technique chez Atlas Copco
Études de cas EOS
Découvrez trois décennies d'excellence en matière d'impression 3D avec EOS